Rigid-flex BGA Substrate Manufacturer
Rigid-flex BGA Substrate Manufacturer,Rigid-flex BGA Substrate combines rigid and flexible materials in a single package, offering versatility and space-saving benefits. This substrate integrates ball grid array (BGA) technology with flexible circuits, enabling conformal fitting into tight spaces and accommodating complex layouts. It ensures reliable electrical connections and efficient heat dissipation, crucial for high-performance electronic devices. Rigid-flex BGA Substrates find applications in aerospace, medical devices, and wearable technology, where compactness and durability are essential. By merging rigid and flexible elements, these substrates support innovative designs, enhance reliability, and facilitate miniaturization in modern electronic assemblies.
What is Rigid-flex BGA Substrate?
A Rigid-flex BGA (Ball Grid Array) Substrate refers to a type of printed circuit board (PCB) that incorporates both rigid and flexible sections. BGA is a type of surface-mount packaging used for integrated circuits, and it typically involves a grid of solder balls on the underside of the package.
In the case of a Rigid-flex BGA Substrate, the substrate material includes both rigid sections (typically made of fiberglass reinforced epoxy laminate) and flexible sections (usually made of polyimide film). This combination allows the PCB to bend or flex in certain areas while maintaining rigidity in others.
Rigid-flex PCBs are commonly used in applications where space is limited, and the PCB needs to conform to a specific shape or fit into tight spaces. They offer advantages such as reduced weight, improved reliability (due to fewer interconnects), and increased design flexibility compared to traditional rigid PCBs.
The BGA aspect indicates that this specific type of PCB includes BGA components, which are widely used in modern electronic devices due to their compact size, high pin count, and reliability. These components are often found in devices like smartphones, tablets, computers, and various other electronic gadgets.
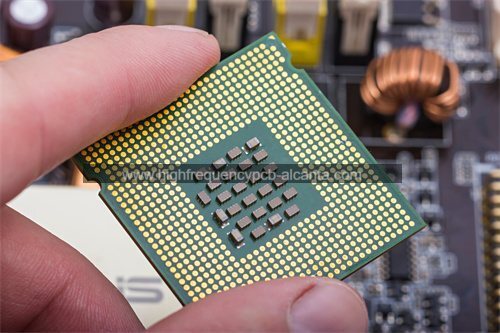
Rigid-flex BGA substrate Manufacturer
What are the Functions of Rigid-flex BGA Substrate?
The functions of a Rigid-flex BGA Substrate can vary depending on the specific application and design requirements. However, some common functions include:
Component Mounting: Rigid-flex BGA substrates allow for the mounting of various electronic components, including BGA integrated circuits (ICs), resistors, capacitors, and other surface-mount devices (SMDs). The BGA components are typically mounted on the rigid sections of the substrate, while the flexible sections may house other components or serve as interconnects between rigid sections.
Interconnection: Rigid-flex BGA substrates provide pathways for electrical signals to travel between different components on the board. This includes both internal connections within the substrate and external connections to other circuitry or devices.
Signal Routing: The flexible sections of the substrate can be used to route signals between different rigid sections or between components mounted on different layers of the PCB. This flexibility allows designers to create complex signal paths while minimizing the need for additional connectors or cables.
Mechanical Support: The rigid sections of the substrate provide structural support for the components mounted on the board and help maintain the overall shape and stability of the PCB. The flexible sections allow the board to bend or flex without breaking, making it suitable for applications where space is limited or where the PCB needs to conform to a specific shape or contour.
Space Savings: Rigid-flex BGA substrates can help save space compared to traditional rigid PCBs and separate flexible interconnects. By integrating both rigid and flexible sections into a single substrate, designers can achieve higher component density and more compact designs.
Reliability: Rigid-flex BGA substrates can improve reliability by reducing the number of interconnects and solder joints compared to designs that use separate rigid and flexible PCBs. This can lead to improved mechanical and electrical performance, as well as increased resistance to environmental factors such as vibration and thermal cycling.
Overall, the functions of a Rigid-flex BGA Substrate revolve around providing a compact, reliable, and flexible platform for mounting and interconnecting electronic components in a variety of applications.
What are the Different Types of Rigid-flex BGA Substrate?
There are several different types of Rigid-flex BGA substrates, each with its own characteristics and applications. Some of the common types include:
Single-Layer Rigid-flex BGA Substrate: This type of substrate consists of a single rigid layer and one or more flexible layers. It is suitable for applications where space is limited, and only a small amount of flexibility is required.
Double-Layer Rigid-flex BGA Substrate: In this type, there are two rigid layers separated by one or more flexible layers. It offers more flexibility and routing options compared to single-layer substrates and is commonly used in applications where moderate flexibility is needed.
Multilayer Rigid-flex BGA Substrate: Multilayer Rigid-flex BGA substrates consist of multiple rigid and flexible layers stacked together. They offer the highest level of flexibility and routing options and are suitable for complex designs and applications where a significant amount of flexibility is required.
Coverlay Rigid-flex BGA Substrate: Coverlay refers to a flexible dielectric material that is applied over the flexible portion of the PCB to protect the circuitry and provide additional insulation. Coverlay Rigid-flex BGA substrates are commonly used in high-reliability applications where extra protection is needed against moisture, dust, and other environmental factors.
Solder Mask Defined (SMD) Rigid-flex BGA Substrate: In SMD Rigid-flex BGA substrates, the solder mask is used to define the flexible areas of the board. This type of substrate offers precise control over the flexible regions and can be tailored to specific design requirements.
Adhesiveless Rigid-flex BGA Substrate: Adhesiveless Rigid-flex BGA substrates use a special bonding technique to laminate the flexible layers to the rigid layers without the need for adhesives. This results in improved reliability and mechanical performance compared to substrates that use adhesives.
Built-up Rigid-flex BGA Substrate: Built-up Rigid-flex BGA substrates involve building up the flexible layers using multiple thin layers of flexible materials, such as polyimide film and adhesive, to achieve the desired flexibility and routing capabilities.
Each type of Rigid-flex BGA substrate has its advantages and limitations, and the choice depends on factors such as the specific application requirements, cost considerations, and manufacturing capabilities.
How does Rigid-flex BGA Substrate Relate to IC Packaging?
Rigid-flex BGA substrates are closely related to IC (Integrated Circuit) packaging, as they provide a platform for mounting and interconnecting ICs within electronic devices. Here’s how they relate:
Mounting of ICs: BGA (Ball Grid Array) is a type of IC packaging where solder balls are arranged in a grid on the underside of the IC package. These solder balls make direct contact with corresponding pads on the substrate, facilitating electrical connections. Rigid-flex BGA substrates provide the structural support necessary for mounting BGA-packaged ICs securely.
Interconnection: ICs often require numerous electrical connections to other components and subsystems within a device. Rigid-flex BGA substrates provide the pathways for these electrical connections. They enable the routing of signals between ICs and other components on the PCB, both within the rigid sections and through the flexible sections of the substrate.
Signal Integrity: Rigid-flex BGA substrates play a crucial role in maintaining signal integrity within an electronic system. By providing controlled impedance traces and minimizing signal loss and noise, they ensure that the signals transmitted between ICs and other components remain accurate and reliable.
Thermal Management: Many ICs generate heat during operation, which can affect their performance and reliability. Rigid-flex BGA substrates can incorporate features such as thermal vias and copper planes to help dissipate heat away from the ICs, thus improving thermal management and prolonging the lifespan of the components.
Space Efficiency: Rigid-flex BGA substrates allow for the integration of multiple ICs and other components into a compact and space-efficient package. By combining rigid and flexible sections in a single substrate, they enable designers to optimize the layout of electronic components and minimize the overall size of the device.
Reliability: The reliability of IC packaging is crucial for the overall performance and longevity of electronic devices. Rigid-flex BGA substrates offer advantages such as reduced solder joint fatigue, improved mechanical stability, and enhanced resistance to environmental factors like vibration and thermal cycling, thereby enhancing the reliability of the packaged ICs.
In summary, Rigid-flex BGA substrates are an integral part of IC packaging, providing the necessary support, interconnection, signal integrity, thermal management, space efficiency, and reliability for mounting and integrating ICs within electronic devices.
What are the Differences Between Rigid-flex BGA Substrate and PCB?
Rigid-flex BGA substrates and traditional PCBs (Printed Circuit Boards) serve similar purposes in electronic systems, but there are several key differences between them:
Flexibility: The most significant difference is the flexibility of Rigid-flex BGA substrates compared to traditional PCBs. Rigid-flex substrates incorporate both rigid and flexible sections, allowing them to bend or flex to fit into irregular shapes or tight spaces. Traditional PCBs are typically rigid and cannot bend or flex without risking damage.
Construction: Rigid-flex BGA substrates are constructed using a combination of rigid and flexible materials, such as fiberglass-reinforced epoxy laminate for the rigid sections and polyimide film for the flexible sections. Traditional PCBs are typically made entirely of rigid materials, such as FR-4 epoxy laminate.
Component Mounting: Both Rigid-flex BGA substrates and traditional PCBs support the mounting of electronic components, including ICs, resistors, capacitors, and connectors. However, Rigid-flex BGA substrates often include specialized features for mounting BGA-packaged ICs, such as solder pads and vias arranged in a grid pattern on the substrate.
Interconnects: Rigid-flex BGA substrates provide pathways for electrical signals to travel between components using both rigid and flexible sections of the substrate. Traditional PCBs also provide interconnects for electrical signals but do not incorporate flexible sections for bending or flexing.
Size and Shape: Rigid-flex BGA substrates are often used in applications where space is limited or where the PCB needs to conform to a specific shape or contour. Traditional PCBs are available in various sizes and shapes but are generally rigid and flat.
Complexity: Rigid-flex BGA substrates can be more complex to design and manufacture compared to traditional PCBs due to the combination of rigid and flexible materials and the need to accommodate both. Traditional PCBs are typically simpler in design and manufacturing, especially for single-layer or double-layer boards.
Reliability: Rigid-flex BGA substrates can offer higher reliability compared to traditional PCBs in certain applications, especially those subject to mechanical stress, vibration, or thermal cycling. The flexible sections of Rigid-flex BGA substrates can absorb mechanical shocks and provide better thermal management compared to rigid PCBs.
In summary, while both Rigid-flex BGA substrates and traditional PCBs serve as platforms for mounting and interconnecting electronic components, Rigid-flex BGA substrates offer additional flexibility and versatility, making them suitable for applications where space is limited or where bending or flexing is required.
What are the Main Structures and Production Technologies of Rigid-flex BGA Substrate?
The main structures and production technologies of Rigid-flex BGA substrates involve several key components and manufacturing processes. Here are the main structures and production technologies typically used:
Rigid Sections: Rigid sections of Rigid-flex BGA substrates are typically made of traditional rigid PCB materials such as fiberglass-reinforced epoxy laminate (FR-4). These sections provide structural support for components and help maintain the overall shape and rigidity of the substrate.
Flexible Sections: Flexible sections of Rigid-flex BGA substrates are typically made of flexible materials such as polyimide (PI) film. These sections allow the substrate to bend or flex without breaking and provide pathways for electrical connections between rigid sections.
Layer Stacking: Rigid-flex BGA substrates are constructed by stacking multiple layers of rigid and flexible materials together. The layers are laminated together using heat and pressure to form a single, integrated substrate.
Adhesive Bonding: Adhesives are often used to bond the layers of rigid and flexible materials together during the lamination process. These adhesives provide mechanical strength and help ensure good adhesion between the layers.
Copper Foil Lamination: Copper foil is typically laminated to the surface of the substrate to provide electrical conductivity and create circuit traces. The copper foil is etched to create the desired circuit patterns and connections between components.
Via Formation: Vias are holes drilled or laser-drilled through the substrate to create electrical connections between different layers of the substrate. These vias are plated with copper to provide conductivity and allow electrical signals to pass between layers.
Coverlay Application: Coverlay is a thin layer of flexible dielectric material applied over the flexible sections of the substrate to protect the circuitry and provide additional insulation. Coverlay is typically applied using a lamination process similar to the lamination of the substrate layers.
Surface Finish: Surface finishes such as solder mask and surface plating are applied to the substrate to protect the copper traces and provide solderable surfaces for component mounting. These surface finishes help ensure reliable electrical connections and protect the substrate from environmental factors.
Overall, the production of Rigid-flex BGA substrates involves a combination of traditional PCB manufacturing techniques such as layer stacking, copper foil lamination, and via formation, as well as specialized processes for bonding rigid and flexible materials together and applying coverlay to protect the flexible sections of the substrate.
Frequently Asked Questions (FAQs)
What is a Rigid-flex BGA substrate?
A Rigid-flex BGA substrate is a type of printed circuit board (PCB) that incorporates both rigid and flexible sections. It is often used in applications where space is limited or where the PCB needs to conform to a specific shape or contour.
What are the advantages of Rigid-flex BGA substrates?
Rigid-flex BGA substrates offer several advantages, including space savings, improved reliability, flexibility in design, reduced weight, and increased resistance to environmental factors such as vibration and thermal cycling.
What are the main structures of Rigid-flex BGA substrates?
The main structures of Rigid-flex BGA substrates include rigid sections made of materials like fiberglass-reinforced epoxy laminate (FR-4) and flexible sections made of materials like polyimide (PI) film. These sections are typically stacked together and laminated to form the substrate.
How are Rigid-flex BGA substrates manufactured?
Rigid-flex BGA substrates are manufactured using a combination of traditional PCB manufacturing techniques such as layer stacking, copper foil lamination, and via formation, as well as specialized processes for bonding rigid and flexible materials together and applying coverlay to protect the flexible sections of the substrate.
What are some common applications of Rigid-flex BGA substrates?
Rigid-flex BGA substrates are commonly used in electronic devices such as smartphones, tablets, wearable devices, medical devices, automotive electronics, and aerospace systems. They are particularly well-suited for applications where space is limited or where the PCB needs to bend or flex to fit into tight spaces.
What are the differences between Rigid-flex BGA substrates and traditional PCBs?
The main differences between Rigid-flex BGA substrates and traditional PCBs lie in their flexibility, construction, and manufacturing processes. Rigid-flex BGA substrates incorporate both rigid and flexible sections, allowing them to bend or flex, whereas traditional PCBs are typically rigid and flat.
Conclusion
In conclusion, Rigid-flex BGA substrates represent an innovative solution in the realm of printed circuit board (PCB) technology, offering a combination of rigid and flexible elements that provide unique advantages in various electronic applications. By integrating both rigid and flexible sections into a single substrate, Rigid-flex BGA substrates enable designers to achieve compact, reliable, and versatile designs that would be challenging or impossible with traditional rigid PCBs.
The main structures and production technologies of Rigid-flex BGA substrates involve a careful combination of materials, such as fiberglass-reinforced epoxy laminate (FR-4) for rigid sections and polyimide (PI) film for flexible sections, along with specialized manufacturing processes including layer stacking, copper foil lamination, via formation, adhesive bonding, and coverlay application.
Rigid-flex BGA substrates offer numerous advantages, including space savings, improved reliability, flexibility in design, reduced weight, and increased resistance to environmental factors such as vibration and thermal cycling. These substrates find applications in a wide range of industries, from consumer electronics to medical devices, automotive systems, and aerospace technology.
Overall, Rigid-flex BGA substrates represent a cutting-edge solution for modern electronics, providing engineers and designers with the flexibility and versatility needed to push the boundaries of innovation and create the next generation of electronic devices.