Organic Packaging Chip Substrates Manufacturer
Organic Packaging Chip Substrates Manufacturer,Organic Packaging Chip Substrates utilize organic materials for semiconductor packaging, offering cost-effective solutions with flexibility and reliability. These substrates support mounting and interconnecting chips within electronic devices. Composed of organic insulators and conductors, they ensure dependable electrical connections and efficient heat dissipation. Organic Packaging Chip Substrates are vital for various industries, including consumer electronics and automotive, where cost efficiency and performance are crucial. Their flexibility enables miniaturization and space optimization, contributing to sleeker designs and improved functionality in modern electronic products. Organic Packaging Chip Substrates drive advancements in semiconductor packaging, providing versatile solutions for diverse applications.
Organic Packaging Chip Substrates, often termed as organic substrates or packaging materials, form an essential element in the intricate construction of semiconductor devices, particularly integrated circuits (ICs). These substrates act as the core for amalgamating and interconnecting a myriad of electronic components within the confines of a semiconductor package.
Highlighted features and traits linked with organic packaging chip substrates comprise:
Material Composition: Diverging from the traditional ceramic substrates, organic substrates incorporate organic materials. Epoxy resin, with a notable mention of fiberglass-reinforced epoxy (FR-4), takes precedence owing to its cost-effectiveness and commendable electrical properties.
Weight Optimization: Organic substrates excel in terms of weight when compared to their ceramic counterparts, contributing significantly to an overall reduction in the weight of the semiconductor package.
Economic Merit: The economic allure of organic substrates positions them as a preferred choice, especially in applications where stringent cost considerations come into play, such as the dynamic field of consumer electronics.
Dielectric Traits: Organic substrates exhibit an elevated dielectric constant relative to ceramic materials. This characteristic holds significance in influencing signal propagation, necessitating nuanced design adjustments, particularly in high-frequency applications.
Thermal Dynamics: While organic substrates may not match the thermal conductivity prowess of ceramics, ongoing advancements in material technology have enhanced their thermal performance. Nonetheless, for applications demanding heightened power or operation in high-temperature environments, ceramic substrates may retain their preferential standing.
Manufacturing Methodology: The manufacturing process of organic substrates closely mirrors that of printed circuit boards (PCBs). This involves strategically layering copper traces and vias onto the substrate material to establish essential electrical connections.
Organic packaging chip substrates find diverse applications across semiconductor packages, spanning Quad Flat Packages (QFPs), Plastic Dual In-Line Packages (PDIPs), and Ball Grid Arrays (BGAs). Their widespread adoption in consumer electronics and varied applications underscores their pivotal role within the ever-evolving landscape of the semiconductor industry.
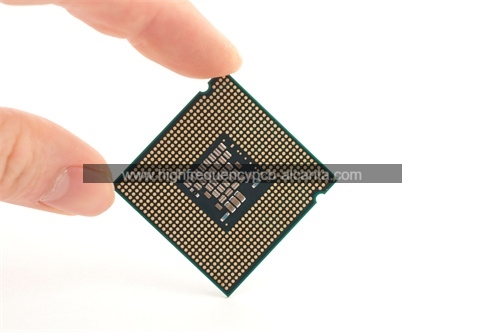
Organic Packaging Chip Substrates Manufacturer
What is the Function of Organic Packaging Chip Substrates?
Organic Packaging Chip Substrates emerge as indispensable contributors to the intricate domain of semiconductor devices, particularly within the nuanced landscape of integrated circuits (ICs). The versatile nature of these substrates encompasses a spectrum of functions, each wielding a pivotal role in orchestrating the seamless operation, reliability, and efficiency of electronic components. Let’s navigate through the diverse roles these substrates play:
Hub of Harmonization: Positioned as a central nexus, organic substrates facilitate the seamless integration of diverse electronic components within the confines of a semiconductor package. This integration forms the bedrock for the creation of cohesive and fully functional ICs.
Conductors of Connectivity: The substrate assumes the role of a conductor, intricately interweaving electrical connections among various components of the integrated circuit. The meticulous arrangement of copper traces and vias on the substrate crafts pathways for the unhindered transmission of electrical signals, fostering inter-component communication.
Sculptors of Signal Dynamics: Organic substrates exert influence over the dynamic interplay of signal propagation within the integrated circuit. The nuanced dielectric properties of the substrate shape the speed and efficiency of signal transmission, thereby dictating the overall performance of the semiconductor device.
Guardians of Thermal Equilibrium: While not rivalling the thermal conductivity prowess of alternatives like ceramics, organic substrates make significant contributions to thermal management. They play a role in dissipating heat generated during operation, mitigating the risk of overheating, and ensuring the sustained reliability of the integrated circuit.
Pillars of Structural Fortitude: Organic packaging chip substrates provide stalwart structural support for the intricate electronic components nestled upon them. This support acts as a shield, warding off potential physical damage and guaranteeing the enduring durability of the semiconductor device.
Advocates of Economic Efficiency: The adoption of organic substrates, featuring materials like epoxy resin or fiberglass-reinforced epoxy, champions economic efficiency in semiconductor manufacturing. This bears particular significance in applications where meticulous cost considerations take precedence, as witnessed in the dynamic landscape of consumer electronics.
In essence, the functions of organic packaging chip substrates encapsulate their role as the hub of harmonization, conductors of connectivity, sculptors of signal dynamics, guardians of thermal equilibrium, pillars of structural fortitude, and advocates of economic efficiency within the intricate mosaic of semiconductor devices.
What Are the Different Types of Organic Packaging Chip Substrates?
In the intricate landscape of semiconductor devices, a diverse array of organic packaging chip substrates takes the stage, each finely tuned for specific applications. These substrates unfold a tapestry of unique attributes, finding their roles in various electronic devices and industries. Here’s an exploration into the spectrum of prominent types:
Fiberglass-Reinforced Epoxy (FR-4): This stalwart among organic substrates garners praise for its cost-effectiveness and ease of fabrication. Woven fiberglass cloth infused with epoxy resin makes it a versatile choice, particularly prevalent in general-purpose and consumer electronics applications.
High-Temperature Epoxy: Engineered to navigate elevated thermal challenges, high-temperature epoxy substrates exhibit resilience in environments where efficient heat dissipation is paramount. Their role becomes pivotal in scenarios where endurance amidst varying temperatures is non-negotiable.
Polyimide (PI): Rising to prominence with outstanding thermal stability and chemical resistance, polyimide stands as a high-performance organic substrate. Its applications span industries demanding reliability amidst high-temperature conditions, notably in aerospace and automotive electronics.
Liquid Crystal Polymer (LCP): Distinguished by a low dielectric constant, minimal loss tangent, chemical resistance, and dimensional stability, LCP emerges as a thermoplastic organic substrate. Its footprint is discernible in high-frequency applications, where preserving signal integrity is paramount.
BT Epoxy (Bismaleimide Triazine): Bridging the realms of epoxy and polyimide, BT epoxy substrates embody a fusion of thermal stability and a low dielectric constant. Their significance amplifies in high-reliability spheres, notably within telecommunications and high-speed data communication.
Teflon (PTFE): Acclaimed for stellar electrical insulation and resilience against chemicals and high temperatures, Teflon-based substrates find resonance in high-frequency and microwave applications. Their low dielectric constant positions them favorably where safeguarding signal integrity takes precedence.
Liquid Epoxy: The adaptive nature of liquid epoxy substrates to cater to low thermal expansion requirements is notable. Tailoring them with specific additives allows for customization to meet thermal property prerequisites, rendering them apt for applications where thermal expansion matching is imperative.
In essence, the selection of an organic packaging chip substrate is a nuanced process, guided by the intricate demands of the application at hand. Electrical performance, thermal characteristics, cost considerations, and environmental resilience play pivotal roles in this selection journey. Each substrate type unveils a unique blend of properties, seamlessly aligning with the diverse requirements of electronic devices across industries.
What is the Relationship Between Organic Packaging Chip Substrates and IC Packaging?
In the intricate dance of semiconductor devices, the collaboration between organic packaging chip substrates and Integrated Circuit (IC) packaging takes center stage. This symbiotic relationship is not just a structural formality; it is the orchestrator of seamless integration, unwavering reliability, and optimal performance within integrated circuits. Let’s navigate the nuances of their interplay:
Architectural Canvas: Organic packaging chip substrates set the stage as the foundational canvas upon which the elements of an integrated circuit come together. This architectural base supports the strategic placement and interconnection of semiconductor devices, resistors, capacitors, and other vital components.
Electrical Nexus: The substrate assumes a central role in establishing an intricate electrical nexus within the integrated circuit. Its copper traces and vias weave a network, facilitating the fluid transmission of electrical signals and fostering a harmonious communication channel between different components.
Dielectric Maestro: Beyond being a mere platform, the organic substrate wields influence over signal propagation through its dielectric properties. Especially in the realm of high-frequency applications, where signal integrity is non-negotiable, the substrate’s material choice becomes a maestro orchestrating optimal performance.
Thermal Guardian: Acting as a guardian of thermal equilibrium, organic substrates actively contribute to managing the heat generated during the operation of the integrated circuit. This role is instrumental in preventing overheating, safeguarding the reliability and longevity of the entire IC.
Structural Guardian: Organic packaging chip substrates transcend their electrical duties to provide essential structural support for the delicate electronic components. This guardianship ensures resilience against physical damage, becoming a stalwart protector of the integrated circuit’s robustness.
Package Composer: The organic substrate isn’t a passive entity; it assumes a pivotal role in composing the overall structure of the IC package. It guides the choice of packaging formats, be it the sleek Quad Flat Packages (QFPs), traditional Plastic Dual In-Line Packages (PDIPs), or the advanced Ball Grid Arrays (BGAs), tailored to meet the specific demands of diverse applications.
Size and Weight Impactor: Material characteristics of organic substrates leave an imprint on the dimensions and weight of the IC package. Their lightweight nature, compared to alternatives like ceramics, positions them strategically in applications where minimizing package weight is a critical consideration, such as in the dynamic realm of consumer electronics.
In essence, the relationship between organic packaging chip substrates and IC packaging is a nuanced symphony, orchestrating not just structural harmony but influencing the very essence of electrical and thermal performance. The careful choreography of substrate material selection and packaging configuration becomes an art, ensuring that each application’s unique needs are met with precision and finesse.
How Do Organic Packaging Chip Substrates Differ from Regular PCBs?
Organic packaging chip substrates and conventional Printed Circuit Boards (PCBs) converge at their core as platforms for electronic components, yet their divergence becomes apparent when exploring material composition, design intricacies, and targeted applications. Let’s navigate the distinctions that set these two entities apart:
Material Composition:
Organic Packaging Chip Substrates: Tailored for semiconductor packaging, these substrates employ materials like fiberglass-reinforced epoxy (FR-4), high-temperature epoxy, polyimide, liquid crystal polymer (LCP), BT epoxy, or Teflon. These choices pivot on electrical properties, thermal efficiency, and seamless integration into semiconductor packaging processes.
Regular PCBs: Casting a broader material net, regular PCBs encompass options like aluminum, ceramic, or flexible alternatives such as polyimide. Material selection caters to the unique demands of the specific application.
Design Nuances:
Organic Packaging Chip Substrates: Meticulously tailored for the intricate demands of semiconductor devices, emphasizing precise component integration, intricate electrical pathways, and considerations for effective thermal management.
Regular PCBs: Exhibiting a more versatile design ethos, regular PCBs accommodate a myriad of electronic applications. They support various components such as resistors, capacitors, and integrated circuits without the specific focus on semiconductor packaging intricacies.
Applications:
Organic Packaging Chip Substrates: Primarily deployed in the assembly and packaging of integrated circuits and semiconductor devices, providing a steadfast foundation for mounting and interconnecting various components within a chip package.
Regular PCBs: Playing a broader role across diverse electronic applications, spanning computers, consumer electronics, automotive systems, and industrial machinery. They serve as the backbone for interconnecting and supporting a spectrum of electronic components on a single board.
Functional Emphasis:
Organic Packaging Chip Substrates: Centralized on delivering stability and reliability in the integration of semiconductor components. This involves meticulous attention to electrical connectivity, efficient thermal dissipation, and robust mechanical support.
Regular PCBs: Geared toward general-purpose electronic applications, with a primary focus on electrical connectivity. Thermal and mechanical considerations may not be as pronounced as those for chip substrates.
In essence, while organic packaging chip substrates and regular PCBs share a foundational purpose, their divergence becomes apparent in material choices, design intricacies, and targeted applications. Organic packaging chip substrates specialize in the sophisticated realm of semiconductor packaging, while regular PCBs showcase adaptability across a broader spectrum of electronic devices and industries.
What are the Main Structures and Production Technologies of Organic Packaging Chip Substrates?
Organic packaging chip substrates epitomize the harmonious fusion of intricate structures and advanced production methodologies, a cornerstone in meeting the multifaceted demands of semiconductor packaging. Let’s unravel the tapestry of key elements and manufacturing techniques that define the essence of these substrates:
Material Tapestry:
FR-4 (Fiberglass-Reinforced Epoxy): A stalwart choice, celebrated for its impeccable electrical insulation, mechanical fortitude, and economical appeal.
Polyimide: A virtuoso in high-temperature resilience, flexibility, and seamless integration with thin-film processes, carving a niche in advanced packaging realms.
Liquid Crystal Polymer (LCP): Distinguished by exceptional thermal stability, chemical resilience, and minimal moisture absorption, particularly influential in high-frequency and high-density arenas.
Architectural Choreography:
Core Ballet: Positioned at the substrate’s epicenter, orchestrating vital mechanical reinforcement and electrical insulation.
Copper Symphony: Delicate layers of copper foil pirouetting on the substrate’s surface, crafting intricate conductive pathways for the symphony of electrical signals.
Prepreg Ensemble: An ensemble of resin-impregnated fiberglass or reinforcing materials, waltzing to seamlessly bond the core layer and copper foil in a choreographed performance.
Precision Production Ballet:
Lamination Ballet: A central ballet involving the graceful melding of multiple substrate layers through the application of heat and pressure, culminating in a unified and robust structure.
Copper Cladding Waltz: The elegant dance of depositing thin copper foil layers onto the substrate surface, executed through refined methods like electroplating or a precise lamination duet.
Etching Sonata: A delicate sonata involving the removal of excess copper from the substrate surface using targeted chemical etchants, painting intricate conductive pathways and circuit patterns.
Drilling Pas de Deux: Executed by precision drilling machines, a balletic creation of holes or vias in the substrate, a fundamental step for seamless component mounting and interconnection.
Surface Treatment Rhapsody: The refined rhapsody of surface finishes, including solder masks, copper plating, or immersion tin, contributing not only to substrate protection but also orchestrating enhanced solderability.
Cutting-Edge Technological Symphony:
Embedded Harmonies: A revolutionary symphony seamlessly integrating passive components such as resistors and capacitors into the substrate structure, orchestrating a reduction in package size and elevating overall performance.
Through-Silicon Vias (TSVs) Crescendo: Paving the way for a crescendo of vertical interconnections between diverse substrate layers, TSV technology emerges as a pivotal player in achieving elevated packaging density and superior electrical functionality.
In essence, the structures and production technologies of organic packaging chip substrates are not mere mechanical compositions but a symphony of meticulous orchestration, continually evolving to strike the right chord with the escalating demands of contemporary semiconductor devices.
Frequently Asked Questions (FAQs)
What characterizes organic packaging chip substrates?
Organic packaging chip substrates emerge as specialized materials pivotal in the realm of semiconductor packaging. They serve as a resilient canvas for integrating diverse components within integrated circuits, providing vital attributes such as electrical insulation, thermal regulation, and robust mechanical support.
How does the production journey of organic packaging chip substrates unfold?
The manufacturing odyssey unfolds through a choreography of lamination, copper cladding, etching, drilling, and surface treatment. These synchronized steps yield layered structures, adorned with copper pathways, vias for component mounting, and a veneer of protective surface finishes.
Are there distinctive genres within the realm of organic packaging chip substrates?
Indeed, the landscape of organic substrates is diverse, shaped by the materials at play—examples include FR-4, polyimide, and LCP. Moreover, avant-garde variations introduce embedded passive components and through-silicon vias (TSVs) as avant-garde elements, elevating the functional symphony.
What distinguishes embedded passive components within organic packaging chip substrates?
The integration of passive components like resistors and capacitors directly into the substrate not only streamlines the ensemble but also orchestrates a reduction in package size, heightening electrical performance, and optimizing spatial dynamics within semiconductor devices.
How do organic packaging chip substrates deviate from the conventional landscape of PCBs?
Tailored explicitly for semiconductor packaging, organic packaging chip substrates venture into a realm where specific materials and design intricacies are meticulously crafted for the nuances of integrated circuits. In contrast, traditional PCBs embrace a more eclectic role, spanning a diverse spectrum of electronic devices.
Unveiling Through-Silicon Vias (TSVs) in the organic packaging chip substrate narrative:
TSVs emerge as the vertical choreographers between distinct substrate layers, ushering in not just heightened packaging density but also an orchestrated enhancement in electrical performance. They stand as instrumental conductors in the symphony of advanced semiconductor packaging.
Can organic packaging chip substrates master the art of serving high-frequency applications?
Indeed, substrates, particularly those woven from polyimide and LCP threads, display an inherent prowess for high-frequency applications, a testament to their stellar electrical properties and thermal resilience.
In what cadence do organic packaging chip substrates contribute to the contemporary dance of electronics miniaturization?
By incorporating materials like polyimide and intertwining with advanced technologies such as embedded passive components, organic packaging chip substrates choreograph the intricate dance of miniaturization, reducing the overall footprint of semiconductor devices.
Conclusion
In summary, organic packaging chip substrates stand as indispensable cornerstones in the intricate landscape of semiconductor packaging. Their pivotal role lies in establishing a robust foundation for seamlessly integrating components within integrated circuits. Through a meticulous interplay of material selection and sophisticated manufacturing processes, these substrates deliver essential functionalities such as electrical insulation, thermal regulation, and mechanical support.
The manufacturing journey of organic packaging chip substrates unfolds as a choreographed sequence, encompassing lamination, copper cladding, etching, drilling, and surface treatment. This orchestrated symphony yields layered structures, incorporating copper pathways, vias for component mounting, and protective surface finishes. This manufacturing finesse ensures that these substrates not only meet but exceed the stringent requirements of semiconductor devices.
The diverse palette of materials, including FR-4, polyimide, and LCP, allows for a tailored approach, addressing specific needs within varied applications. The integration of advanced features, such as embedded passive components and through-silicon vias (TSVs), elevates the functional prowess of these substrates to new heights.
Distinguishing organic packaging chip substrates from their traditional PCB counterparts reveals a specialized focus on semiconductor packaging. These substrates are meticulously engineered to cater to the intricate demands of integrated circuits, setting them apart from the more general-purpose nature of traditional PCBs.
Looking ahead, organic packaging chip substrates play a pivotal role in steering the trajectory of electronics towards miniaturization. Leveraging cutting-edge materials like polyimide and embracing advanced technologies, these substrates actively contribute to reducing the overall footprint of semiconductor devices. This aligns seamlessly with the evolving landscape, where compactness and high performance are paramount.
In essence, organic packaging chip substrates emerge as silent architects, providing unwavering support to the complex interplay of electronic components within semiconductor devices. Their evolution remains at the forefront of innovation, shaped by continual advancements in materials and manufacturing processes, ensuring they stand resilient in the dynamic realm of semiconductor packaging.