What is Rigid-Flex Package Substrate?
Rigid-Flex Package Substrate Manufacturer,Rigid-flex package substrates combine the benefits of rigid and flexible PCBs, enabling versatile and reliable electronic assemblies. These substrates feature rigid sections for component mounting and flexible sections for dynamic bending or folding. They offer enhanced space utilization and reduce the need for connectors, minimizing assembly complexity. Rigid-flex substrates ensure excellent signal integrity, thermal management, and mechanical durability, making them ideal for compact and high-reliability applications like medical devices, aerospace systems, and wearables. Their ability to withstand repeated bending and vibration while maintaining electrical performance makes them essential for modern electronic designs requiring flexibility and durability.
Rigid-Flex Package Substrate and Ro4350B packaging substrate manufacturer, high frequency BGA substrate, using the most advanced Sap process, Msap process technology, fast delivery, stable quality.
A creatively fused packaging substrate stands as a extensively employed technology in the production of electronic devices, notably in the assembly of printed circuit boards (PCBs). This innovative approach integrates both rigid and flexible substrates into a unified package, presenting a solution that is more adaptable and spatially economical when contrasted with traditional PCBs that are exclusively rigid or flexible.
Within a rigid-flex packaging substrate, the rigid segment is crafted from conventional materials commonly found in rigid PCBs, typically consisting of glass-fiber-reinforced epoxy. In contrast, the flexible part utilizes materials characteristic of flexible PCBs, frequently incorporating polyimide. These pliable sections can be harnessed to form areas that are capable of bending or folding within the packaging, facilitating the adaptation of the PCB to the contours of the device or the available space.
The integration of both rigid and flexible substrates within the same package enables designers to craft more compact and lightweight electronic devices, particularly those with intricate form factors or strict space requirements. Rigid-flex technology is commonly applied in fields such as medical devices, aerospace systems, and wearable electronics, where spatial optimization and reliability are paramount.
Designing and manufacturing rigid-flex packaging substrates require specialized techniques and expertise, involving both rigid and flexible PCB fabrication processes and precise assembly methods to ensure reliability and durability.
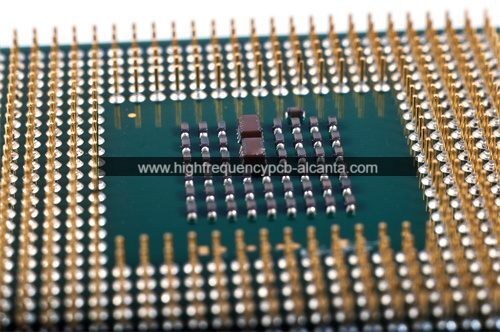
Rigid-Flex Package Substrate Manufacturer
What is the function of Rigid-Flex Package Substrate?
A Rigid-Flex Package Substrate functions as a dynamic and space-optimized solution for seamlessly integrating electronic components into various devices. Its roles and advantages include:
Adaptability to Diverse Shapes:
Rigid-flex substrates streamline the effortless integration of electronic components into devices distinguished by unique or intricate geometries.
The inherent flexibility of the substrate enables it to effortlessly conform to the device’s contours, skillfully optimizing the utilization of the available space.
Efficient Space Utilization:
Rigid-flex technology excels in maximizing space within electronic devices.
The amalgamation of rigid and flexible sections allows for more compact designs, particularly crucial in scenarios where spatial constraints are significant.
Weight Optimization:
By integrating pliable materials, the substrate aids in decreasing the overall weight of the electronic device, rendering it apt for applications where weight sensitivity is critical, such as in aerospace or portable devices..
Enhanced Reliability:
Rigid-flex substrates elevate the reliability of electronic devices by minimizing reliance on connectors and solder joints, potential weak links.
A reduction in interconnects and joints results in improved signal integrity and a diminished risk of mechanical failure.
Augmented Durability:
The substrate’s flexibility enhances durability, enabling it to endure bending and flexing without compromising the functionality of electronic components.
Streamlined Assembly:
The integration of both rigid and flexible elements in a unified substrate streamlines the assembly procedure, diminishing the quantity of interconnections and potential errors in the manufacturing process.
Versatility in Harsh Environments:
Rigid-flex substrates find application in challenging environments marked by widespread vibration, shock, and temperature variations, showcasing resilience in the presence of unfavorable conditions.
Essentially, a Rigid-Flex Package Substrate serves as an enabler in the design and manufacturing of electronic devices, providing adaptability, optimal space usage, and reliability for a wide range of applications.
What types of Rigid-Flex Package Substrate are available?
Various configurations of Rigid-Flex Package Substrates are at your disposal, each tailored to specific requirements in the realm of electronic device manufacturing. These encompass:
Single-Layer Rigid-Flex:
Comprising a solitary rigid layer and a lone flexible layer, apt for applications with straightforward designs or where flexibility is necessary in a singular direction.
Double-Layer Rigid-Flex:
Involving a duo of rigid layers separated by one or more flexible layers, providing heightened flexibility and adaptability for more intricate designs.
Multilayer Rigid-Flex:
Encompassing an array of rigid and flexible layers stacked together, affording increased design flexibility and catering to applications with intricate circuitry.
Conductive Via Rigid-Flex:
Employing conductive vias to establish electrical connections between different layers, commonly applied in applications necessitating intricate interconnections between rigid and flexible sections.
Coverlay Rigid-Flex:
Employing coverlay material to encapsulate flexible circuitry, enhancing both protection and durability.
Double-Sided Rigid-Flex:
Showcasing circuitry on both sides of the flexible layer, facilitating heightened component density and accommodating more elaborate designs.
Multilayer Rigid-Flex with Stiffeners:
Introducing additional rigid layers or stiffeners to provide extra support for components or areas necessitating increased stability.
Flex-to-Flex Rigid-Flex:
Incorporating flexible sections directly connected to each other, enabling the crafting of intricate three-dimensional configurations.
Mixed Dielectric Rigid-Flex:
Making use of different dielectric materials for rigid and flexible sections, optimizing both electrical and mechanical performance.
The selection of a specific Rigid-Flex Package Substrate type hinges on factors such as circuit intricacy, flexibility requirements, space limitations within the device, and the unique needs of a given application. Collaboration between designers and manufacturers is a common practice to pinpoint the most fitting configuration for a particular electronic device.
How does Rigid-Flex Package Substrate relate to IC packaging?
Rigid-Flex Package Substrates and IC (Integrated Circuit) packaging are interconnected elements in the landscape of electronic device manufacturing, often collaborating to achieve optimal performance and design adaptability.
IC Integration:
Rigid-Flex Package Substrates serve as a foundation for incorporating ICs into electronic devices. The amalgamation of rigid and flexible components enables the accommodation of ICs in diverse form factors, aligning with the specific layout needs of the device.
Space Efficiency:
Rigid-Flex technology facilitates the judicious use of space within electronic devices, allowing for the integration of multiple ICs in a space-efficient design. This is particularly crucial in applications where space is at a premium, such as in mobile devices or wearable electronics.
Signal Integrity:
Both Rigid-Flex Package Substrates and IC packaging contribute to preserving signal integrity. Rigid sections provide stability for precise IC placement, while flexible sections mitigate the need for intricate interconnections, thereby minimizing signal degradation.
Incorporating Complex Circuitry:
Rigid-Flex substrates are well-suited for applications necessitating intricate circuitry, often involving the integration of multiple ICs with diverse functionalities. This is prevalent in advanced electronic devices with sophisticated features.
Reliability and Endurance:
The fusion of rigid and flexible components in Rigid-Flex Package Substrates enhances the reliability and durability of electronic devices. This is pivotal for ensuring the enduring performance of ICs, particularly in environments with challenging conditions.
Tailoring to Form and Function:
Rigid-Flex technology allows for the customization of substrate layouts, empowering the creation of unique form factors for electronic devices. This adaptability is advantageous for IC packaging, offering the flexibility to tailor the substrate to the specific requirements of the integrated circuits.
In essence, Rigid-Flex Package Substrates and IC packaging collaborate to provide a versatile and space-efficient framework for seamlessly integrating ICs into electronic devices. This synergistic relationship enables the development of compact, reliable, and customized electronic solutions across diverse applications.
What is its structure and manufacturing technology?
The structure of the Rigid-Flex Package Substrate is characterized by a layered composition that harmoniously blends rigid and flexible elements, crafted through a specialized manufacturing methodology. This intricate process incorporates sophisticated techniques, including refined High-Density Interconnect (HDI) and semi-additive processes, aimed at elevating precision and intricacy.
Structure of Rigid-Flex Package Substrate:
Rigid Layers:
Fashioned from conventional rigid PCB materials like fiberglass-reinforced epoxy, providing a stable foundation for components.
Flexible Layers:
Comprised of flexible PCB materials, typically based on polyimide, offering the flexibility necessary for bending or folding within the package to accommodate the device’s form.
Adhesive Layers:
Utilizes adhesive materials to securely bond the rigid and flexible layers, ensuring a robust connection.
Conductive Layers:
Implements conductive traces and vias to establish electrical connections between layers, crucial for maintaining signal integrity and continuity.
Coverlay:
Applies a protective coverlay over the flexible layers to shield the circuitry from environmental factors such as moisture and mechanical stress.
Manufacturing Technology:
Layer Stacking:
Precisely stacks the rigid and flexible layers in the required configuration based on design specifications.
Lamination:
Subjects the stacked layers to a lamination process involving heat and pressure to securely bond them, ensuring durability.
Drilling and Vias:
Drills holes through the substrate for vias, facilitating electrical connections between layers.
Conductive Traces:
Patterns conductive traces onto the layers using methods such as etching or additive processes, creating electrical pathways on both rigid and flexible sections.
Coverlay Application:
Applies coverlay to the flexible sections, enhancing protection and long-term reliability.
Advanced Manufacturing Methods:
Improved HDI (High-Density Interconnect):
Utilizes HDI technology with finer traces and smaller vias, enabling increased component density and intricate circuitry, particularly beneficial for compact electronic devices.
Semi-Additive Processes:
Implements semi-additive processes to selectively add conductive material only where required, reducing waste and enhancing precision in manufacturing.
These advanced manufacturing methods contribute significantly to the improved performance, reliability, and miniaturization capabilities of Rigid-Flex Package Substrates, making them suitable for a diverse range of applications with complex form factors and strict space constraints.
How is Rigid-Flex Package Substrate manifested in practical applications?
Rigid-Flex Package Substrates exhibit their practical usefulness in various sectors, illustrating their adaptability and versatility in real-world applications.
Aerospace Systems:
In the aerospace realm, Rigid-Flex substrates play a pivotal role in shaping avionics systems. Their capability to conform to the aircraft’s contours and optimize space is critical for crafting compact and lightweight electronic components.
Medical Devices:
Rigid-Flex technology finds application in the medical field, meeting the demands for space-efficient and reliable solutions. This involves incorporating flexible circuits into medical implants or diagnostic equipment, allowing for inventive and tailored form factors.
Wearable Electronics:
The integration of Rigid-Flex Package Substrates brings notable benefits to wearable devices like smartwatches and fitness trackers. These substrates facilitate the development of electronic components with a blend of flexibility and adaptability. This not only ensures user comfort but also contributes to an overall enhancement in the durability of the devices.
Automotive Systems:
In the domain of automotive electronics, Rigid-Flex substrates play a pivotal role, making substantial contributions to both vehicle control systems and instrument clusters. The seamless integration of rigid and flexible elements is crucial for refining the design and augmenting the overall functionality of automotive applications.
Consumer Electronics:
Rigid-Flex technology is a prevalent feature in a wide array of consumer electronic devices, ranging from smartphones to tablets. The incorporation of this technology is instrumental in crafting devices known not only for their sleek and compact design but also for heightened reliability. Consequently, this significantly contributes to elevating the overall performance of these electronic gadgets.
Industrial Control Systems:
In industrial settings, Rigid-Flex Package Substrates find application in control systems and automation equipment. Their adaptability to specific form factors and resilience to environmental factors make them well-suited for creating robust and dependable electronic solutions in industrial applications.
Military and Defense:
Military and defense applications harness the advantages of Rigid-Flex substrates for electronic components across various systems. Their durability, compact design, and resilience to harsh conditions make them invaluable in military electronics.
Communication Devices:
Communication devices, including antennas and radio frequency modules, leverage the benefits of Rigid-Flex technology. The integration of rigid and flexible elements facilitates efficient signal transmission and reception in compact and portable communication equipment.
In summary, the practical applications of Rigid-Flex Package Substrates span a diverse range of industries, underscoring their substantial contribution to innovations in electronic design, miniaturization, and reliability across various technological domains.
Are there common questions about Rigid-Flex Package Substrate?
What characterizes a Rigid-Flex Package Substrate?
This inquiry seeks a foundational definition of Rigid-Flex Package Substrates and an exploration of their primary role in electronic devices.
How does Rigid-Flex technology function?
This question aims to delve into the underlying principles and manufacturing processes involved in creating Rigid-Flex Package Substrates.
What benefits arise from the incorporation of Rigid-Flex substrates?
Queries about the advantages of Rigid-Flex technology, including aspects like space optimization, flexibility, and increased reliability, are commonly raised.
What variations exist in Rigid-Flex configurations?
People often inquire about the different setups of Rigid-Flex substrates, ranging from single-layer to double-layer or multilayer designs.
Are there specific design considerations unique to Rigid-Flex PCBs?
Inquiries may focus on design considerations such as bending radius, layer stacking, and material choices when optimizing Rigid-Flex PCB designs.