RF High Frequency Substrates Manufacturer
RF High Frequency Substrates Manufacturer,RF High Frequency Substrates are specialized materials used in electronic circuits designed to operate at radio frequencies (RF) and microwave frequencies. These substrates are chosen for their low dielectric constant and low loss tangent properties, such as PTFE (polytetrafluoroethylene), ensuring minimal signal loss and maintaining signal integrity. They feature precise impedance control, high thermal stability, and excellent dimensional stability to support high-frequency performance. RF High Frequency Substrates are crucial in applications like wireless communication systems, radar systems, and satellite communications, where reliable signal transmission and minimal interference are paramount. Their advanced properties contribute to efficient and reliable RF circuit designs in modern electronics.
What is an RF High Frequency Substrate?
An RF (Radio Frequency) high-frequency substrate is a specialized material used in electronic circuits designed to operate at high frequencies, typically in the GHz (Gigahertz) range and beyond. These substrates are crucial in applications such as telecommunications, radar systems, satellite communication, and high-speed data transfer.
The key characteristics of an RF high-frequency substrate include low dielectric constant (εr) and low loss tangent (tan δ). Low εr helps in reducing signal propagation delays and improving signal integrity at high frequencies. Low tan δ ensures minimal energy loss as the signal travels through the substrate material, which is critical for maintaining the efficiency and reliability of RF circuits.
Materials commonly used for RF high-frequency substrates include PTFE (Polytetrafluoroethylene) composites like Rogers RO4000 series, ceramics such as alumina (Al2O3), and certain types of polyimides. These materials offer excellent electrical properties and stability across a wide range of frequencies.
Designers select RF high-frequency substrates based on factors such as the desired operating frequency range, power handling capability, thermal management requirements, and mechanical properties. Advanced manufacturing techniques allow these substrates to be fabricated with precise tolerances and tailored characteristics to meet the stringent demands of modern RF applications.
In summary, RF high-frequency substrates play a pivotal role in the performance of electronic devices operating at high frequencies, ensuring efficient signal transmission, minimal loss, and overall reliability in various critical applications.
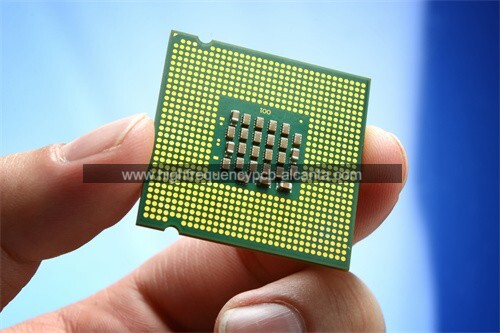
RF High Frequency Substrates Manufacturer
What are RF High Frequency Substrate Design Guidelines?
Designing with RF high-frequency substrates requires careful consideration of several guidelines to ensure optimal performance of electronic circuits operating at GHz frequencies and beyond. Here are some key design guidelines:
- Substrate Material Selection: Choose a substrate material with a low dielectric constant (εr) and low loss tangent (tan δ) suitable for the desired frequency range. Common materials include PTFE-based composites (e.g., Rogers RO4000 series), ceramics (e.g., alumina), and certain polyimides. The material choice affects signal integrity, propagation delay, and power handling capabilities.
- Substrate Thickness: Optimize substrate thickness based on the desired impedance and mechanical stability. Thinner substrates can reduce propagation delay but may affect mechanical robustness and power handling. Thicker substrates offer better mechanical support but can increase signal losses.
- Impedance Control: Maintain consistent impedance across the PCB traces, vias, and components to minimize signal reflections and ensure proper signal integrity. Use controlled impedance routing techniques and match the characteristic impedance of the transmission lines to the substrate and components.
- Component Placement: Place RF components and transmission lines with short and direct paths to minimize parasitic effects and signal losses. Keep high-frequency paths as short as possible to reduce transmission line losses and electromagnetic interference (EMI).
- Grounding and Shielding: Implement effective grounding techniques to minimize ground loops and ensure low impedance paths for return currents. Use solid ground planes and consider incorporating shielding techniques to isolate sensitive RF signals from noise sources.
- Via Design: Optimize via structures for minimal impedance discontinuities and signal losses. Use plated-through holes (PTHs) or vias with controlled impedance characteristics. Avoid stubs and use proper via stitching techniques for connecting ground planes.
- Thermal Management: Consider thermal dissipation requirements, especially for high-power RF applications. Ensure adequate heat sinking and thermal vias to manage heat generated by active components and power amplifiers.
- High-Frequency PCB Layout: Follow best practices for high-frequency PCB layout, such as maintaining signal integrity, minimizing crosstalk, and reducing parasitic capacitance and inductance. Use microstrip or stripline transmission line configurations depending on the application requirements.
- RF Testing and Validation: Perform thorough RF testing and validation of the designed circuit to verify performance parameters such as insertion loss, return loss, and isolation. Use vector network analyzers (VNAs) and other RF measurement equipment to characterize the circuit’s behavior at the intended frequencies.
- Simulation and Prototyping: Utilize electromagnetic simulation tools (e.g., HFSS, ADS) to simulate and optimize the RF circuit design before prototyping. Prototyping allows for real-world validation and fine-tuning of the design based on actual performance measurements.
By adhering to these RF high-frequency substrate design guidelines, designers can achieve reliable and high-performance RF circuits suitable for various applications ranging from telecommunications to aerospace and beyond.
What is the RF High Frequency Substrate Fabrication Process?
Fabricating RF high-frequency substrates involves several critical steps to ensure the material’s electrical properties and dimensional accuracy meet the stringent requirements for GHz-frequency applications. Here’s an overview of the fabrication process:
- Substrate Material Selection: Choose a substrate material based on its dielectric constant (εr), loss tangent (tan δ), thermal properties, and mechanical strength. Common materials include PTFE-based composites (e.g., Rogers RO4000 series), ceramics (e.g., alumina), and polyimides. The material choice depends on the desired frequency range, impedance requirements, and environmental conditions.
- Preparation and Cleaning: Ensure the substrate material is clean and free from contaminants that could affect adhesion and electrical performance. Cleanliness is crucial to achieve consistent dielectric properties and surface finish.
- Circuit Design and Layout: Design the RF circuit layout using specialized CAD software that supports high-frequency design rules. Consider impedance matching, signal integrity, and minimizing parasitic effects such as crosstalk and EMI. Layout considerations include trace width, spacing, via placement, and component orientation.
- Photolithography: Transfer the circuit design onto the substrate using photolithography. This process involves applying a photoresist layer over the substrate, exposing it to UV light through a photomask, and developing to define the circuit pattern. The exposed areas are then ready for further processing.
- Etching: Etch away the exposed copper or other metal layers on the substrate using chemical etchants. This step defines the conductive traces and patterns according to the circuit design. Control over etching parameters such as temperature and etchant concentration ensures precise trace dimensions and uniformity.
- Surface Treatment: Treat the substrate surface to enhance adhesion and promote solderability. Surface treatments may include plasma cleaning, chemical treatments, or applying adhesion promoters depending on the substrate material.
- Plating and Via Formation: Create vias (plated-through holes) to interconnect different layers of the substrate. Via formation involves drilling or laser ablation followed by electroplating or chemical deposition of conductive material (e.g., copper) to establish electrical connections between layers.
- Solder Mask Application: Apply solder mask over the substrate surface to protect the circuit traces, define pad areas for component attachment, and improve insulation between conductive elements. Solder mask is typically applied using a screen-printing process and cured under UV light.
- Surface Finish: Apply a surface finish to the exposed copper pads to prevent oxidation and ensure reliable solder joints during component assembly. Common surface finishes include electroless nickel immersion gold (ENIG), immersion silver, and lead-free hot air solder leveling (HASL).
- Quality Control and Testing: Conduct rigorous quality control tests to verify dimensional accuracy, electrical continuity, and adherence to specifications such as impedance matching and signal integrity. Testing may involve automated optical inspection (AOI), electrical testing, and RF performance characterization using network analyzers.
- Packaging and Delivery: Package the finished RF substrates securely to protect them from handling damage and environmental factors during shipment and storage. Proper packaging ensures the substrates arrive in optimal condition for assembly into electronic devices.
By following these fabrication steps meticulously, manufacturers can produce RF high-frequency substrates that meet the demanding requirements of modern telecommunications, aerospace, and high-speed data communication applications. Each step plays a crucial role in ensuring the substrate’s electrical performance, reliability, and overall quality.
How do you manufacture an RF High Frequency Substrate?
Manufacturing RF high-frequency substrates involves a series of specialized processes to achieve precise electrical characteristics and mechanical stability required for GHz-frequency applications. Here’s a detailed overview of the manufacturing process:
- Substrate Material Selection: Choose a substrate material based on the desired electrical properties such as dielectric constant (εr) and loss tangent (tan δ), as well as mechanical properties like thermal conductivity and dimensional stability. Common materials include PTFE-based composites (e.g., Rogers RO4000 series), ceramics (e.g., alumina), and polyimides.
- Material Preparation and Cutting: Start with raw substrate material in sheet or panel form. The material is inspected for defects and then cut into specific sizes and shapes according to the design requirements of the RF circuit boards.
- Cleaning and Surface Preparation: Clean the substrate material thoroughly to remove contaminants such as oils, dust, and residues that could affect bonding and electrical performance. Surface preparation may involve processes like solvent cleaning, plasma treatment, or chemical etching to improve adhesion.
- Circuit Design and CAD Layout: Design the RF circuit layout using computer-aided design (CAD) software specialized for high-frequency PCB design. This step includes defining trace widths, spacing, via locations, and component placements to optimize signal integrity, impedance matching, and minimize parasitic effects.
- Photolithography: Transfer the circuit pattern onto the substrate using photolithography techniques. This involves applying a photoresist layer over the substrate, exposing it to UV light through a photomask that contains the circuit pattern, and developing the resist to reveal the patterned areas.
- Etching: Etch away the exposed copper or other conductive material on the substrate using chemical etchants. This step defines the conductive traces and pads according to the circuit design. Control over etching parameters such as temperature, agitation, and etchant concentration ensures precise trace dimensions and uniformity.
- Drilling and Via Formation: Drill holes or use laser ablation to create vias (plated-through holes) that connect different layers of the substrate. After drilling, the vias are typically plated with conductive material (e.g., copper) through electroplating or chemical deposition to establish electrical connections between layers.
- Surface Treatment: Apply surface treatments to the substrate to enhance adhesion and solderability. This may include plasma cleaning, chemical treatments, or applying adhesion promoters to ensure components and solder adhere properly to the substrate surface.
- Solder Mask Application: Apply solder mask over the substrate surface to protect the circuit traces, define pad areas for component attachment, and improve insulation between conductive elements. Solder mask is typically applied using screen-printing techniques and cured under UV light.
- Surface Finish Application: Apply a surface finish to the exposed copper pads to prevent oxidation and ensure reliable solder joints during component assembly. Common surface finishes include electroless nickel immersion gold (ENIG), immersion silver, and lead-free hot air solder leveling (HASL).
- Quality Control and Testing: Perform rigorous quality control checks throughout the manufacturing process to verify dimensional accuracy, electrical continuity, and adherence to specifications such as impedance matching and signal integrity. Testing may involve automated optical inspection (AOI), electrical testing, and RF performance characterization using network analyzers.
- Packaging and Delivery:Package the finished RF substrates securely to protect them from handling damage and environmental factors during shipment and storage. Proper packaging ensures the substrates arrive in optimal condition for assembly into electronic devices.
By following these manufacturing steps with precision and attention to detail, manufacturers can produce RF high-frequency substrates that meet the stringent requirements of various applications in telecommunications, aerospace, radar systems, and high-speed data communication. Each step contributes to ensuring the substrate’s electrical performance, reliability, and overall quality necessary for GHz-frequency operation.
How much should an RF High Frequency Substrate cost?
The cost of RF high-frequency substrates can vary significantly depending on several factors:
- Material Type: Different substrate materials have varying costs. For example, PTFE-based laminates (e.g., Rogers RO4000 series) tend to be more expensive than FR4 due to their superior high-frequency performance.
- Substrate Thickness: Thicker substrates may cost more due to increased material usage and possibly more complex manufacturing processes.
- Dielectric Constant and Loss Tangent: Materials with lower dielectric constant (εr) and lower loss tangent (tan δ) generally command higher prices because of their superior RF performance.
- Manufacturing Complexity: Complex PCB designs, multilayer constructions, and specialized features (like controlled impedance, blind/buried vias) can increase fabrication costs.
- Quantity and Order Size: Larger quantities typically reduce the per-unit cost due to economies of scale in manufacturing.
- Quality Standards: Higher quality standards, tighter tolerances, and additional testing requirements can influence the overall cost.
As a rough estimate, RF high-frequency substrates can range from a few dollars per square inch for simpler designs and materials like FR4, to tens of dollars or more per square inch for advanced materials and complex designs. For specialized materials and designs targeting very high frequencies (GHz range and above), costs can be higher.
It’s important for designers and procurement teams to consider these factors when budgeting for RF high-frequency substrates and to obtain quotes from multiple suppliers to ensure competitive pricing. Additionally, costs may vary regionally and based on specific supplier capabilities and certifications.
What is an RF High Frequency Substrate base material?
An RF (Radio Frequency) high-frequency substrate base material refers to the foundational material used in the construction of printed circuit boards (PCBs) designed to operate at high frequencies, typically in the GHz (Gigahertz) range and above. This base material is critical because it directly influences the electrical and mechanical performance of the RF circuit.
Some common RF high-frequency substrate base materials include:
- PTFE-Based Laminates: These are often the preferred choice for RF applications due to their excellent electrical properties, including low dielectric constant (εr) and low loss tangent (tan δ). Examples include the Rogers RO4000 series, which are PTFE (Polytetrafluoroethylene) glass-reinforced laminates.
- Ceramics: Certain ceramic materials, such as alumina (Al2O3), are used for their high thermal conductivity and stable electrical properties over a wide range of temperatures. Ceramics are often chosen for their ability to handle high power and for applications requiring stringent stability.
- Polyimides: Polyimide-based substrates offer good electrical performance combined with flexibility, making them suitable for applications where mechanical flexibility is required alongside high-frequency operation.
- Other Advanced Composites: There are various other composite materials engineered specifically for RF applications, combining elements like woven glass fabric with epoxy resin or other polymers to achieve desired electrical and mechanical properties.
Each of these materials has unique characteristics that make them suitable for different aspects of RF circuit design. Designers select the RF high-frequency substrate base material based on factors such as frequency range, power handling capability, thermal management requirements, mechanical robustness, and cost considerations.
The choice of RF high-frequency substrate base material is crucial as it impacts the circuit’s signal integrity, impedance control, thermal dissipation, and overall reliability in demanding RF applications such as telecommunications, radar systems, satellite communication, and high-speed data transfer.
Which company makes RF High Frequency Substrates?
Many companies produce RF high-frequency substrates, which are crucial in fields such as electronic communication and radar systems. Some well-known manufacturers include Rogers Corporation, TAIYO YUDEN, Panasonic, Epson, Texas Instruments, and DuPont. They produce various RF high-frequency substrate materials suitable for different frequencies and applications.
For example, Rogers Corporation’s RO4000 series substrates are renowned for their excellent electrical performance and stability, ideal for high-frequency and high-speed digital applications. These substrates feature low dielectric constant and low loss tangent, ensuring efficient signal transmission and minimal signal attenuation.
Regarding our company, if we have the manufacturing capabilities and technology, we could engage in the production of RF high-frequency substrates. Typically, this would require advanced PCB manufacturing equipment and technologies such as precise photolithography, chemical etching, drilling, and lamination processes to ensure that the substrates meet the stringent requirements of high-frequency applications.
In our production of RF high-frequency substrates, we could offer the following advantages:
- Advanced Manufacturing Equipment and Processes: We possess advanced PCB manufacturing equipment capable of accurately controlling key parameters during production to ensure the substrates’ electrical properties and mechanical stability meet design requirements.
- Rich Experience and Technical Support: Our team has extensive experience in RF PCB design and manufacturing, providing professional technical support and customized solutions to meet various application needs.
- Quality Control and Certifications: Strict quality control systems ensure the stability and reliability of each batch of products, meeting international standards and specific customer requirements. We may hold certifications such as ISO 9001 for quality management systems and relevant industry standards certifications.
- Flexible Production Capacity: We can adjust production schedules and delivery times flexibly according to customer demands and order volumes to ensure timely delivery and customer satisfaction.
In conclusion, producing RF high-frequency substrates requires extensive manufacturing experience, advanced equipment technology, and a precise understanding of high-frequency circuit design requirements. If our company possesses these capabilities and resources, we could provide high-quality RF substrate products in this competitive market, meeting various customer application requirements effectively.
What are the 7 qualities of good customer service?
Good customer service is characterized by several key qualities that contribute to a positive and satisfactory experience for customers. Here are seven important qualities:
- Responsiveness:Good customer service is prompt and responsive. It involves addressing customer inquiries, issues, or requests in a timely manner. This includes acknowledging customers promptly, listening actively to their concerns, and providing timely solutions or responses.
- Empathy: Empathy involves understanding and sharing the feelings of customers. It’s crucial in customer service as it helps representatives connect with customers on a human level, showing genuine concern and consideration for their needs or challenges.
- Clear Communication: Effective communication is essential for good customer service. This means conveying information clearly and understandably, whether it’s explaining products, policies, or addressing customer questions. Clear communication helps to avoid misunderstandings and ensures customers feel informed and confident.
- Knowledgeability: Good customer service requires representatives to have a deep understanding of the products or services they are supporting. This knowledge allows them to provide accurate information, offer relevant advice, and troubleshoot effectively. Customers value expertise and rely on it to make informed decisions.
- Professionalism: Professionalism encompasses various aspects such as courtesy, respectfulness, and maintaining a positive attitude. It involves treating customers with dignity and demonstrating integrity in interactions. Professional behavior builds trust and leaves a favorable impression on customers.
- Problem-Solving Skills: Dealing with customer issues and resolving problems effectively is a hallmark of good customer service. This involves identifying root causes, proposing viable solutions, and taking proactive steps to ensure customer satisfaction. Strong problem-solving skills help turn potentially negative experiences into positive ones.
- Personalization: Tailoring interactions to individual customer needs and preferences enhances the customer service experience. This includes remembering customer preferences, past interactions, and offering personalized recommendations or solutions. Personalization shows that the company values the customer’s uniqueness and strives to meet their specific requirements.
By embodying these qualities, businesses can foster strong customer relationships, improve loyalty, and differentiate themselves in competitive markets where exceptional customer service is increasingly valued.
FAQs about RF High Frequency Substrates
What are RF high-frequency substrates?
RF high-frequency substrates are specialized materials used in electronic circuits designed to operate at high frequencies, typically in the GHz range and beyond. These substrates offer specific electrical properties to ensure efficient signal transmission and minimal loss.
What are the key properties of RF high-frequency substrates?
Key properties include low dielectric constant (εr), low loss tangent (tan δ), high thermal stability, and controlled impedance characteristics. These properties are critical for maintaining signal integrity and minimizing signal attenuation at high frequencies.
Which materials are commonly used for RF high-frequency substrates?
Common materials include PTFE-based composites (e.g., Rogers RO4000 series), ceramics such as alumina (Al2O3), and certain polyimides. Each material has distinct electrical and mechanical characteristics suited for different RF applications.
What are the typical applications of RF high-frequency substrates?
RF high-frequency substrates are used in telecommunications, radar systems, satellite communication, high-speed data transfer, and other wireless communication technologies where reliable signal transmission at high frequencies is essential.
How do RF high-frequency substrates differ from standard PCB materials?
RF high-frequency substrates are engineered to have lower dielectric loss, better impedance control, and higher frequency stability compared to standard PCB materials like FR4. They are designed to minimize signal degradation and maintain performance at higher frequencies.
What factors should be considered when selecting RF high-frequency substrates?
Factors include the desired operating frequency range, power handling capability, thermal management requirements, mechanical stability, and cost considerations. The choice of substrate material directly impacts the performance and reliability of RF circuits.
Can RF high-frequency substrates be manufactured with specific design requirements?
Yes, manufacturers can produce RF high-frequency substrates with customized design features such as controlled impedance, specialized layer stack-ups, and integrated heat management solutions. Advanced manufacturing techniques allow for precise customization to meet specific application needs.