Radio Frequency Cavity PCB Manufacturer
Radio Frequency Cavity PCB Manufacturer,Radio Frequency (RF) cavity PCBs are specialized printed circuit boards designed for high-frequency applications. Featuring a unique cavity structure within the substrate, these PCBs offer enhanced RF performance by optimizing signal integrity, minimizing electromagnetic interference (EMI), and improving thermal management. RF cavity PCBs utilize materials with low dielectric loss and high thermal conductivity, such as PTFE (Teflon) or ceramic-based substrates, to ensure optimal RF properties. The cavity structure acts as a shield, providing electromagnetic isolation for components and traces, while also exhibiting resonant behavior at specific frequencies. This resonant property enhances RF circuit performance, making RF cavity PCBs ideal for applications like wireless communication systems, radar systems, RF amplifiers, and RF filters. By leveraging advanced design techniques, precise manufacturing processes, and rigorous testing methodologies, RF cavity PCBs deliver reliable and high-performance solutions for demanding RF applications.
What is a Radio Frequency Cavity PCB?
A Radio Frequency (RF) cavity PCB, also known as a cavity-backed PCB or cavity resonator PCB, is a specialized type of printed circuit board (PCB) used in RF applications. It incorporates a cavity structure into the PCB design to improve the performance of RF circuits.
Here’s how it works:
- Cavity Structure:The PCB contains a cavity, which is essentially an empty space or void within the PCB substrate. This cavity is typically formed by etching away material from the inner layers of the PCB, leaving behind a well-defined space.
- RF Shielding: The cavity acts as a shield, providing electromagnetic isolation for components and traces on the PCB. This shielding helps prevent electromagnetic interference (EMI) from external sources and reduces crosstalk between components on the PCB.
- Resonant Behavior: The cavity can also exhibit resonant behavior at specific frequencies determined by its dimensions and geometry. By carefully designing the cavity’s dimensions, engineers can create a resonant structure that enhances the performance of RF circuits operating at certain frequencies.
- Improved Performance: The presence of the cavity and its resonant properties can improve various aspects of RF circuit performance, such as signal integrity, impedance matching, and radiation characteristics.
RF cavity PCBs are commonly used in applications such as wireless communication systems, radar systems, RF amplifiers, and RF filters, where maintaining signal integrity and minimizing interference are critical. They are designed using specialized simulation and modeling tools to optimize their performance for specific RF frequencies and applications.
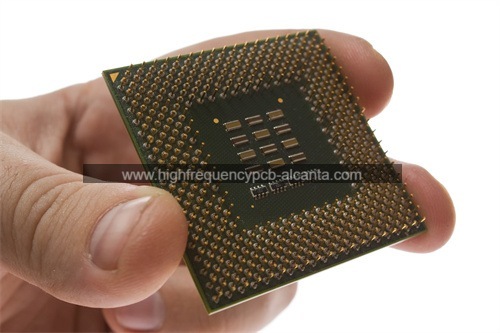
Radio Frequency Cavity PCB Manufacturer
What are the Radio Frequency Cavity PCB Design Guidelines?
Designing a Radio Frequency (RF) cavity PCB requires careful consideration of various factors to ensure optimal performance. Here are some general guidelines:
- Cavity Geometry: Determine the dimensions and shape of the cavity based on the desired resonant frequency and the requirements of the RF circuit. The cavity dimensions should be carefully calculated to achieve the desired resonance and to provide sufficient space for components and traces.
- Substrate Material: Choose a PCB substrate material with appropriate dielectric properties for RF applications. Low-loss dielectric materials, such as PTFE (Teflon) or ceramic, are commonly used to minimize signal attenuation and maintain signal integrity at high frequencies.
- Grounding: Implement a solid ground plane on the PCB to provide electromagnetic shielding and to establish a low-impedance ground reference. Ensure that the cavity is properly connected to the ground plane to minimize RF interference and to maintain signal integrity.
- Component Placement: Place RF components, such as amplifiers, filters, and antennas, within the cavity to take advantage of the shielding and resonant properties. Position components to minimize signal path lengths and impedance mismatches, and ensure that they are adequately isolated from each other to avoid interference.
- Transmission Lines: Design transmission lines, such as microstrip or stripline, with appropriate impedance matching and controlled impedance to minimize signal reflections and losses. Avoid sharp bends or discontinuities in transmission lines, as they can introduce impedance variations and signal distortion.
- Cavity Walls: Maintain a sufficient distance between cavity walls and RF traces to minimize coupling and interference. Use electromagnetic simulation tools to analyze the electromagnetic fields within the cavity and optimize the layout accordingly.
- Feed and Coupling: Design feed structures, such as feedlines or coaxial connectors, to introduce RF signals into the cavity and to couple energy to/from the cavity efficiently. Use impedance matching techniques to ensure maximum power transfer and minimize signal loss.
- Thermal Management: Consider thermal management techniques, such as heat sinks or thermal vias, to dissipate heat generated by RF components within the cavity. Ensure that thermal considerations do not compromise RF performance.
- Testing and Validation:Perform thorough testing and validation of the RF cavity PCB design using RF test equipment, such as network analyzers and spectrum analyzers. Verify that the PCB meets performance specifications and operates correctly at the desired frequencies.
By following these guidelines and leveraging advanced simulation and modeling techniques, engineers can design RF cavity PCBs that meet the requirements of demanding RF applications with high performance and reliability.
What is the Radio Frequency Cavity PCB Fabrication Process?
The fabrication process for a Radio Frequency (RF) cavity PCB involves several steps to create a PCB with a cavity structure optimized for RF applications. Here’s a general overview of the fabrication process:
- Design and Layout: Begin by designing the RF cavity PCB layout using PCB design software. This includes determining the dimensions and shape of the cavity, placing RF components and traces, and designing transmission lines and grounding structures. The layout should be optimized for RF performance, considering factors such as signal integrity, impedance matching, and electromagnetic shielding.
- Material Selection: Choose a suitable PCB substrate material with low dielectric loss and high-frequency performance, such as PTFE (Teflon) or ceramic-based materials. Select the appropriate thickness for the substrate based on the desired RF frequency and impedance requirements.
- Cavity Formation: Use specialized fabrication techniques, such as mechanical milling or chemical etching, to create the cavity structure within the PCB substrate. This involves removing material from the inner layers of the PCB to form the cavity while leaving behind a well-defined cavity structure.
- Layer Lamination: Fabricate the PCB using a multilayer lamination process. This involves stacking and bonding multiple layers of substrate material, copper foils, and prepreg materials together to form the multilayer PCB stack. The cavity structure is integrated into one or more layers of the PCB stack as per the design requirements.
- Copper Deposition: Deposit copper onto the PCB surface using techniques such as electroplating or sputtering. This forms the conductive traces, pads, and ground planes on the PCB surface. Ensure that the copper deposition process achieves the desired thickness and quality for RF performance.
- Circuit Patterning: Use photolithography and etching processes to pattern the copper layer according to the PCB design layout. This involves applying a photoresist layer, exposing it to UV light through a photomask, developing the exposed resist, and etching away the unwanted copper to create the desired circuit traces and features.
- Component Assembly: Place and solder RF components onto the PCB surface using surface mount technology (SMT) or through-hole mounting techniques. Ensure proper alignment and soldering to maintain RF performance and reliability.
- Testing and Inspection: Perform electrical testing and visual inspection of the fabricated RF cavity PCB to verify functionality, RF performance, and quality. Use RF test equipment such as network analyzers and spectrum analyzers to validate RF characteristics and impedance matching.
- Finishing Processes: Apply finishing processes such as solder mask application, silkscreen printing, and surface finish (e.g., ENIG, HASL) to protect the PCB and improve its durability and solderability.
- Final Inspection and Packaging: Conduct final inspection and quality assurance checks to ensure that the fabricated RF cavity PCB meets all specifications and standards. Package the PCB for shipment or integration into the final RF system.
Throughout the fabrication process, it’s essential to maintain cleanliness, precision, and consistency to achieve high-quality RF cavity PCBs with optimal performance for demanding RF applications.
How do you manufacture a Radio Frequency Cavity PCB?
Manufacturing a Radio Frequency (RF) cavity PCB involves a specialized process tailored to the unique requirements of RF applications. Here’s a step-by-step overview of the manufacturing process:
- Design and Layout: Begin by designing the RF cavity PCB layout using PCB design software. This includes determining the dimensions and shape of the cavity, placing RF components and traces, and designing transmission lines and grounding structures. The layout should be optimized for RF performance, considering factors such as signal integrity, impedance matching, and electromagnetic shielding.
- Material Selection: Choose a suitable PCB substrate material with low dielectric loss and high-frequency performance, such as PTFE (Teflon) or ceramic-based materials. Select the appropriate thickness for the substrate based on the desired RF frequency and impedance requirements.
- Cavity Formation: Use specialized fabrication techniques to create the cavity structure within the PCB substrate. This typically involves mechanical milling or chemical etching processes to remove material from the inner layers of the PCB, leaving behind a well-defined cavity structure. The dimensions and geometry of the cavity are critical for achieving the desired resonant properties and RF performance.
- Layer Lamination: Fabricate the PCB using a multilayer lamination process. This involves stacking and bonding multiple layers of substrate material, copper foils, and prepreg materials together to form the multilayer PCB stack. The cavity structure is integrated into one or more layers of the PCB stack as per the design requirements.
- Copper Deposition: Deposit copper onto the PCB surface using techniques such as electroplating or sputtering. This forms the conductive traces, pads, and ground planes on the PCB surface. Ensure that the copper deposition process achieves the desired thickness and quality for RF performance.
- Circuit Patterning: Use photolithography and etching processes to pattern the copper layer according to the PCB design layout. This involves applying a photoresist layer, exposing it to UV light through a photomask, developing the exposed resist, and etching away the unwanted copper to create the desired circuit traces and features.
- Component Assembly: Place and solder RF components onto the PCB surface using surface mount technology (SMT) or through-hole mounting techniques. Ensure proper alignment and soldering to maintain RF performance and reliability.
- Testing and Inspection: Perform electrical testing and visual inspection of the fabricated RF cavity PCB to verify functionality, RF performance, and quality. Use RF test equipment such as network analyzers and spectrum analyzers to validate RF characteristics and impedance matching.
- Finishing Processes: Apply finishing processes such as solder mask application, silkscreen printing, and surface finish (e.g., ENIG, HASL) to protect the PCB and improve its durability and solderability.
- Final Inspection and Packaging: Conduct final inspection and quality assurance checks to ensure that the fabricated RF cavity PCB meets all specifications and standards. Package the PCB for shipment or integration into the final RF system.
Throughout the manufacturing process, it’s essential to maintain cleanliness, precision, and consistency to achieve high-quality RF cavity PCBs with optimal performance for demanding RF applications. Specialized equipment and expertise may be required for certain steps, particularly cavity formation and RF testing.
How much should a Radio Frequency Cavity PCB cost?
The cost of a Radio Frequency (RF) cavity PCB can vary significantly depending on several factors, including:
- Complexity: The complexity of the RF circuit design, including the number of layers, components, and features, can impact the cost. More complex designs may require additional fabrication steps and materials, resulting in higher costs.
- Materials: The choice of materials for the PCB substrate, copper foil, and surface finish can influence the cost. High-performance materials optimized for RF applications, such as PTFE (Teflon) or ceramic-based substrates, tend to be more expensive than standard FR-4 substrates.
- Manufacturing Process: The manufacturing processes involved, such as cavity formation, copper deposition, and circuit patterning, can affect the cost. Specialized processes or equipment required for RF cavity PCB fabrication may add to the overall cost.
- Quantities: The quantity of RF cavity PCBs ordered can impact the unit cost. Larger quantities typically result in lower per-unit costs due to economies of scale, while smaller quantities may incur higher setup and tooling costs.
- Lead Time: Expedited or rush orders may incur additional fees, while longer lead times may offer cost savings through standard manufacturing processes.
- Supplier: The choice of PCB manufacturer or supplier can also influence the cost. Different suppliers may offer varying pricing structures, capabilities, and levels of service.
- Additional Services: Additional services such as testing, inspection, and assembly may incur extra costs depending on the supplier’s offerings and the specific requirements of the project.
Given these factors, it’s challenging to provide a specific cost without knowing the details of the RF cavity PCB design, specifications, and quantity needed. However, RF cavity PCBs are generally considered to be more expensive than standard PCBs due to their specialized requirements and higher performance standards. It’s advisable to obtain quotes from multiple PCB manufacturers to compare pricing and find the best option for your project.
What is the Radio Frequency Cavity PCB base material?
The base material used for Radio Frequency (RF) cavity PCBs is crucial for achieving optimal RF performance. RF cavity PCBs often utilize materials with specific dielectric properties tailored to high-frequency applications. Two common types of base materials used for RF cavity PCBs are:
- PTFE (Polytetrafluoroethylene): PTFE-based materials, such as Rogers RO4000 series or Taconic TLY series, are popular choices for RF cavity PCBs. PTFE has low dielectric loss and excellent stability over a wide range of temperatures, making it suitable for high-frequency applications. PTFE-based substrates provide consistent electrical properties, allowing for precise impedance control and signal integrity in RF circuits.
- Ceramic-based Materials: Ceramic-based substrates, such as alumina (Al2O3) or aluminum nitride (AlN), are also used in RF cavity PCBs. These materials offer high thermal conductivity, low dielectric loss, and excellent mechanical stability, making them well-suited for high-power RF applications. Ceramic-based substrates are capable of handling high temperatures and provide good RF performance at microwave frequencies.
Both PTFE-based and ceramic-based materials offer advantages for RF cavity PCBs, and the choice between them depends on factors such as frequency range, power handling requirements, and thermal considerations. Additionally, manufacturers may offer variations and proprietary formulations of these base materials to meet specific performance criteria and customer requirements.
Which company makes Radio Frequency Cavity PCBs?
Many companies specialize in manufacturing Radio Frequency (RF) cavity PCBs, typically those dedicated to the field of high-frequency electronics manufacturing or supply. Some well-known companies include Rogers Corporation, Taconic Advanced Dielectric Division, Isola Group, Park Electrochemical Corp., and others. These companies have rich experience and expertise in the RF domain, offering various high-performance RF cavity PCB materials and solutions to meet the needs of different applications.
Our company is also capable of producing RF cavity PCBs. We possess advanced production equipment and a skilled technical team with years of experience in the high-frequency electronics field. We use high-quality materials such as PTFE and ceramic-based substrates to ensure excellent RF performance of the PCBs. Our manufacturing process strictly adheres to international standards and customer requirements, ensuring stable and reliable product quality.
We can customize various RF cavity PCBs according to customer requirements, including different sizes, layer configurations, frequency ranges, and power requirements. Our team collaborates with customers to provide customized solutions tailored to their specific application needs. Whether it’s for communication equipment, radar systems, satellite communications, or wireless sensor networks, we can deliver high-quality RF cavity PCBs to support the success of our customers’ projects.
With our expertise, efficient production capabilities, and superior customer service, we are committed to becoming a trusted manufacturing partner for RF cavity PCBs, providing continuous support and assistance for the success and development of our customers.
What are the 7 qualities of good customer service?
Good customer service is characterized by several key qualities that contribute to positive interactions and relationships with customers. Here are seven qualities of good customer service:
- Responsiveness: Good customer service involves being prompt and responsive to customer inquiries, requests, and concerns. This means acknowledging customer communication quickly and providing timely assistance or solutions to address their needs.
- Empathy: Empathy is essential in understanding and relating to customers’ feelings, concerns, and experiences. Good customer service representatives listen actively, show understanding, and demonstrate compassion towards customers’ situations to build rapport and trust.
- Professionalism: Good customer service is conducted with professionalism, which includes maintaining a courteous and respectful demeanor, adhering to company policies and standards, and representing the brand positively in all interactions with customers.
- Knowledgeability: Customers expect to receive accurate and helpful information from customer service representatives. Good customer service involves possessing a thorough understanding of the products or services offered, as well as the company’s policies, procedures, and offerings, to provide informed assistance and guidance to customers.
- Problem-solving skills: Effective problem-solving skills are crucial for resolving customer issues and complaints satisfactorily. Good customer service representatives can identify and analyze problems, propose appropriate solutions, and follow through to ensure customer satisfaction and resolution.
- Flexibility: Good customer service involves being adaptable and flexible in meeting the diverse needs and preferences of customers. This may include accommodating special requests, adjusting procedures or policies when necessary, and finding creative solutions to unique customer situations.
- Consistency: Consistency is key to providing good customer service across all interactions and touchpoints. Customers expect a consistent level of service quality, communication, and support regardless of the channel or representative they engage with. Good customer service ensures that every interaction reflects the company’s commitment to excellence and customer satisfaction.
By embodying these qualities, organizations can cultivate a customer-centric culture and deliver exceptional customer service experiences that foster loyalty, retention, and positive word-of-mouth referrals.
FAQs
What is a Radio Frequency (RF) cavity PCB?
A Radio Frequency (RF) cavity PCB is a specialized type of printed circuit board (PCB) designed for high-frequency RF applications. It incorporates a cavity structure within the PCB to enhance RF performance, including signal integrity, impedance matching, and electromagnetic shielding.
What are the benefits of using RF cavity PCBs?
RF cavity PCBs offer several benefits, including improved signal integrity, reduced electromagnetic interference (EMI), enhanced impedance matching, and better thermal management for high-power RF applications. They are also ideal for miniaturizing RF circuits and optimizing RF performance.
What materials are commonly used in RF cavity PCBs?
Common materials used in RF cavity PCBs include PTFE (Teflon) based substrates, such as Rogers RO4000 series or Taconic TLY series, and ceramic-based materials like alumina (Al2O3) or aluminum nitride (AlN). These materials offer low dielectric loss, high thermal conductivity, and excellent RF properties suitable for high-frequency applications.
What are the key design considerations for RF cavity PCBs?
Design considerations for RF cavity PCBs include cavity geometry and dimensions, substrate material selection, grounding and shielding techniques, transmission line design for impedance matching, component placement for optimal RF performance, and thermal management strategies.
How are RF cavity PCBs manufactured?
The manufacturing process for RF cavity PCBs involves specialized techniques such as cavity formation, multilayer lamination, copper deposition, circuit patterning, component assembly, testing, and finishing processes. These steps are tailored to meet the specific requirements of high-frequency RF applications.
What are some common applications of RF cavity PCBs?
RF cavity PCBs find applications in various industries, including telecommunications, aerospace, defense, automotive, medical devices, and wireless technology. They are used in wireless communication systems, radar systems, RF amplifiers, RF filters, and other RF-based electronic devices requiring high-performance RF circuitry.
How can I ensure the reliability and performance of RF cavity PCBs?
Ensuring the reliability and performance of RF cavity PCBs involves rigorous testing, adherence to industry standards, and collaboration with experienced PCB manufacturers specializing in RF applications. Thorough testing, validation, and quality assurance processes help ensure that RF cavity PCBs meet the required specifications and standards for reliable operation.