Polyimide Substrate Manufacturer
Polyimide Substrate Manufacturer,Polyimide substrates are advanced materials known for their exceptional thermal stability, electrical insulation, and mechanical strength. They are widely used in electronic applications due to their ability to withstand high temperatures and harsh environments. These substrates exhibit excellent chemical resistance and low thermal expansion, making them ideal for flexible and rigid-flex circuits. Polyimide substrates are commonly found in aerospace, automotive, and high-performance electronic devices. Their inherent flexibility allows for complex designs and integration in space-constrained applications. Additionally, they offer good dielectric properties and durability, ensuring reliable performance in demanding and high-temperature conditions.
What is a Polyimide Substrate?
Polyimide substrates are a type of high-performance material used in various electronic and aerospace applications. They are made from polyimide, a polymer known for its excellent thermal stability, chemical resistance, and electrical insulating properties.
Polyimide substrates are particularly valued for their ability to withstand extreme temperatures, ranging from -269°C to +400°C, without significant degradation. This makes them ideal for applications in environments with high thermal stresses, such as in aerospace components or high-power electronics. Additionally, polyimide has a low dielectric constant and dissipation factor, which contributes to its effectiveness as an electrical insulator, ensuring reliable performance in electronic circuits.
These substrates are often used in flexible printed circuits (FPCs), where their flexibility and resistance to deformation are critical. They also play a crucial role in the manufacture of high-density interconnects (HDIs) and in applications requiring precise, high-frequency signal transmission.
The process of making polyimide substrates typically involves coating a polyimide film onto a base material, such as copper or another metal, followed by curing. This results in a durable, flexible, and high-performance substrate that can handle demanding conditions.
Overall, polyimide substrates are indispensable in modern technology, offering durability and reliability across a range of industries, including electronics, aerospace, and automotive applications.
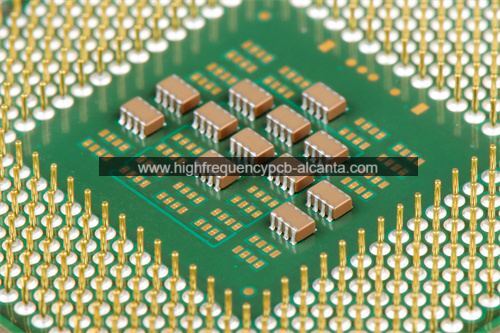
Polyimide Substrate Manufacturer
What is the Polyimide Substrate Design Guidelines?
Polyimide substrate design guidelines are crucial for ensuring that these substrates meet the required performance and reliability standards in their applications. Here are some key considerations:
- Material Selection: Choose high-quality polyimide materials with appropriate thermal and electrical properties. Ensure the material meets the specific requirements for temperature stability, dielectric constant, and chemical resistance.
- Thickness Control: Maintain precise control over the thickness of the polyimide film. Variations in thickness can affect performance and reliability, so consistent thickness is essential for uniform electrical insulation and mechanical properties.
- Layer Construction: For multilayer designs, ensure proper adhesion between layers. Polyimide substrates are often used in flexible circuits, so managing the bond strength and layer alignment is crucial to avoid delamination and ensure reliable operation.
- Thermal Management: Design for efficient thermal management to handle heat dissipation. Polyimide substrates should be evaluated for their thermal conductivity and expansion characteristics to prevent thermal stress and potential failures.
- Circuit Layout: Pay careful attention to the layout of circuit patterns. Minimize signal interference and crosstalk by optimizing trace width, spacing, and layout. Ensure that the design accommodates the polyimide substrate’s flexibility and thermal expansion.
- Mechanical Stress:Consider the mechanical stress and flexibility of the substrate in the design. Polyimide substrates are known for their flexibility, but excessive bending or stretching should be avoided to prevent damage or performance issues.
- Adhesion and Bonding: Ensure proper adhesion of polyimide to other materials, such as copper or adhesives used in the substrate construction. Proper bonding is crucial for maintaining electrical and mechanical integrity.
- Testing and Quality Control: Implement rigorous testing and quality control measures to verify the substrate’s performance under various conditions. This includes thermal cycling, electrical testing, and mechanical stress evaluations.
By following these guidelines, designers can ensure that polyimide substrates perform reliably and meet the demands of their specific applications, from electronics to aerospace components.
What is the Polyimide Substrate Fabrication Process?
The fabrication process of polyimide substrates involves several critical steps to ensure the production of high-quality, high-performance materials. Here’s an overview of the typical fabrication process:
- Material Preparation: Start with the preparation of the polyimide resin. This resin is often supplied as a liquid or pre-cured film. The choice of resin depends on the desired properties of the final substrate, including thermal stability, flexibility, and electrical insulation.
- Coating: Apply the polyimide resin onto a base material, such as a copper foil or a flexible film. This can be done through various methods, including spin coating, dip coating, or roll-to-roll coating. The uniformity of the coating is crucial for consistent substrate performance.
- Drying and Curing: After coating, the polyimide resin needs to be partially cured to form a solid film. This is typically done through a thermal curing process, where the coated material is heated in an oven or a curing furnace. This step transforms the polyimide resin into a cross-linked polymer, enhancing its thermal and mechanical properties.
- Lamination: For multilayer substrates, multiple layers of polyimide film and conductive layers (e.g., copper) are laminated together. This involves applying heat and pressure to bond the layers securely. Proper lamination ensures good adhesion between layers and prevents delamination during use.
- Patterning: The substrate is then patterned to create the desired circuit layout. This involves applying a photoresist material, exposing it to UV light through a mask, and developing it to create the circuit pattern. The unexposed areas are then etched away to reveal the underlying copper or other conductive materials.
- Etching: Etching removes unwanted metal from the substrate, leaving behind the desired circuit patterns. This is typically done using chemical etchants or plasma etching techniques. Careful control of the etching process is essential to achieve precise and clean patterns.
- Insulation and Finishing: Apply additional layers of polyimide or other insulating materials to cover and protect the circuit patterns. This step may include coating with a soldermask or applying other protective finishes.
- Testing and Inspection: Conduct thorough testing and inspection to ensure the substrate meets quality and performance standards. This includes checking for defects, measuring electrical properties, and verifying dimensional accuracy.
- Cutting and Packaging: Finally, cut the fabricated substrates to the required size and package them for shipment. Ensure that the packaging protects the substrates from damage during transport and handling.
Following these steps ensures that polyimide substrates are produced with high precision and reliability, making them suitable for demanding applications in electronics, aerospace, and other high-performance fields.
How Do You Manufacture a Polyimide Substrate?
Manufacturing a polyimide substrate involves several detailed steps to ensure high-quality and performance characteristics. Here’s a step-by-step guide to the typical manufacturing process:
- Resin Preparation: Begin by preparing the polyimide resin. This resin is usually a pre-polymer that needs to be converted into a polyimide through a curing process. The resin is often supplied as a liquid or a film.
- Base Material Selection: Choose a base material for the substrate, such as copper foil or a flexible film. The base material provides structural support and can be coated with the polyimide resin.
- Coating: Apply the polyimide resin to the base material using methods such as spin coating, dip coating, or roll-to-roll coating. Ensure that the resin is evenly distributed and covers the entire surface.
- Drying: After coating, the resin needs to be partially dried to remove solvents and to prepare it for curing. This is typically done by heating the material in an oven or using other drying techniques.
- Curing: The partially dried resin is then fully cured to form a solid polyimide film. This curing process usually involves heating the coated material in a curing oven or furnace at high temperatures. Curing transforms the resin into a cross-linked polyimide polymer, giving it its final properties.
- Lamination:For multilayer substrates, multiple layers of polyimide film and conductive layers (like copper) are laminated together. This step involves applying heat and pressure to bond the layers securely. Proper lamination is critical to ensure adhesion and structural integrity.
- Patterning:Apply a photoresist material to the surface of the substrate. Expose the photoresist to UV light through a mask that defines the circuit pattern. Develop the photoresist to reveal the areas that need to be etched away.
- Etching: Use chemical or plasma etching techniques to remove unwanted metal from the substrate, leaving behind the desired circuit patterns. This step requires precise control to achieve accurate and clean patterns.
- Insulation and Coating: Apply additional insulating layers or coatings to protect the circuit patterns. This may include soldermask coatings or other protective layers.
- Testing: Conduct thorough testing and inspection of the substrates. This includes checking for electrical performance, mechanical properties, and dimensional accuracy. Testing ensures that the substrates meet quality and performance standards.
- Cutting and Packaging: Cut the manufactured substrates to the required dimensions and package them carefully for shipping. Proper packaging protects the substrates from damage during transportation and handling.
By following these steps, manufacturers can produce high-quality polyimide substrates suitable for a variety of demanding applications, including electronics and aerospace components.
How Much Should a Polyimide Substrate Cost?
The cost of a polyimide substrate can vary widely depending on several factors. Here are the key factors influencing the price:
- Material Quality and Specifications: High-performance polyimide substrates with advanced thermal, electrical, and mechanical properties generally cost more. Custom formulations or specific grades of polyimide that meet particular industry standards will also be more expensive.
- Size and Thickness: Larger substrates or those with thicker polyimide layers typically cost more due to the increased material usage and manufacturing complexity. Precision cutting and handling can also affect the cost.
- Layer Count and Complexity: Multilayer polyimide substrates, which involve additional lamination and patterning processes, tend to be more expensive. Complex designs with fine features or high-density interconnects (HDI) also increase costs.
- Production Volume: The cost per unit can decrease with higher production volumes due to economies of scale. For small quantities or prototypes, the cost per substrate is usually higher.
- Manufacturing Process: The choice of manufacturing process, such as advanced coating techniques, precise etching, and high-temperature curing, can impact the cost. More sophisticated processes generally incur higher costs.
- Custom Specifications: Customizations, such as specific circuit designs, unique adhesive properties, or special coatings, can add to the cost. Tailoring the substrate to meet specific application requirements often involves additional engineering and testing.
- Supplier and Market Conditions: The cost of polyimide substrates can also be influenced by market conditions, supplier pricing, and geographical location. Different suppliers may offer varying prices based on their production capabilities and market strategies.
As a rough estimate, the cost of polyimide substrates can range from $10 to $100 or more per square meter. For more precise pricing, it is recommended to request quotes from suppliers based on your specific requirements and volume needs.
Which Company Makes Polyimide Substrates?
Many companies manufacture polyimide (PI) substrates, which are used in high-tech fields such as electronics, aerospace, and automotive applications. Here are some well-known manufacturers of polyimide substrates:
- DuPont: DuPont is a leading global supplier of polyimide materials, with its Kapton® series of polyimide films known for excellent heat resistance and electrical insulation properties. DuPont’s polyimide substrates are highly stable and reliable, making them suitable for various demanding applications.
- Huntsman: Huntsman provides polyimide materials that are widely used in electronic products. Their high-temperature stability and excellent insulation properties make them a preferred choice for high-frequency and high-temperature electronic applications.
- Mitsubishi Chemical: Mitsubishi Chemical’s polyimide substrates are praised for their outstanding mechanical properties and thermal stability. The company offers solutions for a range of industrial applications, including flexible circuits and high-performance printed circuit boards (PCBs).
- Showa Denko:Showa Denko’s polyimide materials are extensively used in semiconductor packaging and electronic devices. Their products offer good chemical resistance and electrical insulation, making them suitable for high-end electronics.
- Nitto Denko: Nitto Denko provides polyimide substrates with high heat resistance and excellent mechanical properties, making them suitable for use in stringent industrial conditions. Their products are widely used in high-frequency electronics and flexible circuits.
In addition to these companies, many other manufacturers offer polyimide substrates, including specialized producers and custom service providers. Each company’s products have unique advantages and characteristics, catering to various application needs.
Our Company’s Polyimide Substrate Manufacturing Capabilities:
Our company manufactures high-quality polyimide substrates to meet the diverse needs of customers in electronics and high-tech applications. We use advanced manufacturing technologies and equipment to ensure that our polyimide substrates meet industry standards in performance, reliability, and consistency.
Our polyimide substrates feature excellent high-temperature performance, capable of withstanding working temperatures up to 400°C, making them ideal for use in high-temperature environments. Additionally, our products offer good electrical insulation and mechanical strength, suitable for various high-frequency and high-density circuit applications.
We provide customized solutions based on specific customer requirements, including different thicknesses, sizes, and multilayer designs. Our quality control system ensures that each substrate undergoes rigorous testing and inspection before leaving the factory to meet high standards of reliability and performance.
If you need polyimide substrates, we are committed to providing you with high-quality products and services to help you meet your specific application needs.
What Are the 7 Qualities of Good Customer Service?
Good customer service is essential for maintaining customer satisfaction and loyalty. Here are seven key qualities that define excellent customer service:
- Responsiveness:Timely and efficient responses to customer inquiries, complaints, and requests are crucial. A good customer service team should provide quick solutions and avoid long wait times. Responsiveness also involves being available through multiple channels, such as phone, email, chat, and social media.
- Empathy: Understanding and addressing customers’ feelings and concerns is vital. Empathetic service means actively listening to customers, acknowledging their issues, and showing genuine concern. This helps build a positive relationship and reassures customers that their concerns are being taken seriously.
- Professionalism: Maintaining a high level of professionalism in all interactions is important. This includes clear communication, respectful behavior, and knowledgeable responses. Professionalism helps build trust and confidence in the service provided.
- Knowledgeability: Customer service representatives should have a deep understanding of the company’s products, services, and policies. Being knowledgeable enables them to provide accurate information, troubleshoot issues effectively, and offer valuable advice.
- Patience: Dealing with customers who may be frustrated or confused requires patience. Good customer service involves remaining calm, polite, and helpful, even in challenging situations. Patience helps resolve issues more effectively and contributes to a positive customer experience.
- Consistency: Providing a consistent level of service across all interactions and channels is crucial. Consistency ensures that customers receive the same quality of service, regardless of who they interact with or how they contact the company. This builds reliability and trust.
- Follow-Up: Effective customer service involves following up to ensure that issues are resolved and customers are satisfied. This may include checking back with customers after a solution has been provided or reaching out to confirm that their needs have been met. Follow-up demonstrates commitment to customer satisfaction and helps address any lingering concerns.
By embodying these qualities, companies can enhance their customer service, leading to greater customer satisfaction and loyalty.
FAQs
What is a Polyimide Substrate?
A Polyimide Substrate is a high-performance circuit board made from polyimide material, known for its excellent thermal and electrical properties.
What are the key design considerations for Polyimide Substrates?
Key considerations include material selection, trace width, via design, and thermal management.
How is a Polyimide Substrate fabricated?
The fabrication process involves material preparation, photoresist application, exposure, etching, lamination, drilling, and final inspection.
How much does a Polyimide Substrate cost?
Costs vary based on size, complexity, quantity, specifications, and manufacturing processes.
What is the base material for Polyimide Substrates?
The base material is polyimide film or laminate known for its thermal stability and electrical insulation.
Which companies manufacture Polyimide Substrates?
Several companies manufacture Polyimide Substrates, including ours.