Rigid-flex Packaging Substrate Manufacturer
Rigid-flex Packaging Substrate Manufacturer,Rigid-flex Packaging Substrate combines rigid and flexible materials, offering versatility and space optimization in electronic device assembly. This substrate accommodates complex designs by integrating both rigid and flexible sections, enabling seamless connections between components. It provides structural support while allowing for bending and folding, ideal for compact and irregularly shaped devices. Comprising multiple layers including rigid and flexible substrates, Rigid-flex Packaging Substrates ensure reliable electrical connections and effective thermal management. They find applications in wearable devices, medical implants, and aerospace systems, where flexibility, durability, and space efficiency are essential. Rigid-flex Packaging Substrates drive innovation in electronic packaging, enabling advancements in various industries.
What is Rigid-flex Packaging Substrate?
Rigid-flex packaging substrate is a type of packaging base material used in electronic devices, especially in situations where circuit connections need to be made within limited space. It combines the advantages of rigid and flexible materials to meet complex design requirements.
This type of substrate typically consists of rigid base material (usually polyimide or other high-temperature materials) and flexible base material (usually polyester or polyamide). The rigid portion is used to support and protect circuit components, while the flexible portion allows the substrate to bend or fold between different components to accommodate specific spatial layouts or form factor requirements.
Rigid-flex packaging substrate offers the following advantages:
- Space efficiency: It can accommodate more circuit connections in limited space.
- Reliability: By reducing the number of interconnects and joints, the risk of faults and damage is reduced.
- Weight reduction: The presence of flexible material can reduce weight compared to traditional rigid packaging, making it useful for applications requiring lightweight solutions.
- Design flexibility: It allows designers to create electronic devices with complex shapes more freely.
Rigid-flex packaging substrates are widely used in various fields such as smartphones, tablets, wearable devices, medical equipment, etc., providing more possibilities for the design and manufacturing of electronic products.
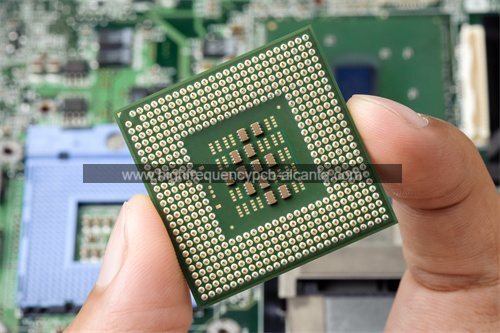
Rigid-flex Packaging Substrate Manufacturer
What are the functions of Rigid-flex Packaging Substrate?
The functions of Rigid-flex Packaging Substrate include:
- Providing mechanical support and protection: The rigid portion offers sufficient mechanical support to protect circuit components from external damage.
- Facilitating circuit connections: The flexible portion allows the substrate to bend or fold between different components, enabling the connection of circuit elements and facilitating circuit connections.
- Optimizing space utilization: Through flexible design, Rigid-flex Packaging Substrate can achieve more circuit connections within limited space, thus optimizing space utilization.
- Offering design flexibility: Rigid-flex Packaging Substrate enables designers to create electronic devices with complex shapes, meeting various design requirements.
- Weight reduction: Compared to traditional rigid packaging, the presence of flexible material can reduce weight, suitable for applications with weight requirements.
Overall, the functions of Rigid-flex Packaging Substrate are to provide reliable mechanical support, facilitate circuit connections, optimize space utilization, offer design flexibility, and reduce weight for electronic devices.
What are the different types of Rigid-flex Packaging Substrate?
The different types of Rigid-flex Packaging Substrates include:
- Single-sided Rigid-flex: These substrates consist of a single layer of flexible material with a rigid layer on one side.
- Double-sided Rigid-flex: These substrates feature flexible material with rigid layers on both sides, allowing for more complex circuit designs.
- Multilayer Rigid-flex: These substrates incorporate multiple layers of flexible material interleaved with rigid layers, providing enhanced functionality and versatility for intricate circuitry.
- Sculptured Rigid-flex: This type of substrate involves the selective removal of material from one or more layers, creating three-dimensional structures for specific applications.
- Dual-access Rigid-flex: These substrates feature access to circuitry from both sides, enabling increased flexibility in device design and assembly.
- Single-layer Rigid-flex: These substrates have a single layer of rigid material bonded to a single layer of flexible material, offering simplicity and cost-effectiveness for certain applications.
These various types of Rigid-flex Packaging Substrates cater to different design requirements and application scenarios in electronic device manufacturing.
Comparison between Rigid-flex Packaging Substrate and traditional packaging technologies
Comparison between Rigid-flex Packaging Substrate and traditional packaging technology:
Rigid-flex Packaging Substrates offer several advantages compared to traditional packaging technology:
- Space efficiency: Rigid-flex Packaging Substrates can accommodate more circuit connections in limited space since they allow circuits to bend or fold within the flexible part, reducing the physical footprint required.
- Reliability: With fewer interconnects and joints, Rigid-flex Packaging Substrates have fewer points of failure, enhancing overall system reliability and stability.
- Weight reduction: Rigid-flex Packaging Substrates are typically lighter compared to traditional rigid packaging, which is beneficial for applications requiring lightweight solutions.
- Design flexibility: Rigid-flex Packaging Substrates enable designers to create electronic devices with complex shapes, fulfilling diverse design requirements.
- Streamlined assembly processes: Due to fewer interconnects and joints, Rigid-flex Packaging Substrates require fewer steps during assembly, reducing manufacturing costs and enhancing production efficiency.
However, Rigid-flex Packaging Substrates may come with some limitations and challenges compared to traditional packaging technology. For example, they may have higher production costs, more complex manufacturing processes, and in some specific application scenarios, traditional packaging technology may still be more suitable. Therefore, when selecting packaging technology, it is essential to consider factors such as product design requirements, cost, and manufacturing capabilities comprehensively.
Main structure and manufacturing technology of Rigid-flex Packaging Substrate
The main structure and production technology of Rigid-flex Packaging Substrate are as follows:
Main Structure:
Rigid Substrate: Typically composed of polyimide (PI) or other high-temperature materials, providing mechanical support and protection for circuit components.
Flex Substrate: Usually made of materials such as polyester (PET) or polyimide (PI), allowing the substrate to bend or fold to facilitate circuit connections and adapt to spatial layouts.
Dielectric and Metal Layers: Used to form circuit structures between the rigid substrate and flexible substrate, where the dielectric layers isolate the metal layers to prevent short circuits.
Production Technology:
Lamination: The rigid substrate, flex substrate, dielectric layers, and metal layers are stacked according to design requirements and bonded together through a lamination process involving high temperature and pressure. This process ensures secure bonding of different materials and ensures overall structural stability.
Patterning: Techniques such as photolithography and chemical etching are used on the stacked substrates to form conductors and connection points on the metal layers according to design patterns. This process enables the creation of complex circuit structures through precise control.
Processing and Assembly: After patterning, subsequent processing and assembly steps such as cutting, drilling, and component mounting are carried out. These steps ensure that the final Rigid-flex Packaging Substrate meets design requirements and is ready for integration into electronic devices.
Through these production technologies, Rigid-flex Packaging Substrate can achieve complex circuit structures while providing mechanical support and flexibility, suitable for various application requirements in electronic devices.
FAQs (Frequently Asked Questions)
What is Rigid-flex Packaging Substrate?
Rigid-flex Packaging Substrate is a type of packaging base material used in electronic devices, combining rigid and flexible materials to enable complex circuit designs and accommodate limited space constraints.
What are the advantages of Rigid-flex Packaging Substrate?
Rigid-flex Packaging Substrate offers advantages such as space efficiency, reliability, weight reduction, design flexibility, and streamlined assembly processes compared to traditional packaging technologies.
What are the common applications of Rigid-flex Packaging Substrate?
Rigid-flex Packaging Substrate is commonly used in various electronic devices such as smartphones, tablets, wearable devices, medical equipment, and aerospace systems, where space-saving and reliability are crucial.
How is Rigid-flex Packaging Substrate manufactured?
Rigid-flex Packaging Substrate is typically manufactured through processes such as lamination, patterning, and processing/assembly, involving the stacking and bonding of rigid and flexible layers, patterning of circuit structures, and subsequent processing steps.
What design considerations should be taken into account when using Rigid-flex Packaging Substrate?
Designers should consider factors such as bending radius, flex layer thickness, material compatibility, signal integrity, thermal management, and mechanical stress to ensure the reliability and performance of Rigid-flex Packaging Substrate in their applications.
What are the limitations of Rigid-flex Packaging Substrate?
Rigid-flex Packaging Substrate may have limitations such as higher production costs, more complex manufacturing processes, and limited availability of materials suitable for high-temperature and high-frequency applications.
How does Rigid-flex Packaging Substrate contribute to product miniaturization and lightweight design?
Rigid-flex Packaging Substrate allows for more compact and lightweight designs by enabling the integration of multiple functions into a single component, reducing the need for additional connectors and cables.
What are the key factors influencing the selection of Rigid-flex Packaging Substrate for a specific application?
Factors such as application requirements, operating environment, cost considerations, manufacturing capabilities, and expected product lifecycle should be taken into account when selecting Rigid-flex Packaging Substrate.
Conclusion
In conclusion, Rigid-flex Packaging Substrate is a versatile and innovative solution for electronic packaging, offering a combination of rigid and flexible materials to meet the demands of modern electronic devices. Its unique structure and production techniques enable compact designs, enhanced reliability, and improved performance in various applications.
Despite its numerous advantages, designers must carefully consider factors such as material compatibility, signal integrity, and manufacturing costs when implementing Rigid-flex Packaging Substrate in their designs. Additionally, ongoing advancements in materials and manufacturing processes continue to expand the capabilities and applications of Rigid-flex Packaging Substrate.
Overall, Rigid-flex Packaging Substrate plays a crucial role in enabling the development of smaller, lighter, and more reliable electronic devices, driving progress in industries ranging from consumer electronics to aerospace and healthcare. With continued innovation and optimization, Rigid-flex Packaging Substrate is poised to remain a key technology in the ever-evolving field of electronic packaging.