Radar/Antenna Substrate Manufacturer
Radar/Antenna Substrate Manufacturer,The radar/antenna substrate is a crucial component used to support and transmit radar and antenna systems. Typically made of highly conductive materials such as metal or composite materials, it ensures effective electromagnetic wave transmission. One of its primary functions is to provide a stable support structure to ensure the stability and accuracy of the radar or antenna. Additionally, the radar/antenna substrate must possess excellent thermal stability and durability to withstand various environmental conditions and workloads. To achieve higher performance, modern radar/antenna substrates often employ composite materials with lower weight and higher strength while maintaining good electromagnetic properties. Therefore, radar/antenna substrates play a crucial role in ensuring the normal operation of radar and antenna systems and are vital for various application areas such as aerospace, communications, and military.
What is a Radar/Antenna Substrate?
A radar/antenna substrate is a crucial component in radar and antenna systems, serving as the physical platform upon which the radar or antenna elements are mounted. It’s essentially the base or foundation that supports the components necessary for transmitting and receiving electromagnetic waves.
The substrate needs to possess specific properties to ensure optimal performance. These properties include electrical insulation, thermal stability, mechanical strength, and compatibility with the frequency range of operation. Materials commonly used for radar/antenna substrates include various types of ceramics, polymers, and composite materials.
In addition to providing a stable mounting surface, the substrate also plays a role in shaping the radiation pattern of the antenna or radar system. The substrate’s properties can influence the propagation of electromagnetic waves, affecting characteristics such as beamwidth, gain, and polarization.
Furthermore, advancements in substrate materials and fabrication techniques have led to the development of more compact, lightweight, and efficient radar and antenna systems. These substrates can be designed to meet the requirements of specific applications, such as aerospace, telecommunications, and military systems, where factors like size, weight, and performance are critical. Overall, the radar/antenna substrate is a foundational element that significantly impacts the functionality and effectiveness of radar and antenna systems.
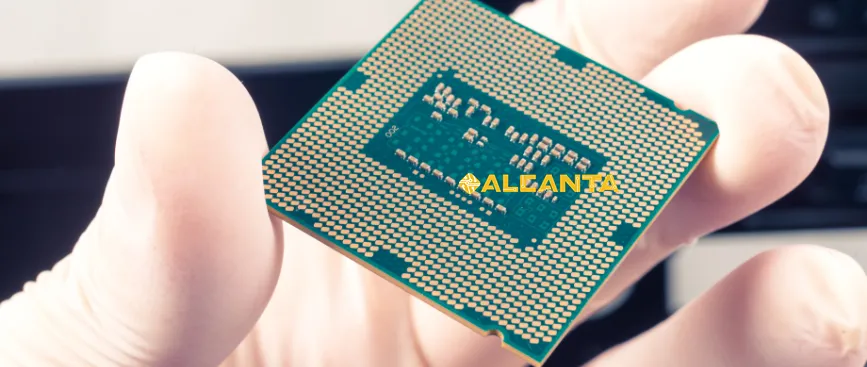
Radar/Antenna Substrate Manufacturer
What are Radar/Antenna Substrate Design Guidelines?
Designing radar/antenna substrates involves several key guidelines to ensure optimal performance and functionality:
- Material Selection: Choose materials with properties tailored to the specific application and frequency range of operation. Common substrate materials include ceramics, polymers, and composite materials.
- Dielectric Constant: The dielectric constant of the substrate material affects the propagation velocity of electromagnetic waves. It should be selected to match the desired characteristics of the antenna or radar system, such as beamwidth and impedance matching.
- Thickness and Dimensions: The substrate thickness and dimensions influence the electrical characteristics and mechanical stability of the system. Design these parameters to achieve the desired electrical performance while considering space constraints and weight limitations.
- Mechanical Stability: Ensure that the substrate material provides sufficient mechanical strength and stability to withstand environmental conditions, including temperature variations, vibrations, and mechanical stress.
- Dielectric Loss:Minimize dielectric loss in the substrate material to prevent energy dissipation and maintain high efficiency in the antenna or radar system.
- Manufacturability:Design the substrate with manufacturing processes in mind, considering factors such as ease of fabrication, cost-effectiveness, and scalability for mass production.
- Integration: Account for the integration of other components, such as feed networks, transmission lines, and active elements, into the substrate design to optimize performance and streamline assembly processes.
- Environmental Considerations: Evaluate the substrate’s resistance to environmental factors like moisture, chemicals, and electromagnetic interference to ensure long-term reliability and durability.
- Radiation Pattern and Beam Steering: The substrate design can influence the radiation pattern and beam steering capabilities of the antenna or radar system. Consider the substrate’s shape, surface features, and material properties to achieve the desired performance characteristics.
- Testing and Validation: Conduct thorough testing and validation of the substrate design to verify its electrical performance, mechanical integrity, and compatibility with system requirements before deployment.
By adhering to these design guidelines, engineers can develop radar/antenna substrates that meet the specific performance, reliability, and manufacturability requirements of their applications.
What is the Radar/Antenna Substrate Fabrication Process?
The fabrication process for radar/antenna substrates involves several key steps:
- Material Preparation: The fabrication process begins with the preparation of the substrate material. This may involve mixing raw materials, forming them into the desired shape (such as sheets or blocks), and curing or solidifying the material through processes like sintering, polymerization, or curing.
- Substrate Shaping: Once the material is prepared, it is shaped into the desired substrate geometry. This can be achieved through various techniques such as machining, cutting, molding, or casting. The substrate may be formed into sheets, panels, or three-dimensional structures depending on the design requirements.
- Surface Treatment: Surface treatment processes may be employed to modify the substrate’s surface properties, such as roughness or conductivity. This can involve techniques like polishing, coating, metallization, or etching to achieve the desired surface characteristics for optimal antenna or radar performance.
- Pattern Formation: If the substrate includes integrated antenna elements or other features, patterns may be formed on its surface. This can be done using techniques such as photolithography, printing, or deposition processes like sputtering or chemical vapor deposition (CVD). These patterns define the layout of antenna elements, feed networks, or other components on the substrate.
- Metallization: In many cases, the substrate surface or patterns are metallized to enhance conductivity and facilitate electrical connections. This typically involves depositing a thin layer of metal (such as gold, silver, or copper) onto the substrate surface using techniques like physical vapor deposition (PVD) or electroplating.
- Layer Bonding: In cases where multiple substrate layers are required, such as in multilayer circuit boards or stacked structures, the layers may be bonded together using adhesives, bonding agents, or thermal processes. This ensures mechanical stability and electrical connectivity between the layers.
- Quality Control and Testing: Throughout the fabrication process, quality control measures are implemented to ensure that the substrates meet specified dimensional tolerances, material properties, and performance requirements. Various testing techniques may be employed, including dimensional inspection, electrical testing, and performance characterization.
- Packaging and Protection: Once fabricated and tested, the substrates may be packaged and protected for transport and handling. This can involve encapsulation, sealing, or coating the substrates to safeguard them from environmental factors such as moisture, dust, and mechanical damage.
By following these fabrication steps with precision and attention to detail, engineers can produce radar/antenna substrates that meet the performance, reliability, and quality standards required for their applications.
How do you manufacture a Radar/Antenna Substrate?
Manufacturing a radar/antenna substrate involves several key steps, which can vary depending on the specific design requirements and materials used. Here’s a generalized overview of the manufacturing process:
- Material Selection: Choose a suitable substrate material based on the application requirements, considering factors such as dielectric constant, thermal stability, mechanical strength, and manufacturability.
- Material Preparation: If necessary, prepare the substrate material by mixing raw ingredients or forming it into the desired shape. This may involve processes such as mixing, extrusion, compression molding, or casting.
- Shaping and Forming: Shape the substrate material into the desired geometry using techniques such as cutting, milling, turning, or grinding. This step forms the basis of the substrate structure, whether it’s a flat panel, a three-dimensional structure, or a complex shape.
- Surface Treatment: Modify the substrate surface to achieve the desired properties for antenna or radar performance. This may involve processes such as polishing, coating, metallization, or surface etching to enhance conductivity, roughness, or other surface characteristics.
- Pattern Formation: Create patterns on the substrate surface to define the layout of antenna elements, feed networks, or other components. This can be achieved using techniques such as photolithography, printing, or deposition processes like sputtering or chemical vapor deposition (CVD).
- Metallization: Deposit a thin layer of metal onto the substrate surface to enhance conductivity and facilitate electrical connections. This is typically done using techniques such as physical vapor deposition (PVD), chemical vapor deposition (CVD), electroplating, or screen printing.
- Layer Bonding (if applicable): If the substrate requires multiple layers, bond them together using adhesives, bonding agents, or thermal processes to ensure mechanical stability and electrical connectivity between the layers.
- Quality Control and Testing: Throughout the manufacturing process, implement quality control measures to ensure that the substrates meet specified dimensional tolerances, material properties, and performance requirements. Test the substrates using techniques such as dimensional inspection, electrical testing, and performance characterization.
- Packaging and Protection: Once manufactured and tested, package and protect the substrates for transport and handling. This may involve encapsulation, sealing, or coating the substrates to safeguard them from environmental factors such as moisture, dust, and mechanical damage.
By following these steps with precision and attention to detail, manufacturers can produce radar/antenna substrates that meet the performance, reliability, and quality standards required for their intended applications.
How much should a Radar/Antenna Substrate cost?
The cost of a radar/antenna substrate can vary significantly depending on various factors, including:
- Material: The type of material used for the substrate can have a significant impact on its cost. Advanced materials with specific properties tailored for radar and antenna applications may be more expensive than standard materials.
- Manufacturing Process: The complexity of the manufacturing process required to produce the substrate can influence its cost. Processes involving precision machining, surface treatment, metallization, and quality control measures may increase production costs.
- Size and Thickness: Larger or thicker substrates may require more material and processing time, leading to higher costs. Conversely, smaller or thinner substrates may be more cost-effective.
- Quantity: Economies of scale often apply in manufacturing, meaning that larger production quantities can reduce the per-unit cost of substrates. Ordering substrates in bulk may result in lower costs per unit.
- Customization: If the substrate requires customization or specific design features tailored to a particular application, this may increase its cost. Custom tooling, design engineering, and testing may contribute to higher expenses.
- Quality and Certification: Substrates manufactured to meet stringent quality standards or industry certifications may command a higher price due to the additional costs associated with quality control measures and compliance processes.
- Supplier and Location: The choice of supplier and their location can affect substrate costs due to differences in labor costs, overhead expenses, and supply chain logistics.
Overall, the cost of a radar/antenna substrate can range from a few dollars for simple, mass-produced substrates to several hundred or even thousands of dollars for complex, customized substrates with advanced materials and manufacturing processes. For accurate pricing, it’s recommended to consult with substrate manufacturers or suppliers who can provide quotes based on specific requirements and quantities.
What is Radar/Antenna Substrate base material?
The choice of base material for radar/antenna substrates depends on various factors, including the specific requirements of the application, frequency range of operation, environmental conditions, and manufacturing considerations. Some common materials used as base substrates for radar/antenna applications include:
- Ceramics: Ceramics such as alumina (Al2O3) and aluminum nitride (AlN) are popular choices for high-frequency radar and antenna applications. They offer excellent thermal conductivity, mechanical strength, and electrical insulation properties, making them suitable for demanding environments.
- Polymer Composites: Polymer-based substrates, reinforced with materials like fiberglass or carbon fiber, are lightweight and offer good electrical properties. They are often used in portable or mobile antenna systems where weight is a concern.
- Printed Circuit Board (PCB) Materials: PCB materials, such as FR-4 (a type of epoxy resin), are commonly used for antenna substrates in lower frequency applications. They offer good electrical properties and are cost-effective for mass production.
- Rogers High Frequency Laminates: Rogers Corporation produces high-frequency laminates specifically designed for RF/microwave applications. These laminates offer low dielectric loss, consistent electrical properties, and good dimensional stability.
- Metal Substrates: In some cases, metal substrates such as aluminum or copper can be used for antenna applications, especially for applications requiring high thermal conductivity or electromagnetic shielding.
- Glass: Glass substrates, particularly low-loss glasses such as quartz, can be used for high-frequency applications where low dielectric loss is critical. Glass substrates offer excellent dimensional stability and resistance to environmental factors.
- Flexible Substrates: Flexible substrates made from materials like polyimide or liquid crystal polymers (LCP) are used in applications requiring flexibility or conformability, such as conformal antennas or wearable devices.
The choice of base material depends on balancing factors such as electrical performance, mechanical properties, thermal characteristics, cost, and manufacturability to meet the specific requirements of the radar/antenna system. Additionally, hybrid approaches may be used, combining different materials to achieve the desired performance characteristics.
Which company makes Radar/Antenna Substrate?
Many companies manufacture radar/antenna substrates, including internationally renowned electronic materials suppliers and specialized manufacturers. Some of these companies include Rogers Corporation, DuPont, Taconic Advanced Dielectric Division, and Murata Manufacturing Co., Ltd. These companies have rich experience and technological expertise in the field of electronic materials, enabling them to provide various types of radar/antenna substrates, including ceramic substrates, polymer substrates, metal substrates, etc., to meet the diverse needs of different applications.
Like these companies, our company also has the capability to manufacture radar/antenna substrates. We have been focusing on the field of electronic materials for many years, possessing advanced production equipment and a skilled technical team. Our manufacturing process includes material preparation, substrate shaping, surface treatment, pattern formation, metallization, lamination bonding, and more. We prioritize quality control to ensure that each manufacturing step meets stringent quality standards.
Our company can also customize radar/antenna substrates according to customer requirements, including different materials, sizes, shapes, and special requirements. Our design team collaborates with customers to provide customized solutions, ensuring that the substrates meet the performance and reliability requirements of their specific applications.
Our company’s strengths lie in flexibility, high-quality manufacturing, and customized services. Whether customers need simple substrates or complex customized solutions, we can provide products and services that meet their needs.
What are the 7 qualities of good customer service?
Good customer service is characterized by several key qualities that contribute to positive experiences and satisfaction for customers. Here are seven qualities of good customer service:
- Responsiveness: A good customer service team is responsive to customer inquiries, concerns, and feedback in a timely manner. This means acknowledging customer queries promptly and providing timely assistance or solutions to their issues.
- Empathy: Empathy involves understanding and acknowledging the customer’s perspective, emotions, and needs. Customer service representatives who demonstrate empathy show genuine concern for the customer’s situation and strive to address their concerns with compassion and understanding.
- Clear Communication: Effective communication is essential for good customer service. Customer service representatives should communicate clearly and concisely, ensuring that information is conveyed accurately and easily understood by the customer. This includes listening attentively to customer inquiries and providing clear explanations and instructions.
- Problem-Solving Skills: Good customer service involves effectively resolving customer problems and addressing their needs. Customer service representatives should be equipped with problem-solving skills to identify issues, explore solutions, and take appropriate action to resolve customer concerns satisfactorily.
- Professionalism:Professionalism encompasses aspects such as courtesy, respect, and professionalism in interactions with customers. Customer service representatives should maintain a professional demeanor, regardless of the situation, and strive to uphold the company’s standards and values in their interactions with customers.
- Product Knowledge: Having comprehensive product or service knowledge is essential for providing effective customer service. Customer service representatives should be well-informed about the company’s products or services, including features, benefits, pricing, and policies, enabling them to answer customer inquiries accurately and offer helpful recommendations.
- Follow-Up and Feedback: Good customer service doesn’t end with the resolution of a customer’s immediate issue. It involves following up with customers to ensure their satisfaction, seeking feedback on their experience, and using that feedback to continuously improve the quality of service. This demonstrates a commitment to ongoing customer support and improvement.
By embodying these qualities, businesses can cultivate a reputation for excellent customer service and build strong relationships with their customers, leading to increased loyalty, retention, and positive word-of-mouth referrals.
FAQs (Frequently Asked Questions)
What is a radar/antenna substrate?
A radar/antenna substrate is a physical platform on which radar or antenna elements are mounted. It provides mechanical support and electrical insulation while influencing the performance of radar or antenna systems.
What materials are used for radar/antenna substrates?
Common materials include ceramics (such as alumina and aluminum nitride), polymers, composite materials, printed circuit board (PCB) materials, and specialty materials like Rogers high-frequency laminates.
What properties are important for radar/antenna substrates?
Important properties include dielectric constant, dielectric loss, thermal conductivity, mechanical strength, dimensional stability, and compatibility with the frequency range of operation.
How are radar/antenna substrates manufactured?
The manufacturing process typically involves material preparation, shaping, surface treatment, pattern formation, metallization, layer bonding (if applicable), quality control, and packaging.
What factors affect the cost of radar/antenna substrates?
Factors such as material type, manufacturing process complexity, substrate size and thickness, quantity ordered, customization requirements, quality standards, and supplier selection can influence the cost.
What are some applications of radar/antenna substrates?
Radar/antenna substrates are used in various applications, including aerospace and defense systems, telecommunications infrastructure, automotive radar systems, weather monitoring equipment, and consumer electronics.
Can radar/antenna substrates be customized?
Yes, radar/antenna substrates can be customized to meet specific application requirements, including material selection, size and shape, surface features, and performance specifications.
What are the advantages of using radar/antenna substrates?
Advantages include improved signal transmission and reception, enhanced mechanical stability, reduced electromagnetic interference, compatibility with high-frequency operation, and the ability to integrate complex antenna designs.
How do radar/antenna substrates contribute to antenna performance?
Radar/antenna substrates play a critical role in shaping the radiation pattern, beamwidth, gain, and impedance matching of antennas, influencing overall performance and efficiency.
Where can I find suppliers of radar/antenna substrates?
Suppliers can be found through electronic materials suppliers, specialized manufacturers, online marketplaces, or by directly contacting companies that specialize in radar and antenna systems.