RF Package Substrate Manufacturer
RF Package Substrate Manufacturer,RF Package Substrates are specialized materials essential for assembling high-frequency electronic circuits. They provide a stable platform for mounting RF components like amplifiers, filters, and antennas, ensuring efficient signal transmission and minimal loss. These substrates, made from materials like ceramic or organic laminates, undergo precise fabrication processes including patterning, metallization, and via formation. RF package substrates are designed to meet stringent performance requirements, offering low signal loss, high-frequency operation, and effective heat dissipation. They play a crucial role in the development of RF systems for applications ranging from telecommunications and radar to wireless connectivity and satellite communications.
What is an RF Package Substrate?
An RF package substrate, in the realm of electronics, is a specialized material serving as a foundation for mounting and connecting radio frequency (RF) components. These substrates are designed to meet the stringent requirements of RF circuits, such as low signal loss, high-frequency operation, and efficient heat dissipation. They’re typically made from materials like ceramic, organic laminate, or metal, chosen for their electrical properties and mechanical stability.
The substrate provides a stable platform for bonding RF chips, such as amplifiers, filters, and antennas, as well as for creating the necessary interconnections between these components. This interconnectivity is crucial for maintaining signal integrity and minimizing losses in high-frequency applications.
Additionally, RF package substrates often incorporate features like plated through-holes, vias, and metal traces to facilitate the routing of signals and ensure proper grounding and shielding. Advanced fabrication techniques, such as thin-film deposition and laser drilling, are commonly employed to achieve precise geometries and electrical properties.
In summary, an RF package substrate plays a vital role in the construction of RF circuits by providing a stable and efficient platform for integrating and connecting various components while maintaining the required electrical performance at high frequencies.
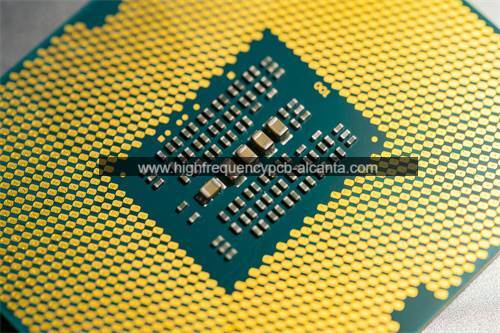
RF Package Substrate Manufacturer
What are the RF Package Substrate Design Guidelines?
Designing RF package substrates requires careful consideration of various factors to ensure optimal performance. Some key design guidelines include:
- Substrate Material Selection: Choose a substrate material with properties suitable for RF applications, such as low dielectric constant (εr) and low loss tangent (tan δ), to minimize signal loss and distortion.
- Substrate Thickness: Optimize substrate thickness based on the operating frequency and desired performance. Thinner substrates are preferred for higher frequencies to reduce signal propagation delays and losses.
- Grounding and Shielding: Implement effective grounding and shielding techniques to minimize electromagnetic interference (EMI) and maintain signal integrity. This involves proper placement of ground planes and shielding structures to isolate sensitive RF components.
- Transmission Line Design: Design transmission lines (e.g., microstrips, coplanar waveguides) with appropriate dimensions and impedance matching techniques to minimize signal reflections and maximize power transfer efficiency.
- Via Design: Optimize via structures for signal routing and interconnecting different layers of the substrate. Consider parameters such as via size, spacing, and placement to minimize parasitic effects and maintain signal integrity.
- Heat Dissipation: Incorporate thermal management features, such as thermal vias and heat sinks, to dissipate heat generated by active RF components and prevent overheating, which can degrade performance and reliability.
- Package Integration: Design the substrate layout to accommodate the integration of RF components, such as amplifiers, filters, and antennas, while minimizing signal coupling and interference.
- Manufacturability: Consider manufacturability aspects during the design phase to ensure that the substrate can be fabricated using standard processes with high yield and reliability.
- Simulation and Validation: Use RF simulation tools and prototyping techniques to validate the design and ensure that it meets the desired performance specifications before mass production.
By following these design guidelines, engineers can develop RF package substrates that meet the stringent requirements of modern RF applications, including low signal loss, high-frequency operation, and reliable performance.
What is the RF Package Substrate Fabrication Process?
The fabrication process of an RF package substrate involves several precise and controlled steps to ensure the substrate meets the stringent requirements for high-frequency applications. Here’s an overview of the typical fabrication process:
- Material Selection: Choose a suitable substrate material such as ceramic (e.g., alumina or LTCC – Low Temperature Co-fired Ceramic), organic laminates (e.g., PTFE or Rogers materials), or metal-backed substrates. The material should have properties like a low dielectric constant, low loss tangent, and good thermal conductivity.
- Substrate Preparation: Prepare the raw substrate material by cutting it into the desired shape and size. Surface treatment may be applied to improve adhesion of subsequent layers.
- Patterning: Apply a photoresist layer to the substrate and use photolithography to define the circuit patterns. UV light exposure through a mask transfers the desired pattern onto the photoresist.
- Etching: Remove the exposed (or unexposed, depending on the type of photoresist) areas of the photoresist, and then etch away the substrate material in these areas to create the circuit patterns. Common etching techniques include wet chemical etching and dry etching (plasma etching).
- Metallization:Deposit metal layers onto the patterned substrate to form the conductive traces, ground planes, and pads. This is typically done using sputtering, evaporation, or electroplating techniques. Common metals used include gold, copper, and silver.
- Via Formation: Drill vias (vertical interconnections between layers) using mechanical drilling, laser drilling, or etching. Vias are then metallized to create electrical connections between different layers of the substrate.
- Layer Stacking (for Multilayer Substrates): If a multilayer substrate is required, individual layers are fabricated separately and then aligned and laminated together. This process often involves pressing the layers at high temperatures and pressures.
- Sintering (for Ceramic Substrates): For ceramic substrates like LTCC, the layers are co-fired at high temperatures to achieve densification and mechanical strength. This step ensures that the ceramic and metal layers are bonded together properly.
- Surface Finishing:Apply surface finishes such as solder masks, anti-corrosion coatings, or gold plating to protect the substrate and enhance its solderability and longevity.
- Inspection and Testing: Perform thorough inspection and testing to ensure the substrate meets design specifications. This includes visual inspection, electrical testing, and sometimes X-ray or other imaging techniques to check for internal defects.
- Component Assembly: Mount and bond the RF components onto the substrate using soldering, wire bonding, or flip-chip techniques. Ensure proper alignment and secure electrical connections.
- Final Testing and Quality Control: Conduct final functional tests to verify the performance of the assembled RF package. This ensures that the substrate and components work together as intended and meet the required performance standards.
By following these detailed steps, manufacturers can produce high-quality RF package substrates that are capable of supporting high-frequency signals with minimal loss and interference.
How do you manufacture an RF Package Substrate?
Manufacturing an RF package substrate involves a series of intricate steps to create a robust substrate capable of supporting high-frequency RF components. Here’s a detailed overview of the manufacturing process:
- Substrate Material Selection: Choose a substrate material appropriate for RF applications, such as ceramic (e.g., alumina, aluminum nitride), organic laminates (e.g., FR-4, Rogers materials), or metal-backed substrates. Consider properties like dielectric constant, loss tangent, thermal conductivity, and cost.
- Substrate Preparation: Cut the raw substrate material into the desired size and shape using precision machining techniques like sawing, milling, or laser cutting. Clean the substrate surface to remove any contaminants that could affect subsequent processing steps.
- Surface Treatment (Optional): Apply surface treatments such as chemical cleaning, plasma treatment, or primer coating to enhance adhesion and surface uniformity for subsequent processing steps.
- Circuit Design and Layout: Design the RF circuit layout using computer-aided design (CAD) software, considering factors like signal integrity, impedance matching, and thermal management. Define the placement of components, traces, vias, and ground planes to optimize RF performance.
- Photolithography: Apply a layer of photoresist onto the substrate surface. Use photolithography techniques to selectively expose the photoresist to UV light through a photomask, defining the desired circuit patterns. Develop the exposed photoresist to reveal the pattern on the substrate surface.
- Etching: Etch away the exposed substrate material using wet chemical etching or dry etching techniques (e.g., plasma etching) to create the circuit features defined by the patterned photoresist. Control the etching process parameters to achieve precise feature dimensions and sidewall profiles.
- Metallization: Deposit metal layers onto the substrate surface to form conductive traces, pads, and vias. Common deposition techniques include sputtering, evaporation, electroplating, or electroless plating. Choose metals with suitable conductivity, adhesion, and solderability properties (e.g., gold, copper, silver).
- Dielectric Layer Formation (for Multilayer Substrates): If manufacturing a multilayer substrate, repeat the photolithography, etching, and metallization steps to create additional circuit layers. Introduce dielectric layers (e.g., polymer films, ceramic pastes) between metal layers to insulate and separate conductive traces.
- Via Formation: Drill or laser ablate via holes through the substrate material to create electrical connections between different circuit layers. Metallize the via holes to ensure electrical continuity and low impedance paths between layers.
- Surface Finishing: Apply surface finishes such as solder masks, protective coatings, or surface treatments (e.g., immersion gold, OSP – Organic Solderability Preservatives) to improve solderability, corrosion resistance, and surface flatness. Perform surface planarization if necessary to achieve uniformity.
- Inspection and Testing: Conduct rigorous quality control inspections throughout the manufacturing process to detect defects, dimensional inaccuracies, and electrical anomalies. Utilize techniques like visual inspection, automated optical inspection (AOI), X-ray inspection, and electrical testing to ensure compliance with specifications.
- Packaging and Assembly: Package the RF substrate into protective containers or carriers to prevent damage during handling and transportation. Assemble RF components (e.g., integrated circuits, passive devices) onto the substrate using techniques like soldering, wire bonding, or flip-chip bonding. Ensure precise alignment and secure electrical connections.
- Final Testing and Characterization: Perform comprehensive electrical testing and characterization of the assembled RF package to verify performance parameters such as impedance matching, insertion loss, return loss, and power handling capability. Validate the functionality and reliability of the RF subsystem in simulated or real-world operating conditions.
By following these manufacturing steps with precision and attention to detail, manufacturers can produce high-quality RF package substrates that meet the stringent requirements of modern RF applications, including low signal loss, high frequency operation, and reliable performance.
How much should an RF Package Substrate cost?
The cost of an RF package substrate can vary widely depending on several factors, including the substrate material, manufacturing complexity, size, thickness, layer count (for multilayer substrates), surface finish, and volume of production. Here are some key factors influencing the cost:
- Substrate Material: Different materials have varying costs. Ceramic substrates tend to be more expensive than organic laminates due to their superior electrical properties and manufacturing complexity.
- Manufacturing Complexity: Complex substrates with intricate circuitry, fine feature sizes, tight tolerances, and multiple layers require more sophisticated manufacturing processes, which can increase production costs.
- Size and Thickness: Larger substrates or thicker substrates may require more material and longer processing times, leading to higher costs.
- Layer Count: Multilayer substrates, which consist of several stacked layers interconnected with vias, are more expensive to manufacture than single-layer substrates due to the added complexity and processing steps.
- Surface Finish: Certain surface finishes, such as gold plating or immersion gold, can add to the cost of the substrate due to the additional materials and processing involved.
- Volume of Production: Economies of scale typically apply in manufacturing, meaning that larger production volumes often result in lower per-unit costs due to optimized processes and bulk material purchasing.
- Quality Requirements: Higher quality standards, tighter tolerances, and additional testing may increase production costs but can improve the reliability and performance of the substrate.
- Supplier and Location: The choice of supplier and manufacturing location can also impact costs due to differences in labor rates, overhead expenses, and logistical factors.
Given these factors, the cost of an RF package substrate can range from a few dollars for simple single-layer substrates to several hundred dollars or more for complex multilayer substrates with advanced features and materials. It’s essential for companies to carefully evaluate their requirements and budget constraints when selecting a substrate solution. Additionally, engaging with substrate manufacturers early in the design process can help optimize the design for cost-effective production.
What is RF Package Substrate Base Material?
The RF package substrate base material refers to the foundational material upon which the RF circuitry and components are fabricated. This material serves as the substrate or “canvas” for building the RF package, providing structural support, electrical insulation, and mechanical stability. The choice of base material is critical as it directly impacts the performance, reliability, and cost of the RF package.
Several types of materials are commonly used as RF package substrate base materials, each with its own characteristics and suitability for different applications. Some of the most prevalent base materials include:
- Ceramic Substrates: Ceramic materials such as alumina (Al2O3), aluminum nitride (AlN), and silicon nitride (Si3N4) are widely used for RF applications due to their excellent electrical properties, high thermal conductivity, and dimensional stability over a wide temperature range. Ceramic substrates are ideal for high-power RF devices and applications requiring high-frequency operation.
- Organic Laminates: Organic laminate materials, including fiberglass-reinforced epoxy (FR-4) and specialized high-frequency laminates like polytetrafluoroethylene (PTFE) or Rogers materials, are commonly used for lower-frequency RF applications. While organic laminates may not offer the same level of electrical performance as ceramics, they are cost-effective and well-suited for applications where high-frequency operation is not critical.
- Metal-Backed Substrates: Metal-backed substrates consist of a metal base layer (typically copper or aluminum) bonded to a dielectric material such as FR-4 or PTFE. These substrates offer enhanced thermal conductivity and heat dissipation capabilities, making them suitable for power amplifier and RF power module applications.
- Flexible Substrates: Flexible substrates, often made of polyimide or liquid crystal polymer (LCP), are used in applications requiring bendability or conformal mounting, such as wearable electronics or flexible RF circuits. While flexible substrates may have slightly lower electrical performance compared to rigid materials, they offer unique advantages in certain applications.
The selection of the RF package substrate base material depends on various factors, including the desired electrical performance, thermal management requirements, mechanical constraints, cost considerations, and specific application needs. Designers must carefully evaluate these factors to choose the most suitable base material for their RF package design. Additionally, advances in material science and manufacturing techniques continue to expand the range of available substrate materials, providing designers with more options to meet evolving RF design challenges.
Which company manufactures RF Package Substrates?
Many companies manufacture RF package substrates, including Murata, Rogers Corporation, KYOCERA, Taiyo Yuden, Mitsubishi Electric, and Amkor Technology, among others. These companies offer various types of substrates, including ceramic substrates, organic composite substrates, and metal substrates, to meet the needs of different RF applications.
As for our company, we also manufacture RF package substrates. We have advanced manufacturing equipment and a professional team capable of meeting custom requirements. Our production process covers the entire process from substrate material preparation to final packaging. We can provide various types of substrates, including ceramic, organic composite, and metal substrates, according to customer specifications and design requirements.
Our strengths include:
- Customization: We can customize various types and specifications of RF package substrates according to customer requirements, including different materials, thicknesses, layer counts, and surface treatments.
- High-Quality Manufacturing: We use advanced manufacturing processes and strict quality control standards to ensure high-quality, reliable products.
- Flexible Production Capacity: We have flexible production capabilities to meet both small-scale custom orders and large-scale production requirements.
- Technical Support: Our experienced engineering team and technical support staff can provide professional technical support and consulting services to help customers solve various RF package design and manufacturing issues.
In summary, our company can provide customers with high-quality, customized RF package substrate solutions to meet their performance and reliability requirements for RF applications.
What are the qualities of good customer service?
Good customer service is characterized by several qualities that prioritize the satisfaction and needs of customers. Some key qualities include:
- Empathy: Understanding and empathizing with the customer’s perspective, concerns, and emotions. Empathetic customer service representatives can connect with customers on a personal level and provide more effective assistance.
- Responsiveness: Being prompt and proactive in addressing customer inquiries, issues, and requests. Customers appreciate timely responses and solutions to their concerns, which helps build trust and loyalty.
- Clear Communication: Communicating clearly and effectively with customers, using language that is easy to understand and providing accurate information. Clear communication helps prevent misunderstandings and ensures that customers have realistic expectations.
- Knowledgeability: Possessing in-depth knowledge about products, services, policies, and procedures. Knowledgeable customer service representatives can answer questions, provide guidance, and resolve issues more efficiently, instilling confidence in customers.
- Problem-Solving Skills: Having strong problem-solving skills to identify and address customer concerns effectively. This may involve thinking creatively, finding alternative solutions, and going above and beyond to meet customer needs.
- Professionalism: Maintaining a professional demeanor and attitude at all times, even in challenging situations. Professionalism fosters respect and trust between the customer and the service provider, enhancing the overall customer experience.
- Adaptability: Being flexible and adaptable to accommodate diverse customer needs and preferences. Adaptable customer service representatives can adjust their approach based on the specific situation and customer requirements.
- Patience: Demonstrating patience and tolerance, especially when dealing with frustrated or irate customers. Patient customer service representatives can listen attentively, diffuse tension, and work towards resolving issues calmly.
- Follow-Up: Following up with customers after resolving their concerns to ensure satisfaction and address any lingering issues. This demonstrates commitment to customer care and reinforces the relationship between the customer and the company.
- Continuous Improvement: Striving for continuous improvement by soliciting feedback from customers, analyzing trends, and identifying areas for enhancement. Companies that prioritize ongoing improvement in their customer service practices can better meet evolving customer expectations and stay competitive in the market.
Overall, good customer service is about building positive relationships, exceeding expectations, and making customers feel valued and appreciated throughout their interactions with the company.
FAQs
What is an RF package substrate?
An RF package substrate is a specialized material used as a foundation for mounting and connecting radio frequency (RF) components in electronic circuits. It provides structural support, electrical insulation, and interconnection pathways for RF devices.
What are the common materials used for RF package substrates?
Common materials include ceramic (e.g., alumina, aluminum nitride), organic laminates (e.g., FR-4, Rogers materials), and metal-backed substrates. Each material has its own electrical, thermal, and mechanical properties suited for different RF applications.
What factors should be considered when selecting an RF package substrate?
Factors to consider include frequency of operation, signal loss requirements, thermal management needs, cost considerations, and compatibility with manufacturing processes. The substrate material, thickness, dielectric properties, and surface finish are also important factors.
What are the advantages of ceramic substrates for RF applications?
Ceramic substrates offer high electrical insulation, excellent thermal conductivity, and dimensional stability over a wide temperature range. They are well-suited for high-frequency RF devices and applications requiring high power handling capabilities.
What is the difference between single-layer and multilayer RF package substrates?
Single-layer substrates consist of a single layer of material with circuitry patterned on one side. Multilayer substrates consist of multiple layers stacked and interconnected with vias, allowing for more complex circuitry and improved signal integrity.
How are RF package substrates manufactured?
The manufacturing process typically involves steps such as substrate material preparation, patterning, metallization, via formation, surface finishing, inspection, and testing. Advanced techniques such as photolithography, etching, and sintering may be used depending on the substrate material and design requirements.
What are some common surface finishes used for RF package substrates?
Common surface finishes include immersion gold, HASL (Hot Air Solder Leveling), OSP (Organic Solderability Preservatives), and ENIG (Electroless Nickel Immersion Gold). These finishes improve solderability, corrosion resistance, and surface flatness.
How can I ensure the reliability of RF package substrates in my application?
Ensuring proper design, material selection, manufacturing processes, and testing procedures are essential for achieving reliable RF package substrates. Working with reputable suppliers and adhering to industry standards and guidelines can also help ensure reliability.