RO4003C 24G Radar PCB Manufacturer
RO4003C 24G Radar PCB Manufacturer,RO4003C 24G Radar PCBs are high-frequency printed circuit boards specifically engineered for 24 GHz radar applications. Utilizing advanced RO4003C laminate material from Rogers Corporation, these PCBs offer exceptional electrical performance, including low dielectric loss and precise impedance control. Designed for automotive collision avoidance, adaptive cruise control, and industrial sensing, they ensure reliable signal transmission and minimal interference. With stringent design considerations and meticulous manufacturing processes, RO4003C 24G Radar PCBs deliver superior performance and durability in demanding radar systems.
What is RO4003C 24G Radar PCB?
RO4003C 24G Radar PCB is a specific type of printed circuit board (PCB) designed for use in 24 GHz radar systems. The “RO4003C” refers to the material used in manufacturing the PCB, which is a high-frequency laminate material known for its excellent electrical properties, particularly in applications requiring high signal integrity and low loss.
The “24G” designation indicates that this PCB is optimized for use in radar systems operating at a frequency of 24 gigahertz (GHz). Radar systems operating in this frequency range are commonly used in automotive applications for features like collision avoidance, adaptive cruise control, and blind spot detection. Additionally, they find applications in industrial settings for distance measurement, motion detection, and object tracking.
This PCB likely features specialized design elements tailored to the requirements of radar systems, such as controlled impedance traces, RF/microwave components, and high-frequency signal routing techniques to ensure minimal signal loss and interference.
In summary, the RO4003C 24G Radar PCB is a high-quality, high-frequency printed circuit board optimized for use in 24 GHz radar systems, offering excellent performance and reliability for applications in automotive, industrial, and other fields requiring radar technology.
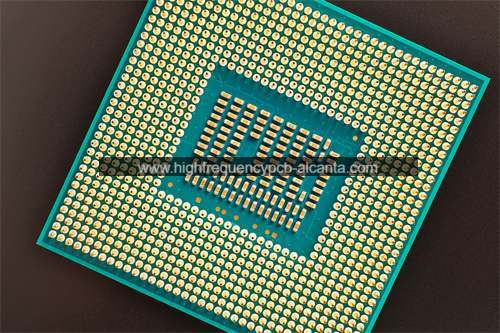
RO4003C 24G Radar PCB Manufacturer
What are the PCB Design Guidelines for RO4003C 24G Radar PCB?
Designing a PCB using RO4003C material for a 24 GHz radar system involves adhering to specific guidelines to ensure optimal performance. Here are some general PCB design guidelines for RO4003C 24G Radar PCB:
- Impedance Matching: Maintain controlled impedance for RF/microwave traces to minimize signal loss and reflections. Use impedance calculators or simulation tools to determine trace width, thickness, and spacing.
- Signal Integrity: Pay attention to signal integrity to minimize electromagnetic interference (EMI) and ensure reliable signal transmission. This includes proper ground plane placement, signal routing techniques (such as avoiding sharp bends and corners), and signal isolation.
- Grounding: Implement a solid ground plane to provide a low-impedance return path for high-frequency signals and to minimize ground loops. Ensure proper grounding of components and connectors.
- Component Placement: Carefully place components to minimize signal path lengths and reduce parasitic capacitance and inductance. Place RF/microwave components close to each other to minimize interconnect lengths.
- Decoupling Capacitors: Include decoupling capacitors near power supply pins of active components to filter out high-frequency noise and maintain stable power distribution.
- Thermal Management:Consider thermal management techniques, such as thermal vias and heat sinks, to dissipate heat generated by active components, especially in high-power radar systems.
- RF Shielding: Use RF shielding techniques, such as grounded metal enclosures or shielding cans, to minimize electromagnetic interference and prevent crosstalk between RF/microwave components.
- Transmission Line Design: Use microstrip or stripline transmission line configurations for RF/microwave traces, depending on the application requirements and signal frequencies.
- PCB Stackup: Optimize the PCB stackup to achieve desired impedance characteristics and to minimize signal loss. Consider using multiple layers for better signal routing and impedance control.
- Testing and Validation: Perform thorough testing and validation of the PCB design using simulation tools, such as electromagnetic field solvers and network analyzers, to verify signal integrity, impedance matching, and overall performance.
By following these guidelines, designers can develop RO4003C 24G Radar PCBs that meet the stringent requirements of high-frequency radar systems, ensuring reliable and accurate performance in applications such as automotive radar, industrial sensing, and wireless communication.
What is the RO4003C 24G Radar PCB Fabrication Process?
The fabrication process for RO4003C 24G Radar PCBs involves several steps to ensure the precise manufacturing of high-frequency printed circuit boards optimized for radar applications. Here’s a general overview of the fabrication process:
- Material Preparation: The fabrication process starts with the preparation of RO4003C laminate material. This involves cutting the laminate sheets to the required size based on the dimensions of the PCB design.
- Drilling: Holes are drilled into the laminate material for through-hole components and vias. High-precision drilling equipment is used to ensure accuracy and consistency in hole placement.
- Copper Cladding: Copper foil is laminated onto one or both sides of the RO4003C laminate material. The copper foil thickness is selected based on the design requirements for signal integrity and impedance control.
- Photoresist Application: A layer of photoresist material is applied to the surface of the copper-clad laminate. The photoresist acts as a protective layer during the etching process.
- Exposure and Development:The PCB design is transferred onto the photoresist layer using a photomask and exposure to UV light. After exposure, the unexposed areas of the photoresist are developed, leaving behind a pattern of hardened resist that corresponds to the PCB traces and pads.
- Etching: The exposed copper areas not protected by the photoresist are etched away using chemical etchants. This process removes the unwanted copper, leaving behind the desired copper traces and pads on the laminate surface.
- Strip and Clean: The remaining photoresist is stripped away from the PCB surface, leaving clean copper traces and pads. The PCB is then cleaned to remove any residues from the fabrication process.
- Surface Finish:Depending on the design requirements, the PCB may undergo surface finishing processes such as immersion gold, immersion silver, or immersion tin plating to protect the copper surfaces from oxidation and improve solderability.
- Solder Mask Application: A solder mask layer is applied over the copper traces and pads, leaving only the areas where soldering is required exposed. The solder mask helps prevent solder bridges and protects the PCB from environmental factors.
- Silkscreen Printing: Component labels, reference designators, and other markings are printed onto the PCB surface using a silkscreen printing process for ease of assembly and identification.
- Final Inspection: The fabricated PCBs undergo a final inspection to ensure they meet the specified design requirements and quality standards. This may include dimensional checks, electrical testing, and visual inspection of the PCBs.
- Panelization and Separation: If multiple PCBs are fabricated on a single panel, they are separated into individual boards using routing or depanelization techniques.
Overall, the fabrication process for RO4003C 24G Radar PCBs involves a series of precise and controlled steps to produce high-quality printed circuit boards optimized for use in radar systems operating at 24 GHz frequencies. Each step requires careful attention to detail to ensure the performance and reliability of the final PCB product.
How do you manufacture a RO4003C 24G Radar PCB?
Manufacturing a RO4003C 24G Radar PCB involves several steps, from designing the layout to final assembly. Here’s a detailed guide:
- Designing the PCB Layout: Use PCB design software to create the layout of the PCB, considering the specifications of the radar system and the characteristics of RO4003C material. Ensure proper placement of components, signal traces, ground planes, and other features.
- Material Selection:Choose RO4003C laminate material based on its high-frequency performance and low loss characteristics, suitable for 24 GHz radar applications.
- Panelization (Optional): If producing multiple PCBs simultaneously, arrange them on a panel for efficient manufacturing.
- Film Generation: Generate films or photomasks based on the PCB layout to transfer the circuit pattern onto the copper-clad laminate during the manufacturing process.
- Preparation of Laminate Material: Cut the RO4003C laminate sheets to the required size, ensuring they match the dimensions of the PCB layout.
- Copper Cladding: Laminate copper foil onto one or both sides of the RO4003C laminate material, typically using heat and pressure to bond the copper to the substrate.
- Lamination: Place the photomask onto the copper-clad laminate and expose it to UV light. This process transfers the PCB layout onto a layer of photoresist applied to the copper surface.
- Development: Develop the exposed photoresist using chemical solutions to reveal the copper traces and pads pattern.
- Etching: Submerge the laminate material in an etchant solution, which removes the unprotected copper, leaving behind the desired traces and pads on the PCB.
- Stripping and Cleaning: Remove the remaining photoresist from the PCB surface, followed by thorough cleaning to remove any residues from the fabrication process.
- Surface Finishing: Apply surface finish to protect the exposed copper surfaces from oxidation and enhance solderability. Common surface finishes include immersion gold, immersion silver, and immersion tin.
- Solder Mask Application: Apply a solder mask layer over the copper traces and pads, leaving only the desired areas exposed for soldering.
- Silkscreen Printing: Print component labels, reference designators, and other markings onto the PCB surface using silkscreen printing for assembly and identification purposes.
- Final Inspection:Inspect the fabricated PCBs to ensure they meet quality standards and specifications. This may include dimensional checks, electrical testing, and visual inspection.
- Panel Separation: If PCBs were fabricated on a panel, separate them into individual boards using routing or depanelization techniques.
- Assembly:Populate the PCB with electronic components, such as resistors, capacitors, ICs, and connectors, according to the Bill of Materials (BOM) and assembly instructions.
- Soldering: Solder the components onto the PCB using reflow soldering, wave soldering, or hand soldering techniques, depending on the component type and assembly requirements.
- Testing: Perform functional testing and quality assurance checks to verify the performance and reliability of the assembled RO4003C 24G Radar PCB.
By following these steps, manufacturers can produce high-quality RO4003C 24G Radar PCBs suitable for use in radar systems operating at 24 GHz frequencies, ensuring optimal performance and reliability in various applications.
How much should a RO4003C 24G Radar PCB cost?
The cost of a RO4003C 24G Radar PCB can vary widely depending on several factors, including the complexity of the design, the size of the board, the quantity ordered, and the specific requirements of the application. Here are some factors that can influence the cost:
- PCB Size and Layers: Larger PCBs with more layers typically cost more to manufacture due to increased material and manufacturing complexity.
- Material Cost: RO4003C laminate material is higher in cost compared to standard FR-4 materials due to its superior high-frequency performance.
- Design Complexity:PCB designs with dense component placement, high-speed signal routing, and fine pitch components may require advanced manufacturing techniques and incur higher costs.
- Surface Finish and Additional Features: The choice of surface finish (e.g., immersion gold, immersion silver) and additional features like impedance control, blind/buried vias, and controlled dielectric thickness can impact the cost.
- Order Quantity: Bulk orders typically result in lower per-unit costs compared to smaller quantities due to economies of scale.
- Turnaround Time: Expedited fabrication services may come at a premium compared to standard lead times.
- Supplier and Location: PCB fabrication costs can vary depending on the supplier and their location. Offshore manufacturing may offer lower costs but can involve longer lead times and potential quality control issues.
As a rough estimate, a simple single-layer RO4003C 24G Radar PCB with standard features and a small size might cost anywhere from $50 to $200 per unit for low-volume orders. However, complex multilayer boards with advanced features and larger sizes could cost several hundred to a few thousand dollars per unit or more.
For accurate pricing, it’s best to consult with PCB manufacturers or suppliers, providing them with detailed specifications and quantities required for a customized quote.
What is the RO4003C 24G Radar PCB Base Material?
The base material for RO4003C 24G Radar PCBs is RO4003C laminate. RO4003C is a high-frequency laminate material specifically designed for applications requiring excellent electrical performance at microwave frequencies. It is manufactured by Rogers Corporation, a leading supplier of advanced materials for PCBs.
RO4003C laminate is composed of woven glass reinforced hydrocarbon/ceramic composite with a dielectric constant (Dk) of 3.38 ± 0.05 and a dissipation factor (Df) of 0.0027 at 10 GHz. These electrical properties make RO4003C suitable for high-frequency applications, including radar systems operating at 24 GHz.
RO4003C laminate offers low loss, tight dielectric thickness control, and stable electrical performance over a wide frequency range, making it an ideal choice for RF/microwave PCBs where signal integrity and performance are critical.
In summary, the base material for RO4003C 24G Radar PCBs is RO4003C laminate, known for its high-frequency performance and reliability in demanding applications such as radar systems.
Which company makes RO4003C 24G Radar PCBs?
The manufacturer of RO4003C 24G Radar PCBs is Rogers Corporation. Rogers Corporation is a globally leading manufacturer of high-performance materials, specializing in advanced materials for printed circuit board (PCB) manufacturing. RO4003C is a high-frequency laminate material produced by Rogers Corporation, designed specifically for applications requiring excellent electrical performance at microwave frequencies.
Our company can also produce RO4003C 24G Radar PCBs. As a professional PCB manufacturer, we have advanced production equipment and a skilled technical team capable of producing high-quality, high-performance RO4003C 24G Radar PCBs according to customer requirements. Our production process strictly adheres to industry standards and incorporates advanced quality control systems to ensure that each PCB meets customer needs and specifications.
Our production capabilities cover various stages from prototyping to mass production, catering to customers’ requirements for different quantities. We also offer customization services to provide tailored PCB solutions based on customer design requirements and application scenarios, ensuring optimal performance and reliability.
With rich experience and expertise, our company provides comprehensive technical support and services to assist customers in achieving the success of their projects. We are committed to building long-term partnerships with customers and continuously improving our manufacturing capabilities and technical expertise to meet evolving market demands.
Whether it’s prototyping or large-scale production, we can efficiently complete orders with high quality. If you are looking for a reliable PCB manufacturer to produce RO4003C 24G Radar PCBs, our company would be an ideal choice.
What are the 7 qualities of good customer service?
Good customer service is essential for building strong relationships with customers and fostering loyalty. Here are seven qualities that define good customer service:
- Responsiveness: Good customer service involves being attentive and responsive to customer inquiries, requests, and concerns in a timely manner. Promptly addressing customer needs demonstrates care and commitment to their satisfaction.
- Empathy: Empathy is the ability to understand and share the feelings of others. Good customer service representatives listen actively, show genuine concern for customers’ issues, and strive to put themselves in the customers’ shoes to better address their needs and concerns.
- Clarity: Clear communication is crucial in customer service interactions. Good customer service representatives communicate effectively, using simple and easy-to-understand language to explain solutions, policies, and procedures to customers.
- Knowledgeability: Good customer service requires having a thorough understanding of the products or services being offered, as well as company policies and procedures. Knowledgeable representatives can provide accurate information, answer questions, and offer helpful guidance to customers.
- Professionalism:Professionalism involves maintaining a courteous and respectful demeanor when interacting with customers, even in challenging situations. Good customer service representatives remain calm, patient, and composed, demonstrating professionalism in every interaction.
- Problem-solving Skills: Good customer service representatives are skilled problem solvers who can effectively address customer issues and resolve conflicts. They actively listen to customers’ concerns, identify root causes of problems, and work collaboratively to find satisfactory solutions.
- Follow-through: Following through on commitments and promises is essential for building trust and credibility with customers. Good customer service representatives take ownership of customer issues, follow up on inquiries or complaints, and ensure that resolutions are implemented effectively.
By embodying these qualities, businesses can deliver exceptional customer service experiences that leave a positive impression on customers and contribute to long-term success.
FAQs about RO4003C 24G Radar PCBs
What are the advantages of using RO4003C for radar PCBs?
RO4003C offers low dielectric loss, tight dielectric thickness control, and stable electrical properties over a wide frequency range, making it ideal for high-frequency radar systems operating at 24 GHz.
What are the typical applications of RO4003C 24G Radar PCBs?
RO4003C 24G Radar PCBs are commonly used in automotive radar systems for features such as collision avoidance, adaptive cruise control, and blind spot detection. They are also used in industrial radar applications for distance measurement, motion detection, and object tracking.
What are the key design considerations for RO4003C 24G Radar PCBs?
Design considerations include controlled impedance routing, signal integrity optimization, proper grounding techniques, thermal management, and RF shielding to ensure optimal performance and reliability.
What are the manufacturing capabilities for RO4003C 24G Radar PCBs?
Manufacturers can produce RO4003C 24G Radar PCBs in various sizes, layers, and quantities, utilizing advanced fabrication techniques such as precision drilling, copper cladding, surface finishing, and solder mask application.
What is the cost range for RO4003C 24G Radar PCBs?
The cost of RO4003C 24G Radar PCBs varies depending on factors such as size, complexity, quantity, and specific requirements. Generally, prices can range from tens to hundreds of dollars per unit for low to medium volumes.
Where can I find reliable suppliers for RO4003C 24G Radar PCBs?
Reliable suppliers of RO4003C 24G Radar PCBs can be found through online directories, industry trade shows, or referrals from colleagues and industry experts. It’s important to choose a reputable supplier with experience in high-frequency PCB manufacturing and a track record of quality and reliability.