Omega Materials PCB Manufacturer
Omega Materials PCB Manufacturer,Omega Materials PCBs refer to a category of high-performance printed circuit board materials optimized for demanding applications. These materials typically feature advanced properties such as high thermal conductivity, excellent electrical insulation, and low dielectric loss. Omega Materials PCBs are crucial in industries requiring high reliability and performance under extreme conditions, including aerospace, automotive, and telecommunications. They are designed to facilitate efficient heat dissipation, minimize signal loss, and ensure stable operation of electronic components. Omega Materials PCBs are chosen for their ability to meet stringent quality standards and support the development of cutting-edge technologies in fields where reliability and durability are paramount.
What is an Omega Materials PCB?
An Omega Materials PCB (Printed Circuit Board) refers to a specialized type of PCB that incorporates Omega Materials, which are advanced materials known for their exceptional properties like high thermal conductivity, excellent electrical insulation, and sometimes unique magnetic properties. These materials are crucial in applications where standard PCB materials like FR4 (a type of glass-reinforced epoxy laminate) might not meet specific performance requirements.
Omega Materials PCBs are typically used in industries such as aerospace, automotive, telecommunications, and electronics manufacturing, where reliability, performance under extreme conditions (like high temperatures or high frequencies), and durability are paramount. These PCBs are designed to handle higher power densities, provide better thermal management, and ensure stable electrical performance over time.
The choice of Omega Materials (such as certain ceramics, metals, or composites) depends on the exact needs of the application. For instance, some Omega Materials PCBs might use materials like aluminum nitride (AlN) or silicon carbide (SiC) for their excellent thermal conductivity, which helps dissipate heat efficiently from high-power components. Others might use magnetic materials like ferrites for applications requiring electromagnetic interference (EMI) shielding or inductive components.
In essence, Omega Materials PCBs represent a specialized solution tailored to demanding technological requirements, offering enhanced performance characteristics compared to conventional PCBs made from standard materials like FR4. Their use enables engineers to achieve higher efficiency, reliability, and longevity in electronic and electrical systems where performance cannot be compromised.
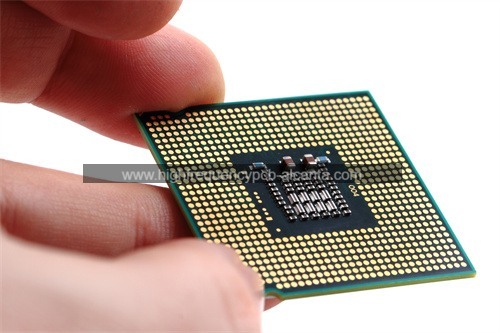
Omega Materials PCB Manufacturer
What are the Omega Materials PCB Design Guidelines?
Omega Materials PCB design guidelines focus on optimizing the performance and reliability of printed circuit boards that incorporate advanced materials such as ceramics, metals, or composites. These guidelines typically include:
- Material Selection: Choose Omega Materials (e.g., ceramics like aluminum nitride or silicon carbide) based on the specific application requirements such as thermal conductivity, dielectric properties, mechanical strength, and compatibility with manufacturing processes.
- Thermal Management: Design the PCB layout to maximize heat dissipation from high-power components. This may involve placing heat sinks, vias for thermal conduction, and ensuring adequate airflow around critical components.
- Electrical Performance: Ensure signal integrity and minimize electromagnetic interference (EMI) by carefully planning signal routing, ground planes, and shielding techniques suitable for the specific Omega Material used.
- Mechanical Considerations: Omega Materials may have different mechanical properties compared to standard PCB materials. Design the PCB to withstand mechanical stresses, vibrations, and thermal expansion coefficients that can affect reliability over the PCB’s lifecycle.
- Manufacturability: Understand the manufacturing processes compatible with Omega Materials, such as specific soldering techniques (e.g., reflow soldering for certain ceramics) and handling procedures to avoid material damage or contamination.
- Testing and Validation: Establish rigorous testing protocols to verify the PCB’s performance under expected operating conditions, including thermal cycling, electrical testing for signal integrity, and reliability testing to ensure long-term durability.
- Documentation and Standards Compliance: Document the design choices, material specifications, and compliance with industry standards (e.g., IPC standards for PCB design and manufacturing) to facilitate quality assurance and future maintenance.
- Collaboration with Suppliers: Work closely with suppliers of Omega Materials to ensure alignment between design requirements and material capabilities, including obtaining technical support and material data necessary for design validation.
By adhering to these Omega Materials PCB design guidelines, engineers can optimize the performance, reliability, and manufacturability of PCBs tailored for high-performance applications in industries such as aerospace, automotive, telecommunications, and power electronics.
What is the Omega Materials PCB Fabrication Process?
The fabrication process for Omega Materials PCBs involves several specialized steps to accommodate the unique properties of Omega Materials such as ceramics, metals, or composites. Here’s an overview of the typical fabrication process:
- Material Selection: Choose the appropriate Omega Material based on the specific application requirements, such as thermal conductivity, dielectric properties, mechanical strength, and compatibility with the manufacturing processes.
- Design Preparation: Develop a PCB design that considers the unique characteristics of Omega Materials. This includes layout design, component placement, routing considerations for thermal management and signal integrity, and adherence to manufacturability guidelines.
- Substrate Preparation: Prepare the substrate using the selected OmegaMaterial. This may involve cutting, polishing, and cleaning the material to ensure a smooth surface and proper dimensions for subsequent processing.
- Layer Preparation: Depending on the complexity of the PCB, prepare multiple layers of Omega Material substrates. This could involve stacking layers to form a multi-layer PCB structure, ensuring alignment and bonding between layers.
- Circuit Patterning: Apply the circuit pattern onto the Omega Material substrate using techniques suitable for the specific material. This typically involves photolithography or direct laser writing for precision patterning of conductive traces and vias.
- Metallization: Deposit metal layers (such as copper) onto the substrate to form the conductive pathways and vias required for electrical connections between layers and components. Techniques like sputtering or electroplating are commonly used for metallization.
- Etching: Use chemical etching processes to remove excess metal and define the final conductive traces and features according to the PCB design. This step ensures accurate alignment and connectivity between layers.
- Lamination: If producing a multi-layer PCB, laminate the individual layers together using heat and pressure to form a single integrated structure. This step ensures strong adhesion between layers and creates the necessary electrical connections through drilled vias.
- Surface Finishing: Apply surface finishes such as solder mask and protective coatings to the PCB to protect the conductive traces, facilitate soldering of components, and provide insulation where necessary.
- Quality Assurance: Conduct rigorous testing and inspection throughout the fabrication process to verify dimensional accuracy, electrical continuity, and adherence to design specifications. Testing may include electrical testing, thermal cycling, and mechanical stress testing to ensure reliability.
- Assembly: Once fabricated, assemble the Omega Materials PCB with electronic components using standard assembly techniques. This may involve surface mount technology (SMT) or through-hole components depending on the design and application requirements.
- Final Testing: Perform final electrical testing and functional testing of the assembled PCB to ensure proper functionality and reliability under operating conditions.
By following these steps tailored to Omega Materials, manufacturers can produce PCBs that meet stringent performance requirements for applications in high-power electronics, telecommunications, aerospace, and other advanced industries. Each step is crucial in ensuring the PCB’s performance, reliability, and longevity in demanding environments.
How do you manufacture an Omega Materials PCB?
Manufacturing an Omega Materials PCB involves a specialized process tailored to the unique properties of advanced materials such as ceramics, metals, or composites. Here’s a detailed outline of the typical manufacturing process:
- Material Selection: Choose the appropriate Omega Material based on application requirements like thermal conductivity, dielectric properties, and mechanical strength. Common materials include aluminum nitride (AlN) for high thermal conductivity or silicon carbide (SiC) for high-temperature applications.
- Design and Layout: Prepare the PCB design considering the specific characteristics of Omega Materials. Design considerations include thermal management, signal integrity, and mechanical stability. Use CAD software to create the layout, determining component placement and trace routing.
- Substrate Preparation: Prepare the Omega Material substrate by cutting it to size and ensuring surface smoothness. Clean the substrate thoroughly to remove contaminants that could affect adhesion and circuit performance.
- Metallization: Deposit conductive layers onto the substrate to create the circuitry. Techniques like sputtering or electroplating are used to apply metal (typically copper) onto the substrate surface. This forms the conductive traces and pads necessary for electrical connections.
- Patterning: Use photolithography or laser etching to define the circuit pattern on the metallized Omega Material substrate. This step involves applying a photoresist layer, exposing it to UV light through a mask, and developing to remove unwanted areas before etching away excess metal.
- Etching: Chemically etch away the exposed metal to leave behind the desired conductive traces and pads according to the PCB design. Ensure precise alignment and accuracy to maintain electrical connectivity and signal integrity.
- Drilling and Vias: Drill holes (vias) through the substrate where electrical connections are needed between different layers of the PCB. Vias are plated with metal to establish electrical continuity between layers, using processes like electroplating.
- Lamination (for multi-layer PCBs): If producing a multi-layer PCB, laminate the individual Omega Material layers together using heat and pressure. This process ensures strong adhesion between layers and creates interconnected pathways through the vias.
- Surface Finishing: Apply surface finishes such as solder mask to protect exposed metal traces and facilitate soldering during component assembly. Apply a final protective coating to enhance durability and resistance to environmental factors.
- Quality Control: Conduct rigorous testing and inspection throughout the manufacturing process. Perform electrical tests to verify connectivity, impedance control, and insulation resistance. Inspect for defects, dimensional accuracy, and adherence to design specifications.
- Component Assembly: Mount electronic components onto the Omega Materials PCB using automated surface mount technology (SMT) or through-hole assembly techniques. Ensure components are soldered securely to the PCB for reliable electrical connections.
- Final Testing and Verification: Perform comprehensive functional testing of the assembled PCB to ensure proper operation under expected conditions. Test for functionality, reliability, and performance metrics to meet customer requirements and industry standards.
By following these steps, manufacturers can produce Omega Materials PCBs that meet the demanding performance criteria for applications in aerospace, automotive, telecommunications, and high-power electronics industries. Each stage is critical to ensuring the PCB’s functionality, reliability, and longevity in specialized environments.
Test the finished PCB for functionality and quality.
How much should an Omega Materials PCB cost?
The cost of an Omega Materials PCB can vary significantly depending on several factors:
- Material Type: The specific Omega Material used (e.g., aluminum nitride, silicon carbide) can influence cost due to variations in material availability, processing complexity, and performance characteristics.
- Complexity of Design: The complexity of the PCB design, including the number of layers, size of the board, density of components, and routing requirements, impacts manufacturing costs. More complex designs require higher precision and may involve additional processes.
- Manufacturing Process: The chosen manufacturing processes (e.g., metallization techniques, etching methods, lamination for multi-layer boards) affect costs. Specialized processes required for Omega Materials, such as specific etching solutions or controlled atmosphere handling, can increase expenses.
- Quantity: Economies of scale apply in PCB manufacturing; larger production quantities generally result in lower per-unit costs due to optimized setup and production efficiencies.
- Quality Requirements: Higher quality standards, such as tighter tolerances, rigorous testing, and certifications (e.g., IPC standards), can increase costs but ensure reliability and compliance with industry standards.
- Additional Services: Additional services such as assembly of components, testing, conformal coating for protection, and packaging can add to the total cost.
To provide a rough estimate, Omega Materials PCBs typically cost more than conventional FR4 PCBs due to the specialized materials and processes involved. Prices can range from tens to hundreds or even thousands of dollars per board, depending on the factors mentioned above.
For a precise cost estimate, it’s recommended to consult with PCB manufacturers who specialize in Omega Materials PCB fabrication. They can assess your specific design requirements, material choices, and production volume to provide an accurate quotation based on current market conditions and production capabilities.
What is Omega Materials PCB base material?
Omega Materials PCBs often use advanced materials known for their unique properties, including high thermal conductivity, excellent electrical insulation, and sometimes specific magnetic characteristics. The most common base materials used in Omega Materials PCBs include:
- Aluminum Nitride (AlN): This ceramic material is widely used for PCBs that require high thermal conductivity. AlN can efficiently dissipate heat from electronic components, making it ideal for applications in power electronics, RF components, and laser diodes.
- Silicon Carbide (SiC): Another ceramic material known for its high thermal conductivity and excellent mechanical properties. SiC is often used in high-power electronics and semiconductor applications where performance at elevated temperatures is crucial.
- Beryllium Oxide (BeO):A less common material due to its toxic properties but valued for its high thermal conductivity and excellent electrical insulation properties. BeO was historically used in military and aerospace applications.
- Metals and Composites: Some Omega Materials PCBs may use metal substrates like aluminum or copper due to their excellent thermal conductivity. These metal-based substrates are often used in high-power RF applications where thermal management is critical.
- Composite Materials:These materials can include combinations of metals and ceramics or other materials, tailored to specific application needs. Composite materials offer the advantage of combining the best properties of different materials, such as high thermal conductivity with the flexibility of a composite structure.
The choice of base material depends on the specific requirements of the application, such as thermal management, mechanical strength, electrical performance, and operating environment. These materials allow for the creation of high-performance PCBs that can handle the demanding conditions of advanced electronics.
Which company makes Omega Materials PCB?
Currently, companies that produce Omega Materials PCBs mainly include advanced technology firms specializing in high-performance electronic materials and PCB manufacturing. These companies typically possess advanced technologies and facilities capable of handling complex material and process requirements to meet the diverse needs of high-end applications.
Notable companies such as Rogers Corporation, Fujitsu, and Laird Performance Materials have extensive experience in manufacturing high-performance PCBs. They offer a variety of material choices, including high-frequency PCB materials for RF and microwave applications, as well as specialty PCB materials for high-temperature and high-frequency applications.
For our company to enter the field of Omega Materials PCB production, we would need to have the following capabilities and resources:
- Advanced Material Selection and Process Technology: Ability to select and process various Omega Materials such as Aluminum Nitride (AlN), Silicon Carbide (SiC), etc., to customize PCB materials based on customer requirements.
- Professional PCB Design Capability: Experienced PCB design team capable of optimizing designs based on customer specifications to ensure electrical performance, thermal management, and mechanical stability.
- Advanced Manufacturing Facilities and Technology: Equipped with advanced PCB manufacturing equipment and process technologies, including high-precision imaging equipment, chemical etching equipment, metallization equipment, etc., to achieve high-precision manufacturing of complex PCB structures.
- Quality Control and Certification: Establish a rigorous quality control system to ensure quality and stability at every production step, meeting international PCB manufacturing standards and specific customer requirements.
- Customer Service and Technical Support: Provide comprehensive customer service and technical support, including real-time communication and feedback throughout the design and production process, to ensure full understanding and fulfillment of customer needs.
Our company aims to become a leader in the high-end PCB manufacturing sector by offering customized solutions for Omega Materials PCBs through technological innovation and excellent customer service. We have a professional team and advanced equipment capable of meeting stringent requirements in thermal management, high frequency, high power, and environmental adaptability for various high-performance electronic devices.
What are the 7 qualities of good customer service?
Good customer service is characterized by several key qualities that contribute to a positive customer experience. Here are seven important qualities:
- Responsiveness: Being prompt and timely in addressing customer inquiries, issues, or requests. Customers appreciate quick responses and efficient resolutions to their concerns.
- Empathy:Showing empathy means understanding and acknowledging the customer’s feelings, perspectives, and situation. It involves listening attentively, showing compassion, and demonstrating a genuine desire to help.
- Communication skills: Effective communication is essential in customer service. This includes clarity in explanations, active listening to understand customer needs, and the ability to convey information in a courteous and professional manner.
- Problem-solving skills: Being able to resolve customer issues effectively and efficiently. This may involve troubleshooting, finding solutions, and taking proactive steps to prevent similar issues in the future.
- Professionalism: Maintaining a professional demeanor and attitude at all times. This includes being courteous, respectful, and demonstrating competence in handling customer interactions.
- Knowledgeability: Having a good understanding of products or services offered by the company. Knowledgeable customer service representatives can provide accurate information, answer questions confidently, and offer helpful advice.
- Follow-up: Following up with customers to ensure that their concerns have been fully addressed and that they are satisfied with the resolution. This may involve checking in after a service call, confirming that an issue has been resolved, or seeking feedback on their experience.
By embodying these qualities, companies can enhance customer satisfaction, build loyalty, and maintain positive relationships with their customer base. Good customer service not only resolves issues but also leaves customers feeling valued and respected.
FAQs
What are Omega Materials PCBs?
Omega Materials PCBs are printed circuit boards that utilize advanced materials such as ceramics (e.g., aluminum nitride, silicon carbide) or specialized metals. These materials offer enhanced properties like high thermal conductivity, excellent electrical insulation, and sometimes unique magnetic characteristics.
What are the benefits of using Omega Materials PCBs?
Omega Materials PCBs provide superior thermal management capabilities, making them suitable for high-power electronic devices and applications requiring efficient heat dissipation. They also offer excellent electrical performance and can withstand challenging environmental conditions.
In which industries are Omega Materials PCBs commonly used?
Omega Materials PCBs are used in industries such as aerospace, automotive, telecommunications, power electronics, and medical devices. They are preferred for applications where reliability, high performance, and durability are critical.
What types of Omega Materials are typically used in PCBs?
Common Omega Materials used in PCBs include aluminum nitride (AlN), silicon carbide (SiC), beryllium oxide (BeO), and certain specialized metals or composites. Each material has unique properties that cater to specific application requirements.
Are Omega Materials PCBs more expensive than standard PCBs?
Yes, Omega Materials PCBs generally cost more than standard PCBs made from materials like FR4 due to the specialized nature of the materials used and the advanced manufacturing processes required.
What design considerations are important for Omega Materials PCBs?
Design considerations include optimizing thermal management through layout and material selection, ensuring proper electrical performance, and addressing mechanical stability to handle thermal expansion and environmental stresses.
Can any PCB manufacturer produce Omega Materials PCBs?
Not all PCB manufacturers have the capabilities to produce Omega Materials PCBs. It requires expertise in handling advanced materials, specialized equipment for metallization and etching, and adherence to strict quality standards.