Organic Substrate FC-BGA Design Guideline
Organic Substrate FC-BGA Design Guideline,Organic Substrate FC-BGA (Flip Chip Ball Grid Array) is a cutting-edge packaging technology revolutionizing the semiconductor industry. It entails mounting integrated circuits (ICs) onto an organic substrate using a flip chip configuration, where the active side of the IC is flipped and connected directly to the substrate using tiny solder bumps or balls. This innovative approach offers numerous benefits, including enhanced electrical performance, improved thermal management, and cost-effectiveness compared to traditional packaging methods. With its high-density interconnects and efficient signal transmission capabilities, Organic Substrate FC-BGA is well-suited for a wide range of applications, from high-performance computing to mobile devices and automotive electronics. Its versatility, reliability, and scalability make it a preferred choice for manufacturers seeking advanced packaging solutions to meet the demands of today’s rapidly evolving technology landscape.
What is an Organic Substrate FC-BGA?
An Organic Substrate FC-BGA (Flip Chip Ball Grid Array) refers to a type of packaging technology used in integrated circuits (ICs) and semiconductor devices. Let’s break down the term:
- Organic Substrate: This refers to the material on which the integrated circuit is mounted. In semiconductor packaging, substrates are typically made of materials like fiberglass-reinforced epoxy resin (FR-4), which is an organic material. Organic substrates are commonly used due to their lower cost and good electrical properties.
- FC-BGA (Flip Chip Ball Grid Array): This is a type of packaging arrangement for integrated circuits. In a flip-chip configuration, the active side of the IC (the side containing the actual circuitry) is flipped upside down and connected directly to the substrate or carrier using tiny solder bumps or balls. The BGA part refers to the array of solder balls arranged in a grid on the underside of the package, which provide electrical connections to the circuit board.
Putting it together, an Organic Substrate FC-BGA is a packaging technology where the integrated circuit is mounted on an organic substrate using a flip-chip configuration, with solder balls forming a grid array for electrical connections. This technology is commonly used in a variety of electronic devices, including computers, smartphones, and other consumer electronics.
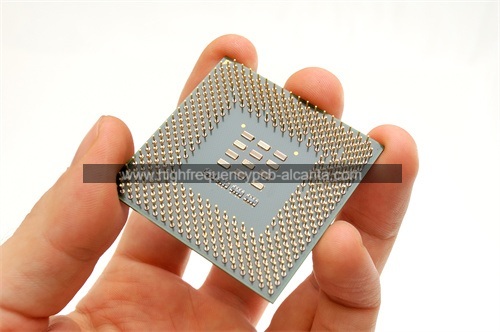
Organic Substrate FC-BGA Design Guideline
What are the Design Guidelines for Organic Substrate FC-BGA?
Design guidelines for Organic Substrate FC-BGA packaging typically encompass several key considerations to ensure successful integration and performance. These guidelines may include:
- Thermal Management: Proper thermal management is crucial to prevent overheating of the integrated circuit. Designers must consider factors such as thermal vias, heat spreaders, and the layout of power and ground planes to optimize heat dissipation.
- Electrical Performance: Designers should ensure that the routing of signal traces, power, and ground planes adheres to best practices to minimize signal interference, crosstalk, and impedance mismatches. Maintaining controlled impedance is particularly important for high-speed signal integrity.
- Signal Integrity: Signal integrity considerations involve maintaining signal quality throughout the PCB (Printed Circuit Board) layout. This includes minimizing signal reflections, ensuring signal integrity in high-speed signal paths, and managing impedance matching.
- Power Delivery: Adequate power delivery is essential to ensure stable operation of the integrated circuit. Designers must carefully plan power distribution networks, including power plane design and decoupling capacitor placement, to minimize voltage drops and noise.
- Mechanical Stability: The mechanical stability of the FC-BGA package is crucial to prevent damage during handling and operation. Designers should consider factors such as package warpage, solder joint reliability, and mechanical stress during assembly.
- Manufacturability and Assembly: Design guidelines should also take into account manufacturability and assembly considerations to ensure cost-effective production. This includes considerations such as solder paste stencil design, component placement accuracy, and assembly process compatibility.
- Reliability and Robustness: Designers must prioritize reliability and robustness to ensure the long-term performance and durability of the FC-BGA package. This involves considering factors such as material selection, environmental conditions, and reliability testing.
Overall, adhering to these design guidelines helps ensure the successful development and deployment of Organic Substrate FC-BGA packages, minimizing risks and optimizing performance in various electronic applications.
What is the Fabrication Process for Organic Substrate FC-BGA?
The fabrication process for Organic Substrate FC-BGA (Flip Chip Ball Grid Array) involves several steps, including substrate fabrication, flip chip attachment, ball attachment, and assembly. Here’s an overview of the typical fabrication process:
- Substrate Fabrication:
– Substrate Preparation: The process begins with the preparation of the organic substrate material, often FR-4 or similar materials. The substrate is typically in the form of a laminate with multiple layers of fiberglass and epoxy resin.
– Layer Stacking: Multiple layers of dielectric material and conductive traces are stacked and laminated together to form the substrate structure. These layers are patterned using photolithography and etching processes to create the required circuitry and vias.
– Surface Preparation: The surface of the substrate is prepared for subsequent attachment processes, typically involving cleaning and surface treatment to promote adhesion.
- Flip Chip Attachment:
– Die Preparation: Integrated circuit chips (ICs) are prepared for attachment by applying solder bumps or balls to the bonding pads on the chip’s active side. This process can involve wafer-level processing techniques.
– Alignment and Bonding: The IC chips are aligned and bonded to the substrate using flip chip bonding equipment. This process typically involves aligning the solder bumps on the chip with corresponding pads on the substrate and then bonding them using controlled pressure and heat.
- Ball Attachment:
– Solder Ball Placement: Solder balls are placed onto the exposed bonding pads on the substrate using techniques such as solder paste stencil printing or solder ball placement equipment.
– Reflow Soldering: The substrate with attached solder balls is subjected to reflow soldering, where it is heated to melt the solder balls and create reliable electrical connections between the substrate and the IC chips.
- Assembly:
– Underfill Encapsulation: An underfill material may be applied between the IC chips and the substrate to enhance mechanical strength and reliability. This material is typically dispensed and cured under the IC chips.
– Final Assembly: Additional components, such as passive components or heat sinks, may be assembled onto the substrate to complete the packaging process.
- Testing and Inspection:
– Functional Testing: The assembled FC-BGA packages undergo functional testing to ensure proper electrical functionality.
– Inspection: Visual inspection and various testing methods, such as X-ray inspection and automated optical inspection (AOI), are performed to detect any defects or anomalies in the packaging process.
- Packaging and Shipping:
– Packaging: The completed FC-BGA packages are packaged according to industry standards and customer requirements.
– Shipping: The packaged FC-BGA devices are then shipped to customers for integration into electronic products.
Throughout the fabrication process, quality control measures are implemented to ensure the reliability and performance of the Organic Substrate FC-BGA packages. These measures include process monitoring, defect detection, and adherence to industry standards and specifications.
How do you manufacture an Organic Substrate FC-BGA?
Manufacturing an Organic Substrate FC-BGA (Flip Chip Ball Grid Array) involves several steps, including substrate fabrication, chip attachment, ball attachment, and assembly. Here’s a detailed overview of the manufacturing process:
- Substrate Fabrication:
– Substrate Preparation: The manufacturing process begins with the preparation of the organic substrate material, typically FR-4 (fiberglass-reinforced epoxy resin) or similar materials.
– Layer Stacking: Multiple layers of dielectric material and conductive traces are stacked and laminated together to form the substrate structure. These layers are patterned using photolithography and etching processes to create the required circuitry and vias.
– Surface Preparation: The surface of the substrate is prepared for subsequent attachment processes, involving cleaning and surface treatment to promote adhesion.
- Chip Attachment:
– Die Preparation: Integrated circuit chips (ICs) are prepared for attachment by applying solder bumps or balls to the bonding pads on the chip’s active side. This process may involve wafer-level processing techniques.
– Alignment and Bonding: The IC chips are aligned and bonded to the substrate using flip chip bonding equipment. This process typically involves aligning the solder bumps on the chip with corresponding pads on the substrate and then bonding them using controlled pressure and heat.
- Ball Attachment:
– Solder Ball Placement: Solder balls are placed onto the exposed bonding pads on the substrate using techniques such as solder paste stencil printing or solder ball placement equipment.
– Reflow Soldering: The substrate with attached solder balls undergoes reflow soldering, where it is heated to melt the solder balls and create reliable electrical connections between the substrate and the IC chips.
- Assembly:
– Underfill Encapsulation: An underfill material may be applied between the IC chips and the substrate to enhance mechanical strength and reliability. This material is typically dispensed and cured under the IC chips.
– Final Assembly: Additional components, such as passive components or heat sinks, may be assembled onto the substrate to complete the packaging process.
- Testing and Inspection:
– Functional Testing: The assembled FC-BGA packages undergo functional testing to ensure proper electrical functionality.
– Inspection: Visual inspection and various testing methods, such as X-ray inspection and automated optical inspection (AOI), are performed to detect any defects or anomalies in the packaging process.
- Packaging and Shipping:
– Packaging: The completed FC-BGA packages are packaged according to industry standards and customer requirements.
– Shipping: The packaged FC-BGA devices are then shipped to customers for integration into electronic products.
Throughout the manufacturing process, quality control measures are implemented to ensure the reliability and performance of the Organic Substrate FC-BGA packages. These measures include process monitoring, defect detection, and adherence to industry standards and specifications.
How much should an Organic Substrate FC-BGA cost?
The cost of an Organic Substrate FC-BGA (Flip Chip Ball Grid Array) can vary significantly depending on various factors, including the complexity of the design, the size of the substrate, the number of layers, the type of materials used, manufacturing volume, and additional features such as advanced thermal management or special testing requirements.
In general, Organic Substrate FC-BGA packages are often more cost-effective compared to other advanced packaging technologies like ceramic substrates or silicon interposers. However, they still involve several manufacturing processes and materials, which contribute to their overall cost.
To provide a rough estimate, the cost of an Organic Substrate FC-BGA package can range from a few cents to several dollars per unit in high volume production. However, for more precise pricing, it’s essential to consult with semiconductor packaging suppliers or contract manufacturers who can provide quotes based on specific project requirements and volume levels.
What is Organic Substrate FC-BGA base material?
The base material for an Organic Substrate FC-BGA (Flip Chip Ball Grid Array) is typically a type of organic laminate, commonly referred to as FR-4 (Flame Retardant 4). FR-4 is a widely used material in electronics manufacturing, particularly for printed circuit boards (PCBs) and substrates.
FR-4 consists of layers of woven fiberglass cloth impregnated with an epoxy resin binder. This combination provides excellent electrical insulation properties, mechanical strength, and dimensional stability. Additionally, FR-4 is relatively inexpensive compared to alternative materials such as ceramics, making it a popular choice for organic substrate applications.
In the context of FC-BGA packages, FR-4 serves as the substrate on which the integrated circuit (IC) chips are mounted. It provides the structural support and electrical interconnections necessary for the proper functioning of the packaged ICs. The FR-4 substrate is typically fabricated using processes such as layer stacking, photolithography, etching, and surface treatment to create the required circuitry, vias, and bonding pads.
Which company manufactures Organic Substrate FC-BGA?
Manufacturing of Organic Substrate FC-BGA (Flip Chip Ball Grid Array) is typically carried out by semiconductor packaging and electronics manufacturing companies. Some well-known companies such as Intel, Taiwan Semiconductor Manufacturing Company (TSMC), United Microelectronics Corporation (UMC), Qualcomm, among others, have extensive experience in semiconductor packaging and may offer Organic Substrate FC-BGA manufacturing services.
Our company is also a professional semiconductor packaging and electronics manufacturing enterprise, equipped with advanced production equipment, rich technical experience, and efficient production processes. We have the following characteristics and advantages:
- Technical Strength: We have an experienced and skilled R&D team capable of addressing complex Organic Substrate FC-BGA design and manufacturing requirements. We continuously invest in research and development to maintain a leading position in the semiconductor packaging field.
- Production Capacity: We have advanced production equipment and process technology to meet large-scale production needs. Our production lines adopt automation and intelligent technology, improving production efficiency and product quality.
- Quality Control: We strictly adhere to the ISO quality management system and have established a comprehensive quality control system. From raw material procurement to finished product delivery, we conduct rigorous inspection and testing to ensure products meet customer requirements and standards.
- Customization Services: We provide flexible customization services to tailor product specifications, process flows, and quality standards according to customer requirements. We can quickly respond to customer needs and provide personalized solutions.
- Customer Service: We prioritize communication and cooperation with customers, always putting customer needs first. We provide timely technical support and after-sales service to ensure customer satisfaction with our products and services.
With our company’s professional capabilities and high-quality service, we can provide customers with high-quality Organic Substrate FC-BGA products to meet their application needs in the electronics field. We are willing to collaborate with customers to promote the development of the electronics industry and achieve mutual benefits and win-win goals.
What are the 7 qualities of good customer service?
The 7 qualities of good customer service are:
- Responsiveness: Good customer service involves being prompt and responsive to customer inquiries, requests, and concerns. Customers appreciate timely assistance and expect their needs to be addressed promptly.
- Empathy: Empathy is the ability to understand and relate to the customer’s feelings, concerns, and perspectives. Good customer service representatives listen actively, show genuine concern for the customer’s situation, and strive to empathize with their experiences.
- Clear Communication: Effective communication is essential for good customer service. Customer service representatives should communicate clearly and concisely, ensuring that customers understand the information provided and feel confident in the solutions offered.
- Problem-solving Skills: Good customer service requires strong problem-solving skills to address customer issues and resolve conflicts effectively. Customer service representatives should be resourceful, proactive, and capable of finding solutions that meet the customer’s needs.
- Professionalism: Professionalism involves maintaining a positive attitude, remaining courteous and respectful, and upholding high ethical standards in all interactions with customers. Good customer service representatives conduct themselves professionally at all times, regardless of the situation.
- Product Knowledge: Having a thorough understanding of the products or services offered is crucial for providing good customer service. Customer service representatives should be knowledgeable about the features, benefits, and usage of the products or services, enabling them to provide accurate information and assistance to customers.
- Follow-up and Follow-through: Good customer service extends beyond the initial interaction. Customer service representatives should follow up with customers to ensure that their issues have been resolved satisfactorily and follow through on any promises or commitments made during the interaction. This demonstrates accountability and reinforces trust and loyalty with the customer.
FAQs
What is an Organic Substrate FC-BGA?
An Organic Substrate FC-BGA is a type of packaging technology used in integrated circuits (ICs) and semiconductor devices. It involves mounting the ICs on an organic substrate using flip chip bonding, with solder balls forming a grid array for electrical connections.
What are the advantages of Organic Substrate FC-BGA?
Organic Substrate FC-BGA offers several advantages, including lower cost compared to alternatives like ceramic substrates, good electrical properties, and compatibility with high-volume manufacturing processes.
What materials are used in Organic Substrate FC-BGA?
The base material for Organic Substrate FC-BGA is typically a type of organic laminate, such as FR-4 (Flame Retardant 4), which consists of layers of fiberglass cloth impregnated with epoxy resin.
What are the key considerations in the design of Organic Substrate FC-BGA?
Design considerations include thermal management, electrical performance, signal integrity, power delivery, mechanical stability, manufacturability, and reliability.
How is Organic Substrate FC-BGA manufactured?
The manufacturing process involves substrate fabrication, chip attachment (flip chip bonding), ball attachment (solder ball placement and reflow soldering), assembly (including underfill encapsulation), testing, and packaging.
What is the cost of Organic Substrate FC-BGA?
The cost varies depending on factors such as design complexity, substrate size, materials used, manufacturing volume, and additional features. It can range from a few cents to several dollars per unit in high-volume production.
Which companies manufacture Organic Substrate FC-BGA?
Companies specializing in semiconductor packaging and electronics manufacturing, such as Intel, TSMC, UMC, and Qualcomm, may offer Organic Substrate FC-BGA manufacturing services.
What are the quality standards for Organic Substrate FC-BGA?
Quality standards may vary depending on customer requirements and industry regulations. Common standards include ISO 9001 for quality management and IPC standards for electronic assemblies.
What applications are suitable for Organic Substrate FC-BGA?
Organic Substrate FC-BGA is used in various electronic applications, including computers, smartphones, consumer electronics, automotive electronics, and industrial equipment.
How can I choose a reliable supplier for Organic Substrate FC-BGA?
When selecting a supplier, consider factors such as their technical capabilities, manufacturing expertise, quality control measures, production capacity, and customer service reputation. Requesting samples and references can also help assess their suitability for your project.