RO4350B PCB Manufacturing
RO4350B PCB Manufacturing,RO4350B PCBs are high-frequency printed circuit boards known for their exceptional performance in RF (Radio Frequency) and microwave applications. Composed of a ceramic-filled hydrocarbon laminate, RO4350B offers a low dielectric constant and low loss tangent, ensuring minimal signal loss and maintaining signal integrity even at high frequencies. Its stable electrical properties over a wide frequency range make it suitable for various high-speed applications, including RF amplifiers, microwave circuits, antennas, and radar systems. With excellent thermal stability and mechanical strength, RO4350B PCBs provide reliability in demanding environments. Design considerations such as trace width and spacing, ground plane design, and via placement are crucial for optimizing performance. RO4350B PCBs can be manufactured using lead-free processes, meeting modern electronics manufacturing standards. Overall, RO4350B PCBs are preferred for applications requiring high-frequency performance, signal integrity, and reliability.
What is RO4350B PCB?
RO4350B is a high-frequency laminate material used in the manufacturing of printed circuit boards (PCBs). It is designed for applications requiring high performance at RF (Radio Frequency) and microwave frequencies.
Here are some key features and characteristics of RO4350B PCB material:
- Dielectric Constant (Dk): RO4350B typically has a dielectric constant of around 3.48 ± 0.05, which is relatively stable over a wide frequency range. This property is crucial for maintaining signal integrity in high-frequency circuits.
- Low Loss Tangent: It exhibits a low dissipation factor (loss tangent) which is essential for minimizing signal loss, especially in high-frequency applications.
- Temperature Stability: RO4350B offers good thermal stability, making it suitable for applications that operate in varying temperature environments.
- Mechanical Properties: It has good mechanical strength and dimensional stability, which are important for maintaining the integrity of the PCB during fabrication and operation.
- Lead-free Compatible: RO4350B is compatible with lead-free processing, meeting the requirements of modern electronics manufacturing standards.
- Applications: Due to its high-frequency performance and reliability, RO4350B is commonly used in applications such as RF amplifiers, microwave circuits, antennas, satellite communication systems, radar systems, and other high-speed digital systems where signal integrity is critical.
Overall, RO4350B PCBs are favored in industries where high-frequency performance, low loss, and thermal stability are essential requirements.
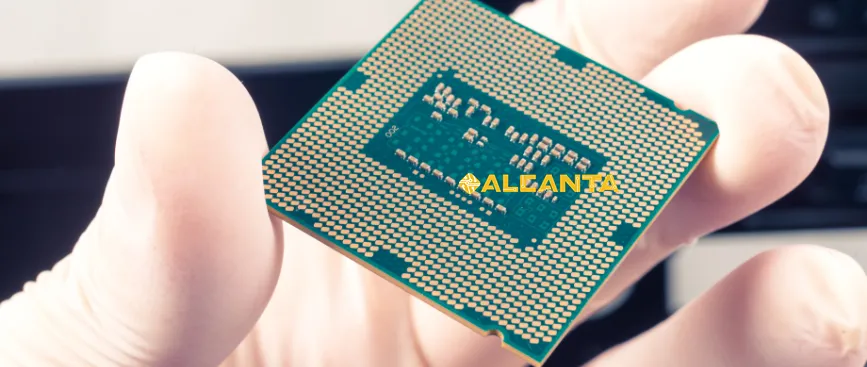
RO4350B PCB Manufacturing
What are the RO4350B PCB Design Guidelines?
Designing PCBs with RO4350B material requires careful consideration of its properties to ensure optimal performance. Here are some general design guidelines:
- Trace Width and Spacing: Use appropriate trace widths and spacing to match the desired characteristic impedance. This helps minimize signal loss and impedance mismatches. The trace width and spacing should be calculated based on the desired impedance using appropriate transmission line theory equations or PCB design software.
- Ground Plane: Maintain a solid ground plane on the PCB to provide good signal return paths and minimize electromagnetic interference (EMI). A continuous ground plane helps improve signal integrity and reduces crosstalk between traces.
- Via Design: Pay attention to via design to minimize signal reflections and impedance mismatches. Use short and wide vias to reduce parasitic inductance and impedance discontinuities.
- Component Placement: Place components strategically to minimize signal paths and reduce parasitic capacitance and inductance. Keep high-speed signal traces short and direct to minimize signal degradation.
- Copper Thickness: RO4350B PCBs are available in various copper thicknesses. Choose the appropriate copper thickness based on the current carrying capacity and impedance requirements of your design.
- Thermal Management: Consider thermal management techniques to dissipate heat effectively, especially in high-power applications. Ensure adequate spacing between high-power components and use thermal vias to transfer heat away from critical components.
- Edge Treatment: Consider edge treatment techniques such as chamfering or rounding to reduce the risk of delamination and improve the overall reliability of the PCB.
- Stackup Design: Design the PCB stackup carefully, considering factors such as layer count, dielectric thickness, and material properties. Optimize the stackup to meet impedance requirements, minimize signal loss, and provide adequate isolation between signal layers.
- Manufacturability: Keep manufacturability in mind throughout the design process. Ensure that the design adheres to the capabilities of the chosen fabrication process and manufacturer’s guidelines.
- EMC Considerations: Implement appropriate EMC (electromagnetic compatibility) measures such as shielding, filtering, and grounding to minimize EMI and ensure compliance with regulatory requirements.
By following these guidelines and working closely with your PCB manufacturer, you can design RO4350B PCBs that meet your performance requirements and ensure reliable operation in high-frequency applications.
What is the RO4350B PCB Fabrication Process?
The fabrication process for RO4350B PCBs is similar to that of standard PCBs, but there are specific considerations due to the material’s properties and intended applications. Here is a general overview of the fabrication process:
- Preparation of Design Files: The fabrication process begins with the preparation of design files using PCB design software. These files include the PCB layout, including trace routing, component placement, drill files, and any other necessary documentation.
- Material Selection: Choose RO4350B laminate material with the desired thickness and copper weight based on the requirements of your design.
- Prepreg Cutting: If multiple layers are required, prepreg sheets are cut to the appropriate size to match the dimensions of the core material.
- Drilling: Holes for through-hole components and vias are drilled into the core material using precision drilling equipment. The drill files generated from the design files guide the drilling process.
- Copper Cladding: Copper foil is laminated onto both sides of the core material using heat and pressure to create the conductive layers. The copper thickness should match the design specifications.
- Imaging and Etching: A photoresist layer is applied to the copper surfaces, and the design pattern is transferred onto the photoresist using photolithography techniques. The exposed copper is then etched away using chemical processes, leaving behind the desired copper traces.
- Layer Alignment and Lamination: If multiple layers are used, the layers are aligned and laminated together using heat and pressure to form a single, multi-layered PCB.
- Plating and Surface Finish: Through-holes and vias are plated with conductive material to provide electrical connections between layers. Surface finish processes such as HASL (Hot Air Solder Leveling), ENIG (Electroless Nickel Immersion Gold), or immersion tin are applied to protect exposed copper surfaces and facilitate soldering.
- Silkscreen Printing: Component outlines, reference designators, and other markings are printed onto the PCB surface using a silkscreen printing process.
- Routing and Profiling: Individual PCBs are routed from the larger panel using CNC routing machines or other cutting methods. The edges are profiled to remove excess material and achieve the final PCB dimensions.
- Inspection and Testing: Each PCB undergoes visual inspection, electrical testing, and quality control checks to ensure it meets the design specifications and industry standards.
- Packaging and Shipping: Finished PCBs are packaged according to customer requirements and shipped to the assembly facility for component placement and soldering.
Throughout the fabrication process, strict adherence to design specifications, material handling procedures, and quality control measures is essential to ensure the reliability and performance of the final RO4350B PCBs. Working with experienced PCB manufacturers familiar with high-frequency materials and processes can help streamline the fabrication process and ensure optimal results.
How do you manufacture RO4350B PCBs?
Manufacturing RO4350B PCBs involves several steps, including material preparation, fabrication processes, and quality control measures. Here’s an overview of the manufacturing process:
- Material Selection: Choose RO4350B laminate material with the desired thickness and copper weight based on the requirements of your design. RO4350B material is typically supplied in sheets or panels.
- Panel Preparation: Cut the RO4350B material into panels of appropriate size based on the PCB design requirements. The panels are cleaned and prepared for subsequent processing steps.
- Drilling: Holes for through-hole components and vias are drilled into the RO4350B panels using precision drilling equipment. The drill files generated from the design files guide the drilling process. Special attention is paid to drilling parameters to minimize material damage and ensure hole accuracy.
- Copper Cladding: Copper foil is laminated onto both sides of the RO4350B panels using heat and pressure to create the conductive layers. The copper thickness should match the design specifications. After lamination, the excess copper is trimmed to the desired shape.
- Imaging and Etching: A photoresist layer is applied to the copper surfaces, and the design pattern is transferred onto the photoresist using photolithography techniques. The exposed copper is then etched away using chemical processes, leaving behind the desired copper traces. Multiple etching and imaging steps may be required for multilayer PCBs.
- Layer Alignment and Lamination: If multiple layers are used, the individual layers are aligned and laminated together using heat and pressure to form a single, multi-layered PCB. This process involves carefully aligning the drilled holes and ensuring proper registration between layers.
- Plating and Surface Finish: Through-holes and vias are plated with conductive material to provide electrical connections between layers. Surface finish processes such as HASL (Hot Air Solder Leveling), ENIG (Electroless Nickel Immersion Gold), or immersion tin are applied to protect exposed copper surfaces and facilitate soldering.
- Silkscreen Printing: Component outlines, reference designators, and other markings are printed onto the PCB surface using a silkscreen printing process. This step helps with component placement and assembly.
- Routing and Profiling: Individual PCBs are routed from the larger panel using CNC routing machines or other cutting methods. The edges are profiled to remove excess material and achieve the final PCB dimensions.
- Inspection and Testing: Each RO4350B PCB undergoes visual inspection, electrical testing, and quality control checks to ensure it meets the design specifications and industry standards. This includes checks for dimensional accuracy, layer alignment, trace integrity, and electrical continuity.
- Packaging and Shipping: Finished RO4350B PCBs are packaged according to customer requirements and shipped to the assembly facility for component placement and soldering.
Throughout the manufacturing process, strict adherence to design specifications, material handling procedures, and quality control measures is essential to ensure the reliability and performance of the final RO4350B PCBs. Collaboration with experienced PCB manufacturers familiar with high-frequency materials and processes can help optimize manufacturing efficiency and product quality.
How much should RO4350B PCBs cost?
The cost of RO4350B PCBs can vary depending on various factors such as the PCB size, complexity, layer count, copper thickness, surface finish, quantity, lead time, and the capabilities of the PCB manufacturer.
Here are some factors that can influence the cost:
- PCB Size: Larger PCBs generally cost more due to the increased material and manufacturing time required.
- Complexity: PCBs with intricate designs, tight tolerances, and fine pitch components may require additional manufacturing steps, which can increase the cost.
- Layer Count: Multi-layer PCBs typically cost more than single or double-layer PCBs due to the additional material and processing involved.
- Copper Thickness: Thicker copper layers will increase material costs and may require special processing techniques.
- Surface Finish: Different surface finishes have varying costs. For example, ENIG (Electroless Nickel Immersion Gold) tends to be more expensive than HASL (Hot Air Solder Leveling).
- Quantity: Larger quantities often result in lower per-unit costs due to economies of scale.
- Lead Time: Rush orders or shorter lead times may incur additional fees.
It’s essential to obtain quotes from multiple PCB manufacturers to compare prices and services accurately. Additionally, some PCB manufacturers offer online quotation tools where you can input your PCB specifications to get an estimated cost.
As a rough estimate, the cost of RO4350B PCBs can range from a few dollars for simple prototypes to several hundred dollars or more for complex, high-volume production runs. However, these figures can vary significantly depending on the specific requirements of your project and the chosen manufacturer.
What is RO4350B PCB base material?
RO4350B is a high-performance PCB material known for its excellent electrical properties at high frequencies. It is primarily composed of a ceramic-filled hydrocarbon laminate, which provides a balance of electrical, mechanical, and thermal properties suitable for high-frequency applications.
The base material of RO4350B typically consists of:
- Reinforcement Material: Glass or woven fiberglass is commonly used as reinforcement material in the laminate. This provides mechanical strength and dimensional stability to the PCB.
- Resin System: The resin system in RO4350B is a hydrocarbon-based material that holds the reinforcement material together. It provides electrical insulation and contributes to the overall mechanical properties of the laminate.
- Ceramic Filler: RO4350B contains a ceramic filler, often composed of a blend of different ceramic materials. This filler contributes to the dielectric properties of the material, such as the dielectric constant and dissipation factor, which are crucial for high-frequency performance.
- Copper Foil: Copper foil is laminated onto the surface of the RO4350B material to create the conductive layers necessary for PCB circuitry. The copper foil thickness can vary depending on the design requirements.
Overall, the combination of the reinforcement material, resin system, ceramic filler, and copper foil in RO4350B laminate provides the necessary electrical characteristics, mechanical strength, and thermal stability required for high-frequency PCB applications.
Which company manufactures RO4350B PCBs?
RO4350B PCBs are manufactured by many well-known electronic materials manufacturers, including Rogers Corporation. Rogers Corporation is a company with extensive experience in the field of high-performance materials, and they produce a range of materials for high-frequency applications, including RO4350B.
RO4350B is a high-frequency circuit board material from Rogers Corporation, characterized by excellent dielectric performance and stability, suitable for RF, microwave, and other high-frequency applications. Designed to meet the requirements of high-frequency signal transmission, it is widely used in communication, radar, antenna, satellite communication, and other fields.
As a professional PCB manufacturing company, our company can produce RO4350B PCBs and provide customized solutions to meet specific customer needs. We have advanced production equipment and a technical team capable of ensuring high-quality PCB manufacturing to meet customer requirements for performance, reliability, and delivery time.
Our manufacturing process is carefully designed and optimized to ensure the quality and consistency of RO4350B PCB production. We strictly adhere to international standards and quality management systems, conducting rigorous quality control and inspection at every stage of manufacturing to ensure that each PCB meets customer requirements and standards.
Furthermore, our company emphasizes customer service and communication, committed to building long-term cooperative relationships with customers. We can provide technical support, sample production, quick delivery, and competitive prices to meet diverse customer needs and help customers succeed in the market.
In summary, our company has the technical capabilities, production equipment, and quality assurance system required to produce RO4350B PCBs, and we have earned the trust and satisfaction of customers with professional, reliable, and flexible services.
What are the 7 qualities of good customer service?
Good customer service is essential for businesses to build strong relationships with their customers and maintain their loyalty. Here are seven qualities that characterize good customer service:
- Responsiveness: Good customer service involves being prompt and responsive to customer inquiries, concerns, and requests. Customers appreciate quick and efficient responses to their queries, whether through phone calls, emails, or live chat support.
- Empathy: Empathy is the ability to understand and share the feelings of others. Good customer service representatives listen actively to customers, show empathy for their concerns, and strive to find solutions that address their needs and emotions.
- Clear Communication: Effective communication is crucial in providing good customer service. Clear and concise communication helps avoid misunderstandings and ensures that customers receive accurate information about products, services, policies, and resolutions to their issues.
- Knowledgeability: Good customer service representatives possess in-depth knowledge about the products or services offered by the business. They can answer customer questions, provide guidance, and offer recommendations based on their expertise, enhancing the customer experience.
- Professionalism: Professionalism involves conducting oneself with integrity, respect, and courtesy when interacting with customers. Good customer service representatives maintain a positive attitude, remain calm under pressure, and handle challenging situations with professionalism and diplomacy.
- Problem-Solving Skills: Good customer service requires problem-solving skills to address customer issues effectively. Representatives should be able to identify problems, analyze situations, and propose solutions that meet the needs of customers while aligning with company policies and procedures.
- Follow-Up and Feedback: Following up with customers after resolving their issues demonstrates commitment and care. Good customer service includes seeking feedback from customers to understand their experiences, identify areas for improvement, and continuously enhance the quality of service provided.
By embodying these qualities, businesses can deliver exceptional customer service experiences that foster trust, satisfaction, and loyalty among their customer base.
FAQs
What is RO4350B PCB material?
RO4350B is a high-frequency laminate material used in the manufacturing of printed circuit boards (PCBs). It offers excellent electrical properties at high frequencies, making it suitable for RF, microwave, and other high-speed applications.
What are the key features of RO4350B PCBs?
RO4350B PCBs offer a low dielectric constant, low loss tangent, stable electrical properties over a wide frequency range, good thermal stability, and mechanical strength. These features make them ideal for high-frequency applications requiring signal integrity and reliability.
What are the typical applications of RO4350B PCBs?
RO4350B PCBs are commonly used in RF amplifiers, microwave circuits, antennas, satellite communication systems, radar systems, and high-speed digital systems where signal integrity is critical.
How do RO4350B PCBs differ from standard PCBs?
RO4350B PCBs are specifically designed for high-frequency applications and offer superior electrical performance compared to standard PCB materials. They have a lower dielectric constant, lower loss tangent, and better thermal stability, making them suitable for demanding high-frequency environments.
What are the design considerations for RO4350B PCBs?
Design considerations for RO4350B PCBs include trace width and spacing for impedance matching, ground plane design for signal integrity, via design for minimizing signal reflections, and thermal management for dissipating heat effectively.
Can RO4350B PCBs be manufactured with lead-free processes?
Yes, RO4350B PCBs can be manufactured using lead-free processes, meeting the requirements of modern electronics manufacturing standards and regulations.
Where can I purchase RO4350B PCBs?
RO4350B PCBs can be purchased from various PCB manufacturers and suppliers specializing in high-frequency materials. It’s essential to choose a reputable manufacturer with experience in producing high-quality RO4350B PCBs.