What is QFP Package Substrate?
QFP Package Substrate Manufacturer,QFP (Quad Flat Package) substrate is a versatile semiconductor packaging solution known for its compact design and high pin count. Featuring a square or rectangular body with leads extending from all four sides, QFP substrates enable efficient heat dissipation and reliable electrical connections. They support high-density integration of chips, facilitating miniaturization in electronic assemblies. Widely used in consumer electronics, automotive, and telecommunications industries, QFP package substrates ensure optimal performance in space-constrained environments. With their precise construction and compatibility with surface-mount assembly processes, QFP substrates offer a reliable and cost-effective solution for various electronic designs requiring compactness and high pin counts.
QFP stands for Quad Flat Package, which is a type of integrated circuit package used for surface-mount devices. The package typically has a square or rectangular shape with leads extending from all four sides. The QFP package substrate refers to the material on which the integrated circuit (IC) is mounted within the QFP package. This substrate provides a solid foundation for the IC and facilitates the connection of the IC to the leads that extend from the package.
The substrate material is typically a thin, flat piece of material such as fiberglass-reinforced epoxy resin (FR-4) or similar materials. It has conductive traces on its surface that connect the IC’s bond pads to the package leads. The substrate also provides mechanical support and electrical insulation for the IC.
Overall, the QFP package substrate plays a crucial role in ensuring the electrical performance, mechanical stability, and reliability of the integrated circuit within the package.
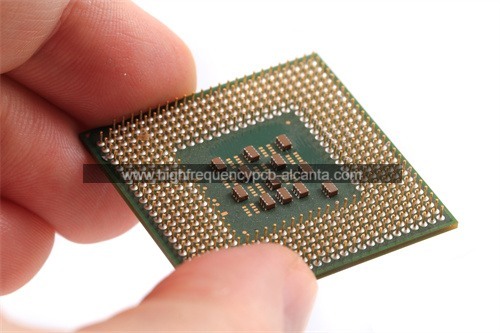
QFP Package Substrate Manufacturer
What are the Functions of QFP Package Substrate?
The QFP (Quad Flat Package) package substrate serves several important functions in the assembly and operation of integrated circuits (ICs). Some of the key functions include:
Mechanical Support: The substrate provides a sturdy base for mounting the IC and other components. It helps to ensure the structural integrity of the package, protecting the IC from physical damage during handling, assembly, and use.
Electrical Interconnection: The substrate facilitates electrical connections between the IC and the package leads. It typically contains conductive traces that connect the bond pads on the IC to the leads on the package, allowing for the transmission of electrical signals between the IC and the external circuitry.
Heat Dissipation: QFP package substrates may also play a role in dissipating heat generated by the IC during operation. Some substrates are designed with thermal vias or other features to help conduct heat away from the IC and distribute it across the package, helping to prevent overheating and ensure the reliable performance of the IC.
Signal Integrity: The layout and design of the substrate can impact the electrical performance and signal integrity of the IC. By carefully controlling trace lengths, widths, and routing, the substrate can help minimize signal distortion, noise, and other electrical issues, ensuring reliable communication between the IC and external components.
Environmental Protection: The substrate provides a protective barrier for the IC, shielding it from environmental factors such as moisture, dust, and contaminants. This helps to ensure the long-term reliability and performance of the IC in various operating conditions.
Overall, the QFP package substrate plays a critical role in the functionality, reliability, and performance of integrated circuits housed within QFP packages.
What are the Different Types of QFP Package Substrate?
There are several different types of substrates used in QFP (Quad Flat Package) packages, each with its own characteristics and advantages. Some common types of QFP package substrates include:
FR-4: Fiberglass-reinforced epoxy resin (FR-4) is one of the most widely used substrate materials for QFP packages. It offers good mechanical strength, electrical insulation, and thermal stability at a relatively low cost. FR-4 substrates are suitable for a wide range of applications and are commonly used in consumer electronics, telecommunications, and industrial equipment.
Polyimide: Polyimide substrates, also known as Kapton, offer excellent thermal stability, chemical resistance, and flexibility. They are often used in high-temperature and harsh environment applications where other substrate materials may not be suitable. Polyimide substrates are lightweight and can be easily customized for specific requirements, making them ideal for aerospace, automotive, and medical devices.
Ceramic: Ceramic substrates are highly durable and offer excellent thermal conductivity, making them suitable for high-power and high-frequency applications. They provide superior heat dissipation and electrical performance compared to organic substrates but are typically more expensive. Ceramic substrates are commonly used in RF (radio frequency), microwave, and power electronics applications.
Metal Core: Metal core substrates, also known as MCPCB (Metal Core Printed Circuit Board), consist of a metal base layer (typically aluminum or copper) sandwiched between layers of dielectric material. They offer superior thermal conductivity and heat dissipation compared to traditional organic substrates, making them ideal for high-power LED (light-emitting diode) and power electronics applications.
Flex: Flex substrates, also known as flexible circuits or flex circuits, are made of thin, flexible materials such as polyimide or polyester. They are used in applications where space constraints or mechanical flexibility are critical, such as in wearable devices, automotive sensors, and medical implants.
These are some of the common types of QFP package substrates, each offering unique characteristics to meet the requirements of different applications and industries. The choice of substrate material depends on factors such as cost, performance, reliability, and environmental conditions.
How does QFP Package Substrate Relate to IC Packaging?
The QFP (Quad Flat Package) package substrate is an integral component of IC (integrated circuit) packaging. It serves as the foundation upon which the integrated circuit is mounted, providing mechanical support, electrical interconnection, and thermal management. The relationship between the QFP package substrate and IC packaging can be understood through several key aspects:
Mechanical Support: The substrate provides a stable platform for mounting the integrated circuit and other components within the package. It helps to protect the IC from physical damage due to handling, assembly, and environmental factors.
Electrical Interconnection: The substrate facilitates the electrical connections between the integrated circuit and the package leads. It typically contains conductive traces that connect the bond pads on the IC to the external leads, enabling the transmission of electrical signals between the IC and the rest of the circuitry.
Heat Dissipation: The substrate plays a crucial role in dissipating heat generated by the integrated circuit during operation. It may incorporate features such as thermal vias, thermal pads, or metal layers to help conduct heat away from the IC and distribute it across the package, thereby preventing overheating and ensuring the reliable performance of the IC.
Signal Integrity: The layout and design of the substrate can impact the electrical performance and signal integrity of the integrated circuit. By carefully controlling trace lengths, widths, and routing, the substrate helps to minimize signal distortion, noise, and other electrical issues, ensuring reliable communication between the IC and external components.
Environmental Protection: The substrate provides a protective barrier for the integrated circuit, shielding it from environmental factors such as moisture, dust, and contaminants. This helps to ensure the long-term reliability and performance of the IC in various operating conditions.
Overall, the QFP package substrate plays a critical role in the functionality, reliability, and performance of integrated circuits housed within QFP packages. It forms an essential link between the IC and the rest of the packaging components, providing the necessary support, electrical connections, thermal management, and environmental protection required for optimal operation.
What are the Differences Between QFP Package Substrate and PCB?
QFP package substrate and PCB (Printed Circuit Board) are both essential components in electronic assemblies, but they serve different functions and have distinct characteristics. Here are some key differences between them:
Function:
QFP Package Substrate: The primary function of the QFP package substrate is to provide a foundation for mounting integrated circuits (ICs) within QFP packages. It facilitates electrical interconnection between the IC and the package leads, offers mechanical support, and aids in heat dissipation and signal integrity.
PCB: PCBs serve as the backbone of electronic devices, providing a platform for mounting and interconnecting various electronic components, including ICs, resistors, capacitors, and connectors. PCBs facilitate electrical connections between components and provide mechanical support for the entire electronic assembly.
Size and Shape:
QFP Package Substrate: QFP package substrates are typically smaller and have a square or rectangular shape. They are designed specifically to fit within QFP packages and accommodate the dimensions of the integrated circuit.
PCB: PCBs come in various sizes and shapes, depending on the requirements of the electronic device. They can be rectangular, square, or irregularly shaped, and their dimensions can range from small to large, depending on the complexity of the electronic assembly.
Material:
QFP Package Substrate: QFP package substrates are often made of materials optimized for their specific functions, such as fiberglass-reinforced epoxy resin (FR-4), polyimide, ceramic, or metal core materials.
PCB: PCBs are typically made of laminated composite materials, such as FR-4, with copper traces etched onto the surface to create electrical pathways. The choice of PCB material depends on factors such as cost, electrical performance, thermal characteristics, and environmental requirements.
Interconnections:
QFP Package Substrate: QFP package substrates typically contain conductive traces that connect the bond pads on the IC to the package leads. These traces are designed specifically to accommodate the electrical requirements of the integrated circuit.
PCB: PCBs contain complex networks of conductive traces that interconnect various electronic components mounted on the board. These traces form the electrical pathways that allow signals to flow between components and enable the functionality of the electronic device.
In summary, while both QFP package substrates and PCBs play important roles in electronic assemblies, they serve different functions and have distinct characteristics tailored to their specific applications within electronic devices.
What are the Main Structures and Production Technologies of QFP Package Substrate?
The main structures and production technologies of QFP (Quad Flat Package) package substrates can vary depending on factors such as the specific application requirements, desired performance characteristics, and manufacturing capabilities. However, there are some common structures and production technologies used in the fabrication of QFP package substrates:
Main Structures:
Base Material: The base material of QFP package substrates is typically a rigid or flexible substrate material that provides mechanical support and electrical insulation for the integrated circuit (IC). Common base materials include fiberglass-reinforced epoxy resin (FR-4), polyimide, ceramic, and metal core materials.
Conductive Traces: QFP package substrates contain conductive traces that connect the bond pads on the IC to the package leads. These traces are typically fabricated using processes such as etching, plating, or printing, and they are designed to meet the electrical requirements of the integrated circuit.
Dielectric Layers: Dielectric layers are used to separate and insulate the conductive traces from each other and from the base material. These layers are typically made of materials such as epoxy resin, polyimide, or ceramic, and they help to minimize signal interference, crosstalk, and electrical leakage.
Solder Mask: Solder mask is a protective coating applied over the conductive traces to prevent solder bridging and ensure proper solder joint formation during assembly. It also provides insulation and protects the substrate from environmental factors such as moisture, dust, and contaminants.
Production Technologies:
Etching: Etching is a common process used to fabricate conductive traces on QFP package substrates. It involves selectively removing material from a metal layer using chemical etchants or plasma etching techniques, leaving behind the desired pattern of traces.
Plating: Plating is used to deposit metal onto the substrate surface, forming conductive traces or pads. Electroplating and electroless plating are commonly used techniques for depositing metal layers with precise thickness and conductivity.
Printing: Printing techniques such as screen printing or inkjet printing can be used to apply conductive inks or pastes onto the substrate surface, creating patterns of traces or pads. Printing offers flexibility in design and can be used with a wide range of substrate materials.
Lamination: Lamination is used to bond together multiple layers of substrate material and dielectric material to form a multilayer structure. This process involves applying heat and pressure to the layers, causing them to adhere together and form a solid, integrated substrate.
Surface Treatment: Surface treatment processes such as surface roughening, plasma treatment, or chemical treatment may be used to improve the adhesion, solderability, and reliability of the substrate surface.
Overall, the main structures and production technologies of QFP package substrates are designed to meet the electrical, mechanical, and environmental requirements of the integrated circuits housed within QFP packages. These substrates are manufactured using a combination of materials and processes to achieve the desired performance characteristics and reliability.
Frequently Asked Questions (FAQs)
What is a QFP package substrate?
A QFP package substrate is a component used in integrated circuit packaging. It serves as the foundation upon which the integrated circuit is mounted within the QFP package, providing mechanical support, electrical interconnection, and thermal management.
What materials are used in QFP package substrates?
Common materials used in QFP package substrates include fiberglass-reinforced epoxy resin (FR-4), polyimide, ceramic, and metal core materials. The choice of material depends on factors such as cost, electrical performance, thermal characteristics, and environmental requirements.
What are the main functions of a QFP package substrate?
The main functions of a QFP package substrate include providing mechanical support for the integrated circuit, facilitating electrical connections between the IC and the package leads, dissipating heat generated by the IC, ensuring signal integrity, and providing environmental protection for the IC.
How are QFP package substrates manufactured?
QFP package substrates are typically manufactured using processes such as etching, plating, printing, lamination, and surface treatment. These processes are used to create conductive traces, bond layers of substrate material together, and apply protective coatings to the substrate surface.
What are the advantages of QFP package substrates?
QFP package substrates offer several advantages, including compact size, high reliability, good electrical performance, efficient heat dissipation, and compatibility with surface-mount assembly processes. They are commonly used in a wide range of electronic devices and applications.
What factors should be considered when selecting a QFP package substrate?
When selecting a QFP package substrate, factors to consider include the electrical requirements of the integrated circuit, the thermal characteristics of the substrate material, the environmental conditions in which the device will operate, cost considerations, and manufacturing capabilities.
Are there different types of QFP package substrates?
Yes, there are different types of QFP package substrates, including standard FR-4 substrates, high-temperature polyimide substrates, ceramic substrates for high-power applications, metal core substrates for improved thermal management, and flexible substrates for applications requiring mechanical flexibility.
Conclusion
In conclusion, QFP (Quad Flat Package) package substrates play a crucial role in integrated circuit packaging, serving as the foundation for mounting the IC within the package. They provide mechanical support, facilitate electrical interconnection, aid in heat dissipation, ensure signal integrity, and offer environmental protection for the IC. QFP package substrates are manufactured using various materials and production technologies, depending on the specific requirements of the application. They offer advantages such as compact size, high reliability, good electrical performance, and compatibility with surface-mount assembly processes. When selecting a QFP package substrate, factors such as electrical requirements, thermal characteristics, environmental conditions, cost considerations, and manufacturing capabilities should be taken into account. Overall, QFP package substrates are essential components in electronic assemblies, contributing to the functionality, reliability, and performance of integrated circuits in a wide range of applications.