RF Antenna Substrate Manufacturer
RF Antenna Substrate Manufacturer,RF antenna substrates are crucial materials used in manufacturing radio frequency antennas, typically in the form of printed circuit boards (PCBs). These substrates possess specific dielectric constants, loss factors, and thermal properties, which are vital for antenna performance. Designing and manufacturing RF antenna substrates involve considerations such as frequency range, impedance matching, radiation efficiency, and mechanical stability. Common substrate materials include FR-4, Rogers RO4003C, and PTFE-based materials, each with different characteristics suitable for various frequency ranges and performance requirements. The fabrication process typically includes steps such as copper foil lamination, photolithography patterning, chemical etching, photoresist removal, surface treatment, and more. With precise manufacturing and optimized design, RF antenna substrates can achieve excellent signal transmission performance, suitable for applications in wireless communication, radar, satellite communication, and other fields.
What is an RF Antenna substrate (PCB)?
An RF (Radio Frequency) antenna substrate, often implemented as a PCB (Printed Circuit Board), is the material on which the antenna elements are fabricated or mounted. This substrate is crucial because it determines many of the antenna’s performance characteristics, including its impedance, bandwidth, radiation efficiency, and more.
The choice of substrate material depends on various factors such as the frequency of operation, mechanical constraints, cost considerations, and manufacturing processes. Common substrate materials for RF antennas include FR-4 (Flame Retardant 4), Rogers RO4003C, RT/Duroid, and various other types of laminates.
These substrates are carefully engineered to have specific dielectric constants, loss tangents, and thermal properties to ensure optimal antenna performance. For instance, materials with low dielectric constants are often preferred for high-frequency applications to minimize signal loss and achieve better impedance matching.
In summary, an RF antenna substrate (PCB) forms the foundation upon which the antenna is built, influencing its performance and characteristics significantly.
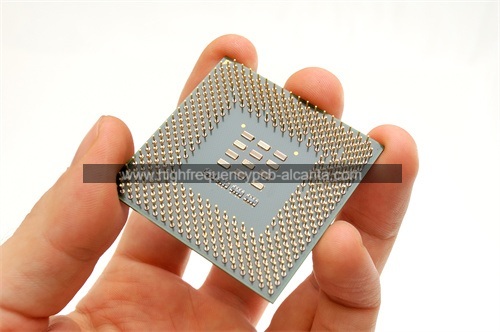
RF Antenna substrate Manufacturer
What are the RF Antenna substrate (PCB) Design Guidelines?
Designing RF antennas on PCB substrates requires careful consideration of various factors to achieve optimal performance. Here are some general guidelines for RF antenna substrate (PCB) design:
- Substrate Selection: Choose a substrate material with appropriate dielectric properties for the frequency of operation. Low-loss substrates with stable dielectric constants over frequency and temperature variations are preferred.
- Dielectric Constant (εr): The dielectric constant of the substrate affects the antenna’s electrical length and impedance. Ensure consistency in the dielectric constant across the substrate to maintain antenna performance.
- Substrate Thickness: The substrate thickness influences the antenna’s radiation pattern, impedance, and bandwidth. Thinner substrates typically offer broader bandwidth, while thicker substrates can provide mechanical stability.
- Substrate Loss Tangent (tan δ): Minimize substrate loss tangent to reduce signal attenuation and improve antenna efficiency, especially at higher frequencies.
- Ground Plane: A solid and continuous ground plane beneath the antenna elements helps to enhance radiation efficiency, reduce impedance variations, and minimize coupling with nearby objects.
- Antenna Placement: Optimal positioning of the antenna on the PCB can affect radiation pattern, impedance matching, and isolation from other components. Avoid placing the antenna near metallic or absorbing materials that could degrade performance.
- Trace Width and Length: Design antenna traces with appropriate widths and lengths to achieve the desired impedance matching and radiation characteristics. Use transmission line theory to calculate trace dimensions for specific impedance requirements.
- Feedline Design: Design feedlines to minimize losses and impedance mismatches. Use controlled impedance transmission lines, such as microstrips or coplanar waveguides, to connect the antenna to the RF circuitry.
- Copper Thickness and Surface Finish: Ensure uniform copper thickness and select appropriate surface finishes to prevent signal degradation and ensure consistent electrical performance.
- Environmental Considerations: Consider environmental factors such as temperature, humidity, and mechanical stress that could affect the substrate material’s properties and, consequently, the antenna’s performance.
- Simulation and Testing: Use electromagnetic simulation software and prototyping to validate the antenna design and optimize performance before finalizing the PCB layout. Conduct thorough testing to verify the antenna’s electrical characteristics and radiation pattern.
By following these guidelines and incorporating best practices in RF antenna substrate (PCB) design, you can develop antennas with improved performance, efficiency, and reliability for various wireless communication applications.
What is the RF Antenna substrate (PCB) Fabrication Process?
The fabrication process for RF antenna substrates on PCBs involves several steps to create the desired antenna structure with precise dimensions and electrical properties. Here’s an overview of the typical RF antenna substrate fabrication process:
- Design and Layout: Begin by designing the RF antenna layout using specialized software tools. This involves determining the antenna geometry, dimensions, trace widths, and other parameters based on the desired operating frequency, impedance matching requirements, and mechanical constraints.
- Material Selection: Choose a suitable substrate material based on the antenna design specifications, such as dielectric constant, loss tangent, thickness, and mechanical properties. Common substrate materials for RF antennas include FR-4, Rogers RO4003C, and various high-frequency laminates.
- Preparation of Substrate: Prepare the substrate material by cleaning it to remove any contaminants and ensuring a smooth surface for the subsequent fabrication steps. This may involve processes such as chemical cleaning or plasma treatment.
- Copper Cladding: Apply a layer of copper foil to one or both sides of the substrate material using lamination or deposition techniques. The thickness of the copper layer should be carefully controlled to meet the design requirements for conductivity and impedance.
- Photoresist Application: Coat the copper-clad substrate with a layer of photoresist material. The photoresist acts as a mask for the subsequent etching process, allowing the desired antenna pattern to be transferred onto the copper layer.
- Exposure and Development: Use photolithography techniques to expose the photoresist layer to UV light through a photomask, which defines the antenna pattern. After exposure, the substrate is developed to remove the unexposed photoresist, leaving behind the patterned areas for the antenna traces.
- Etching: Etch away the unprotected copper areas using chemical etchants such as ferric chloride or ammonium persulfate. The etching process removes the exposed copper, leaving behind the desired antenna traces on the substrate surface.
- Strip and Clean: Remove the remaining photoresist and any etching residues from the substrate through stripping and cleaning processes. This ensures the substrate surface is free from contaminants and residues that could affect antenna performance.
- Surface Finish: Apply a surface finish to the substrate to protect the copper traces and provide solderability for component attachment. Common surface finishes include HASL (Hot Air Solder Leveling), ENIG (Electroless Nickel Immersion Gold), and OSP (Organic Solderability Preservatives).
- Final Inspection: Conduct a thorough inspection of the fabricated RF antenna substrate to ensure dimensional accuracy, electrical continuity, and absence of defects. Use visual inspection, electrical testing, and possibly microscopic analysis to verify the quality of the substrate.
- Integration and Testing: Integrate the fabricated RF antenna substrate into the overall PCB assembly, including any additional components and circuitry. Perform functional testing and characterization to verify the antenna’s performance, radiation pattern, impedance matching, and other electrical parameters.
By following these steps, manufacturers can fabricate RF antenna substrates on PCBs with precise dimensions, accurate antenna patterns, and consistent electrical properties, ensuring reliable performance in various wireless communication applications.
How do you manufacture an RF Antenna substrate (PCB)?
Manufacturing an RF antenna substrate on a PCB involves a series of steps to create the desired antenna structure with precise dimensions and electrical properties. Here’s a general overview of the manufacturing process:
- Design and Layout: Begin by designing the RF antenna layout using specialized software tools. This involves determining the antenna geometry, dimensions, trace widths, and other parameters based on the desired operating frequency, impedance matching requirements, and mechanical constraints.
- Material Selection: Choose a suitable substrate material based on the antenna design specifications, such as dielectric constant, loss tangent, thickness, and mechanical properties. Common substrate materials for RF antennas include FR-4, Rogers RO4003C, and various high-frequency laminates.
- Panel Preparation: Prepare a panel of the chosen substrate material by cutting it to the desired size. Panels may be prepared in large sheets to accommodate multiple antenna designs or smaller batches for specific applications.
- Copper Deposition: Apply a layer of copper foil to one or both sides of the substrate material using lamination or deposition techniques. The thickness of the copper layer should be carefully controlled to meet the design requirements for conductivity and impedance.
- Photoresist Application: Coat the copper-clad substrate with a layer of photoresist material. The photoresist acts as a mask for the subsequent etching process, allowing the desired antenna pattern to be transferred onto the copper layer.
- Exposure and Development: Use photolithography techniques to expose the photoresist layer to UV light through a photomask, which defines the antenna pattern. After exposure, the substrate is developed to remove the unexposed photoresist, leaving behind the patterned areas for the antenna traces.
- Etching: Etch away the unprotected copper areas using chemical etchants such as ferric chloride or ammonium persulfate. The etching process removes the exposed copper, leaving behind the desired antenna traces on the substrate surface.
- Strip and Clean: Remove the remaining photoresist and any etching residues from the substrate through stripping and cleaning processes. This ensures the substrate surface is free from contaminants and residues that could affect antenna performance.
- Surface Finish: Apply a surface finish to the substrate to protect the copper traces and provide solderability for component attachment. Common surface finishes include HASL (Hot Air Solder Leveling), ENIG (Electroless Nickel Immersion Gold), and OSP (Organic Solderability Preservatives).
- Final Inspection:Conduct a thorough inspection of the manufactured RF antenna substrate to ensure dimensional accuracy, electrical continuity, and absence of defects. Use visual inspection, electrical testing, and possibly microscopic analysis to verify the quality of the substrate.
- Integration and Testing: Integrate the manufactured RF antenna substrate into the overall PCB assembly, including any additional components and circuitry. Perform functional testing and characterization to verify the antenna’s performance, radiation pattern, impedance matching, and other electrical parameters.
By following these manufacturing steps, manufacturers can produce RF antenna substrates on PCBs with precise dimensions, accurate antenna patterns, and consistent electrical properties, ensuring reliable performance in various wireless communication applications.
How much should an RF Antenna substrate (PCB) cost?
The cost of an RF antenna substrate (PCB) can vary significantly depending on several factors such as:
- Material: The choice of substrate material can have a substantial impact on the cost. Higher-performance materials with superior electrical properties may be more expensive than standard FR-4 substrates.
- Size and Complexity: Larger or more complex antenna designs may require additional manufacturing steps, materials, and labor, which can contribute to higher costs.
- Quantity: Economies of scale often apply in PCB manufacturing, meaning that larger production runs typically result in lower per-unit costs. Ordering larger quantities can lead to reduced costs per PCB.
- Manufacturing Process: The specific fabrication techniques and processes used can influence the cost. Advanced processes such as multilayer PCB fabrication, controlled impedance routing, and high-precision manufacturing may incur additional expenses.
- Surface Finish and Features: Surface finish options, such as ENIG or immersion tin, can affect the cost. Additionally, features like blind vias, buried vias, and controlled impedance traces may increase the manufacturing complexity and cost.
- Lead Time: Shorter lead times often come with a premium cost, while longer lead times may offer cost savings.
As a rough estimate, the cost of a basic RF antenna substrate (PCB) could range from a few dollars for a simple design to tens or hundreds of dollars for more complex or specialized requirements. For precise pricing, it’s best to consult with PCB manufacturers and provide them with detailed specifications of your RF antenna design and manufacturing needs. They can provide quotes based on your specific requirements, quantities, and desired lead times.
What is RF Antenna substrate (PCB) base material?
The RF antenna substrate (PCB) base material refers to the material upon which the RF antenna is fabricated or mounted. This material is chosen based on its dielectric properties, mechanical characteristics, and suitability for RF applications. Common base materials for RF antenna substrates include:
- FR-4 (Flame Retardant 4): FR-4 is a widely used substrate material for PCBs due to its affordability, availability, and good electrical insulation properties. However, it may not be ideal for high-frequency RF applications due to its relatively high dielectric constant and loss tangent.
- Rogers RO4003C: Rogers RO4003C is a high-frequency laminate specifically designed for RF and microwave applications. It offers excellent electrical performance with low dielectric loss and stable dielectric constant over a wide frequency range.
- RT/Duroid: RT/Duroid is another high-frequency laminate known for its low dielectric constant, low loss tangent, and high thermal conductivity. It is suitable for demanding RF and microwave applications where signal integrity and performance are critical.
- PTFE (Polytetrafluoroethylene) Based Materials: PTFE-based materials, such as Teflon, offer exceptional electrical properties with low dielectric constant, low loss tangent, and high temperature stability. They are often used in high-frequency and high-power RF applications.
- Ceramic Substrates: Ceramic substrates, such as alumina (Al2O3) or aluminum nitride (AlN), provide excellent thermal conductivity and mechanical stability. They are suitable for RF applications requiring high power handling and temperature resistance.
- Liquid Crystal Polymer (LCP): LCP substrates offer good electrical properties with low dielectric constant and low loss tangent. They are often used in flexible or conformal RF antenna designs.
The choice of RF antenna substrate base material depends on various factors such as the operating frequency, power requirements, mechanical constraints, and cost considerations. Designers typically select the substrate material that best balances these factors to achieve optimal antenna performance for a specific application.
Which company makes RF Antenna substrates (PCBs)?
Many companies manufacture RF antenna substrates, including major PCB manufacturers and companies specializing in high-frequency applications. Some well-known RF antenna substrate manufacturers include Rogers Corporation, Shengyi Technology, Isola Group, Taconic Advanced Dielectric Division, Park Electrochemical Corp, and others. These companies offer various types of substrate materials suitable for RF antenna designs with different frequency, power, and performance requirements.
Our company also manufactures RF antenna substrates. We have advanced manufacturing equipment and technology, as well as an experienced engineering team capable of meeting various customer needs. We provide a range of substrate material options, including common ones like FR-4, Rogers RO4003C, PTFE, as well as custom substrate material options. Whether it’s a simple single-layer antenna or a complex multi-layer antenna design, we can provide high-quality, precise RF antenna substrates.
Our production process strictly follows quality management systems, and our engineering team conducts rigorous quality control and inspection at every stage to ensure products meet customer specifications and requirements. We also offer fast delivery and excellent customer service to meet urgent customer needs and provide technical support.
In summary, our company has the capability to produce high-quality RF antenna substrates and is willing to customize various types of substrate materials and designs according to customer requirements. We are committed to providing reliable solutions to customers and establishing long-term, stable partnerships.
What are the 7 qualities of good customer service?
Good customer service is essential for building and maintaining positive relationships with customers. Here are seven qualities of good customer service:
- Responsiveness: Good customer service involves promptly addressing customer inquiries, concerns, and requests. Responding to customers in a timely manner demonstrates attentiveness and a commitment to meeting their needs.
- Empathy: Empathy is the ability to understand and share the feelings of others. Good customer service representatives show empathy by listening actively to customers, acknowledging their emotions, and demonstrating understanding and compassion.
- Communication Skills: Effective communication is crucial for delivering excellent customer service. Clear and concise communication helps customers understand information, resolve issues efficiently, and feel valued and respected.
- Problem-solving Ability: Good customer service involves being proactive and resourceful in solving customer problems and addressing their issues. Customer service representatives should be equipped with problem-solving skills to identify solutions and resolve issues effectively.
- Product Knowledge: Having a deep understanding of the products or services offered is essential for providing helpful and accurate assistance to customers. Customer service representatives should be knowledgeable about product features, benefits, and usage to answer questions and provide guidance.
- Professionalism: Professionalism encompasses maintaining a courteous, respectful, and positive attitude when interacting with customers. Good customer service representatives exhibit professionalism in their demeanor, language, and behavior, fostering trust and confidence in the company.
- Follow-up and Follow-through: Following up with customers after resolving their issues or fulfilling their requests demonstrates commitment and dedication to their satisfaction. Good customer service includes following through on promises, ensuring that customers’ needs are fully addressed, and maintaining ongoing communication to ensure satisfaction.
By embodying these qualities, businesses can deliver exceptional customer service experiences that foster loyalty, satisfaction, and positive word-of-mouth recommendations.
FAQs (Frequently Asked Questions)
What is an RF antenna substrate (PCB)?
An RF antenna substrate, also known as an RF PCB, is the material on which the antenna elements are fabricated or mounted. It plays a crucial role in determining the antenna’s performance characteristics, such as impedance, bandwidth, and radiation efficiency.
What are common substrate materials used for RF antennas?
Common substrate materials for RF antennas include FR-4 (Flame Retardant 4), Rogers RO4003C, RT/Duroid, PTFE (Polytetrafluoroethylene) based materials, ceramic substrates, and liquid crystal polymer (LCP).
Why is substrate selection important for RF antennas?
Substrate selection is critical because it affects the antenna’s electrical properties, such as dielectric constant and loss tangent, which in turn influence impedance matching, signal propagation, and overall performance.
What are the key design considerations for RF antenna substrates?
Design considerations include substrate material selection, dielectric constant, substrate thickness, ground plane configuration, trace width and length, feedline design, environmental factors, and simulation/testing for performance validation.
How are RF antenna substrates fabricated?
The fabrication process typically involves steps such as substrate preparation, copper cladding, photoresist application, exposure and development, etching, stripping and cleaning, surface finish application, and final inspection.
What factors affect the cost of RF antenna substrates?
The cost of RF antenna substrates can vary based on factors such as substrate material, size and complexity of the design, quantity ordered, manufacturing process used, surface finish options, and lead time requirements.
Where can RF antenna substrates be sourced?
RF antenna substrates can be sourced from various suppliers, including PCB manufacturers, distributors, and specialized RF material suppliers. It’s essential to select a reputable supplier that can meet your specific requirements for substrate material, performance, and quality.