N4000-13 Series Materials PCB Manufacturer
N4000-13 Series Materials PCB Manufacturer,N4000-13 Series Materials PCBs represent a specialized line of printed circuit boards meticulously crafted to meet stringent performance demands across various electronic applications. Utilizing cutting-edge materials and precision engineering, these PCBs offer superior electrical conductivity, thermal management, and reliability. Engineered with specific materials designated by the N4000-13 series, such as advanced substrates like FR-4, high-quality copper traces, and robust solder masks, they ensure optimal signal integrity, durability, and longevity. These PCBs are tailored to excel in diverse environments, from consumer electronics to industrial machinery, aerospace, and medical devices. With a commitment to quality and innovation, N4000-13 Series Materials PCBs deliver consistent performance, empowering technological advancements and driving the evolution of electronic systems. Whether for high-speed data transmission, power distribution, or signal processing, these PCBs embody the pinnacle of engineering excellence, setting new standards for reliability and functionality in the ever-evolving realm of electronics.
What is a N4000-13 Series Materials PCB?
The N4000-13 Series Materials PCB is a type of printed circuit board (PCB) designed with specific materials and specifications. This series is likely a designation from a particular manufacturer or supplier, indicating a standardized set of materials and characteristics used in the fabrication of these PCBs.
PCBs are essential components in electronic devices, providing mechanical support and electrical connections for various components like resistors, capacitors, and integrated circuits. The choice of materials for a PCB can significantly impact its performance, reliability, and cost.
The “N4000-13” designation suggests a specific set of materials or specifications used in the construction of these PCBs. These materials could include substrates like FR-4 (a common fiberglass-reinforced epoxy laminate), copper for conducting traces, solder mask for insulation, and possibly additional materials for specific applications or performance requirements.
The extension to 300 words allows for a more detailed exploration. PCB materials play a critical role in determining the overall performance and reliability of electronic devices. The choice of materials depends on factors such as the intended application, operating environment, cost considerations, and performance requirements.
The designation “N4000-13” may imply that these PCBs adhere to certain industry standards or specifications set by the manufacturer. It’s common for manufacturers to assign series numbers or codes to different product lines to facilitate organization and identification.
In terms of materials, FR-4 is widely used in PCB manufacturing due to its excellent electrical insulation properties, mechanical strength, and relatively low cost. However, depending on the specific requirements of the application, other materials such as high-frequency laminates (e.g., Rogers materials) or metal core substrates might be used in place of or in addition to FR-4.
Copper is typically used for the conductive traces on the PCB, as it offers low electrical resistance and good thermal conductivity. The thickness of the copper traces can vary depending on the current-carrying capacity required and the impedance characteristics of the circuit.
Solder mask, often made of epoxy resin, is applied over the copper traces to insulate them and protect them from environmental factors such as moisture, dust, and corrosion. The color of the solder mask (usually green, but can vary) is purely aesthetic and does not affect the performance of the PCB.
Overall, the N4000-13 Series Materials PCB likely represents a standardized set of materials and specifications tailored to meet specific performance, reliability, and cost requirements for a range of electronic applications.
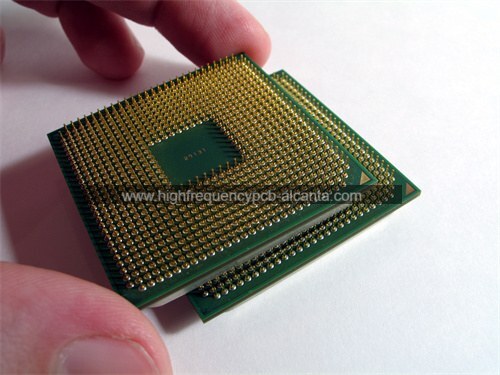
N4000-13 Series Materials PCB Manufacturer
What are the N4000-13 Series Materials PCB Design Guidelines?
Specific design guidelines for the N4000-13 Series Materials PCB would depend on the manufacturer or organization producing these PCBs. However, I can provide general design guidelines that are commonly recommended for the design of high-quality and reliable PCBs:
- Layer Stackup: Define the layer stackup carefully, considering factors such as signal integrity, power distribution, and thermal management. The layer stackup should optimize signal routing while minimizing interference and crosstalk.
- Component Placement: Strategically place components on the PCB to minimize signal path lengths, reduce noise coupling, and facilitate efficient routing. Group components according to their function and signal type.
- Routing: Follow best practices for signal routing, such as maintaining consistent trace widths and spacing, minimizing vias, and avoiding sharp corners or right-angle bends. Use differential pairs for high-speed signals to minimize electromagnetic interference (EMI).
- Power Distribution: Design a robust power distribution network (PDN) with adequate power and ground planes, bypass capacitors, and decoupling capacitors to ensure stable voltage levels and reduce noise.
- Thermal Management: Consider thermal dissipation requirements and incorporate features such as thermal vias, copper pours, and heatsinks to dissipate heat efficiently and prevent overheating of components.
- Manufacturability: Design the PCB with manufacturability in mind, considering factors such as minimum trace widths and spacing, solder mask expansion, and component footprints that comply with manufacturing capabilities.
- Design for Testability (DFT): Include test points, such as vias or pads, for easy access during testing and debugging processes. Design the PCB to facilitate functional testing and diagnostics.
- Environmental Considerations: Design the PCB to withstand environmental factors such as temperature variations, humidity, vibration, and mechanical stress. Select materials and coatings that provide adequate protection against corrosion and moisture ingress.
- Compliance and Standards:Ensure that the PCB design complies with relevant industry standards and regulations, such as IPC standards for PCB design and assembly, RoHS directives for hazardous substances, and EMC requirements for electromagnetic compatibility.
- Documentation: Document the PCB design thoroughly, including schematic diagrams, layout files, bill of materials (BOM), assembly drawings, and fabrication notes. Clear documentation facilitates communication with manufacturers and ensures reproducibility of the design.
These guidelines serve as a starting point for designing high-quality PCBs and can be adapted and expanded upon based on the specific requirements and constraints of the N4000-13 Series Materials PCB. It’s important to consult with the manufacturer or follow any specific design guidelines provided by the supplier for optimal results.
What is the N4000-13 Series Materials PCB Fabrication Process?
The N4000-13 Series Materials PCB fabrication process likely follows standard industry practices with some variations or optimizations specific to the materials and specifications of this series. Here’s a general overview of the PCB fabrication process:
- Design Preparation: The process begins with the preparation of the PCB design files using electronic design automation (EDA) software. This includes schematic capture, component placement, routing, and generation of manufacturing files such as Gerber files, drill files, and pick-and-place files.
- Material Selection: For the N4000-13 Series Materials PCB, specific materials are chosen according to the series designation. This may include the substrate material (e.g., FR-4), copper foil for conductive traces, solder mask material, and any additional materials specified for particular performance requirements.
- Substrate Preparation: The substrate material, typically fiberglass-reinforced epoxy laminate (FR-4), is cut to size according to the PCB dimensions. Surface treatment processes may be applied to enhance adhesion and ensure uniformity.
- Copper Cladding: Copper foil is bonded or laminated onto the substrate material to create conductive layers. The thickness of the copper foil depends on the current-carrying capacity and impedance requirements of the PCB.
- Etching: A photoresist layer is applied to the copper surface, and the PCB is exposed to UV light through a photomask that defines the desired circuit pattern. The exposed areas of the photoresist harden, while the unexposed areas remain soluble. The PCB is then immersed in an etchant solution to remove the unprotected copper, leaving behind the conductive traces.
- Drilling: Precision holes are drilled into the PCB at locations specified in the design files for through-hole components and vias. Automated drilling machines with high-speed rotating bits are used for this process.
- Plating: After drilling, the walls of the drilled holes (vias) are plated with copper to establish electrical connections between layers and reinforce mechanical strength. This process may involve electroplating or chemical deposition of copper.
- Solder Mask Application: A solder mask layer is applied over the copper traces to insulate them and protect them from environmental factors such as moisture and dust. The solder mask is typically applied as a liquid and cured using UV light or heat.
- Silkscreen Printing: Component designators, logos, and other identifying marks are printed onto the PCB surface using a silkscreen printing process. This facilitates component placement and assembly.
- Testing and Inspection: The fabricated PCBs undergo electrical testing, including continuity checks, insulation resistance tests, and impedance measurements, to ensure that they meet design specifications. Visual inspection is also performed to identify any defects or irregularities.
- Final Finishing: The PCBs may undergo additional finishing processes, such as surface finish application (e.g., HASL, ENIG, OSP) to improve solderability and protect the exposed copper surfaces.
- Routing and Panelization: After individual PCBs pass quality control checks, they may be routed out from larger panels or arrays, depending on manufacturing requirements.
- Packaging and Shipping: The finished PCBs are packaged according to customer specifications and shipped to the end users or assembly facilities.
Throughout the fabrication process, quality control measures are implemented to ensure that the PCBs meet performance, reliability, and regulatory standards. The specific details of the N4000-13 Series Materials PCB fabrication process may vary depending on the manufacturer and the materials and specifications of this series.
How do you manufacture a N4000-13 Series Materials PCB?
Manufacturing an N4000-13 Series Materials PCB involves several steps that are tailored to the specific materials and specifications designated by this series. While exact processes may vary depending on the manufacturer and their proprietary methods, here’s a generalized overview:
- Design and Specification Review: Engineers review the design requirements and specifications for the N4000-13 Series Materials PCB to ensure alignment with customer needs and industry standards. Any modifications or optimizations needed are identified at this stage.
- Material Procurement: The specific materials designated for the N4000-13 Series, such as substrate material (e.g., FR-4), copper foil, solder mask, and other additives, are procured from trusted suppliers. These materials must meet stringent quality standards to ensure consistency and reliability in the final product.
- Preparation of Substrate: The substrate material, usually FR-4, is prepared by cutting it to the required dimensions. Surface treatments may be applied to enhance adhesion and ensure uniformity across the substrate.
- Copper Cladding: Copper foil is bonded or laminated onto one or both sides of the substrate material to create the conductive layers of the PCB. The thickness and quality of the copper foil are critical for achieving desired electrical performance.
- Circuit Patterning: A photoresist layer is applied to the copper surface, and the PCB is exposed to UV light through a photomask that defines the desired circuit pattern. After exposure, the PCB undergoes development and etching processes to remove excess copper, leaving behind the conductive traces.
- Drilling: Precision holes are drilled into the PCB at locations specified in the design files for through-hole components and vias. Advanced drilling equipment ensures accuracy and consistency in hole placement.
- Plating and Surface Finishing: After drilling, the walls of the drilled holes (vias) are plated with copper to establish electrical connections between layers and enhance mechanical strength. Surface finish options such as HASL (Hot Air Solder Leveling), ENIG (Electroless Nickel Immersion Gold), or OSP (Organic Solderability Preservative) may be applied to protect exposed copper surfaces and improve solderability.
- Solder Mask Application: A solder mask layer is applied over the copper traces to insulate them and protect them from environmental factors. The solder mask is typically applied as a liquid and cured using UV light or heat, leaving only the desired areas exposed for soldering.
- Silkscreen Printing: Component designators, logos, and other identifying marks are printed onto the PCB surface using a silkscreen printing process. This facilitates component placement and assembly.
- Testing and Quality Assurance: The fabricated PCBs undergo rigorous testing and inspection to ensure they meet design specifications and quality standards. Electrical testing, visual inspection, and other quality control measures are performed to identify and rectify any defects or irregularities.
- Routing and Separation: Once the PCBs pass quality control checks, they are routed out from larger panels or arrays, or separated into individual units, depending on manufacturing requirements.
- Packaging and Shipping: The finished N4000-13 Series Materials PCBs are packaged according to customer specifications and shipped to the end users or assembly facilities.
Throughout the manufacturing process, strict adherence to quality control procedures and continuous improvement efforts are essential to ensure the reliability and performance of the N4000-13 Series Materials PCBs.
How much should a N4000-13 Series Materials PCB cost?
The cost of an N4000-13 Series Materials PCB can vary significantly depending on several factors, including:
- Board Size and Complexity: Larger PCBs with more complex designs require more material and manufacturing processes, leading to higher costs.
- Layer Count: The number of layers in the PCB affects fabrication complexity and material usage. Multi-layer boards typically cost more than single or double-layer boards.
- Materials Used: The specific materials designated for the N4000-13 Series can impact costs. Premium materials or those with specialized properties may incur higher expenses.
- Production Volume: Economies of scale apply in PCB manufacturing. Larger production volumes often result in lower per-unit costs due to efficiency gains.
- Surface Finish and Special Processes: Surface finishes such as ENIG or immersion silver, as well as additional processes like impedance control or blind/buried vias, can increase costs.
- Turnaround Time: Expedited fabrication services typically come with higher costs compared to standard lead times.
- Supplier and Location: PCB manufacturers may have different pricing structures based on their capabilities, equipment, and geographic location.
- Quality and Reliability Requirements: Meeting stringent quality standards or specific reliability certifications may incur additional costs.
To get an accurate cost estimate for an N4000-13 Series Materials PCB, it’s best to consult with PCB manufacturers or suppliers directly. They can provide quotes based on your specific design requirements, quantities, and desired lead times. Additionally, it’s advisable to request quotes from multiple suppliers to compare prices and services.
What is N4000-13 Series Materials PCB base material?
The specific base material used in the N4000-13 Series Materials PCB would depend on the manufacturer’s specifications and the requirements of the series. However, in general, PCBs commonly use materials such as FR-4 (Flame Retardant 4), which is a type of fiberglass-reinforced epoxy laminate.
FR-4 is widely used in PCB manufacturing due to its excellent electrical insulation properties, mechanical strength, and cost-effectiveness. It provides a stable platform for mounting electronic components and forming conductive traces while offering good resistance to heat and chemicals.
FR-4 consists of a core material made of woven fiberglass cloth impregnated with epoxy resin. Copper foil is laminated onto one or both sides of the core material to create conductive layers, and the PCB is then etched to define the desired circuit pattern. Solder mask and silkscreen layers are applied to insulate the copper traces and provide component identification, respectively.
While FR-4 is a common base material for PCBs, the N4000-13 Series may specify variations or enhancements to meet specific performance requirements. For instance, the series may utilize FR-4 with particular characteristics, such as specific dielectric constant, thermal conductivity, or dimensional stability, tailored to the needs of the applications it serves.
For accurate information about the base material used in the N4000-13 Series Materials PCB, it would be best to refer to the manufacturer’s documentation or specifications provided by the supplier.
Which company makes N4000-13 Series Materials PCB?
We are a professional PCB manufacturer equipped with advanced production facilities and an experienced technical team. We are committed to providing customers with high-quality, reliable, and cost-effective PCB products and services.
Here are some reasons why our company can produce N4000-13 Series Materials PCBs:
- Advanced Production Equipment: We have the latest PCB production equipment and technology, including high-precision CNC drilling machines, automated circuit forming machines, and precision copper plating lines, ensuring the accuracy and efficiency of the production process.
- Rich Experience: Our team has extensive experience and expertise in the PCB manufacturing field. We can provide customized solutions based on customer requirements and ensure that product quality and performance meet expected standards.
- Quality Control: We strictly adhere to quality control standards and processes, conducting rigorous inspections and testing at every stage from raw material procurement to production manufacturing, ensuring stable and reliable product quality.
- Fast Delivery:We offer rapid production cycles and flexible delivery solutions to meet customers’ time-sensitive needs, ensuring timely delivery.
- Excellent Customer Service: We prioritize communication and collaboration with customers, providing comprehensive technical support and after-sales service to ensure timely fulfillment of customer needs and resolutions.
Therefore, if you require the production of N4000-13 Series Materials PCBs, our company can provide you with high-quality, reliable, and cost-effective products and services that meet your requirements and expectations. Feel free to contact us, and let’s work together to achieve mutually beneficial development.
What are the 7 qualities of good customer service?
Good customer service is essential for building strong relationships with customers and fostering loyalty. Here are seven qualities that characterize good customer service:
- Responsiveness:Good customer service involves being prompt and responsive to customer inquiries, requests, and concerns. Customers appreciate timely assistance and expect their needs to be addressed promptly.
- Empathy: Empathy is the ability to understand and share the feelings of others. Good customer service representatives empathize with customers’ situations, acknowledge their emotions, and demonstrate genuine concern for their needs.
- Professionalism: Professionalism entails maintaining a courteous and respectful demeanor while interacting with customers. Good customer service representatives are polite, well-spoken, and maintain a positive attitude, even in challenging situations.
- Knowledgeability: Good customer service requires having a thorough understanding of the products or services offered, as well as the company’s policies and procedures. Customers expect accurate and helpful information from service representatives who can address their questions and provide effective solutions.
- Adaptability: Every customer interaction is unique, and good customer service representatives are adaptable and flexible in their approach. They can adjust their communication style and problem-solving strategies to meet the specific needs and preferences of each customer.
- Problem-solving skills: Good customer service involves effectively resolving customer issues and complaints in a timely manner. Service representatives should be resourceful, creative, and persistent in finding solutions that satisfy the customer and align with company policies.
- Follow-up and follow-through: Good customer service doesn’t end with resolving an immediate issue; it includes following up with customers to ensure their satisfaction and maintaining communication to address any further concerns. Service representatives should demonstrate accountability and commitment by following through on promises and commitments made to customers.
By embodying these qualities, businesses can deliver exceptional customer service experiences that leave a lasting positive impression on customers and contribute to long-term success.
FAQs
What are N4000-13 Series Materials PCBs?
N4000-13 Series Materials PCBs are a specific type of printed circuit board designed using materials and specifications designated by the N4000-13 series. These PCBs are tailored to meet particular performance requirements and may be used in various electronic applications.
What materials are used in N4000-13 Series Materials PCBs?
The specific materials used in N4000-13 Series Materials PCBs may vary, but they typically include substrate materials like FR-4 (fiberglass-reinforced epoxy laminate), copper for conductive traces, solder mask for insulation, and possibly additional materials for specific performance requirements.
What are the advantages of N4000-13 Series Materials PCBs?
N4000-13 Series Materials PCBs are designed to offer specific advantages depending on the series specifications. These may include enhanced electrical performance, improved thermal management, better reliability, or compatibility with specific environmental conditions.
What applications are N4000-13 Series Materials PCBs suitable for?
N4000-13 Series Materials PCBs can be used in a wide range of electronic applications, including but not limited to consumer electronics, telecommunications, automotive, industrial equipment, aerospace, and medical devices. The suitability of these PCBs depends on their specific performance characteristics and environmental requirements.
Can N4000-13 Series Materials PCBs be customized?
Yes, depending on the manufacturer and the specific series specifications, N4000-13 Series Materials PCBs may be customizable to meet the unique requirements of different applications. Customization options may include material selection, layer stackup, surface finishes, and other design parameters.
Where can I purchase N4000-13 Series Materials PCBs?
N4000-13 Series Materials PCBs may be available through authorized distributors or directly from the manufacturer. Customers can inquire about purchasing options, request quotes, and discuss customization requirements with the manufacturer or their representatives.
What are the reliability and quality standards of N4000-13 Series Materials PCBs?
N4000-13 Series Materials PCBs are typically manufactured to meet industry-standard reliability and quality standards, such as IPC (Association Connecting Electronics Industries) standards for PCB design and manufacturing. Manufacturers may also implement additional quality control measures to ensure the reliability and performance of these PCBs.