Open Multi-Cavity PCB Manufacturer
Open Multi-Cavity PCB Manufacturer,Open multi-Cavity PCBs represent a cutting-edge innovation in printed circuit board technology, featuring multiple integrated cavities or cutouts within the substrate. These cavities serve as dedicated compartments for housing components or subsystems, offering a host of benefits across various industries. By strategically isolating components, Open multi-Cavity PCBs enhance thermal management, mitigating the risk of heat-induced performance degradation. Moreover, they bolster electromagnetic interference (EMI) shielding, safeguarding sensitive electronics from external disturbances. Their three-dimensional layout optimization facilitates compact designs, ideal for space-constrained applications like aerospace, automotive, and portable electronics. Additionally, the physical protection provided by the cavities enhances system reliability, ensuring robust performance even in challenging environments. Open multi-Cavity PCBs underscore a paradigm shift in PCB design, empowering engineers to realize increasingly complex and compact electronic systems while maintaining superior performance and reliability.
What is an Open multi-Cavity PCB?
An Open multi-Cavity PCB refers to a printed circuit board (PCB) design that incorporates multiple cavities or cutouts within the board itself. These cavities are typically empty spaces or voids within the PCB substrate. This design allows for the integration of various components or subsystems into separate compartments within the same PCB, offering several advantages.
Firstly, an Open multi-Cavity PCB can help with thermal management by isolating heat-generating components into separate cavities, reducing the risk of thermal interference and improving overall heat dissipation efficiency. Additionally, it can aid in electromagnetic interference (EMI) shielding by physically separating sensitive components or signals from sources of electromagnetic noise.
Moreover, this design facilitates miniaturization and optimization of circuit layout by enabling tighter integration of components in a three-dimensional space, which can be particularly advantageous in compact electronic devices where space is limited.
Furthermore, Open multi-Cavity PCBs can enhance system reliability and ruggedness by providing physical protection for sensitive components against environmental factors such as moisture, dust, and mechanical stress.
Overall, the use of Open multi-Cavity PCBs offers designers greater flexibility in designing complex electronic systems, enabling improved performance, reliability, and miniaturization.
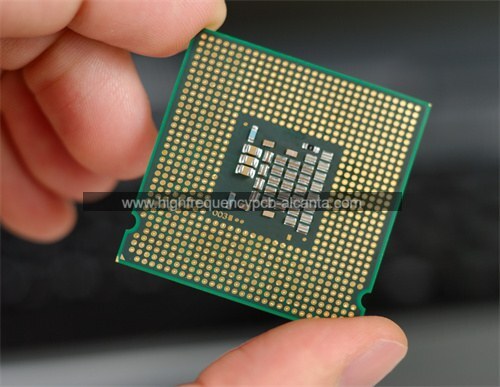
Open Multi-Cavity PCB Manufacturer
What are the PCB Design Guidelines?
PCB design guidelines encompass a set of best practices and recommendations to follow during the design process to ensure the functionality, reliability, and manufacturability of printed circuit boards. Here are some key guidelines:
- Component Placement: Arrange components strategically to minimize signal interference, optimize signal paths, and facilitate efficient routing. Group related components together to reduce trace length and minimize signal degradation.
- Routing Considerations: Follow principles of signal integrity and impedance matching when routing high-speed signals. Maintain appropriate trace widths, separation, and layer stack-up to minimize signal degradation, crosstalk, and EMI.
- Power Integrity:Design power distribution networks (PDNs) to minimize voltage drops, noise, and ground loops. Use adequate power and ground planes with low impedance paths.
- Thermal Management: Ensure effective heat dissipation by placing heat-generating components strategically, providing thermal vias, and incorporating thermal relief patterns in copper pours.
- Mechanical Considerations: Design PCBs with appropriate mechanical strength and stiffness to withstand environmental stressors and mechanical loads. Consider factors such as board thickness, mounting holes, and component clearances.
- Design for Manufacturability (DFM): Design PCBs with manufacturability in mind to minimize production issues and costs. Follow PCB manufacturer’s guidelines regarding minimum trace widths, minimum annular ring sizes, and minimum via sizes.
- Silkscreen and Documentation: Clearly label components, connectors, and test points on the silkscreen layer for ease of assembly and troubleshooting. Include detailed documentation such as assembly drawings, bill of materials (BOM), and fabrication notes.
- Testing and Prototyping: Design PCBs with testability in mind, incorporating test points and access points for debugging and validation. Prototype and test PCB designs thoroughly to identify and address any issues early in the development cycle.
- Environmental Considerations: Design PCBs to withstand the intended operating environment, considering factors such as temperature, humidity, vibration, and shock.
- Compliance and Standards: Ensure PCB designs comply with relevant industry standards and regulations such as RoHS (Restriction of Hazardous Substances) and EMC (Electromagnetic Compatibility) directives.
Following these guidelines can help ensure the successful design, manufacturing, and deployment of high-quality printed circuit boards for various electronic applications.
What is the PCB Fabrication Process?
The PCB fabrication process involves several steps to transform a design layout into a physical printed circuit board. Here’s an overview of the typical PCB fabrication process:
- Design Input: The process begins with the input of the PCB design files, typically in Gerber format, along with any fabrication notes, specifications, and requirements.
- Substrate Preparation: A substrate material, usually fiberglass-reinforced epoxy resin known as FR-4, is prepared in large sheets. The substrate is cleaned and coated with a thin layer of copper on both sides, forming the base copper layer for the PCB.
- Photoresist Application: A layer of photoresist material is applied to the surface of the copper-clad substrate. The photoresist is sensitive to UV light and will harden upon exposure.
- Exposure and Imaging: The PCB design is transferred onto the photoresist layer using a process called photolithography. A UV light source is used to expose the photoresist through a photomask containing the PCB pattern. The areas exposed to UV light become hardened, while the unexposed areas remain soluble.
- Development: The exposed PCB pattern is developed by washing away the unexposed photoresist using a developing solution, leaving behind the desired copper traces and pads on the substrate.
- Etching: The exposed copper areas not protected by the hardened photoresist are etched away using an etchant solution, typically an acidic or alkaline solution. This process removes excess copper, leaving only the copper traces and pads defined by the PCB design.
- Photoresist Stripping: The remaining photoresist is stripped away using a solvent, leaving the bare copper traces and pads on the substrate.
- Drilling: Holes are drilled into the PCB substrate at specified locations for through-hole components and vias. Automated drilling machines are used to precisely drill these holes.
- Through-Hole Plating (Optional): If the design requires plated through-holes, a thin layer of copper is electroplated onto the hole walls to provide electrical continuity between layers.
- Surface Finish: A surface finish is applied to protect the exposed copper surfaces from oxidation and facilitate soldering. Common surface finishes include HASL (Hot Air Solder Leveling), ENIG (Electroless Nickel Immersion Gold), and OSP (Organic Solderability Preservative).
- Final Inspection: The fabricated PCB undergoes final inspection to ensure that it meets the required specifications and quality standards. This may include visual inspection, dimensional measurements, electrical testing, and other quality checks.
- Routing and Profiling: The individual PCBs are routed out from the larger panel using CNC (Computer Numerical Control) machines, and the edges are profiled to the final dimensions.
- Cleaning: The finished PCBs are cleaned to remove any residues from the fabrication process, ensuring the cleanliness of the board’s surface.
Once the fabrication process is complete, the printed circuit boards are ready for assembly, where components are mounted onto the board and soldered in place to create functional electronic devices.
How do you manufacture an Open multi-Cavity PCB?
Manufacturing an Open multi-Cavity PCB involves additional steps compared to standard PCB manufacturing processes due to the inclusion of multiple cavities within the board. Here’s an overview of the manufacturing process for an Open multi-Cavity PCB:
- Design Phase: Develop the PCB design layout, incorporating the required cavities or cutouts within the board. Consider factors such as component placement, cavity dimensions, and overall board size.
- Material Selection: Choose a suitable substrate material that can accommodate the desired number of cavities while maintaining structural integrity and electrical performance. FR-4 is a common choice for multi-Cavity PCBs due to its versatility and cost-effectiveness.
- Substrate Preparation: Prepare the substrate material by cutting it into the desired size and shape. The substrate may be pre-coated with a layer of copper on both sides, or the copper layers can be applied later in the process.
- Cavity Formation: Use specialized CNC milling or routing machines to create the cavities within the substrate material. The cavities should be precisely machined to the specified dimensions and located according to the PCB design layout.
- Copper Cladding: If the substrate does not already have copper layers, apply a thin layer of copper to both sides of the substrate using methods such as electroplating or lamination. Ensure that the copper adheres uniformly to the substrate surface, including the walls of the cavities.
- PCB Imaging and Etching: Apply a photoresist layer to the copper-clad substrate and transfer the PCB design onto the photoresist using photolithography techniques. After development, etch away the excess copper from the exposed areas, leaving behind the copper traces and pads on the substrate surface and within the cavities.
- Drilling and Plating: Drill holes for through-hole components and vias, taking into account the presence of cavities. Optionally, plate the drilled holes to provide electrical continuity between layers, ensuring that the plating process penetrates into the cavities.
- Surface Finish: Apply a suitable surface finish to protect the exposed copper surfaces and facilitate soldering. Choose a surface finish that can penetrate into the cavities and provide adequate coverage.
- Final Inspection and Testing: Conduct thorough inspection and testing of the manufactured PCBs to ensure that the cavities are accurately machined, and the electrical performance meets the required specifications. Inspect for any defects or irregularities in the cavity walls or copper traces.
- Assembly and Integration: Once the Open multi-Cavity PCBs pass inspection, proceed with component assembly and integration according to the design requirements. Mount components onto the PCB surface and within the cavities, solder them in place, and conduct functional testing to verify proper operation.
By following these steps, manufacturers can produce high-quality Open multi-Cavity PCBs suitable for a wide range of applications, including electronic devices that require compact and integrated designs.
How much should an Open multi-Cavity PCB cost?
The cost of an Open multi-Cavity PCB can vary significantly depending on several factors, including the complexity of the design, the number of cavities, the size of the board, the materials used, the manufacturing processes involved, and the quantity ordered. Here are some key factors that can influence the cost:
- Design Complexity: Complex designs with intricate cavity shapes, tight tolerances, and high-density component layouts will generally incur higher manufacturing costs due to the increased complexity of fabrication and assembly.
- Number of Cavities: The number of cavities within the PCB directly impacts the manufacturing cost, as each additional cavity requires additional machining, material, and processing time.
- Board Size: Larger PCBs typically cost more to manufacture than smaller ones due to the increased material usage, longer processing times, and higher shipping costs.
- Materials: The choice of substrate material, copper thickness, and surface finish can affect the cost. Higher-quality materials or specialized substrates may come at a premium price.
- Manufacturing Processes: Specialized manufacturing processes such as CNC milling for cavity formation, electroplating for through-hole plating, and selective surface finishes can add to the overall cost.
- Quantity: Economies of scale apply in PCB manufacturing, meaning that larger production quantities often result in lower per-unit costs due to efficiency gains in setup and production.
- Lead Time: Expedited production or shorter lead times may incur additional costs, as manufacturers may need to prioritize orders or adjust their production schedules to meet tight deadlines.
To get an accurate cost estimate for an Open multi-Cavity PCB, it’s recommended to consult with PCB manufacturers or suppliers directly. They can provide quotes based on the specific requirements of the design, including factors such as materials, dimensions, quantities, and any additional services or customization needed. Additionally, online PCB cost calculators or quotation tools offered by PCB manufacturers can help provide initial estimates based on basic parameters.
What is Open multi-Cavity PCB base material?
The base material for an Open multi-Cavity PCB is typically chosen based on the specific requirements of the design, considering factors such as mechanical strength, thermal performance, electrical properties, and cost. Here are some common base materials used for Open multi-Cavity PCBs:
- FR-4 (Flame Retardant-4): FR-4 is the most widely used substrate material for PCBs due to its excellent overall performance, cost-effectiveness, and availability. It consists of layers of woven fiberglass impregnated with an epoxy resin binder. FR-4 is known for its good mechanical strength, electrical insulation properties, and thermal stability.
- High-Temperature FR-4: For applications requiring higher operating temperatures, high-temperature FR-4 variants are available with enhanced thermal resistance. These materials can withstand elevated temperatures without significant degradation, making them suitable for demanding environments.
- Rogers and Teflon-Based Materials: Rogers and Teflon-based materials offer superior electrical performance, low dielectric constant, and low loss tangent compared to standard FR-4. These materials are often chosen for high-frequency and microwave applications where signal integrity is critical.
- Metal Core PCBs (MCPCB): Metal core PCBs feature a metal substrate layer, typically aluminum or copper, sandwiched between layers of dielectric material. MCPCBs offer excellent thermal conductivity and heat dissipation properties, making them suitable for applications requiring efficient thermal management, such as LED lighting and power electronics.
- Ceramic-Based Materials: Ceramic substrates such as aluminum oxide (Al2O3) or aluminum nitride (AlN) offer high thermal conductivity, excellent dimensional stability, and low coefficient of thermal expansion (CTE). These materials are often chosen for high-power applications and electronic systems operating in harsh environments.
- Flex and Rigid-Flex Materials: For applications requiring flexibility or three-dimensional form factors, flexible and rigid-flex PCB materials are used. These materials feature flexible polyimide or polyester substrates that can bend or conform to complex shapes while maintaining electrical connectivity.
The choice of base material for an Open multi-Cavity PCB depends on the specific requirements of the application, including thermal management needs, signal integrity considerations, mechanical constraints, and budget constraints. Designers should carefully evaluate the properties of different materials and select the most suitable option to meet the performance and reliability requirements of the PCB design.
Which company makes Open multi-Cavity PCB?
Currently, many companies can produce Open multi-Cavity PCBs. Some well-known companies include: Advanced Circuits, APCT, Rigiflex Technology, Multek, Epec Engineered Technologies, Sanmina, JingHongYi PCB, and PCBWay, among others. These companies have rich experience and technical strength in the PCB manufacturing field and can meet the various needs of complex PCB designs.
As for our company, we can also manufacture Open multi-Cavity PCBs. As a professional PCB manufacturer, we have advanced equipment and a skilled technical team capable of meeting the requirements for complex PCBs. Our manufacturing process includes:
- Design Support: Our engineering team can provide PCB design support to help customers optimize their designs to meet the requirements of Open multi-Cavity PCBs. We use advanced CAD/CAM software and simulation tools to ensure the accuracy and reliability of the design.
- Material Selection:We offer a variety of PCB materials, including conventional FR-4 materials, high-frequency materials, metal substrates, etc., to meet customers’ requirements for performance and cost.
- Precision Machining:We have advanced CNC drilling and milling equipment to achieve precise hole and cavity machining, ensuring the accuracy and quality of Open multi-Cavity PCBs.
- Multilayer Stacking: We can manufacture multi-layer Open multi-Cavity PCBs to meet customers’ requirements for complex circuit layouts and signal integrity.
- Surface Treatment: We provide various types of surface treatment, including HASL, ENIG, OSP, etc., to protect the PCB surface and improve solderability.
- Quality Control: We strictly follow the ISO 9001 quality management system and perform multiple quality controls throughout the manufacturing process to ensure the stable and reliable quality of each Open multi-Cavity PCB.
No matter what customers’ needs are, we can provide customized solutions and ensure the delivery of high-quality Open multi-Cavity PCBs within budget and time constraints. Our goal is to establish long-term cooperative relationships with customers and jointly promote the successful implementation of projects.
What are the 7 qualities of good customer service?
Good customer service is characterized by several key qualities that contribute to positive customer experiences and satisfaction. Here are seven qualities of good customer service:
- Responsiveness:Good customer service involves promptly addressing customer inquiries, concerns, and requests. Responsiveness demonstrates attentiveness to customers’ needs and a commitment to providing timely assistance.
- Empathy: Empathy is the ability to understand and share the feelings of customers. Good customer service representatives empathize with customers’ situations, concerns, and frustrations, which helps to build rapport and trust.
- Clear Communication: Effective communication is essential in customer service interactions. Good customer service involves communicating clearly and concisely, using language that is easy to understand, and providing accurate information to address customers’ questions and issues.
- Problem-Solving Skills: Good customer service representatives possess strong problem-solving skills to effectively resolve customers’ issues and complaints. They listen actively, analyze problems, and offer appropriate solutions or alternatives to ensure customer satisfaction.
- Professionalism: Professionalism is crucial in customer service interactions. Good customer service representatives maintain a positive and courteous demeanor, remain calm under pressure, and treat customers with respect and courtesy at all times.
- Product Knowledge: Good customer service requires a deep understanding of the products or services being offered. Customer service representatives should be knowledgeable about the features, benefits, and usage of the products or services to provide accurate information and assistance to customers.
- Follow-Up and Feedback: Following up with customers after resolving their issues or inquiries demonstrates a commitment to customer satisfaction. Good customer service involves seeking feedback from customers to understand their experiences, identify areas for improvement, and continuously enhance the quality of service provided.
By embodying these qualities, organizations can cultivate a customer-centric culture and build long-lasting relationships with their customers.
FAQs
What is an Open multi-Cavity PCB?
An Open multi-Cavity PCB refers to a printed circuit board (PCB) design that incorporates multiple cavities or cutouts within the board itself. These cavities are empty spaces or voids within the PCB substrate, allowing for the integration of various components or subsystems into separate compartments within the same PCB.
What are the benefits of using Open multi-Cavity PCBs?
Open multi-Cavity PCBs offer several advantages, including improved thermal management by isolating heat-generating components, enhanced electromagnetic interference (EMI) shielding, optimization of circuit layout for miniaturization, and enhanced system reliability and ruggedness by providing physical protection for sensitive components.
What applications are Open multi-Cavity PCBs suitable for?
Open multi-Cavity PCBs are suitable for a wide range of applications, including aerospace, automotive, telecommunications, medical devices, consumer electronics, and industrial equipment. They are particularly beneficial for electronic devices where space is limited, and thermal management and electromagnetic compatibility are critical.
What considerations should be taken into account when designing Open multi-Cavity PCBs?
When designing Open multi-Cavity PCBs, factors such as component placement, cavity dimensions, thermal management, signal integrity, mechanical stability, and manufacturing feasibility should be carefully considered to ensure optimal performance and reliability.
Can any PCB manufacturer produce Open multi-Cavity PCBs?
While many PCB manufacturers can produce Open multi-Cavity PCBs, it’s essential to choose a manufacturer with experience and expertise in manufacturing complex PCB designs. Manufacturers with advanced equipment, skilled personnel, and a track record of producing high-quality PCBs are better suited for producing Open multi-Cavity PCBs.
What are the cost implications of manufacturing Open multi-Cavity PCBs?
The cost of manufacturing Open multi-Cavity PCBs can vary depending on factors such as design complexity, number of cavities, board size, materials used, manufacturing processes involved, and quantity ordered. Generally, the more complex the design and the higher the quantity, the higher the manufacturing cost.
How can I ensure the quality of Open multi-Cavity PCBs?
To ensure the quality of Open multi-Cavity PCBs, it’s essential to work with a reputable PCB manufacturer that follows industry best practices, quality standards, and rigorous quality control processes throughout the manufacturing process. Additionally, thorough testing and inspection should be conducted to verify the performance and reliability of the PCBs before deployment.