Radar Substrate Manufacturer
Radar Substrate Manufacturer,Radar substrates are foundational materials used in radar systems to support and integrate various electronic components, including antennas, circuits, and transmitters. These substrates are engineered with specific properties to ensure optimal performance and reliability in radar applications. Typically made from ceramics such as alumina or aluminum nitride, radar substrates exhibit characteristics such as low dielectric constant, high thermal conductivity, and mechanical stability. This enables efficient transmission and reception of radar signals while minimizing signal loss and interference. The manufacturing process for radar substrates involves shaping the material, sintering it at high temperatures to enhance density and strength, and applying surface treatments for improved performance. Customizable to meet the requirements of different radar systems, radar substrates play a critical role in enabling the functionality and effectiveness of radar technology in diverse fields, including military, aerospace, automotive, and weather monitoring.
What is a Radar substrate?
A radar substrate is a crucial component in radar systems, serving as the foundation upon which radar antennas and other electronic components are mounted. It’s essentially the material upon which radar systems are built. Radar substrates must possess specific characteristics to effectively support radar operations. They need to have excellent electrical properties to minimize signal loss and interference, high thermal conductivity to dissipate heat generated by electronic components, and mechanical stability to withstand environmental conditions such as vibrations and temperature fluctuations.
These substrates are typically made from materials like ceramics, such as alumina or aluminum nitride, or specialized composites. Ceramics offer excellent electrical insulation and thermal conductivity, making them suitable for radar applications. Additionally, radar substrates may incorporate features like microstrip lines, vias, and other structures to facilitate signal transmission and integration with other radar components.
In summary, a radar substrate is a foundational material in radar systems, providing support and facilitating the efficient operation of radar antennas and electronics. Its design and material properties play a critical role in the performance and reliability of radar systems.
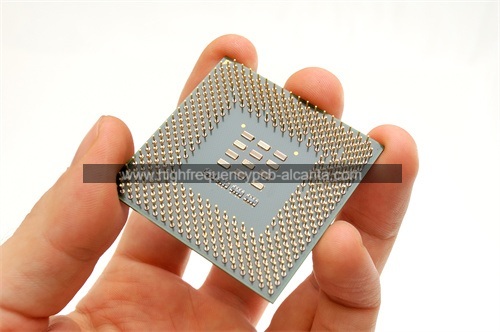
Radar Substrate Manufacturer
What are the Radar substrate Design Guidelines?
Design guidelines for radar substrates are essential to ensure optimal performance and reliability of radar systems. Here are some key guidelines typically considered:
- Dielectric Constant (εr): Radar substrates should have a stable dielectric constant to maintain consistent signal propagation speed. Low dielectric constant materials are preferred to minimize signal dispersion and loss.
- Loss Tangent (tanδ): Low loss tangent materials are crucial to minimize signal attenuation and maintain high radar sensitivity. Materials with low dielectric loss are preferred.
- Thermal Conductivity: Radar substrates should have high thermal conductivity to efficiently dissipate heat generated by electronic components. This helps in maintaining stable operating temperatures and prolonging component lifespan.
- Coefficient of Thermal Expansion (CTE): The CTE of the substrate should match closely with other materials in the radar system to prevent mechanical stress and potential damage due to thermal cycling.
- Mechanical Strength: Substrates must possess sufficient mechanical strength to withstand environmental stressors such as vibrations, shocks, and mechanical loads.
- Surface Smoothness: A smooth substrate surface is essential for precise fabrication of radar components such as microstrip lines, vias, and antennas. Surface roughness can lead to signal distortion and losses.
- Chemical Compatibility: Substrate materials should be chemically compatible with other components and materials used in the radar system to prevent degradation and ensure long-term reliability.
- Manufacturability: Radar substrate materials should be compatible with common fabrication techniques such as milling, drilling, and etching to facilitate efficient manufacturing processes.
- Cost: While striving for optimal performance, cost-effectiveness is also a crucial consideration in substrate selection. Balancing performance requirements with cost constraints is important in radar system design.
By adhering to these design guidelines, radar engineers can ensure that the chosen substrate material meets the performance, reliability, and manufacturability requirements of the radar system.
What is the Radar substrate Fabrication Process?
The fabrication process for radar substrates involves several steps to produce the desired material with the required properties. Here’s a generalized overview of the radar substrate fabrication process:
- Material Selection: The process begins with selecting the appropriate substrate material based on the specific requirements of the radar system, considering factors such as dielectric constant, thermal conductivity, mechanical strength, and cost.
- Preparation of Raw Material: The selected raw material, typically in the form of powders or pre-fabricated sheets, undergoes preparation steps such as cleaning, drying, and mixing to ensure uniformity and purity.
- Forming:The prepared material is then shaped into the desired substrate form. This can be achieved through various techniques such as pressing, casting, or extrusion, depending on the material and substrate design.
- Sintering: The formed substrate undergoes sintering, a process in which it is heated to high temperatures (typically above the material’s melting point) in a controlled atmosphere. Sintering helps in densifying the substrate, removing any porosity, and enhancing its mechanical and electrical properties.
- Machining: After sintering, the substrate may undergo machining processes such as milling, drilling, and lapping to achieve the desired dimensions, surface finish, and features required for radar component integration.
- Surface Treatment: Surface treatment techniques such as polishing, coating, or metallization may be applied to improve surface smoothness, electrical conductivity, or to provide protective layers against environmental factors.
- Quality Control: Throughout the fabrication process, quality control measures are implemented to ensure that the substrate meets the specified requirements and standards for dielectric properties, mechanical strength, thermal conductivity, and dimensional accuracy.
- Testing and Characterization: Once fabricated, the radar substrate undergoes testing and characterization to validate its performance and properties. This may involve electrical tests to measure dielectric constant and loss tangent, thermal tests to assess thermal conductivity, and mechanical tests to evaluate strength and durability.
- Packaging and Delivery: Upon successful testing and characterization, the fabricated radar substrates are packaged appropriately to protect them during transportation and storage before being delivered to the end-users or incorporated into radar system assemblies.
By following these steps, manufacturers can produce high-quality radar substrates that meet the stringent requirements of radar system applications.
How do you manufacture a Radar substrate?
Manufacturing a radar substrate involves a series of steps to create a material with the desired properties for supporting radar components. Here’s a detailed overview of the manufacturing process:
- Material Selection: Choose a substrate material based on the radar system’s requirements, considering factors such as dielectric constant, thermal conductivity, mechanical strength, and cost. Common substrate materials include ceramics like alumina or aluminum nitride, as well as specialized composites.
- Preparation of Raw Materials: If starting with powders or granules, raw materials undergo preparation steps such as cleaning, drying, and mixing to ensure uniformity and purity. This step is critical for achieving consistent material properties.
- Forming: The prepared material is shaped into the desired substrate form. This can be accomplished through methods like pressing (uniaxial or isostatic), casting, or extrusion. The choice of forming method depends on factors such as material properties and substrate design.
- Sintering: The formed substrate undergoes sintering, a process where it’s heated to high temperatures (typically above the material’s melting point) in a controlled atmosphere. Sintering helps densify the substrate, removing porosity and enhancing its mechanical and electrical properties.
- Machining: After sintering, the substrate may undergo machining processes such as milling, drilling, and lapping to achieve the desired dimensions, surface finish, and features necessary for integrating radar components. Precision machining ensures accuracy and consistency in substrate fabrication.
- Surface Treatment: Surface treatment techniques like polishing, coating, or metallization may be applied to improve surface smoothness, electrical conductivity, or provide protective layers against environmental factors. These treatments enhance substrate performance and longevity.
- Quality Control: Throughout the manufacturing process, quality control measures are implemented to ensure substrate compliance with specified requirements and standards. This includes testing material properties, dimensional accuracy, and surface quality at various stages of fabrication.
- Testing and Characterization: Once fabricated, radar substrates undergo testing and characterization to validate their performance. This includes electrical tests to measure dielectric properties, thermal tests to assess conductivity, and mechanical tests to evaluate strength and durability.
- Packaging and Delivery: Upon successful testing and characterization, manufactured radar substrates are packaged for transportation and storage. Proper packaging protects substrates from damage and environmental factors during transit to end-users or integration into radar systems.
By following these manufacturing steps with precision and care, radar substrate manufacturers can produce high-quality materials that meet the demanding requirements of radar system applications.
How much should a Radar substrate cost?
The cost of a radar substrate can vary widely depending on several factors, including the material used, its dimensions, complexity of fabrication, required tolerances, surface finish, and volume of production. Here are some considerations that can influence the cost:
- Material: Different substrate materials have varying costs. Common materials like alumina and aluminum nitride may have lower costs compared to more exotic or specialized materials.
- Size and Thickness: Larger substrates or those with greater thicknesses typically require more raw material and may involve additional machining steps, impacting the cost.
- Tolerances: Tighter tolerances and precision requirements in substrate dimensions and features often increase manufacturing complexity and cost.
- Surface Finish: Substrates with specific surface finish requirements may involve additional processing steps, such as polishing or coating, which can add to the overall cost.
- Volume of Production: Economies of scale apply in manufacturing, so larger production runs generally lead to lower per-unit costs due to efficiencies in material usage, labor, and equipment utilization.
- Customization:Customized substrate designs or features may require specialized tooling or processes, potentially increasing the cost compared to standard off-the-shelf substrates.
- Quality Control and Testing: Stringent quality control measures and extensive testing can contribute to higher production costs but ensure consistent quality and reliability of the substrates.
- Market Demand: Market conditions and competition among suppliers can also influence substrate pricing.
Given these factors, it’s challenging to provide a specific cost without detailed specifications. Generally, radar substrates can range from a few dollars per unit for simpler, standard substrates to hundreds or even thousands of dollars for highly customized, specialized substrates used in advanced radar systems. Working closely with substrate manufacturers to understand your specific requirements and optimize design and production processes can help manage costs effectively.
What is Radar substrate base material?
The base material of a radar substrate refers to the primary substance from which the substrate is made. This material serves as the foundation upon which radar components are mounted and integrated. Radar substrates are typically made from materials with specific properties that make them suitable for radar system applications. Common base materials for radar substrates include:
- Ceramics: Ceramics such as alumina (Al2O3) and aluminum nitride (AlN) are widely used as base materials for radar substrates. These materials offer excellent electrical insulation, high thermal conductivity, and mechanical stability, making them ideal for radar applications.
- Specialized Composites:Some radar substrates are made from composite materials that combine different elements to achieve desired properties. For example, composite substrates may combine ceramics with polymers or metals to enhance specific characteristics such as mechanical strength or thermal stability.
- Glass: Certain types of glass can also be used as base materials for radar substrates, particularly in applications where optical transparency or specific dielectric properties are required.
- Polymers: In some cases, polymers or plastic materials may be used as base materials for radar substrates, especially in applications where flexibility, lightweight, or cost-effectiveness are prioritized over high-performance characteristics.
The choice of base material depends on various factors such as the specific requirements of the radar system, operating conditions, performance goals, and cost considerations. Each material has its advantages and limitations, and selecting the most appropriate base material is crucial for achieving optimal performance and reliability in radar applications.
Which company makes Radar substrates?
Many companies specialize in the manufacture of radar substrates, some of the well-known ones include Rogers Corporation, DuPont, Murata Manufacturing, Kyocera, and Fujitsu. These companies have extensive experience and technological expertise in the field of radar substrates, providing high-quality substrate materials for various types of radar systems.
Our company is also a professional radar substrate manufacturer with advanced production equipment and a skilled technical team. We cover the entire production process from raw material selection to final product, ensuring that our products meet the quality and performance requirements of our customers.
Firstly, we carefully select the raw materials based on customer requirements and application scenarios, choosing suitable substrate materials such as ceramics, composites, etc. Then, we use advanced processing equipment to shape and process the raw materials, ensuring dimensional accuracy and surface quality of the substrates.
Next, we employ advanced sintering techniques to subject the formed substrates to high-temperature treatment, improving their density, mechanical strength, and ensuring that their electrical properties and thermal conductivity meet the requirements. Throughout the processing, we strictly control various process parameters to ensure product consistency and stability.
In addition, we have a rigorous quality control system in place, conducting comprehensive testing and inspection on each batch of products to ensure that they meet customer expectations. Our production line is flexible and can customize radar substrates of different specifications and characteristics according to customer requirements, meeting the needs of various application scenarios.
In summary, as a professional radar substrate manufacturer, our company has rich experience and technological strength, enabling us to provide customers with high-quality, reliable radar substrate products, helping their radar systems achieve excellent performance.
What are the 7 qualities of good customer service?
Good customer service is characterized by several key qualities that help foster positive relationships with customers and enhance their overall experience. Here are seven qualities of good customer service:
- Responsiveness: Good customer service involves being prompt and timely in addressing customer inquiries, concerns, and requests. Responding quickly to customer needs demonstrates attentiveness and a commitment to providing timely assistance.
- Empathy: Empathy is the ability to understand and relate to the feelings and perspectives of customers. Good customer service representatives listen actively, show genuine concern for customers’ issues, and strive to understand their perspective to provide appropriate support and solutions.
- Clarity: Clear communication is essential for effective customer service. Good customer service representatives communicate clearly and concisely, avoiding jargon or technical language that may confuse customers. They ensure that information, instructions, and explanations are easy to understand.
- Professionalism:Good customer service involves maintaining a professional demeanor and attitude at all times. Customer service representatives demonstrate professionalism through their behavior, language, and appearance, fostering trust and confidence in their ability to assist customers.
- Problem-Solving Skills: Good customer service representatives are adept at identifying and resolving customer issues effectively. They demonstrate strong problem-solving skills, using creativity and resourcefulness to address customer concerns and find satisfactory solutions.
- Adaptability: In the dynamic environment of customer service, adaptability is crucial. Good customer service representatives are flexible and adaptable, able to handle unexpected challenges, changes, and diverse customer needs with ease.
- Follow-Up: Following up with customers after resolving their issues or inquiries demonstrates a commitment to their satisfaction and reinforces positive relationships. Good customer service includes proactive follow-up to ensure that customers’ needs have been met and to gather feedback for continuous improvement.
By embodying these qualities, businesses can provide excellent customer service that leaves a lasting positive impression on customers and builds loyalty to the brand.
FAQs
What is a radar substrate?
A radar substrate is a material used as the base for radar system components, such as antennas and electronic circuits. It provides support and facilitates the integration of these components into radar systems.
What materials are used to make radar substrates?
Common materials used for radar substrates include ceramics like alumina and aluminum nitride, as well as specialized composites. These materials offer properties such as high thermal conductivity, electrical insulation, and mechanical stability.
What are the key properties of radar substrates?
Radar substrates should have properties such as low dielectric constant, low loss tangent, high thermal conductivity, and mechanical strength. These properties ensure efficient signal transmission, minimal signal loss, and reliability in radar system operation.
How are radar substrates manufactured?
Radar substrates are typically manufactured through processes such as forming, sintering, machining, and surface treatment. These processes involve shaping the substrate material, densifying it through heating, and adding surface finishes or coatings as needed.
What factors should be considered when selecting a radar substrate?
When selecting a radar substrate, factors such as dielectric properties, thermal conductivity, mechanical strength, cost, and compatibility with other components in the radar system should be considered to ensure optimal performance and reliability.
What are the applications of radar substrates?
Radar substrates are used in various radar applications, including military radar systems, weather radar, automotive radar, and aerospace radar. They play a critical role in supporting radar components and enabling the transmission and reception of radar signals.
Can radar substrates be customized for specific applications?
Yes, radar substrates can be customized to meet the specific requirements of different radar applications. This includes tailoring the material composition, dimensions, surface finish, and other properties to optimize performance and functionality.
Are radar substrates subject to quality testing?
Yes, radar substrates undergo rigorous quality testing to ensure they meet specified standards and performance requirements. This may include testing for dielectric properties, thermal conductivity, mechanical strength, and dimensional accuracy.