Organic Package Manufacturer
Organic Package Manufacturer,An Organic Package refers to semiconductor packaging utilizing organic materials like epoxy resin and fiberglass. These materials offer cost-effectiveness, mechanical flexibility, and improved thermal performance. Organic Packages provide platforms for mounting and interconnecting electronic components in devices like integrated circuits and microprocessors. They ensure reliable electrical connections and efficient heat dissipation, crucial for high-performance applications in consumer electronics, automotive, and telecommunications. This technology supports lightweight, compact designs, meeting the demand for portable and high-performance electronic devices. Organic Packages drive innovation in electronics manufacturing, balancing performance, cost, and reliability in various industries.
“Organic packaging substrates” pertain to packaging foundations primarily crafted from organic materials. In the sphere of electronic device production, these substrates assume a crucial role as the core structures, facilitating support and interconnection for electronic components while ensuring electrical insulation and protective measures.
Typically featuring organic polymers, with the prevalent use of glass fiber-reinforced epoxy resin (FR-4), these substrates are widely deployed in the fabrication of Printed Circuit Boards (PCBs). Renowned for their dependable insulation, robust mechanical resilience, and thermal resistance, FR-4 substrates find application across a spectrum of uses.
In contrast to their inorganic counterparts, relying on ceramics or metals as foundational materials, organic packaging substrates distinguish themselves through their cost-effectiveness and uncomplicated manufacturing processes. While inorganic substrates excel in demanding arenas such as high-performance and high-frequency environments due to superior thermal stability and electrical properties, organic substrates remain the preferred choice for numerous general applications.
In essence, organic packaging substrates represent a prevailing and economically viable option extensively integrated into the PCB manufacturing landscape for electronic devices.
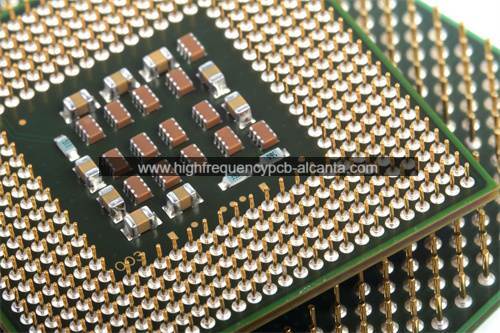
Organic Package Manufacturer
What Functions Does Organic Package Serve?
Organic packaging is a linchpin in ensuring the efficiency and resilience of electronic devices, especially in the realm of integrated circuits and printed circuit boards (PCBs). Let’s explore the manifold functions fulfilled by organic packaging:
Foundational Fortitude: Organic packages form a robust foundation, providing a secure anchor for electronic components like integrated circuits and semiconductor devices. This fortification guards against physical harm and external influences.
Conductive Path Networks: These packages facilitate interconnections among diverse electronic components through a network of conductive traces. These pathways enable seamless transmission of electrical signals across different segments of the circuit.
Heat Harmony: Organic packaging aids in adeptly managing heat generated during electronic component operation. By incorporating features like heat sinks and thermal vias, the design ensures efficient heat transfer and dissipation, thwarting overheating and preserving peak performance.
Electrical Insulation Assurance: Employing organic materials, such as glass fiber-reinforced epoxy resin (FR-4), organic packages provide vital electrical insulation. This insulation is pivotal in forestalling unintended electrical connections and preserving the circuit’s proper functionality.
Guardianship Against the Elements: Organic packages function as protective shields, shielding electronic components from external elements like moisture, dust, and contaminants. This protective role is paramount for upholding the reliability and longevity of electronic devices.
Signal Fidelity Adherence: Organic package design factors in elements affecting signal integrity, including impedance control, electromagnetic interference (EMI), and radiofrequency interference (RFI). This meticulous approach ensures precise signal propagation without degradation.
Optimized Dimensions: Organic packaging allows for the optimization of electronic device size and form factors. This aspect is particularly salient in the modern electronics landscape, where sleek and lightweight designs are often preferred.
Streamlined Manufacturing Efficiency: Organic packaging materials, exemplified by FR-4, offer cost-effectiveness and compatibility with standard PCB manufacturing processes. This contributes to the smooth and efficient mass production of electronic devices.
In essence, organic packaging in electronic devices serves as a versatile cornerstone, embracing roles such as foundational fortitude, conductive path facilitation, heat harmony, electrical insulation assurance, environmental guardianship, signal fidelity adherence, optimized dimensions, and streamlined manufacturing efficiency.
What Are the Different Types of Organic Package?
In the dynamic landscape of the electronics industry, a multitude of organic packaging types caters to specific functionalities and applications. Let’s navigate through some prominent varieties:
Dual In-Line Package (DIP): DIP, with its historical significance, presents two rows of pins for seamless insertion into PCB holes. Widely embraced for through-hole mounting of integrated circuits, it retains a timeless presence.
Quad Flat Package (QFP): Exhibiting a square or rectangular profile with a flat demeanor, QFP introduces leads extending from all four sides. This design lends itself favorably to surface mount technology (SMT), finding popularity in microcontrollers and assorted integrated circuits.
Surface Mount Device (SMD): SMD serves as an umbrella term encompassing diverse organic packages like Quad Flat Packs (QFP) and Small Outline Integrated Circuits (SOIC). Tailored for direct mounting onto PCB surfaces, SMD encapsulates versatile surface-mounted components.
Ball Grid Array (BGA): Noteworthy for solder balls on the lower surface establishing contact with the PCB, BGA packages emerge as go-to solutions for applications demanding an abundance of connections, exemplified by microprocessors and graphic processors.
Chip-on-Board (COB): Pioneering a direct mount of bare chips on the PCB, COB culminates in encapsulation with materials like epoxy. It carves a niche in applications such as LED modules and specialized sensors.
Chip-on-Flex (COF): A distinctive approach unfolds as bare chips grace a flexible substrate, offering a blend of flexibility and spatial efficiency. COF steps into the spotlight where spatial constraints dictate design.
Chip Scale Package (CSP): Redefining compactness, CSP mirrors the size of the bare die, minimizing excess packaging material. This sleek design finds its stride in devices yearning for miniaturization, like mobile phones and portable electronics.
Plastic Leaded Chip Carrier (PLCC): A rectangular or square silhouette, PLCC extends leads from all sides, making it a fixture in devices such as memory chips and programmable logic devices.
This array of organic packaging types barely scratches the surface. The journey through choosing a specific type unfolds, guided by the nature of the component, intended application, spatial constraints, and the intricacies of manufacturing processes.
How Does Organic Package Differ from IC Packaging?
In the realm of electronic components, the term “organic package” specifically delves into the meticulous selection of materials for crafting protective enclosures, particularly within the intricate landscape of printed circuit boards (PCBs). This expression places a focused lens on the deliberate utilization of organic materials such as epoxy resin or polymers, prized for their insulation qualities and cost-effectiveness.
Conversely, the term “IC packaging” extends its embrace to a broader panorama, encompassing the holistic process of safeguarding integrated circuits within protective casings. This all-encompassing term weaves through a diverse fabric of materials, intermingling organic elements like epoxy and plastic with inorganic counterparts such as ceramics and metals. The selection of materials here is an art, tailored to meet the nuanced needs and applications of the integrated circuit.
Here are the pivotal distinctions accentuated:
Scope and Emphasis:
Organic Package: Zeroes in on the materials shaping the packaging of electronic components, placing explicit emphasis on the use of organic materials.
IC Packaging: Widens the perspective, encapsulating the entire journey of enclosing integrated circuits, employing a diverse tapestry of materials.
Material Composition:
Organic Package: Specifically underscores the prevalence of packages predominantly composed of organic materials, esteemed for their insulation prowess and economical attributes.
IC Packaging: Embraces a broad spectrum of materials, seamlessly blending organic and inorganic options, harmonized based on the unique demands of the integrated circuit.
Application Context:
Organic Package: Tied to applications involving PCBs and the packaging of discrete electronic components such as resistors, capacitors, and transistors.
IC Packaging: Spreads its influence across a myriad of applications, from microprocessors to memory chips, employing a rich array of packaging techniques and materials strategically tailored to meet specific circuit requirements.
Techniques and Processes:
Organic Package: Often aligns with standard PCB manufacturing practices, where materials like FR-4 contribute to the substrate.
IC Packaging: Unfurls a diverse canvas of packaging techniques—Dual In-Line Packages (DIP), Quad Flat Packages (QFP), Ball Grid Arrays (BGA), Chip-on-Board (COB), among others—each intricately choreographed to cater to the distinctive needs of the integrated circuit.
In essence, while “organic package” hones in on the materials characterizing electronic component packaging, “IC packaging” unfolds a comprehensive narrative, weaving through a rich array of materials and techniques applied to safeguard integrated circuits across a spectrum of applications. Organic packages, within this narrative, emerge as a distinctive subset marked by their intentional use of organic materials.
How Does Organic Package Differ from Traditional PCBs?
In the realm of electronic components, “organic package” and “traditional PCBs” carve distinct niches, each providing a unique lens through which we perceive materials, functionality, and purpose.
Role and Purpose:
Organic Package: This term directs our attention to the shielding shell enveloping individual electronic components, with a focus on materials like epoxy resin or polymers. Its primary goal is to protect components, such as integrated circuits (ICs), from environmental factors and potential harm.
Traditional PCBs: In contrast, traditional Printed Circuit Boards (PCBs) serve as the cornerstone for mounting and interconnecting a diverse array of electronic components. They furnish essential electrical pathways and mechanical support, acting as the structural foundation of electronic devices.
Material Composition:
Organic Package: Crafted predominantly from organic materials like epoxy resin or polymers, chosen for their insulation properties and cost-effectiveness.
Traditional PCBs: Typically fashioned from materials like fiberglass-reinforced epoxy laminates (FR-4), providing a robust substrate supporting the mounting of electronic components while ensuring electrical insulation between layers.
Functionality:
Organic Package: Primarily concentrates on encapsulating and safeguarding individual electronic components, ensuring their resilience against external elements.
Traditional PCBs: Serve as the fundamental platform for mounting and interconnecting a diverse range of electronic components, enabling essential electrical connections for the seamless flow of signals and power within electronic systems.
Components Involved:
Organic Package: Encompasses the packaging of discrete electronic components, including integrated circuits (ICs), transistors, and resistors.
Traditional PCBs: Envelop the mounting and interconnection of various electronic components, spanning ICs, resistors, capacitors, and connectors, playing a pivotal role in the intricate landscape of electronic circuitry.
In essence, “organic package” directs our gaze to the protective housing of individual components, with a specific emphasis on organic materials, while “traditional PCBs” unfold a broader narrative, serving as the foundational structure for a diverse spectrum of electronic elements. The organic package emerges as a specialized component within the encompassing story of traditional PCBs.
What Constitutes the Core Structure and Production Technologies of Organic Package?
The nucleus of an organic package lies in its structural essence and the intricate methodologies employed in its creation. These encompass a diverse array of vital components shaping its design, manufacturing processes, and operational prowess. Let’s navigate through these pivotal facets:
Inherent Structure:
Substrate Material: At its very core, the organic package is crafted from organic materials, commonly epoxy resin or polymers. This substrate forms the foundational canvas for mounting and orchestrating connections among electronic components.
Stratified Configuration: The substrate adopts a stratified configuration, intricately weaving copper traces for indispensable electrical connections. This layered design is meticulously tailored to meet the specific idiosyncrasies of electronic components and their nuanced interrelationships.
Dielectric Layers: Infused dielectric layers act as guardians, insulating conductive traces, minimizing the risk of short circuits, and ensuring the overall reliability of the package.
Manufacturing Artistry:
Substrate Fabrication: The artistry of crafting the organic substrate involves a diverse palette of techniques, ranging from lamination to printing. Lamination involves the harmonious bonding of material layers, while printing methods such as screen printing or inkjet printing offer a symphony of control over material deposition.
Copper Trace Patterning: Copper traces are delicately patterned on the substrate through processes like photolithography. This intricate dance involves the use of a light-sensitive material to transfer the desired copper choreography onto the substrate.
Via Elegance: Vias, the graceful connectors facilitating electrical communion across substrate layers, are established through techniques like laser drilling or mechanical drilling, followed by a copper-plated waltz.
Surface Finish Flourish: Exposed copper surfaces don a flourish of surface finishes, shielding against the elements, enhancing solderability during component assembly. The repertoire includes tin-lead, gold, or lead-free alternatives.
Solder Mask Symphony: Strategically orchestrated solder masks cover areas where soldering is unnecessary, ensuring a precise soldering ballet during component assembly. This not only provides insulation but also acts as a protective guard for the electronic ensemble.
Component Attachment Pas de Deux: Electronic components, akin to performers in a pas de deux, are affixed to the substrate using advanced techniques like surface mount technology (SMT) or through-hole technology (THT).
Encapsulation Sonata: To shield components from the environmental crescendo, mechanical stresses, and potential damage, the entire package performs a sonata of encapsulation using a protective material like epoxy molding compound (EMC).
Testing and Quality Overture: Rigorous testing protocols form the overture, ensuring the harmony and reliability of the organic package. This includes comprehensive electrical testing, thermal assessments, and meticulous visual inspections.
By fusing these elemental strokes and employing advanced production techniques, the organic package is not merely crafted; it orchestrates a symphony, meeting the nuanced demands of electronic components and providing a secure, reliable environment for their optimal performance.
Frequently Asked Questions (FAQs)
Which materials are frequently employed in the construction of organic packages?
Common materials for organic packages include epoxy resin and various polymers. These materials provide insulation, mechanical support, and protection for electronic components.
Can you provide an overview of the manufacturing process for organic packages?
The manufacturing process typically encompasses substrate fabrication, copper trace patterning, via establishment, surface finish application, solder mask implementation, component attachment, encapsulation, and thorough testing. These steps are crucial to ensure high-quality and reliable organic packages.
Is customization possible for organic packages based on specific applications?
Yes, organic packages can be customized to meet the unique requirements of different electronic components and applications. Manufacturers often collaborate closely with clients to adapt designs and features according to specific project needs.
What testing procedures are implemented by organic package manufacturers?
Testing procedures typically include electrical testing, thermal assessments, and meticulous visual inspections. These tests are essential to ensure the functionality, reliability, and durability of organic packages.
How environmentally sustainable are organic packages?
Organic packages, crafted from materials like epoxy resin and polymers, are generally considered more environmentally friendly compared to certain alternatives. However, a comprehensive assessment of the entire lifecycle of materials and the manufacturing process is essential.
Conclusion
In summary, the domain of organic package manufacturing entails a meticulous orchestration of materials, design nuances, and production processes to craft protective enclosures for electronic components. Organic packages, hewn from materials like epoxy resin and polymers, assume a pivotal role in shielding delicate components from environmental stressors and mechanical strains.
Manufacturers in this specialized field master a comprehensive production process, encompassing substrate fabrication, copper trace patterning, via establishment, surface finish application, solder mask implementation, component attachment, encapsulation, and rigorous testing. These meticulous steps stand as linchpins, ensuring the end product’s high quality, reliability, and enduring durability.
The selection of an organic package manufacturer demands astute consideration of factors such as experience, material proficiency, adherence to industry benchmarks, production capabilities, and the adeptness to tailor packages to precise client specifications. The symbiotic collaboration between manufacturers and clients becomes paramount, tailoring designs and features to cater to the distinctive requisites of diverse electronic components and applications.
While organic packages are purpose-built to safeguard individual electronic components, they diverge from traditional Printed Circuit Boards (PCBs), which serve as foundational hubs for mounting and interconnecting an array of components. The potential environmental sustainability of organic packages, rooted in their materials and manufacturing processes, positions them as potentially more eco-conscious alternatives.
Entrenched in industries spanning consumer electronics, telecommunications, automotive, and medical devices, organic packages emerge as catalysts, elevating the performance and fortification of electronic components. As technology propels forward and the clamor for compact, reliable electronic systems amplifies, the role of organic package manufacturers ascends in significance, safeguarding the integrity and functionality of electronic devices.