What is Package Substrate?
Package Substrate,Package Substrate is a critical component in electronic device manufacturing, used for mounting and connecting integrated circuits (ICs) to Printed Circuit Boards (PCBs). It provides structural support and electrical pathways, enabling efficient signal transmission and power distribution. Typically composed of insulating materials and metal traces, Package Substrate ensures reliable connections between ICs and external components. Design considerations include thermal management, signal integrity, and miniaturization to meet the demands of modern electronics. These substrates play a crucial role in optimizing the performance, reliability, and form factor of electronic products.
Package substrate stands as a pivotal linchpin in the realm of modern electronic devices, assuming a role of paramount importance. It acts as a linchpin, constituting a foundational bedrock for the integration of integrated circuits (ICs) and microelectronic packages, orchestrating the attachment and interconnection of semiconductor components.
Crafted from materials such as ceramics or organic laminates, the substrate takes on a svelte, planar demeanor. Its raison d’être lies in providing not only physical bolstering but also a sophisticated electrical nexus between semiconductor chips like CPUs and GPUs, fostering a harmonious collaboration among these electronic entities.
The substrate, through its intricate network of conductive pathways—aptly named traces or interconnects—serves as a clandestine conductor, orchestrating connections between the sundry pins or pads on the semiconductor devices. These pathways, akin to the synapses of an electronic nervous system, are indispensable for facilitating data transfer, power dissemination, and internal dialogues within the electronic microcosm.
Beyond its role as a mere connector, the package substrate dons the hat of a thermal maestro, playing a pivotal role in dissipating the heat generated during the electronic ballet of operations. This thermal choreography ensures that the device pirouettes within the confines of safe operating temperatures.
The substrate’s repertoire may extend further, incorporating features such as vias, solder balls, and ground planes, enriching the symphony of electrical performance, reliability, and the manufacturing cadence.
In summation, the package substrate emerges not just as a passive participant but as a dynamic orchestrator, a silent architect shaping the structural and electrical symphony that underlies the functionality and reliability of contemporary electronic devices.
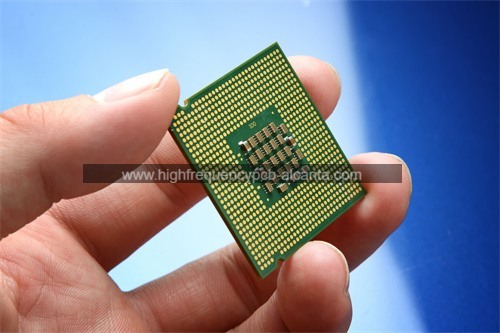
Package Substrate
What Specific Functions Does Package Substrate Have?
Enter the stage, the package substrate, a behind-the-scenes luminary in the dazzling world of electronic devices. This unsung hero dons a myriad of roles, each contributing to the symphony of seamless functionality and reliability of integrated circuits (ICs) and microelectronic packages. Let’s unravel the layers of its versatile responsibilities:
Electric Maestro: At its very essence, the substrate is the conductor of the electrical orchestra. Housing semiconductor chips, it orchestrates a ballet of conductive pathways — the traces and interconnects — allowing a harmonious exchange of electrical signals between the diverse pins and pads on the semiconductor devices.
Thermal Choreographer: Beyond the limelight, the substrate takes center stage in the thermal drama. With a repertoire including thermal vias, heat spreaders, and thermal planes, it dances gracefully to dissipate the heat generated during the electronic performance, ensuring a cool and composed environment for semiconductor devices.
Architect of Stability: Beyond the glitz of electrical prowess, the substrate provides a stoic foundation, offering the much-needed mechanical support to shield semiconductor chips from the tumultuous world of mechanical stress. In doing so, it becomes the guardian of the structural integrity of the electronic device.
Guardian of Signal Virtuosity: In the realm of signals, the substrate emerges as a virtuoso. Its intricate designs, thoughtful trace layouts, and measures to minimize signal cross-talk become the notes that compose the melody of signal integrity, ensuring the reliability of the electrical performance.
Power Maven: An efficient power distributor, the substrate conducts the energy symphony within the electronic ecosystem. Power planes and conductive pathways ensure a reliable and steady supply of power to the semiconductor devices, powering their electronic endeavors.
Master of Manufacturing Arts: More than just a performer, the substrate is a key player in the manufacturing spectacle. Solder pads, vias, and alignment marks become the choreography, streamlining the assembly processes, ensuring efficiency, and raising the curtain on high production yields.
Precision Timekeeper: The substrate, with its meticulous design, becomes the timekeeper in the electronic ensemble. Minimizing signal delays, upholding signal integrity, and synchronizing the rhythm, it ensures the electronic device dances in harmony within specified timing constraints.
EMC Custodian: In the cacophony of electromagnetic waves, the substrate dons the role of a custodian. Incorporating shielding and grounding techniques, it maintains electromagnetic harmony, reducing unwanted emissions and fortifying the device against external interferences.
In summary, the package substrate, far from a passive participant, emerges as a polymath, seamlessly weaving electrical, thermal, and mechanical elements into the intricate tapestry of electronic functionality. Its design is a bespoke creation, tailored to the unique needs of the electronic system, an indispensable artisan in the creation of today’s electronic marvels.
What Are the Different Types of Package Substrate?
Diverse as the needs of electronic devices may be, package substrates exhibit a rich array of types, each tailored to fulfill distinct requirements based on application nuances, thermal dynamics, and the unique demands posed by integrated circuits (ICs). Let’s explore the manifold varieties:
Printed Circuit Boards (PCBs): PCBs, stalwarts in the electronic realm, comprise layers of insulating material interspersed with conductive copper traces. Their versatility makes them a go-to choice across a myriad of applications.
Ceramic Substrates: Crafted from materials like alumina or aluminum nitride, ceramic substrates boast excellent thermal conductivity. They shine in high-power scenarios where efficient heat dissipation is paramount, as seen in power amplifiers and high-frequency devices.
Organic Substrates: Composed of materials such as epoxy resin and glass fiber, organic substrates balance cost-effectiveness with decent electrical insulation. They find favor in consumer electronics and applications where stringent thermal performance takes a back seat.
Flexible Substrates: These substrates, often hewn from polyimide, offer a pliable nature, allowing bending or flexing. Ideal for applications with form factor constraints, think wearable devices or the realm of flexible electronics.
Leadframe Packages: The marriage of substrate and package body occurs through a metal frame (leadframe). The semiconductor die attaches to the leadframe, with the leads serving as conduits for external connections. Cost-effectiveness makes these packages a stalwart in various applications.
System-in-Package (SiP) Substrates: SiP substrates redefine integration, corralling multiple chips or components within a solitary package. The substrate takes center stage, providing the playground for interconnecting and mounting diverse ICs.
Ball Grid Array (BGA) Substrates: The BGA dance involves an array of solder balls for external connections. The substrate, often a concoction of organic materials, facilitates the marriage of semiconductor die and electrical connections via those spherical soldiers.
Flip-Chip Substrates: Flip-chip elegance unfolds with the semiconductor die facing downward, its connection to the substrate orchestrated by solder bumps. High-performance applications with space constraints revel in the prowess of flip-chip substrates.
Multi-Chip Modules (MCM): The symphony of MCMs harmonizes multiple semiconductor chips within a singular module. The substrate, akin to a conductor’s podium, orchestrates interconnections, yielding a compact and efficient system.
Integrated Passive Devices (IPD): A substrate that wears multiple hats, integrating not just the semiconductor die but also passive components like resistors and capacitors. Efficiency thrives as the substrate itself becomes a realm of circuitry.
These substrates, akin to a diverse ensemble, cater to a symphony of electronic needs. The choice amongst them hinges on a delicate balance of application demands, thermal intricacies, and the unique character of the integrated circuits seeking a home.
How is Package Substrate Related to IC Packaging?
The intricate dance between package substrate and IC packaging reveals a symbiotic relationship, where the substrate serves as the silent orchestrator of a myriad of crucial functions within the realm of integrated circuits (ICs).
Picture the package substrate as the solid foundation on which the ICs find their home. It’s not just about physical support; it shields these delicate semiconductor components from the tumultuous forces of the environment and external handling, ensuring their structural integrity.
But the substrate’s role doesn’t stop there—it extends into the realm of electrical connectivity. Through a network of conductive pathways intricately woven into its fabric, the substrate becomes the maestro conducting the flow of electrical signals between the pins and pads of various ICs, facilitating a harmonious symphony of data exchange.
Heat, the inevitable byproduct of IC operation, finds a mitigating force in the substrate’s design. Thermal vias, heat spreaders, and thermal planes become the unsung heroes, aiding in the dissipation of heat away from the ICs and maintaining an environment conducive to optimal performance.
Imagine a scenario where multiple ICs coexist within a single package—enter the substrate as the architect of integration. In configurations like System-in-Package (SiP), the substrate orchestrates the layout and interconnection of diverse ICs, ensuring they work in tandem within the confined space of a singular package.
Various packaging technologies, from the familiar Ball Grid Array (BGA) to the avant-garde Flip-Chip, find their ally in the tailored design of the package substrate. It adapts to the specific demands of each technology, providing the necessary connectivity or solder ball arrays to bring these packaging methods to life.
Signal integrity, the lifeblood of electronic communication, is under the watchful eye of the substrate’s design. Through meticulous layout and impedance control, the substrate safeguards the quality and reliability of electrical signals traversing the interconnected ICs.
Size matters in the world of electronics, and the package substrate is the key to meeting form factor and size constraints. Its design allows for miniaturization, contributing to the sleekness and efficiency of electronic devices.
In essence, the package substrate is not just a passive participant; it is the unsung hero, the indispensable enabler in the ballet of IC packaging. It weaves together the physical, electrical, and thermal intricacies, ensuring the seamless integration and optimal performance of integrated circuits within the confines of electronic packages.
How Does Package Substrate Differ from Traditional PCBs?
Enter the realm of electronic connectivity, where package substrates and traditional printed circuit boards (PCBs) emerge as distinctive players with nuanced roles and characteristics.
Distinct Missions:
Package Substrate: Fashioned for a specific mission, package substrates take the lead in mounting and connecting semiconductor components within electronic packages. Their focus is honed to the specialized requirements of integrated circuits (ICs), ensuring an optimal stage for their performance.
Traditional PCB: The versatile maestros, traditional PCBs, orchestrate a broader ensemble of electronic components, extending beyond the confines of ICs. They serve as the canvas for a diverse composition of passive and active elements, embodying adaptability in electronic system design.
Compatibility Choreography:
Package Substrate: The choreography of package substrates is finely tuned for the dance of semiconductor chips. Elements like solder balls, vias, and traces are the deft moves, facilitating seamless integration and connection within the confined space of a compact package.
Traditional PCB: The dance floor of traditional PCBs accommodates a diverse cast of electronic components – resistors, capacitors, transistors, and connectors. Their adaptability allows for a harmonious arrangement to meet the unique demands of each electronic system.
Materials as Artistic Mediums:
Package Substrate: The palette for package substrates includes ceramics, organic laminates, and avant-garde materials like liquid crystal polymer (LCP). The choice is akin to selecting the perfect artistic medium, considering factors such as thermal dynamics, electrical traits, and the unique canvas of the packaged device.
Traditional PCB: Grounded in materials like fiberglass-reinforced epoxy (FR-4), traditional PCBs find their artistic expression in a blend of electrical insulation and cost-effectiveness, catering to a broad spectrum of electronic applications.
Thermal Symphony:
Package Substrate: Thermal considerations take center stage in the substrate’s symphony, with thermal vias, heat spreaders, and thermal planes performing a delicate dance to dissipate heat efficiently. This emphasis becomes crucial in the performance theaters of high-powered electronic devices.
Traditional PCB: Thermal considerations are not neglected in the design of traditional PCBs, adapting to the unique thermal requirements of the diverse components they house.
Applications as Stages:
Package Substrate: The spotlight of package substrates shines on stages where the integration of semiconductor devices into compact packages steals the show. Microprocessors, memory modules, and system-on-chip (SoC) devices embody their prowess.
Traditional PCB: Versatility takes center stage for traditional PCBs, performing in diverse applications ranging from consumer electronics to industrial machinery. They are the silent architects behind the scenes, crafting the backdrop for various electronic functions.
In summary, the electronic theater witnesses a dynamic interplay between package substrates and traditional PCBs, each with its own choreography, artistic expression, and stage presence. One excels in the specialized world of IC packaging, while the other embraces the diverse roles demanded by the broader spectrum of electronic applications.
What is the Main Structure and Production Technology of Package Substrate?
Embark on the journey of understanding the intricate structure and production technology that shapes package substrates, the unsung heroes of integrated circuits. The canvas begins with a foundational base material, a versatile palette that could be composed of ceramics, organic laminates, or the avant-garde liquid crystal polymer (LCP), chosen with a keen eye on thermal dynamics, electrical characteristics, and application-specific needs.
Layers unfold as dielectric layers delicately grace the substrate, forming insulating barriers that set the stage for the intricate dance of electrical pathways. Enter the conductive layers, often crafted from copper, etched and patterned with precision through processes like photolithography, weaving a network that orchestrates the seamless flow of electrical signals.
A solder mask, akin to a protective cloak, is carefully applied, leaving strategic openings where soldering is destined to occur. This mask shields the substrate from the elements, preventing unintended electrical connections from disrupting the electronic symphony. Surface finishes, whether gleaming with immersion gold or adopting the steadfast tin-lead, prepare the substrate for the crucial act of soldering.
The narrative unfolds with areas earmarked for semiconductor chips, passive components, and bonding pads. These regions become the designated stages where components will find their place, held in position through processes like die attachment, wire bonding, or the elegant flip-chip bonding.
The curtain rises on testing and inspection, a meticulous performance review ensuring the integrity of the circuitry, the fidelity of electrical connections, and the overall functionality of the substrate. It’s a symphony of precision, where every note, every connection is scrutinized to meet the demanding standards of electronic excellence.
The final act involves the integration of the substrate into its ultimate package. Here, additional components may join the ensemble, encapsulation may embrace the assembly, and protective measures ensure the resilience of the substrate in its electronic habitat.
This, in essence, is the tale of package substrates—a narrative that combines artistry and technology, where the marriage of materials, the choreography of layers, and the precision of processes converge to give life to the silent foundations of integrated circuits.
FAQs
What is a package substrate?
A package substrate is a crucial component in electronic devices, serving as a foundation for mounting and interconnecting semiconductor chips or integrated circuits (ICs) within a packaged device.
What is the main function of a package substrate?
The main function of a package substrate is to provide a physical and electrical platform for the integration of semiconductor chips. It facilitates the mounting of ICs, establishes electrical connections, and contributes to heat dissipation.
What materials are commonly used in package substrates?
Package substrates can be made from various materials, including ceramics (such as alumina or aluminum nitride), organic laminates (epoxy resin and glass fiber), and advanced materials like liquid crystal polymer (LCP). The choice depends on factors like thermal performance and application requirements.
How does a package substrate differ from a traditional PCB?
While both serve in electronic connectivity, a package substrate is specialized for IC packaging, focusing on mounting and interconnecting semiconductor chips. In contrast, a traditional printed circuit board (PCB) accommodates a broader range of electronic components beyond ICs.
What is the production process for package substrates?
The production process involves preparing the substrate material, applying dielectric layers, forming conductive layers, applying a solder mask, adding a surface finish, mounting components, and conducting rigorous testing and inspection to ensure functionality.
What role does thermal management play in package substrates?
Thermal management is crucial in package substrates to dissipate heat generated by the semiconductor chips. Features like thermal vias, heat spreaders, and thermal planes are incorporated to ensure efficient heat dissipation.
What are some common types of package substrates?
Common types include printed circuit boards (PCBs), ceramic substrates, organic substrates, flexible substrates (polyimide), leadframe packages, ball grid array (BGA) substrates, flip-chip substrates, and integrated passive devices (IPD), among others.
In what applications are package substrates used?
Package substrates find applications in a wide range of electronic devices, including consumer electronics, telecommunications equipment, automotive electronics, medical devices, and industrial machinery.
How does the design of package substrates impact signal integrity?
The design of package substrates, including proper layout and impedance control, plays a crucial role in preserving signal integrity. It ensures that electrical signals traveling between interconnected ICs maintain their quality and reliability.
What is the significance of package substrates in System-in-Package (SiP) technology?
In SiP technology, package substrates play a key role in integrating multiple chips or components within a single package. The substrate serves as a platform for interconnecting and mounting different ICs, enabling compact and efficient system integration.
Conclusion
In the grand tapestry of electronic components, package substrates stand as the unsung heroes, weaving the intricate connections that power our modern devices. As we conclude our exploration, it becomes evident that these substrates are not mere platforms; they are the silent conductors orchestrating the symphony of integrated circuits.
From the diverse materials that form their foundation—ceramics, organic laminates, or avant-garde liquid crystal polymers—to the meticulous production processes that bring them to life, package substrates embody a fusion of technology and artistry. Their ability to provide both a physical structure and electrical connectivity for semiconductor chips places them at the heart of electronic innovation.
The dance of conductive layers, the protective embrace of solder masks, and the strategic application of surface finishes create a harmonious composition. Yet, it is in the thermal ballet where package substrates truly shine, adeptly managing the heat generated by semiconductor chips with features like thermal vias and heat spreaders.
As the curtain falls on our exploration, we see package substrates not as passive elements, but as dynamic enablers of progress. Their role extends beyond the visible, influencing signal integrity, accommodating diverse types, and finding applications in a plethora of electronic devices.
In the world of System-in-Package (SiP) technology, these substrates take center stage, seamlessly integrating multiple chips within a confined space—a testament to their adaptability and efficiency.
In essence, package substrates are the silent architects of our electronic landscape. Through their nuanced design, diverse materials, and pivotal role in integration, they lay the foundation for the technological marvels that define our interconnected world. As we applaud the elegance of their design and the resilience of their performance, let us recognize the indelible mark that package substrates leave on the canvas of electronic innovation.