RF High Frequency Flip Chip Substrate Manufacturer
RF High Frequency Flip Chip Substrate Manufacturer,RF High Frequency Flip Chip Substrates (RF HF FCS) represent the pinnacle of modern engineering in the realm of high-frequency electronics. These substrates are meticulously crafted to meet the demanding requirements of advanced RF applications, where signal integrity, thermal management, and compact design are paramount. By employing innovative flip chip assembly techniques, active components are precisely mounted upside down onto the substrate, minimizing electrical path lengths and optimizing signal propagation. This configuration not only enhances performance but also facilitates efficient heat dissipation, ensuring reliable operation even under extreme conditions. RF HF FCS find wide-ranging applications across wireless communication systems, radar technologies, satellite communications, and beyond, where the need for high-speed data transmission and robust signal processing is imperative. With their superior design, materials, and manufacturing techniques, RF HF FCS epitomize the convergence of cutting-edge technology and engineering excellence in the field of high-frequency electronics.
What is an RF High Frequency Flip Chip Substrate (RF HF FCS)?
An RF High Frequency Flip Chip Substrate (RF HF FCS) is a specialized substrate designed for high-frequency radio frequency (RF) applications, typically used in integrated circuits (ICs) or microelectronic devices.
Here’s a breakdown of its components:
- RF (Radio Frequency): This indicates that the substrate is intended for use in applications that involve transmitting or receiving radio signals, typically in the range of MHz (megahertz) to GHz (gigahertz).
- High Frequency (HF): The term “high frequency” denotes that the substrate is optimized for use in circuits operating at relatively high frequencies, typically in the GHz range and above. These frequencies are commonly used in wireless communication systems, radar systems, satellite communications, and other similar applications.
- Flip Chip: In a flip chip assembly, the active components of an integrated circuit are flipped upside down and mounted directly onto the substrate, allowing for a shorter electrical path and improved performance compared to traditional wire bonding methods. This configuration also enhances heat dissipation and signal integrity.
- Substrate: The substrate serves as the foundation for the integrated circuit, providing mechanical support as well as electrical connections between various components. It is typically made of a material with good electrical properties, such as silicon, gallium arsenide (GaAs), or other semiconductor materials, and may include layers of insulating or conductive materials as needed for the specific application.
Overall, an RF High Frequency Flip Chip Substrate combines the advantages of high-frequency operation, flip chip packaging, and RF-optimized design to meet the demanding requirements of modern RF applications. These substrates are crucial components in the development of advanced wireless communication systems, radar systems, and other RF-based technologies.
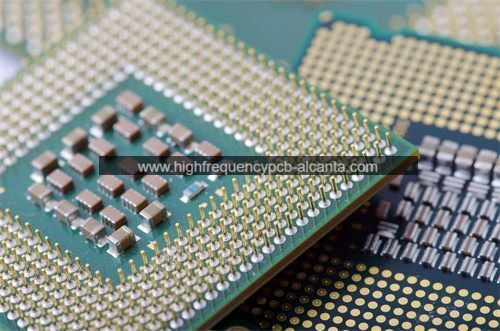
RF High Frequency Flip Chip Substrate Manufacturer
What are the RF HF FCS Design Guidelines?
Designing RF HF FCS involves adhering to specific guidelines to ensure optimal performance in high-frequency applications. Here are some key design guidelines:
- Substrate Material Selection: Choose a substrate material with low dielectric loss and high thermal conductivity to minimize signal attenuation and manage heat dissipation effectively. Common substrate materials for RF HF FCS include ceramic materials like alumina (Al2O3) or specialized high-frequency circuit board materials like Rogers Corporation’s RO4000 series.
- Layer Stackup Design: Design the layer stackup carefully to achieve desired impedance control and signal integrity. This involves determining the number of layers, their thicknesses, and the dielectric constants of each layer. Controlled impedance transmission lines are often used for RF signal routing to minimize reflections and ensure signal integrity.
- Grounding: Implement a solid grounding strategy to minimize ground loops and ensure low ground impedance. Ground vias and stitching vias can be strategically placed to provide low impedance paths to the ground plane.
- RF Signal Routing: Route RF signal traces carefully to minimize signal loss and interference. Use transmission line structures (such as microstrips or coplanar waveguides) for high-frequency signals to maintain controlled impedance and minimize electromagnetic interference (EMI).
- Component Placement:Place RF components and critical components such as amplifiers, oscillators, and filters close to each other to minimize signal path lengths and reduce parasitic effects. This helps improve signal integrity and reduces the risk of unwanted coupling between components.
- Thermal Management: Incorporate thermal vias and thermal pads to efficiently dissipate heat generated by active components. Proper thermal management is crucial for maintaining device reliability and preventing thermal-induced performance degradation.
- EMI Shielding: Implement EMI shielding techniques such as grounded metal layers or shielding cans to prevent electromagnetic interference from affecting sensitive RF circuits.
- Testing and Characterization: Perform thorough testing and characterization of the RF HF FCS to verify its performance meets the design specifications. This includes testing for parameters such as impedance matching, insertion loss, return loss, and isolation.
By following these design guidelines, engineers can develop RF HF FCS that meets the stringent requirements of high-frequency RF applications, ensuring optimal performance and reliability.
What is the RF HF FCS Fabrication Process?
The fabrication process for RF HF FCS involves several steps, each aimed at creating the necessary components and structures to meet the design requirements for high-frequency RF applications. While the specifics can vary depending on the materials and technologies used, here is a general overview of the fabrication process:
- Substrate Preparation: The process begins with preparing the substrate material. This may involve cutting the substrate into the desired size and shape and cleaning it to remove any contaminants that could affect the fabrication process.
- Layer Deposition: Thin film deposition techniques such as sputtering, chemical vapor deposition (CVD), or physical vapor deposition (PVD) are used to deposit conductive and dielectric materials onto the substrate surface. These layers form the basis for the circuitry and interconnects.
- Photolithography:Photolithography is used to define the circuit patterns on the substrate. A layer of photoresist is deposited onto the substrate, exposed to UV light through a photomask, and then developed to remove the exposed areas, leaving behind the desired circuit patterns.
- Etching: Etching processes such as wet chemical etching or dry plasma etching are used to remove the unwanted material from the substrate, leaving behind the patterned conductive and dielectric layers that form the circuitry and interconnects.
- Metallization: Metal layers such as copper or gold are deposited onto the substrate surface using techniques such as sputtering or electroplating. These metal layers serve as the conductive traces and interconnects for the RF circuitry.
- Dielectric Layer Deposition: Additional dielectric layers may be deposited onto the substrate surface to provide insulation between conductive layers and to define the substrate’s electrical properties.
- Via Formation: Vias are openings drilled or etched through the dielectric layers to provide electrical connections between different conductive layers. Via formation may involve processes such as laser drilling or chemical etching.
- Surface Finish: Surface finish processes such as plating or coating may be applied to the substrate to enhance its electrical properties, provide corrosion resistance, or improve solderability.
- Component Attachment: RF components such as amplifiers, filters, and antennas may be attached to the substrate using flip chip bonding or wire bonding techniques. Careful alignment and bonding are essential to ensure proper electrical connections and performance.
- Testing and Quality Control: The fabricated RF HF FCS undergoes rigorous testing and quality control measures to ensure that it meets the specified electrical and mechanical requirements. This may include testing for impedance matching, insertion loss, return loss, and dimensional accuracy.
By following these fabrication steps and employing advanced manufacturing techniques, engineers can produce RF HF FCS with the precise dimensions, electrical properties, and performance characteristics required for high-frequency RF applications.
How do you manufacture RF HF FCS?
Manufacturing RF HF FCS (Radio Frequency High Frequency Flip Chip Substrates) involves a series of sophisticated processes and techniques to create precise circuitry optimized for high-frequency RF applications. Here’s an overview of the manufacturing process:
- Design Phase: The process begins with the design of the RF HF FCS. Engineers use specialized design software to layout the circuitry, including transmission lines, vias, and component placements, while adhering to RF design guidelines.
- Material Selection: Selecting the appropriate substrate material is crucial. Common materials include high-frequency laminates like Rogers Corporation’s RO4000 series or specialized ceramics like alumina (Al2O3). The material choice depends on factors such as dielectric constant, thermal properties, and cost.
- Substrate Preparation: The selected substrate material undergoes preparation, which may involve cutting it into the desired size and shape and cleaning it to remove any contaminants.
- Thin Film Deposition: Thin film deposition techniques are used to deposit conductive and dielectric materials onto the substrate. This step may involve sputtering, chemical vapor deposition (CVD), or physical vapor deposition (PVD) to create the necessary layers for circuitry and interconnects.
- Photolithography: Photolithography is used to define the circuit patterns on the substrate. A layer of photoresist is applied, exposed to UV light through a photomask, and developed to remove the exposed areas, leaving behind the desired circuit patterns.
- Etching: Etching processes are used to remove the unwanted material from the substrate, leaving behind the patterned conductive and dielectric layers. This step may involve wet chemical etching or dry plasma etching.
- Metallization: Metal layers, typically copper or gold, are deposited onto the substrate surface using techniques like sputtering or electroplating. These metal layers serve as the conductive traces and interconnects for the RF circuitry.
- Via Formation: Vias are created to provide electrical connections between different conductive layers. This step may involve drilling or etching holes through the dielectric layers and filling them with conductive material to establish the necessary connections.
- Component Attachment: RF components such as amplifiers, filters, and antennas are attached to the substrate using flip chip bonding or wire bonding techniques. Careful alignment and bonding are essential to ensure proper electrical connections and performance.
- Testing and Quality Control: The manufactured RF HF FCS undergoes rigorous testing and quality control measures to verify its electrical and mechanical properties. This may include testing for impedance matching, insertion loss, return loss, and dimensional accuracy.
Throughout the manufacturing process, precision, cleanliness, and adherence to design specifications are critical to producing RF HF FCS that meets the demanding requirements of high-frequency RF applications. Advanced manufacturing equipment and techniques are often employed to achieve the necessary level of precision and reliability.
How much should RF HF FCS cost?
The cost of RF HF FCS (Radio Frequency High Frequency Flip Chip Substrates) can vary widely depending on several factors, including:
- Complexity: The complexity of the RF HF FCS design, including the number of layers, circuit density, and the intricacy of the circuit patterns, can significantly influence the cost. More complex designs typically require more manufacturing steps and specialized processes, resulting in higher costs.
- Materials: The choice of substrate material and metallization can impact the cost. High-quality materials with specific electrical and thermal properties, such as high-frequency laminates or specialized ceramics, may be more expensive than standard materials.
- Manufacturing Processes: The manufacturing processes used to fabricate RF HF FCS, including thin film deposition, photolithography, etching, metallization, and testing, contribute to the overall cost. Advanced manufacturing techniques and equipment may incur higher operational expenses.
- Volume: The volume of RF HF FCS being produced can affect the unit cost. Larger production runs typically benefit from economies of scale, resulting in lower per-unit costs compared to smaller production runs.
- Customization: Customized features or additional requirements, such as specific impedance matching, thermal management features, or EMI shielding, may increase the cost of RF HF FCS production.
- Supplier: The supplier or manufacturer chosen to produce the RF HF FCS can impact the cost. Different suppliers may offer varying levels of expertise, quality, and pricing structures.
Given these factors, it’s challenging to provide a specific cost estimate for RF HF FCS without knowing the details of the design, materials, manufacturing processes, and volume requirements. It’s advisable to consult with RF engineering experts or suppliers to obtain accurate cost estimates based on your specific needs and specifications.
What is the RF HF FCS base material?
The base material for RF HF FCS (Radio Frequency High Frequency Flip Chip Substrates) is typically chosen based on its electrical properties, thermal characteristics, and suitability for high-frequency RF applications. Common materials used as the base substrate for RF HF FCS include:
- High-Frequency Laminates: High-frequency laminates are specialized materials designed specifically for RF and microwave applications. They typically consist of a reinforced composite substrate with a high dielectric constant and low loss tangent, providing excellent electrical performance at high frequencies. Examples include the RO4000 series from Rogers Corporation and similar products from other manufacturers.
- Specialized Ceramics: Ceramics such as alumina (Al2O3) and aluminum nitride (AlN) are also used as base materials for RF HF FCS. These materials offer high thermal conductivity and excellent electrical insulation properties, making them suitable for high-power RF applications where heat dissipation is critical.
- Semiconductor Substrates: Silicon and other semiconductor materials can be used as the base substrate for RF HF FCS, especially in integrated circuits (ICs) where RF functionality is integrated with other electronic components. Semiconductor substrates offer precise fabrication capabilities and compatibility with standard semiconductor manufacturing processes.
The choice of base material depends on various factors such as the desired electrical properties (dielectric constant, loss tangent, impedance control), thermal management requirements, cost considerations, and compatibility with the manufacturing processes used to fabricate the RF HF FCS. Designers typically select the base material that best balances these factors to achieve the desired performance and reliability for their specific RF application.
Which company manufactures RF HF FCS?
Currently, there are many companies specializing in the production of RF High Frequency Flip Chip Substrates. Some well-known companies include Rogers Corporation in the United States, Panasonic in Japan, and Fujitsu in Germany. These companies have rich experience and advanced manufacturing technologies in the RF high-frequency field, enabling them to produce high-performance RF High Frequency Flip Chip Substrates to meet various high-frequency application requirements.
In our company, we also have a professional team and advanced manufacturing equipment capable of producing high-quality RF High Frequency Flip Chip Substrates. Our manufacturing process is carefully designed and optimized to ensure excellent performance and reliability in high-frequency applications. We use advanced materials and techniques such as high-frequency laminates, precision thin film deposition, photolithography, metallization, and packaging to ensure that our products meet our customers’ requirements.
Our team has extensive experience and expertise in RF design, manufacturing, and testing. We are committed to working closely with customers to understand their needs and provide customized solutions. Whether customers require simple RF High Frequency Flip Chip Substrates or complex high-integration packages, we can deliver high-quality, high-performance products and ensure timely delivery.
In summary, while there are many companies producing RF High Frequency Flip Chip Substrates in the market, our company distinguishes itself through a professional team, advanced technology, and a quality assurance system, enabling us to provide high-quality, customized products to meet various customer needs in the high-frequency field.
What are the 7 qualities of good customer service?
Good customer service is characterized by several key qualities that help foster positive relationships with customers and enhance their overall experience. Here are seven qualities of good customer service:
- Responsiveness: Good customer service involves being responsive to customer inquiries, requests, and concerns in a timely manner. This includes promptly answering phone calls, responding to emails, and addressing customer questions or issues efficiently.
- Empathy: Empathy is essential in understanding and acknowledging the customer’s perspective and feelings. Good customer service representatives listen attentively to customers, express empathy for their concerns, and demonstrate a genuine desire to help resolve their issues.
- Clear Communication: Clear communication is vital for effective customer service interactions. Customer service representatives should communicate information clearly and concisely, using language that is easy for customers to understand. They should also ensure that customers fully comprehend any solutions or actions being proposed.
- Knowledgeability: Good customer service requires having a thorough understanding of the products or services being offered. Customer service representatives should be knowledgeable about their company’s offerings, policies, and procedures so they can provide accurate information and assistance to customers.
- Problem-Solving Skills: Effective problem-solving skills are crucial for resolving customer issues and addressing their concerns. Customer service representatives should be resourceful and proactive in finding solutions to customer problems, taking ownership of issues, and following through until the customer’s needs are met.
- Professionalism:Professionalism entails maintaining a courteous and respectful demeanor at all times when interacting with customers. Customer service representatives should exhibit patience, politeness, and professionalism, even in challenging or stressful situations.
- Follow-Up: Good customer service doesn’t end with resolving the immediate issue—it also involves following up with customers to ensure their satisfaction and address any lingering concerns. Following up demonstrates a commitment to customer care and helps build trust and loyalty over time.
By embodying these qualities, organizations can deliver exceptional customer service experiences that leave a positive impression on customers and contribute to long-term customer satisfaction and loyalty.
FAQs
What are RF High Frequency Flip Chip Substrates?
RF High Frequency Flip Chip Substrates are specialized substrates designed for high-frequency radio frequency (RF) applications. They typically involve flip chip assembly techniques, where active components are flipped upside down and mounted directly onto the substrate.
What are the advantages of using RF High Frequency Flip Chip Substrates?
RF High Frequency Flip Chip Substrates offer several advantages, including shorter electrical paths, improved signal integrity, enhanced thermal management, and better performance at high frequencies compared to traditional wire bonding methods.
What materials are used in RF High Frequency Flip Chip Substrates?
Common materials used in RF High Frequency Flip Chip Substrates include high-frequency laminates, specialized ceramics, and semiconductor substrates. These materials are chosen for their electrical properties, thermal conductivity, and compatibility with high-frequency RF applications.
What are some typical applications of RF High Frequency Flip Chip Substrates?
RF High Frequency Flip Chip Substrates are used in a wide range of applications, including wireless communication systems, radar systems, satellite communications, automotive radar, aerospace and defense electronics, and high-speed data transmission.
What design considerations are important for RF High Frequency Flip Chip Substrates?
Design considerations for RF High Frequency Flip Chip Substrates include impedance control, signal routing, grounding, thermal management, EMI shielding, and component placement. These factors are crucial for optimizing performance and reliability in high-frequency RF applications.
How are RF High Frequency Flip Chip Substrates manufactured?
The manufacturing process for RF High Frequency Flip Chip Substrates involves several steps, including substrate preparation, layer deposition, photolithography, etching, metallization, via formation, component attachment, and testing. Advanced manufacturing techniques and equipment are used to achieve precise fabrication and ensure high-quality products.
What are some key quality metrics for RF High Frequency Flip Chip Substrates?
Key quality metrics for RF High Frequency Flip Chip Substrates include impedance matching, insertion loss, return loss, isolation, thermal performance, dimensional accuracy, and reliability under high-frequency operating conditions.