RF/microwave PCB Manufacturer
RF/microwave PCB Manufacturer,RF/microwave PCBs (Printed Circuit Boards) are specialized boards designed to handle high-frequency signals effectively. They utilize materials with low dielectric constant and loss tangent, such as PTFE or ceramic, to minimize signal loss and maintain signal integrity at microwave frequencies. These PCBs are meticulously designed with controlled impedance traces, optimized ground planes, and shielding techniques to prevent electromagnetic interference (EMI) and ensure reliable performance in applications like wireless communication, radar systems, and high-speed data transfer. RF/microwave PCBs are crucial components in modern electronics, enabling the efficient transmission and processing of high-frequency signals with minimal attenuation.
What is an RF/Microwave PCB?
An RF/Microwave PCB (Printed Circuit Board) is specifically designed to handle radio frequency (RF) and microwave signals efficiently. Unlike standard PCBs, RF/Microwave PCBs are engineered with materials and structures that minimize signal loss, impedance mismatch, and electromagnetic interference (EMI), which are critical for maintaining signal integrity at high frequencies.
These PCBs typically use specialized substrates like PTFE (Polytetrafluoroethylene) or ceramic materials with low dielectric constants to reduce signal attenuation. They may also incorporate controlled impedance traces, which are essential for matching the impedance of the transmission lines to optimize signal transfer and minimize reflections.
Design considerations for RF/Microwave PCBs include the layout of components, transmission line routing, grounding techniques, and the use of shielding to isolate sensitive RF circuits from external interference. These boards are used extensively in applications such as wireless communication systems (e.g., cellular base stations, WiFi routers), radar systems, satellite communications, and medical devices like MRI machines.
In summary, RF/Microwave PCBs are specialized circuit boards engineered to ensure reliable performance of high-frequency signals, making them indispensable in modern wireless and communication technologies.
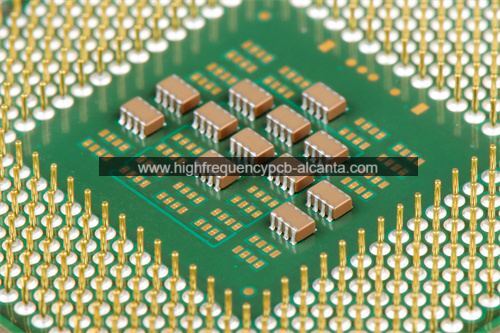
RF/microwave PCB Manufacturer
What are RF/Microwave PCB Design Guidelines?
Designing RF/Microwave PCBs requires adhering to specific guidelines to ensure optimal performance of high-frequency signals. Here are some key design guidelines:
- 1. Substrate Selection: Choose a substrate material with a low dielectric constant (e.g., PTFE, FR-4 with low-loss tangent) to minimize signal loss and dispersion.
- Trace Width and Impedance Control: Design transmission lines with controlled impedance matching the characteristic impedance of the circuit (e.g., 50 ohms for many RF applications). Use trace width and spacing calculations based on the chosen substrate and copper thickness.
- Grounding: Implement a solid ground plane beneath RF traces to minimize noise, provide return paths for signals, and reduce electromagnetic interference (EMI). Avoid interruptions or splits in the ground plane under RF signal paths.
- Component Placement: Position RF components and transmission lines to minimize signal path lengths and avoid sharp bends, which can cause signal reflections and losses. Place high-frequency components closer together to minimize parasitic elements.
- Via Design: Minimize the number of vias in RF paths to reduce signal loss and impedance mismatch. Use through-hole vias with proper sizing and spacing, and avoid stubs that can create unwanted resonances.
- Shielding and Isolation: Use shielding techniques (such as metal cans or grounded enclosures) to isolate sensitive RF circuits from external electromagnetic interference and to prevent RF leakage.
- Routing and Layout: Route RF traces as direct and straight as possible to minimize losses. Use wide, straight traces for high-current RF signals and avoid sharp corners or acute angles which can cause impedance mismatches.
- Decoupling and Filtering: Include appropriate decoupling capacitors and RF filters near power supply pins and sensitive RF circuits to suppress noise and ensure stable operation.
- Thermal Management: Consider heat dissipation for high-power RF components. Ensure adequate thermal relief and heat sinking as needed to maintain reliability and performance.
- Simulation and Testing: Perform electromagnetic simulation (e.g., using tools like HFSS, CST Microwave Studio) to verify signal integrity, impedance matching, and EMI compliance. Test prototypes rigorously using network analyzers and spectrum analyzers to validate performance.
By following these RF/Microwave PCB design guidelines, engineers can achieve reliable, high-performance circuit boards optimized for handling radio frequency and microwave signals effectively in various applications.
What is the RF/Microwave PCB Fabrication Process?
The fabrication process for RF/Microwave PCBs involves several specialized steps to ensure the board meets the stringent requirements for handling high-frequency signals with minimal loss and interference. Here are the key steps involved:
- Substrate Selection: Choose a substrate material suitable for RF/Microwave applications, typically PTFE (Polytetrafluoroethylene), FR-4 with low-loss tangent, or ceramic materials with low dielectric constants. The choice depends on the specific performance requirements of the circuit.
- Material Preparation: Prepare the substrate material by cleaning and applying any necessary surface treatments to ensure proper adhesion of copper layers.
- Copper Cladding: Apply copper foil to both sides of the substrate using lamination or deposition techniques. The copper thickness is critical and usually specified to meet impedance and conductivity requirements.
- Photoresist Application: Apply a photoresist layer over the copper surfaces. This layer will be used to define the circuit pattern.
- Exposure and Development: Use a photomask to expose the desired circuit pattern onto the photoresist layer. Then, develop the exposed photoresist to remove the unwanted areas, leaving behind the pattern of the circuit traces.
- Etching: Submerge the substrate in an etchant solution (e.g., ferric chloride) to selectively remove the exposed copper and define the circuit traces according to the pattern transferred from the photoresist.
- Strip and Clean: Strip off the remaining photoresist and clean the substrate thoroughly to remove any residues from the etching process.
- Surface Finish: Apply a suitable surface finish to the PCB to protect the exposed copper traces from oxidation and ensure good solderability. Common surface finishes include immersion gold, ENIG (Electroless Nickel Immersion Gold), and OSP (Organic Solderability Preservative).
- Drilling: Precision-drill holes (vias) through the PCB where connections between different layers or components are needed. Special care is taken to minimize the formation of stubs that could affect RF performance.
- Plating and Finalization:Plate the vias with copper to ensure electrical continuity between layers if the PCB is multilayered. The PCB may undergo additional processes such as solder mask application, legend printing, and final inspection to ensure it meets all specifications.
- Testing: Perform electrical testing using techniques like continuity testing, impedance testing, and possibly RF testing to verify that the PCB meets the design requirements for signal integrity and performance.
- Quality Control:Conduct final inspections and quality control checks to ensure the PCB meets all specified tolerances and performance criteria before shipment.
Each step in the RF/Microwave PCB fabrication process is critical to producing a high-quality board capable of reliably handling high-frequency signals without significant loss or interference. Advanced manufacturing techniques and stringent quality control are essential to meeting the demanding requirements of RF and microwave applications.
How do you manufacture an RF/Microwave PCB?
Manufacturing an RF/Microwave PCB involves a series of specialized steps tailored to ensure the board meets the stringent requirements for handling high-frequency signals effectively. Here’s a detailed outline of the manufacturing process:
- Substrate Selection: Choose a substrate material suitable for RF/Microwave applications, such as PTFE (Polytetrafluoroethylene), FR-4 with low-loss tangent, or specialized ceramics with low dielectric constants. The material choice depends on factors like frequency, power handling, and environmental conditions.
- Material Preparation: Clean and prepare the substrate material to ensure it is free from contaminants and suitable for receiving copper layers.
- Copper Cladding:Apply copper foil to the substrate through lamination or deposition. The thickness and quality of the copper are crucial for conductivity and impedance control.
- Photoresist Application:Apply a photoresist layer evenly over the copper surfaces of the substrate. This layer will later define the pattern of the circuit traces.
- Exposure and Development: Use a photomask to expose the desired circuit pattern onto the photoresist layer. Then, develop the photoresist to remove the unexposed areas, leaving behind the pattern of the circuit traces.
- Etching: Submerge the substrate in an etchant solution (e.g., ferric chloride) to selectively remove the exposed copper and define the circuit traces according to the pattern transferred from the photoresist.
- Strip and Clean: Strip off the remaining photoresist and thoroughly clean the substrate to remove any etchant residues and ensure the copper traces are pristine.
- Surface Finish: Apply a surface finish to protect the exposed copper traces from oxidation and ensure good solderability. Common surface finishes for RF/Microwave PCBs include immersion gold, ENIG (Electroless Nickel Immersion Gold), and OSP (Organic Solderability Preservative).
- Drilling:Precision-drill holes (vias) through the PCB where connections between different layers or components are required. Care is taken to minimize via stubs, which can affect RF signal integrity.
- Plating and Finalization:Plate the vias with copper to ensure electrical continuity between layers, particularly in multilayer PCBs. Apply solder mask to protect the PCB’s surface except where soldering is required, and add legend printing for component identification.
- Testing: Perform electrical testing using techniques such as continuity testing, impedance testing, and RF testing to verify that the PCB meets the design specifications for signal integrity and performance.
- Quality Control: Conduct final inspections and quality control checks to ensure the PCB meets all specified tolerances, dimensional accuracy, and performance criteria before final approval and shipment.
By meticulously following these steps and utilizing advanced manufacturing techniques, manufacturers can produce RF/Microwave PCBs that deliver reliable performance in high-frequency applications such as wireless communication systems, radar systems, and satellite communications. Each step in the process plays a critical role in ensuring the PCB meets the demanding requirements of RF and microwave technology.
How much should an RF/Microwave PCB cost?
The cost of an RF/Microwave PCB can vary widely depending on several factors:
- Complexity of Design: The more intricate the design with dense routing, controlled impedance requirements, and high-frequency considerations, the higher the cost.
- Materials Used: Specialized substrates like PTFE or ceramic materials with low dielectric constants are more expensive than standard FR-4. High-quality copper foils and surface finishes (e.g., immersion gold) also contribute to cost.
- Layer Count:RF/Microwave PCBs are often multilayered to accommodate complex RF circuitry and impedance matching. More layers generally increase the cost due to additional materials and processing steps.
- Production Volume: Economies of scale apply—larger production runs typically lower the per-unit cost due to amortization of setup and tooling costs.
- Manufacturing Technology: Advanced manufacturing processes such as laser drilling for vias, fine line width control, and impedance testing can increase costs but may be necessary for high-frequency performance.
- Quality Standards and Testing: Additional costs may arise from stringent quality control measures and specialized testing (e.g., RF testing) to ensure the PCB meets performance specifications.
As a rough estimate, RF/Microwave PCBs can range from tens to hundreds of dollars per board, with prices varying significantly based on the above factors. For a more accurate cost estimate, it’s advisable to consult with PCB manufacturers who specialize in RF and microwave applications. Providing detailed specifications and requirements will help them provide a precise quote tailored to your needs.
What is an RF/Microwave PCB base material?
An RF/Microwave PCB base material refers to the substrate on which the circuit traces and components are built. This material is critical for maintaining signal integrity, minimizing losses, and reducing interference in high-frequency applications. Here are some common RF/Microwave PCB base materials:
- PTFE (Polytetrafluoroethylene): Known for its low dielectric constant (typically around 2.1), PTFE is widely used in RF/Microwave PCBs. It offers excellent electrical properties across a broad frequency range, low loss tangent, and stable performance over temperature variations.
- FR-4 with Low-Loss Tangent:Standard FR-4 (Flame Retardant 4) is a common PCB material, but versions with lower loss tangents (around 0.02) are suitable for RF/Microwave applications. FR-4 with low-loss tangent provides good electrical performance at lower frequencies and is more cost-effective compared to PTFE.
- Ceramic Materials: Various ceramic materials, such as alumina (Al2O3) and aluminum nitride (AlN), are used for their superior electrical properties, high thermal conductivity, and stable performance at high frequencies. They have low dielectric constants and low loss tangents, making them ideal for high-power RF applications and demanding environments.
- Rogers Materials: Rogers Corporation manufactures high-performance laminates specifically designed for RF/Microwave applications, such as RO3000 series and RO4000 series. These materials offer low dielectric constants, low loss tangents, and excellent dimensional stability, catering to precise impedance control and high-frequency requirements.
- Other Specialized Materials: Depending on specific performance needs, other materials like liquid crystal polymer (LCP) and polyimide (PI) may be used. These materials offer unique properties such as flexibility, high-temperature resistance, and reduced moisture absorption.
The choice of RF/Microwave PCB base material depends on factors such as frequency range, power handling capability, environmental conditions, and cost considerations. Engineers select the material that best balances performance requirements with manufacturing feasibility to ensure optimal functionality in high-frequency electronic systems.
Which companies manufacture RF/Microwave PCBs?
Many companies specialize in manufacturing RF/Microwave PCBs, offering the expertise and equipment necessary for handling high-frequency signal processing and optimizing circuit performance. Globally recognized manufacturers include Rogers Corporation, Taconic Advanced Dielectric Division, Isola Group from the United States; Schweizer Electronic AG from Germany; Nippon Mektron, Shin-Etsu Chemical from Japan; as well as Kingboard PCB Group, Shenbei Group from China. These companies provide customized RF/Microwave PCB solutions for various markets through the use of high-performance substrate materials (such as PTFE, ceramics), precise manufacturing processes (including controlled impedance design, RF signal simulation), and stringent quality control.
At our company, we also have the capability and experience to manufacture RF/Microwave PCBs. We possess advanced production equipment and a skilled technical team capable of meeting the demands of high-frequency signal processing and circuit performance optimization. We employ advanced material selection and precise process controls to ensure each PCB meets strict technical specifications and performance requirements. Our engineering team has extensive experience in design and simulation, providing professional design advice and technical support to ensure the success of our customers’ projects.
Furthermore, we emphasize personalized customer requirements and prioritize close cooperation and communication with our clients. We are committed to delivering customized solutions that include material selection, impedance control, layout design, and more, tailored to meet specific customer needs, ensuring each RF/Microwave PCB achieves optimal performance and reliability.
In conclusion, our company not only possesses the technical capabilities and manufacturing resources required for RF/Microwave PCB production but also upholds a commitment to high quality and customer-centric service, providing superior products and comprehensive technical support. We are eager to collaborate with customers to drive innovation and advancement in the field of high-frequency electronic technology.
What are the 7 qualities of good customer service?
Good customer service encompasses several key qualities that contribute to a positive experience for customers. Here are seven qualities that are essential:
- Responsiveness: Being prompt and timely in addressing customer inquiries, concerns, and requests. Customers appreciate quick responses that demonstrate attentiveness to their needs.
- Empathy:Understanding and empathizing with the customer’s situation, emotions, and perspective. Empathetic customer service representatives show genuine concern and work to find solutions that meet the customer’s needs.
- Clear Communication: Communicating clearly and effectively to ensure the customer understands the information provided. This includes using simple language, active listening, and avoiding jargon or technical terms that might confuse the customer.
- Knowledgeability: Possessing adequate knowledge about products, services, policies, and procedures. Customers value interacting with service representatives who can provide accurate information and guidance.
- Professionalism: Maintaining a courteous and respectful demeanor in all interactions with customers. Professional behavior includes being patient, maintaining composure, and refraining from arguments or confrontations.
- Problem-Solving Skills: Ability to identify issues, analyze problems, and propose effective solutions. Good customer service involves actively working to resolve customer concerns and ensuring a satisfactory outcome.
- Personalization:Treating each customer as an individual and tailoring interactions based on their preferences and history with the company. Personalized service can include remembering customer preferences, addressing them by name, and offering relevant recommendations.
These qualities collectively contribute to creating a positive customer service experience that builds trust, satisfaction, and loyalty. Companies that prioritize these qualities typically enjoy higher customer retention rates and positive word-of-mouth referrals.
FAQs
What are the applications of RF/Microwave PCBs?
They are used in various applications such as wireless communication systems (e.g., cellular base stations, WiFi routers), radar systems, satellite communications, medical devices (e.g., MRI machines), and aerospace technologies.
How do RF/Microwave PCBs differ from standard PCBs?
RF/Microwave PCBs are designed with materials and layouts optimized for high-frequency signals, whereas standard PCBs may not prioritize characteristics like impedance control and low loss tangent.
What materials are used in RF/Microwave PCBs?
Common materials include PTFE (Polytetrafluoroethylene), FR-4 with low-loss tangent variants, ceramics (e.g., alumina, aluminum nitride), and specialty laminates like those from Rogers Corporation (e.g., RO3000 series).
What design considerations are important for RF/Microwave PCBs?
Important considerations include controlled impedance matching, minimizing signal path lengths, avoiding sharp bends, proper grounding techniques, and using shielding to reduce EMI.
How are RF/Microwave PCBs manufactured?
The manufacturing process involves substrate preparation, copper cladding, photoresist application, exposure and development, etching, surface finish application, drilling vias, plating, finalization, testing, and quality control.
What are the benefits of using RF/Microwave PCBs?
Benefits include enhanced signal integrity, reduced losses at high frequencies, improved reliability in communication systems, and support for high-speed data transmission.
What factors influence the cost of RF/Microwave PCBs?
Cost factors include substrate material choice, complexity of design (e.g., number of layers, impedance control requirements), production volume, and specialized manufacturing techniques.
How can I ensure the performance of RF/Microwave PCBs?
Ensuring performance involves thorough design validation through simulations, adherence to manufacturing standards, rigorous testing (e.g., impedance testing, RF testing), and selecting reputable manufacturers with expertise in RF/Microwave PCB production.