Organic Substrate FC BGA Substrate Manufacturer
Organic Substrate FC BGA Substrate Manufacturer,The Organic Substrate FC BGA substrate is a key component in semiconductor packaging, employing organic materials for enhanced flexibility and cost efficiency. This substrate supports Flip Chip Ball Grid Array (FC BGA) packaging, enabling direct chip-to-board connections. Composed of multiple layers including organic insulators, conductors, and metal layers, it ensures reliable electrical connections and efficient heat dissipation. The organic substrate’s flexibility accommodates miniaturization and space optimization, vital for modern electronic devices. It finds applications in various industries including consumer electronics, telecommunications, and automotive, where cost-effective packaging solutions with reliable performance are essential.
Organic Substrate FC BGA Substrate stands out as a key player in the realm of integrated circuit packaging, finding its niche in the domain of high-density and high-performance chip encapsulation, notably within the Ball Grid Array (BGA) framework. This nomenclature encapsulates a substrate crafted from organic materials, typically a resin fortified with glass fibers, serving as the linchpin for supporting and interconnecting integrated circuits.
BGA packaging, an advanced methodology facilitating chip-to-printed circuit board (PCB) linkage via solder balls, takes a distinctive turn in the case of Organic Substrate FC BGA. Here, the approach involves a “Flip-Chip Ball Grid Array,” wherein the chip undergoes a literal flip, positioning its connection points on the underside and establishing links with the substrate through solder balls.
The perks of this substrate variant are manifold, encompassing reduced inductance, amped-up thermal efficiency, and an elevated capacity for integration. Tailored to applications hungry for high-speed signal transmission and intricate circuitry, it finds its stride in sectors like high-performance computing, communication gadgets, and graphic processors. The economic allure of manufacturing organic substrates further burnishes its appeal, especially in the landscape of large-scale production.
In sum, Organic Substrate FC BGA Substrate emerges as a linchpin in the contemporary electronic landscape, furnishing an effective blueprint for the reliable packaging and linkage of high-octane chips.
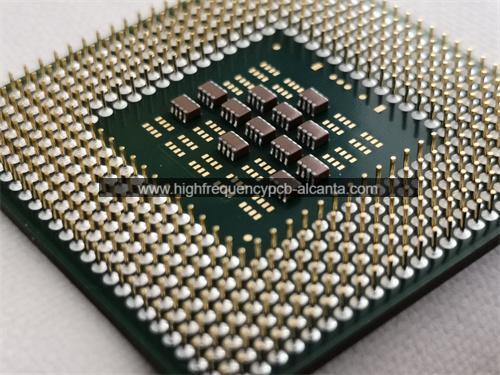
Organic Substrate FC BGA substrate Manufacturer
What Functions Does Organic Substrate FC BGA Substrate Serve?
Organic Substrate FC BGA Substrate is the maestro orchestrating a diverse array of functions within the intricate ballet of integrated circuit packaging, crafting the symphony that defines the performance and reliability of electronic devices:
Robust Foundation for Integrated Circuits: At its essence, the organic substrate lays the groundwork, providing a steadfast stage for the intricate choreography of placing and interconnecting integrated circuits (ICs).
Conduit for Effortless Electrical Connectivity: Acting as a conduit, the substrate ensures the fluid transmission of electrical connections. It enables a seamless dance of signals between integrated circuits and other components on the printed circuit board (PCB).
Mastery of Thermal Ballet: A central performance involves the substrate’s mastery of the thermal ballet within integrated circuits. By gracefully dissipating the heat generated during IC operation, it ensures a performance of optimal efficiency and reliability, gracefully averting the risk of overheating.
Guardian of Mechanical Harmony: Beyond its electrical and thermal roles, the substrate serves as a vigilant guardian, offering essential mechanical support to integrated circuits. This support is a harmonious dance, shielding ICs from the strains of mechanical stresses and vibrations throughout the lifecycle of the device.
Architect of Flip-Chip Choreography: In the realm of FC BGA, the substrate transforms into an architect of choreography, facilitating the implementation of the Flip-Chip technique. This dance places IC connection points on the underside, orchestrating a performance that optimizes signal paths and minimizes inductance with grace.
Solder Ball Ensemble for Connectivity: The BGA element introduces an ensemble of solder balls, orchestrating robust connections between ICs and the PCB. This ensemble not only streamlines the assembly with finesse but also enhances the reliability of connections, contributing to the overall durability of the electronic ensemble.
Tailored Performance for High-Speed Symphony: Organic Substrate FC BGA Substrate is a virtuoso, tailor-made to conduct the high-speed symphony demanded by applications requiring swift signal transmission and intricate circuitry. Its design and composition harmonize to minimize signal loss, creating an overall crescendo of electronic efficacy.
In conclusion, Organic Substrate FC BGA Substrate takes on a multifaceted role, conducting a ballet of functions related to electrical connectivity, thermal grace, mechanical resilience, and the integration of avant-garde packaging technologies. This symphony caters to the nuanced demands of contemporary high-performance electronic devices.
Are There Different Types of Organic Substrate FC BGA Substrate?
Within the realm of Organic Substrate FC BGA Substrate, a tapestry of diversity unfolds, revealing a spectrum of types that adapt to specific requisites and technological strides. While the overarching term signifies a genre of substrate technology amalgamating organic materials with the Flip-Chip Ball Grid Array (FC BGA) packaging methodology, intricacies emerge in terms of materials, design nuances, and targeted applications. Here are several facets illuminating this rich tapestry:
Material Symphony:
Glass Fiber-Reinforced Resin: A prevalent choice involves a substrate rooted in resin fortified with glass fibers, fortifying its resilience.
Polymer Ballet: Alternately, some substrates gracefully dance with diverse polymer-based materials, introducing variations in thermal conductivity and electrical properties.
Technological Choreography:
Advanced Dielectric Materials: An ongoing ballet incorporates cutting-edge dielectric materials, enhancing the substrate’s performance in realms such as signal integrity and thermal modulation.
Innovative Manufacturing Pas de Deux: Variations pirouette into existence as manufacturing processes gracefully evolve, integrating new technologies to enhance precision and efficiency.
Application-Specific Rhythms:
High-Speed Sonata: Tailored for high-speed applications, some substrates conduct a symphony that optimizes signal paths, minimizing signal loss with a melodic finesse.
High-Density Ensemble: Other compositions are orchestrated for high-density packaging, allowing for a crescendo of connections within a confined space.
Customized Designs:
Size and Form Factor Ballet: The stage is set with substrates donning diverse sizes and form factors, choreographing performances that align with specific device requirements.
Layer Configuration Waltz: The dance continues with variations in layer configurations, harmonizing with the complexity of integrated circuits and the distinctive demands of diverse applications.
Market-Specific Overture:
Consumer Electronics vs. Industrial Symphony: Distinct movements unfold based on whether substrates are crafted for the rhythm of consumer electronics, where compactness and efficiency are spotlighted, or for the industrial overture, where resilience and reliability take center stage.
It’s paramount to recognize that the orchestra of Organic Substrate FC BGA Substrate types is dynamic, evolving with the cadence of technological advancements and the ever-shifting demands of diverse industries and applications. Manufacturers, as virtuosos, continually fine-tune their compositions to resonate with the evolving symphony of the electronics market.
Is Organic Substrate FC BGA Substrate Related to IC Packaging?
Certainly, the relationship between Organic Substrate FC BGA Substrate and integrated circuit (IC) packaging is pivotal in the intricate dance of semiconductor device manufacturing.
Integral to IC Packaging Ballet: In the elaborate performance of IC packaging, the substrate takes on a leading role. This phase revolves around encapsulating the semiconductor die within a protective package, providing not only a shield against environmental factors but also the necessary infrastructure for electrical connections, thermal equilibrium, and mechanical fortification.
Essential Choreography of the Substrate: Within this grand production, the substrate emerges as a key player, providing the stage for the semiconductor die to shine. Crafted from materials like resin fortified with glass fibers, organic substrates form the foundation, influencing the electrical behavior, thermal dynamics, and overall robustness of the IC package.
Innovative Moves with FC BGA Technology: The Organic Substrate FC BGA Substrate introduces a dynamic twist to this performance. The Flip-Chip Ball Grid Array (FC BGA) technique orchestrates a daring move – flipping the semiconductor die and placing it in an inverted position on the substrate. This not only shortens the connections but also introduces a more direct and efficient pathway for electrical signals. The substrate, adorned with an array of solder balls, becomes the connector extraordinaire, forging the link between the IC and the printed circuit board (PCB).
In the narrative of Organic Substrate FC BGA Substrate, we uncover a captivating subplot within IC packaging. This symbiotic duo is engineered to enhance the overall efficiency, reliability, and performance of the integrated circuit packaging spectacle, particularly in arenas where the demand for high-density and high-performance chip packaging takes center stage.
How Does Organic Substrate FC BGA Substrate Differ from Ordinary PCBs?
Organic Substrate FC BGA Substrate and conventional Printed Circuit Boards (PCBs) traverse distinct trajectories, each defined by unique characteristics in purpose, packaging methodology, material composition, and application scope.
Tailored Precision vs. Universal Versatility:
Organic Substrate FC BGA Substrate: Meticulously crafted for the art of integrated circuit (IC) packaging, featuring the innovative Flip-Chip Ball Grid Array (FC BGA) technology. This precision is aimed at meeting the demands of high-density IC mounting, particularly in realms where advanced signal transmission and efficient thermal management take center stage.
Ordinary PCBs: Embrace a more universal role, acting as versatile canvases for hosting an array of electronic components. Unlike their specialized counterpart, they lack the intricate optimizations tailored to the specific demands of advanced IC packaging.
Packaging Choreography:
Organic Substrate FC BGA Substrate: Dances to the beat of FC BGA packaging technology, orchestrating a transformative flip for ICs and connecting them through solder balls. This dynamic choreography enhances both electrical performance and thermal dissipation, a spectacle tailored for the demands of high-performance applications.
Ordinary PCBs: Engage in a more conventional dance, relying on methods such as Surface Mount Technology (SMT) or Through-Hole Technology (THT). These methods lack the specialized flair of FC BGA, catering to a broader spectrum of applications.
Material Symphony:
Organic Substrate FC BGA Substrate: Composed of organic materials, often a fusion of resin fortified with glass fibers. The selection of materials is an artistic endeavor, finely tuned to the intricate demands of IC packaging, emphasizing not just functionality but performance and reliability.
Ordinary PCBs: Showcase a symphony of material choices, from fiberglass-reinforced epoxy to paper-reinforced phenolic resin. Material selection leans towards considerations such as cost and general applicability, without the precision demanded by the specialized IC packaging realm.
Performance Theater:
Organic Substrate FC BGA Substrate: Takes center stage in high-performance applications, where the nuances of swift signal transmission, minimal inductance, and effective thermal management are critical. Its performance theater finds resonance in domains like high-end computing, graphics processing, and advanced communication devices.
Ordinary PCBs: Feature in a broader ensemble, contributing to a variety of electronic devices ranging from consumer electronics to industrial machinery. Their design considerations may not be as finely tuned for the intricate demands of specialized IC packaging.
In essence, Organic Substrate FC BGA Substrate emerges as a virtuoso, finely attuned to the nuances of advanced IC packaging, while ordinary PCBs play a versatile role across the broader landscape of electronic applications.
What is the Structure and Production Technology of Organic Substrate FC BGA Substrate?
The structure and production technology of Organic Substrate FC BGA Substrate involve several key elements, including the substrate’s composition, layers, and the manufacturing processes used. Here’s an overview:
Structure:
Base Material:
The base material of Organic Substrate FC BGA Substrate is typically organic, often composed of a resin matrix reinforced with materials like glass fibers. This choice of material provides a balance of mechanical strength, thermal performance, and electrical properties.
Layers:
The substrate is designed with multiple layers to accommodate the complex interconnections and requirements of integrated circuits. The layers may include conductive traces, dielectric materials, and possibly additional features like power and ground planes.
Copper Traces:
Copper traces are patterned on the substrate to form the electrical pathways that connect various components, including the integrated circuits, on the substrate.
Dielectric Layers:
Dielectric layers insulate the conductive traces, preventing unintended electrical interactions and ensuring signal integrity. The dielectric material used should have suitable electrical properties and thermal conductivity.
Solder Balls (for FC BGA):
In the context of FC BGA technology, the substrate features an array of solder balls on its surface. These solder balls serve as the connection points between the integrated circuit (IC) and the printed circuit board (PCB). FC BGA allows for a more direct connection between the IC and the substrate, enhancing electrical performance.
Production Technology:
Substrate Fabrication:
The production process begins with the fabrication of the substrate. This involves creating multiple layers with the desired material properties. The choice of materials and their arrangement is crucial for achieving the required electrical and thermal characteristics.
Copper Tracing:
Copper traces are then patterned onto the substrate layers using processes like photolithography. These traces form the intricate pathways that carry electrical signals throughout the substrate.
Dielectric Layer Deposition:
Dielectric materials are deposited between the copper traces to insulate them from each other. This is essential for preventing short circuits and ensuring the reliability of the substrate.
FC BGA Integration:
If FC BGA technology is employed, the substrate undergoes a specific integration process for accommodating the flipped IC and solder ball connections. This may involve precision placement of the IC on the substrate, followed by the attachment of solder balls.
Quality Control:
Rigorous quality control measures are implemented throughout the production process to ensure the substrate meets the specified standards for performance, reliability, and dimensional accuracy.
Final Assembly:
Once the substrate is fabricated and the necessary components are integrated, it becomes part of the larger assembly process, where it is connected to other elements on the printed circuit board.
The production technology of Organic Substrate FC BGA Substrate demands precision and attention to detail to meet the stringent requirements of modern high-performance electronic devices. Continuous advancements in materials and manufacturing techniques contribute to the ongoing refinement of these substrates.
Frequently Asked Questions (FAQs)
How does FC BGA technology differ from other packaging methods?
FC BGA introduces a unique approach by flipping the semiconductor die and mounting it inverted on the substrate. This results in more direct connections, improving electrical performance and bolstering thermal dissipation compared to conventional packaging methods.
Which electronic devices benefit from Organic Substrate FC BGA Substrate?
Devices requiring high-density and high-performance IC packaging experience significant advantages. This includes applications in high-end computing, graphics processors, communication devices, and other electronics where efficient signal transmission and thermal management are critical.
What does the production process of Organic Substrate FC BGA Substrate involve?
The production process encompasses substrate fabrication, copper tracing, dielectric layer deposition, potential integration of FC BGA technology, and rigorous quality control measures. Precision in manufacturing is paramount to meet stringent performance standards.
How can one select the right manufacturer for specific applications?
Considerations include the manufacturer’s experience, industry reputation, product portfolio, adherence to quality standards, and their capability to customize solutions for specific application requirements.
Are there variations in Organic Substrate FC BGA Substrate for different applications?
Yes, variations exist based on factors like materials used, design configurations, and intended applications. Some substrates may be optimized for high-speed applications, while others focus on high-density packaging or cater to specific industries.
How can I obtain more information or contact a manufacturer for specific inquiries?
Explore the official website of the manufacturer, engage with their customer support, or reach out to their sales representatives for detailed information and assistance with specific inquiries regarding Organic Substrate FC BGA Substrate.
Conclusion
In summary, the Frequently Asked Questions (FAQs) provide a thorough exploration of Organic Substrate FC BGA Substrate, shedding light on its intricate nature and pivotal role in advancing integrated circuit (IC) packaging.
The FAQs navigate through the substrate’s essential functions in IC packaging, emphasizing its significance in offering a robust foundation for IC mounting, enabling seamless electrical connections, and effectively managing thermal considerations. The distinctiveness of FC BGA technology, dissected within the FAQs, underscores its superiority in enhancing electrical performance and optimizing thermal dissipation compared to conventional packaging methods.
A closer examination of material selection, particularly the use of resin matrices reinforced with glass fibers, underscores the precision required to achieve the desired mechanical, thermal, and electrical properties. The FAQs also highlight the versatile applications of Organic Substrate FC BGA Substrate across various high-performance electronic devices, spanning computing and communication systems.
The manufacturing process, intricately detailed in the FAQs, emphasizes the need for meticulous precision and stringent quality control measures. Additionally, the outlined criteria for selecting an exemplary manufacturer underscore the importance of experience, industry reputation, and a commitment to innovation to meet the evolving demands of diverse applications.
In essence, the FAQs offer a comprehensive narrative, demystifying the complexities of Organic Substrate FC BGA Substrate and positioning it as a cornerstone in shaping the landscape of electronic packaging technologies.