RF Module Packaging Substrate Manufacturer
RF Module Packaging Substrate Manufacturer,RF module packaging substrates are crucial elements used to package and mount RF components such as chips, circuits, and antennas. These substrates provide the electrical and mechanical properties necessary to support and connect these components, ensuring high performance and reliability in RF systems. Common substrate materials include ceramics, organic substrates, and high-frequency laminates, each offering different electrical, thermal, and mechanical characteristics suitable for various RF applications. The design and manufacturing process of substrates involve considerations such as dielectric constant, loss tangent, thermal conductivity, and dimensional stability to meet the performance requirements of RF systems. High-quality RF module packaging substrates exhibit excellent signal transmission properties, effective thermal management capabilities, and reliable structural stability, providing a solid foundation for stable operation and efficient functioning of RF equipment.
What is an RF Module Packaging Substrate?
An RF (Radio Frequency) module packaging substrate refers to the material or platform used to package and mount RF components such as chips, circuits, antennas, and other electronic elements within a module. This substrate serves as the foundation that supports and connects these components while also providing necessary electrical and mechanical properties for optimal performance in RF applications.
The choice of substrate material is crucial in RF module design as it directly impacts the electrical performance, thermal management, signal integrity, and overall reliability of the module. Common substrate materials for RF modules include ceramics, organic substrates (such as FR4), and specialized high-frequency materials like Rogers, DuPont’s Pyralux, or Taconic.
The packaging substrate is often designed with specific characteristics tailored to the requirements of RF applications, such as low dielectric constant, low loss tangent, high thermal conductivity, and excellent dimensional stability. These properties help minimize signal loss, interference, and heat generation, ensuring efficient operation of the RF module. Additionally, the substrate may incorporate features like microstrip or stripline transmission lines, vias, and grounding structures to facilitate RF signal propagation and minimize electromagnetic interference (EMI).
Overall, the RF module packaging substrate plays a critical role in enabling high-performance, compact, and reliable RF systems for various wireless communication, radar, and sensing applications.
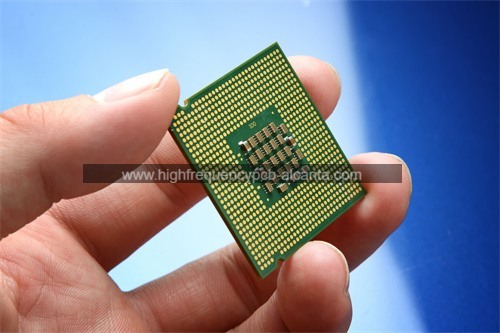
RF Module Packaging Substrate Manufacturer
What are the RF Module Packaging Substrate Design Guidelines?
Designing RF module packaging substrates requires careful consideration of various factors to ensure optimal performance. Here are some key guidelines:
- Substrate Material Selection: Choose a substrate material with suitable electrical, mechanical, and thermal properties for RF applications. Consider factors such as dielectric constant, loss tangent, thermal conductivity, and dimensional stability.
- Dielectric Constant (Dk) and Loss Tangent (Df): Use substrates with low dielectric constant and low loss tangent to minimize signal attenuation and phase distortion, especially at higher frequencies.
- Substrate Thickness: Optimize substrate thickness to achieve desired impedance matching and signal propagation characteristics. Thinner substrates are often preferred for higher frequencies to minimize signal loss and improve performance.
- Transmission Line Design: Design transmission lines (microstrip or stripline) on the substrate carefully to maintain controlled impedance and minimize signal reflections. Use appropriate trace widths, spacing, and impedance matching techniques.
- Grounding and Shielding:Implement proper grounding techniques and shielding structures to minimize electromagnetic interference (EMI) and ensure signal integrity. Design ground planes and shielding structures to provide effective RF isolation and noise suppression.
- Via Design: Design vias carefully to provide electrical connections between different layers of the substrate while minimizing signal loss and impedance mismatch. Consider via placement, size, and via stub reduction techniques to optimize RF performance.
- Thermal Management: Incorporate thermal vias, heat spreaders, or thermal pads to enhance heat dissipation and prevent overheating of RF components. Ensure proper thermal coupling between components and the substrate to maintain reliability and performance under temperature variations.
- RF Component Placement: Optimize the placement of RF components (such as chips, antennas, filters) on the substrate to minimize signal path lengths, reduce parasitic effects, and improve RF performance. Consider layout symmetry and component spacing to mitigate coupling effects and interference.
- Manufacturability and Cost: Consider manufacturability aspects such as substrate fabrication techniques, material availability, and cost-effectiveness. Balance performance requirements with practical considerations to ensure a feasible and cost-efficient design.
- Testing and Validation: Perform thorough testing and validation of the RF module packaging substrate design to verify electrical performance, signal integrity, thermal behavior, and reliability under real-world operating conditions. Use simulation tools, prototype testing, and characterization techniques to validate the design before production.
By following these guidelines, RF module packaging substrates can be designed to meet the stringent requirements of modern RF systems, ensuring high performance, reliability, and compatibility with various wireless communication, radar, and sensing applications.
What is the RF Module Packaging Substrate Fabrication Process?
The fabrication process for RF module packaging substrates involves several steps to create a substrate with the required electrical, mechanical, and thermal properties for RF applications. Here’s an overview of the typical fabrication process:
- Substrate Material Selection: Choose a suitable substrate material based on the requirements of the RF module design, considering factors such as dielectric constant, loss tangent, thermal conductivity, and dimensional stability. Common substrate materials include ceramics, organic substrates (e.g., FR4), and specialized high-frequency materials like Rogers or DuPont’s Pyralux.
- Substrate Preparation: Start with a blank substrate material in the desired size and thickness. Clean the substrate surface to remove any contaminants or residues that could affect subsequent processing steps.
- Surface Preparation: Apply surface treatments or coatings to the substrate material as needed to enhance adhesion, solderability, or electrical properties. This may involve processes such as surface roughening, chemical treatment, or deposition of metal layers (e.g., copper).
- Circuit Patterning: Use photolithography or direct patterning techniques to define the desired circuit patterns on the substrate surface. This typically involves applying a photoresist material, exposing it to UV light through a mask with the circuit pattern, and then developing the resist to remove the exposed areas.
- Circuit Formation: Deposit or etch conductive materials (e.g., copper) onto the substrate surface to form the conductive traces, pads, and interconnects of the RF circuit. This may involve processes such as sputtering, electroplating, or chemical etching, depending on the desired circuit layout and substrate material.
- Dielectric Layer Formation: Deposit or laminate dielectric materials onto the substrate surface to create the insulating layers between conductive traces and components. This may involve processes such as spin coating, chemical vapor deposition (CVD), or lamination with pre-fabricated dielectric sheets.
- Via Formation: Create vias (plated or filled holes) in the substrate to provide electrical connections between different layers of the circuit. This may involve drilling or laser ablation to form the via holes, followed by processes such as electroplating or chemical deposition to fill the vias with conductive material.
- Surface Finish:Apply a surface finish to the substrate to protect the circuitry, enhance solderability, and improve electrical performance. Common surface finishes for RF applications include immersion gold (ENIG), immersion silver, or organic solderability preservatives (OSP).
- Final Inspection and Testing: Conduct thorough inspection and testing of the fabricated substrate to ensure it meets the specified requirements for dimensional accuracy, electrical performance, signal integrity, and reliability. This may involve visual inspection, electrical continuity testing, impedance measurements, and other quality assurance techniques.
- Packaging and Assembly: Once the substrate is fabricated and tested, it can be assembled with RF components (such as chips, antennas, filters) to form the complete RF module. This may involve soldering, wire bonding, or other assembly techniques to mount and interconnect the components on the substrate.
Overall, the fabrication process for RF module packaging substrates requires precision and attention to detail to produce substrates with the necessary properties for optimal RF performance and reliability. Collaboration between designers, engineers, and manufacturing specialists is essential to ensure successful fabrication and integration into RF systems.
How do you manufacture an RF Module Packaging Substrate?
Manufacturing an RF module packaging substrate involves a series of steps to create a substrate with the necessary electrical, mechanical, and thermal properties for RF applications. Here’s a detailed overview of the manufacturing process:
- Design and Layout: Begin by designing the RF module packaging substrate using specialized CAD (Computer-Aided Design) software. This involves defining the circuit layout, component placement, signal traces, vias, and other features according to the design requirements and specifications.
- Material Selection:Choose a substrate material that meets the performance requirements of the RF module, considering factors such as dielectric constant, loss tangent, thermal conductivity, and dimensional stability. Common substrate materials include ceramics, organic substrates (e.g., FR4), and high-frequency materials like Rogers or DuPont’s Pyralux.
- Substrate Preparation: Start with a blank substrate material in the desired size and thickness. Clean the substrate surface to remove any contaminants or residues that could affect subsequent processing steps.
- Surface Preparation: Apply surface treatments or coatings to the substrate material to enhance adhesion, solderability, or electrical properties. This may involve processes such as surface roughening, chemical treatment, or deposition of metal layers (e.g., copper seed layer).
- Circuit Patterning: Use photolithography or direct patterning techniques to define the desired circuit patterns on the substrate surface. This involves applying a photoresist material, exposing it to UV light through a mask with the circuit pattern, and then developing the resist to remove the exposed areas.
- Conductive Layer Deposition: Deposit a thin layer of conductive material (e.g., copper) onto the substrate surface to form the conductive traces, pads, and interconnects of the RF circuit. This can be done using techniques such as sputtering, electroplating, or chemical vapor deposition (CVD).
- Dielectric Layer Formation: Deposit or laminate dielectric materials onto the substrate surface to create the insulating layers between conductive traces and components. This may involve processes such as spin coating, CVD, or lamination with pre-fabricated dielectric sheets.
- Via Formation: Create vias (plated or filled holes) in the substrate to provide electrical connections between different layers of the circuit. This may involve drilling or laser ablation to form the via holes, followed by processes such as electroplating or chemical deposition to fill the vias with conductive material.
- Surface Finish: Apply a surface finish to the substrate to protect the circuitry, enhance solderability, and improve electrical performance. Common surface finishes for RF applications include immersion gold (ENIG), immersion silver, or organic solderability preservatives (OSP).
- Final Inspection and Testing: Conduct thorough inspection and testing of the fabricated substrate to ensure it meets the specified requirements for dimensional accuracy, electrical performance, signal integrity, and reliability. This may involve visual inspection, electrical continuity testing, impedance measurements, and other quality assurance techniques.
- Packaging and Assembly: Once the substrate is fabricated and tested, it can be assembled with RF components (such as chips, antennas, filters) to form the complete RF module. This may involve soldering, wire bonding, or other assembly techniques to mount and interconnect the components on the substrate.
- Quality Control: Implement quality control measures throughout the manufacturing process to identify and address any defects or deviations from the specifications. This includes monitoring process parameters, conducting in-process inspections, and performing final quality checks before shipment.
By following these steps, manufacturers can produce RF module packaging substrates with the required performance characteristics for a wide range of RF applications, including wireless communication, radar, and sensing systems. Collaboration between design, engineering, and manufacturing teams is essential to ensure successful fabrication and integration of RF substrates into electronic devices.
How much should an RF Module Packaging Substrate cost?
The cost of an RF module packaging substrate can vary widely depending on several factors, including the substrate material, fabrication processes, complexity of the design, dimensions, and volume of production. Here are some factors that influence the cost:
- Substrate Material: Different substrate materials have different costs associated with them. Specialized high-frequency materials like Rogers or DuPont’s Pyralux tend to be more expensive than standard FR4 or ceramic substrates.
- Fabrication Processes: The complexity of the fabrication processes required to manufacture the substrate can significantly impact the cost. Processes such as photolithography, deposition, and via formation may add to the overall cost.
- Design Complexity: The complexity of the substrate design, including the number of layers, density of traces, and presence of features like blind or buried vias, can affect the cost of fabrication.
- Dimension and Size: The size and dimensions of the substrate also play a role in determining the cost. Larger substrates typically require more material and may involve additional processing steps, leading to higher costs.
- Volume of Production: Economies of scale apply to substrate fabrication, meaning that higher volumes typically result in lower unit costs. Larger production runs can spread fixed costs across a greater number of units, reducing the cost per substrate.
- Surface Finish and Quality Requirements: The choice of surface finish and any additional quality requirements, such as tight tolerances or specialized testing, can affect the overall cost of the substrate.
- Supplier and Location: The choice of supplier and their location can influence the cost due to differences in labor costs, overheads, and shipping expenses.
Given these factors, it’s challenging to provide a specific cost without knowing the details of the substrate design and production requirements. However, as a rough estimate, the cost of an RF module packaging substrate can range from a few dollars for simpler designs produced in high volumes to several hundred dollars or more for complex, specialized substrates with low production volumes.
For accurate pricing, it’s best to consult with substrate manufacturers or suppliers who can provide quotes based on the specific requirements of your project.
What is the RF Module Packaging Substrate base material?
The base material used for RF module packaging substrates can vary depending on the specific requirements of the application. Some common base materials include:
- Ceramics: Ceramics such as alumina (Al2O3) and aluminum nitride (AlN) are popular choices for RF substrates due to their excellent electrical properties, high thermal conductivity, and stability over a wide temperature range. These materials are well-suited for high-power RF applications and environments where thermal management is critical.
- Organic Substrates: Organic substrates, typically made from materials like FR4 (flame-retardant epoxy), are widely used in RF module packaging due to their cost-effectiveness, ease of fabrication, and compatibility with standard PCB manufacturing processes. While organic substrates may not offer the same level of performance as ceramics at higher frequencies, they are suitable for many RF applications, especially those operating below GHz frequencies.
- High-Frequency Laminates: Specialized high-frequency laminates, such as those made by Rogers Corporation, DuPont, or Taconic, are engineered specifically for RF and microwave applications. These laminates typically consist of woven glass fabric or other reinforcing materials impregnated with high-performance thermoset resins. They offer low dielectric loss, excellent dimensional stability, and consistent electrical properties over a wide frequency range, making them ideal for demanding RF applications.
- Metal Substrates: Metal-based substrates, such as aluminum or copper-clad substrates, are used in certain RF module designs where high thermal conductivity and mechanical strength are required. These substrates can provide effective heat dissipation and thermal management, particularly in high-power RF modules or those operating in harsh environments.
- Flexible Substrates: Flexible substrates, such as polyimide (e.g., Kapton) or polyester films, are used in RF modules that require flexibility or conformability to fit into compact or irregularly shaped spaces. Flexible substrates offer advantages in terms of size, weight, and ease of integration but may have limitations in terms of electrical performance compared to rigid substrates.
The choice of base material for an RF module packaging substrate depends on factors such as operating frequency, power requirements, thermal management needs, mechanical constraints, cost considerations, and manufacturability. Designers typically select the substrate material that best balances these factors to meet the performance, reliability, and cost targets of the RF module.
Which company manufactures RF Module Packaging Substrates?
Several companies manufacture RF module packaging substrates, including Rogers Corporation, DuPont, Taconic Advanced Dielectric Division, Isola Group, and Mitsubishi Electric. These companies offer various types of substrate materials, including high-frequency laminates, ceramic substrates, and flexible substrates, to meet the needs of various RF applications. These substrate materials have different electrical, mechanical, and thermal properties suitable for applications such as RF communication, radar, wireless sensing, and more.
Our company also manufactures RF module packaging substrates. We have advanced manufacturing equipment and a skilled technical team capable of designing and producing various types of substrates to meet our customers’ specific requirements and specifications. Our production processes adhere to international standards, ensuring reliable quality and consistent performance of the substrates. We provide customized solutions tailored to our customers’ design requirements and application scenarios, offering suitable substrate materials, layout designs, and manufacturing processes to ensure optimal performance and cost-effectiveness.
Our substrates find wide applications in various RF modules, including wireless communication, radar systems, antenna arrays, RF front-end modules, and more. Whether for low-frequency or high-frequency, low-power or high-power applications, we can provide suitable solutions. We are committed to providing high-quality products and services to our customers, building long-term partnerships, and advancing the development and application of RF technology together.
What are the 7 qualities of good customer service?
Good customer service is essential for building strong relationships with customers and ensuring satisfaction. Here are seven qualities that contribute to providing excellent customer service:
- Responsiveness: Responding promptly to customer inquiries, concerns, or requests demonstrates attentiveness and shows customers that their needs are valued. Whether it’s answering phone calls, replying to emails, or addressing queries on social media, being responsive is crucial for delivering good customer service.
- Empathy: Understanding and empathizing with customers’ perspectives, feelings, and concerns is key to providing personalized and compassionate service. Empathetic interactions help build trust and rapport with customers, making them feel heard and appreciated.
- Clear Communication: Communicating clearly and effectively with customers is essential for ensuring mutual understanding and resolving issues efficiently. Using plain language, active listening, and providing relevant information helps avoid misunderstandings and fosters positive interactions.
- Problem-Solving Skills: Having strong problem-solving skills enables customer service representatives to address issues and resolve conflicts effectively. Empowered with knowledge and resources, they can identify solutions, offer alternatives, and take proactive steps to meet customers’ needs.
- Professionalism: Maintaining professionalism in all customer interactions, regardless of the situation, reflects positively on the company’s image and reputation. This includes being courteous, respectful, and maintaining a positive attitude even in challenging situations.
- Product Knowledge: Having in-depth knowledge about the company’s products or services enables customer service representatives to provide accurate information, address inquiries, and offer relevant recommendations. A thorough understanding of the offerings helps build credibility and instills confidence in customers.
- Follow-Up and Feedback: Following up with customers after resolving their issues or completing a transaction shows commitment to their satisfaction and helps ensure their needs were met. Additionally, seeking feedback from customers about their experience allows businesses to identify areas for improvement and make necessary adjustments to enhance the quality of service.
By embodying these qualities, businesses can deliver exceptional customer service experiences that foster loyalty, retention, and positive word-of-mouth referrals.
FAQs
What is an RF module packaging substrate?
An RF module packaging substrate is the material or platform used to package and mount RF components such as chips, circuits, antennas, and other electronic elements within a module. It serves as the foundation that supports and connects these components while providing necessary electrical and mechanical properties for optimal RF performance.
What are the common substrate materials used for RF modules?
Common substrate materials for RF modules include ceramics (e.g., alumina, aluminum nitride), organic substrates (e.g., FR4), specialized high-frequency laminates (e.g., Rogers, DuPont’s Pyralux), and metal substrates (e.g., aluminum, copper-clad).
What factors should be considered when selecting an RF module packaging substrate?
Factors to consider include dielectric constant, loss tangent, thermal conductivity, dimensional stability, substrate thickness, transmission line design, grounding and shielding, via design, and thermal management properties.
What is the fabrication process for RF module packaging substrates?
The fabrication process involves substrate material selection, surface preparation, circuit patterning, conductive layer deposition, dielectric layer formation, via formation, surface finish, final inspection and testing, and packaging and assembly.
How much does an RF module packaging substrate cost?
The cost varies depending on factors such as substrate material, fabrication complexity, size, quantity, additional features, supplier, and quality requirements. Costs can range from a few dollars to several hundred dollars per unit.
Which companies manufacture RF module packaging substrates?
Several companies manufacture RF module packaging substrates, including Rogers Corporation, DuPont, Taconic Advanced Dielectric Division, Isola Group, and Mitsubishi Electric, among others.
What are the qualities of a good RF module packaging substrate?
A good RF module packaging substrate should have low dielectric constant and loss tangent, high thermal conductivity, excellent dimensional stability, controlled impedance transmission lines, effective grounding and shielding, optimized via design, and reliable thermal management properties.