Radar HF Substrate Manufacturer
Radar HF Substrate Manufacturer,Radar HF substrates are specialized materials used in the construction of high-frequency (HF) radar systems, operating within the frequency range of 3 MHz to 30 MHz. These substrates serve as the foundation for critical components such as antennas, transmission lines, and circuitry in radar systems. Designed to meet the demanding requirements of HF radar applications, these substrates possess specific properties essential for optimal performance.
Characterized by low dielectric loss, high electrical conductivity, and excellent thermal stability, radar HF substrates ensure efficient signal transmission and reception with minimal distortion or loss. They provide dimensional stability under varying environmental conditions, maintaining the integrity of radar system components over time. Fabricated through precision processes such as molding, machining, and surface treatment, radar HF substrates are engineered to meet stringent performance standards and reliability requirements.
By offering superior signal integrity, thermal resilience, and compatibility with HF radar systems, radar HF substrates play a crucial role in the development of reliable and high-performance radar systems for various applications, including military surveillance, weather monitoring, and air traffic control.
What is Radar HF substrate?
Radar HF substrate typically refers to a type of material used in the construction of high-frequency (HF) radar systems. HF radar operates in the high-frequency range of the electromagnetic spectrum, typically between 3 MHz and 30 MHz.
The substrate material used in HF radar systems needs to meet specific requirements to ensure optimal performance at these frequencies. It should have low dielectric loss, high electrical conductivity, and good thermal stability. These properties help minimize signal loss and distortion, allowing the radar system to effectively transmit and receive signals.
Common substrate materials used in HF radar systems include various types of ceramics, composites, and specialized polymer materials that are engineered to meet the demanding requirements of high-frequency applications. The choice of substrate material depends on factors such as the specific operating frequency, power requirements, environmental conditions, and cost considerations.
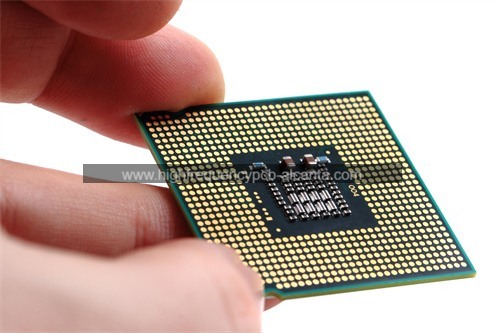
Radar HF substrate Manufacturer
What are the Radar HF substrate Design Guidelines?
Designing radar HF substrates involves several guidelines to ensure optimal performance. Here are some key considerations:
- Dielectric Constant (ε):The dielectric constant of the substrate material should be carefully selected based on the desired electrical properties of the radar system. Lower dielectric constants are generally preferred for HF radar substrates as they help reduce signal loss and maintain signal integrity.
- Dielectric Loss (tan δ):The substrate material should exhibit low dielectric loss to minimize signal attenuation. This ensures efficient transmission and reception of radar signals without significant degradation.
- Electrical Conductivity:High-frequency radar substrates often require good electrical conductivity to facilitate efficient signal propagation. Conductive materials such as certain types of ceramics or metal-filled composites may be chosen to enhance conductivity while maintaining other desirable properties.
- Thermal Stability:The substrate material should possess good thermal stability to withstand the operating conditions of the radar system without significant changes in electrical properties. This ensures reliable performance over a wide range of temperatures.
- Dimensional Stability: Dimensional stability is crucial to maintain the structural integrity and performance of the radar system over time. The substrate material should exhibit minimal dimensional changes due to factors such as temperature variations, humidity, and mechanical stress.
- Cost Considerations:While selecting substrate materials, cost-effectiveness is an important factor to consider. The chosen material should meet performance requirements while being economically viable for large-scale production of radar systems.
- Manufacturability:The substrate material should be compatible with the manufacturing processes used to fabricate radar components such as antennas, transmission lines, and circuit boards. Considerations such as ease of machining, bonding, and assembly should be taken into account during substrate selection.
By adhering to these design guidelines, engineers can develop radar HF substrates that meet the performance, reliability, and cost requirements of high-frequency radar systems.
What is the Radar HF substrate Fabrication Process?
The fabrication process for radar HF substrates involves several steps, which may vary depending on the specific substrate material and the desired characteristics of the radar system. Here’s a generalized overview of the fabrication process:
- Material Selection:Choose a substrate material that meets the required electrical, mechanical, and thermal properties for the HF radar application. Common substrate materials include ceramics, polymers, composites, and specialized materials with tailored properties.
- Material Preparation: Prepare the chosen substrate material for processing. This may involve steps such as cleaning, shaping, and sizing the material to the desired dimensions for fabrication.
- Substrate Formation:Depending on the material, the substrate may be formed using techniques such as molding, casting, or machining. For example, ceramics may be formed through shaping and firing processes, while polymers may be molded or extruded into the desired shape.
- Surface Treatment:Treat the substrate surface to enhance its electrical properties, adhesion, and compatibility with subsequent processing steps. Surface treatments may include chemical etching, plasma treatment, or deposition of thin films.
- Pattern Generation:Create patterns or features on the substrate surface to define the circuitry, antenna elements, or other components of the radar system. This can be achieved through techniques such as photolithography, screen printing, or direct machining.
- Additive Processes:Implement additive processes such as printing or deposition to add conductive traces, components, or coatings onto the substrate surface. This may involve techniques like inkjet printing, sputtering, or chemical vapor deposition (CVD).
- Curing and Bonding:Cure or bond the deposited materials to the substrate surface to ensure strong adhesion and structural integrity. This may involve thermal curing, UV curing, or other bonding techniques depending on the materials used.
- Finishing and Quality Control:Perform finishing steps such as polishing, coating, or surface treatment to improve the substrate’s performance and durability. Conduct thorough quality control inspections to verify dimensional accuracy, electrical properties, and overall quality of the fabricated substrates.
- Integration:Integrate the fabricated substrates with other components of the radar system, such as antennas, circuit boards, and signal processing units, to assemble the complete radar system.
- Testing and Validation:Test the fabricated radar HF substrates and the assembled radar system to validate performance, functionality, and compliance with specifications. This may involve electrical testing, signal characterization, and environmental testing under simulated operating conditions.
By following these fabrication steps and employing appropriate techniques and materials, engineers can produce radar HF substrates that meet the stringent requirements of high-frequency radar systems.
How do you manufacture a Radar HF substrate?
Manufacturing a radar HF substrate involves several steps, from material selection to final quality control. Here’s a detailed breakdown of the process:
- Material Selection:Choose a substrate material that meets the required electrical, mechanical, and thermal properties for the HF radar application. Common substrate materials include ceramics, polymers, composites, and specialized materials with tailored properties.
- Material Preparation:Prepare the chosen substrate material for processing. This may involve cleaning, shaping, and sizing the material to the desired dimensions for fabrication.
- Substrate Formation:Form the substrate into the desired shape and dimensions using techniques such as molding, casting, or machining. For example, ceramics may be formed through shaping and firing processes, while polymers may be molded or extruded into the desired shape.
- Surface Treatment:Treat the substrate surface to enhance its electrical properties, adhesion, and compatibility with subsequent processing steps. Surface treatments may include chemical etching, plasma treatment, or deposition of thin films to modify surface properties.
- Pattern Generation:Create patterns or features on the substrate surface to define the circuitry, antenna elements, or other components of the radar system. This can be achieved through techniques such as photolithography, screen printing, or direct machining.
- Additive Processes:Implement additive processes to add conductive traces, components, or coatings onto the substrate surface. This may involve techniques like inkjet printing, sputtering, or chemical vapor deposition (CVD) to deposit materials onto the substrate.
- Curing and Bonding:Cure or bond the deposited materials to the substrate surface to ensure strong adhesion and structural integrity. This may involve thermal curing, UV curing, or other bonding techniques depending on the materials used.
- Finishing and Quality Control:Perform finishing steps such as polishing, coating, or surface treatment to improve the substrate’s performance and durability. Conduct thorough quality control inspections to verify dimensional accuracy, electrical properties, and overall quality of the fabricated substrates.
- Integration:Integrate the fabricated substrates with other components of the radar system, such as antennas, circuit boards, and signal processing units, to assemble the complete radar system.
- Testing and Validation:Test the fabricated radar HF substrates and the assembled radar system to validate performance, functionality, and compliance with specifications. This may involve electrical testing, signal characterization, and environmental testing under simulated operating conditions.
By following these manufacturing steps and employing appropriate techniques and materials, engineers can produce radar HF substrates that meet the stringent requirements of high-frequency radar systems.
How much should a Radar HF substrate cost?
The cost of a radar HF substrate can vary widely depending on several factors, including the material used, manufacturing processes, complexity of design, and quantity produced. Here are some considerations that can influence the cost:
- Material Cost:The cost of the substrate material itself is a significant factor. Specialized materials with tailored properties may be more expensive than standard materials.
- Manufacturing Processes:The complexity of manufacturing processes involved in fabricating the substrate can affect the cost. Processes such as photolithography, chemical deposition, and precision machining may incur higher manufacturing expenses.
- Labor Costs:Labor costs associated with substrate fabrication, including skilled labor required for machining, assembly, and quality control, contribute to the overall cost.
- Volume Production: Economies of scale play a role in determining the cost. Higher volumes typically lead to lower per-unit costs due to efficiencies in production and economies of scale.
- Quality Control:Rigorous quality control measures increase manufacturing costs but are essential for ensuring the reliability and performance of radar HF substrates.
- Customization:Customized designs or unique requirements may increase costs compared to off-the-shelf or standard substrates.
- Supplier and Location:The choice of supplier and geographical location can impact costs due to differences in labor rates, material availability, and shipping expenses.
- Additional Features:Incorporating additional features such as integrated components, specialized coatings, or advanced manufacturing techniques may increase the cost of the substrate.
Given these factors, it’s challenging to provide a specific cost without knowing the detailed specifications and requirements of the radar HF substrate. Costs can range from a few dollars for simpler substrates to hundreds or even thousands of dollars for highly specialized or customized substrates. Consulting with suppliers and manufacturers to obtain quotes based on specific project requirements is recommended for accurate cost estimation.
What is Radar HF substrate base material?
The base material used for radar HF substrates can vary depending on the specific requirements of the radar system, including frequency range, power levels, environmental conditions, and manufacturing considerations. Here are some common types of base materials used for radar HF substrates:
- Ceramics:Ceramics such as alumina (Al2O3), aluminum nitride (AlN), and ferrites are commonly used for radar HF substrates due to their high thermal conductivity, excellent electrical insulation properties, and stability over a wide temperature range.
- Polymers:Certain polymers, such as polytetrafluoroethylene (PTFE) or liquid crystal polymers (LCP), are suitable for radar HF substrates, especially for applications requiring lightweight and flexible materials. These polymers offer good electrical properties and can be processed using techniques like injection molding or extrusion.
- Composites:Composite materials, which combine two or more materials to achieve specific properties, are used for radar HF substrates. For example, fiberglass-reinforced epoxy composites offer a balance of electrical, mechanical, and thermal properties suitable for radar applications.
- Metals:Metals such as copper, aluminum, or stainless steel can be used as base materials for radar HF substrates, particularly for applications requiring high electrical conductivity and robust mechanical properties. Metal substrates are often used for components like antennas and ground planes in radar systems.
- Semiconductors:In certain specialized radar applications, semiconductor materials such as silicon (Si) or gallium arsenide (GaAs) may be used as base materials for radar HF substrates, particularly for integrated circuit components and semiconductor-based devices.
The choice of base material depends on factors such as electrical properties, thermal conductivity, mechanical strength, cost considerations, and manufacturability. Engineers select the most suitable base material based on the specific requirements and performance criteria of the radar HF substrate and the overall radar system.
Which company makes Radar HF substrate?
Currently, there are many companies specializing in the manufacturing of radar HF substrates. Some well-known companies include Rogers Corporation, DuPont, Murata Manufacturing Co., Ltd., Taconic Advanced Dielectric Division, and Tesa Semiconductor Corporation. These companies have extensive experience and expertise in the HF substrate field and offer a variety of radar HF substrates made from different materials and technologies to meet the requirements of various radar systems.
Our company is also capable of producing radar HF substrates. With advanced manufacturing equipment and technology, a professional engineering team, and rich experience, we are able to design and manufacture high-quality radar HF substrates. Our engineering team can customize the substrate materials, dimensions, electrical characteristics, and surface treatments according to the specific requirements of our customers, ensuring that the substrates integrate seamlessly with their radar systems.
The radar HF substrates produced by our company have the following features and advantages:
- High-performance material selection:We use high-performance substrate materials such as high-frequency ceramics, specialized polymers, or composite materials to ensure that the substrates have excellent electrical properties, thermal stability, and mechanical strength.
- Advanced manufacturing processes:We employ advanced manufacturing processes and equipment, including precision machining and surface treatment techniques, to ensure that the substrates have precise dimensions, smooth surfaces, and good electrical properties.
- Customized design: We can customize the design of radar HF substrates according to the specific requirements of our customers, including dimensions, shapes, electrical characteristics, and surface treatments, to meet the needs of different radar systems.
- Strict quality control:We implement strict quality control measures to ensure that each production batch of radar HF substrates meets the specifications and requirements of our customers.
- Timely technical support and service:We have a professional technical team and a good after-sales service system to provide timely technical support and solutions to our customers.
Through the radar HF substrates produced by our company, customers can obtain high-quality, reliable, and cost-effective products, providing strong support for the performance enhancement and successful operation of their radar systems.
What are the qualities of good customer service?
Good customer service encompasses several qualities that contribute to positive interactions and experiences for customers. Here are some key qualities:
- Empathy:Good customer service involves understanding and empathizing with the customer’s needs, concerns, and emotions. Empathetic customer service representatives listen actively, acknowledge the customer’s feelings, and demonstrate genuine care and understanding.
- Communication Skills:Effective communication is essential for good customer service. Customer service representatives should be clear, concise, and articulate in their communication, both verbally and in writing. They should also be good listeners, allowing customers to express themselves fully and actively engaging in two-way communication.
- Patience:Patience is a crucial quality in customer service, especially when dealing with frustrated or upset customers. Customer service representatives should remain calm and composed, even in challenging situations, and be willing to take the time to resolve issues satisfactorily.
- Product Knowledge:Good customer service requires a deep understanding of the company’s products or services. Customer service representatives should be knowledgeable about the features, benefits, and usage of the products or services they support, enabling them to provide accurate information and helpful guidance to customers.
- Problem-Solving Skills:Strong problem-solving skills are essential for resolving customer issues effectively. Customer service representatives should be resourceful, proactive, and creative in finding solutions to customer problems, whether it involves troubleshooting technical issues, addressing billing discrepancies, or handling complaints.
- Professionalism:Professionalism encompasses aspects such as reliability, integrity, and accountability. Customer service representatives should conduct themselves professionally at all times, adhering to company policies and procedures, maintaining confidentiality, and following through on commitments made to customers.
- Positive Attitude:A positive attitude can go a long way in creating a pleasant customer service experience. Customer service representatives should approach interactions with enthusiasm, optimism, and a willingness to help, fostering a positive atmosphere and leaving customers with a favorable impression of the company.
- Adaptability:In today’s fast-paced and ever-changing business environment, adaptability is crucial in customer service. Customer service representatives should be flexible and adaptable, able to adjust to shifting priorities, handle unexpected challenges, and accommodate diverse customer needs and preferences.
- Respect:Respect for customers’ time, opinions, and concerns is fundamental to good customer service. Customer service representatives should treat customers with courtesy, dignity, and respect, acknowledging their value and demonstrating appreciation for their business.
By embodying these qualities, companies can deliver exceptional customer service experiences that foster loyalty, satisfaction, and positive word-of-mouth referrals.
FAQs
What is a radar HF substrate?
A radar HF substrate is a material used in the construction of radar systems operating in the high-frequency (HF) range of the electromagnetic spectrum. It serves as a base for components such as antennas, transmission lines, and circuitry, providing support and electrical properties suitable for HF radar applications.
What are the key properties of radar HF substrates?
Radar HF substrates should exhibit low dielectric loss, high electrical conductivity, good thermal stability, and dimensional stability. These properties ensure efficient signal transmission, minimal signal loss, and reliable performance over a wide range of operating conditions.
What materials are commonly used for radar HF substrates?
Common materials for radar HF substrates include ceramics (e.g., alumina, aluminum nitride), polymers (e.g., polytetrafluoroethylene, liquid crystal polymers), composites, and specialized materials tailored for HF applications.
How are radar HF substrates fabricated?
Radar HF substrates are typically fabricated through processes such as molding, casting, machining, surface treatment, additive processes (e.g., printing, deposition), curing, bonding, and finishing. These processes are tailored to the specific material properties and design requirements of the substrate.
What are the design considerations for radar HF substrates?
Design considerations for radar HF substrates include dielectric constant, dielectric loss, electrical conductivity, thermal stability, dimensional stability, cost-effectiveness, and manufacturability. These factors influence material selection, fabrication processes, and overall performance.
What companies manufacture radar HF substrates?
Several companies specialize in the manufacture of radar HF substrates, offering a range of materials, designs, and services to meet the needs of radar system developers and manufacturers. Common manufacturers include Rogers Corporation, DuPont, Murata Manufacturing Co., Ltd., and Taconic Advanced Dielectric Division.
What are the advantages of using radar HF substrates?
Radar HF substrates provide advantages such as improved signal integrity, reduced signal loss, enhanced thermal stability, and compatibility with high-frequency radar systems. They enable the construction of reliable and efficient radar systems for various applications.
How can I choose the right radar HF substrate for my application?
Choosing the right radar HF substrate involves considering factors such as operating frequency, power requirements, environmental conditions, design complexity, cost constraints, and supplier capabilities. Consulting with experts and conducting thorough evaluations can help identify the most suitable substrate for your specific application.