MW4000 Materials PCB Manufacturer
MW4000 Materials PCB Manufacturer,MW4000 Materials PCBs represent the pinnacle of innovation in the field of printed circuit boards, engineered to meet the rigorous demands of high-performance electronic applications. Utilizing advanced MW4000 materials, these PCBs offer unparalleled thermal conductivity, signal integrity, and mechanical stability. They are meticulously designed to excel in environments where reliability and performance are non-negotiable, such as aerospace, telecommunications, and medical devices. MW4000 Materials PCBs boast exceptional properties, including low loss tangent, high dielectric constant, and resistance to environmental stressors like moisture and temperature fluctuations. With their superior design and construction, MW4000 Materials PCBs enable the development of cutting-edge electronic systems that push the boundaries of technology. Whether in radar systems, microwave devices, or power amplifiers, these PCBs provide the foundation for innovation, ensuring that electronic devices operate at peak efficiency and reliability.
What is a MW4000 Materials PCB?
The MW4000 Materials PCB refers to a specific type of printed circuit board (PCB) designed to meet the requirements of MW4000 materials. These materials could include a range of substances such as ceramics, polymers, metals, or composites, tailored for specific industrial or electronic applications.
The MW4000 designation likely denotes a particular set of specifications or standards, possibly related to the material composition, durability, thermal conductivity, or electrical properties required for the intended application. This PCB might be optimized for high-frequency operations, harsh environments, or other specialized uses where standard PCB materials wouldn’t suffice.
Manufacturers might develop MW4000 Materials PCBs to cater to industries like aerospace, telecommunications, or medical devices, where reliability, performance, and longevity are paramount. These PCBs could undergo rigorous testing and quality control to ensure they meet stringent industry standards and regulatory requirements.
In essence, the MW4000 Materials PCB is a tailored circuit board solution optimized for specific material properties, aimed at fulfilling the demands of advanced technological applications. Its design and composition are likely carefully engineered to deliver optimal performance and reliability in challenging operating conditions.
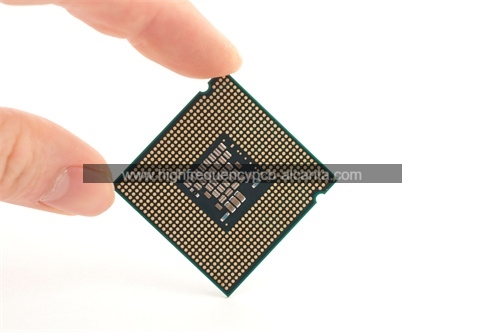
MW4000 Materials PCB Manufacturer
What are MW4000 Materials PCB Design Guidelines?
MW4000 Materials PCB design guidelines are specific recommendations and principles for designing printed circuit boards (PCBs) using MW4000 materials. These guidelines are crucial for ensuring the reliability, performance, and manufacturability of the PCBs, especially when dealing with specialized materials like MW4000.
Here are some common aspects covered in MW4000 Materials PCB design guidelines:
- Material Selection: Guidelines would specify the types of MW4000 materials suitable for PCB fabrication, considering factors such as thermal conductivity, dielectric properties, and mechanical strength.
- Layer Stackup: Recommendations for layer stackup configuration to optimize signal integrity, minimize impedance mismatches, and provide sufficient isolation between signal layers and power/ground planes.
- Trace Routing: Guidelines for routing signal traces to maintain controlled impedance, minimize signal distortion, and reduce electromagnetic interference (EMI). This includes specifying trace widths, spacing, and via placement rules.
- Component Placement: Recommendations for placing components on the PCB to minimize signal distortion, optimize signal paths, and ensure thermal management. Proper component placement can also aid in efficient assembly and testing processes.
- Thermal Management: Guidelines for managing heat dissipation, especially important for MW4000 materials that may have specific thermal properties. This includes proper placement of thermal vias, heat sinks, and consideration of airflow within the system.
- Manufacturability: Design guidelines should ensure that the PCB design is manufacturable using standard fabrication processes while adhering to the unique requirements of MW4000 materials. This involves considerations such as minimum feature sizes, aspect ratios, and tolerances.
- Signal Integrity and EMI: Recommendations for reducing signal distortion and minimizing electromagnetic interference to ensure reliable operation of the PCB in its intended environment.
- Testing and Validation: Guidelines for testing and validating the PCB design to ensure it meets performance specifications and reliability requirements. This may involve simulation, prototyping, and testing under various operating conditions.
- Compliance and Standards: Ensuring that the PCB design complies with relevant industry standards and regulations, particularly in industries with stringent quality and safety requirements.
By following these design guidelines, engineers can create MW4000 Materials PCBs that meet the performance, reliability, and manufacturability requirements of their intended applications.
What is the MW4000 Materials PCB Fabrication Process?
The MW4000 Materials PCB fabrication process involves several key steps tailored to the specific requirements of MW4000 materials. While the exact process may vary depending on factors like the material composition and intended application, here’s a general overview of the typical steps involved:
- Material Selection and Preparation:The process begins with selecting the appropriate MW4000 materials based on the desired electrical, mechanical, and thermal properties. These materials may include specialized substrates, copper foils, and dielectric layers. The materials are inspected for quality and prepared for subsequent manufacturing steps.
- Layer Stackup Design: Engineers design the layer stackup configuration based on the PCB’s electrical requirements, including signal integrity, impedance control, and thermal management. This involves determining the number of layers, copper thickness, dielectric constants, and material properties for each layer in the stack.
- Printed Circuit Board Design: Using specialized PCB design software, engineers create the layout of the PCB, including the placement of components, routing of signal traces, and allocation of power and ground planes. Design considerations include minimizing signal distortion, optimizing signal paths, and ensuring proper thermal management.
- Prepreg and Core Material Preparation: Prepreg (pre-impregnated) and core materials are prepared by cutting them to the required dimensions and stacking them according to the layer stackup design. Prepreg layers are typically bonded together using heat and pressure to form a rigid composite structure.
- Drilling: Precision drilling machines are used to create holes (vias) in the PCB substrate for component mounting and interconnection between layers. Laser drilling may be used for high-density interconnect (HDI) PCBs or applications requiring fine features.
- Through-Hole Plating: After drilling, the vias are plated with conductive materials such as copper to establish electrical connections between layers. This process may involve electroless or electrolytic plating techniques to deposit metal inside the vias and onto the surface of the PCB.
- Copper Etching:Excess copper is removed from the surface of the PCB using chemical etching processes. Etching is controlled by applying a mask (usually photoresist) to protect desired copper traces while exposing areas for removal.
- Surface Finish: The exposed copper surfaces are treated with a surface finish to improve solderability, prevent oxidation, and enhance reliability. Common surface finish options include immersion gold, electroless nickel immersion gold (ENIG), and immersion tin.
- Solder Mask Application: A solder mask is applied to the PCB surface to insulate copper traces and pads, protect against environmental factors, and define solderable areas for component attachment. Solder mask application typically involves screen printing and curing processes.
- Silkscreen Printing: PCBs may undergo silkscreen printing to apply component designators, logos, and other identifying information to the board surface. This information helps during assembly, testing, and troubleshooting processes.
- Testing and Inspection: Finished PCBs undergo thorough testing and inspection to verify electrical continuity, signal integrity, dimensional accuracy, and compliance with design specifications. This may include automated optical inspection (AOI), electrical testing, and functional testing.
- Packaging and Shipping: Once PCBs pass quality control checks, they are packaged according to customer requirements and shipped to their destination for assembly into electronic devices or systems.
Throughout the fabrication process, quality control measures are implemented to ensure that MW4000 Materials PCBs meet the required performance, reliability, and regulatory standards for their intended applications. Collaboration between design engineers, fabricators, and quality assurance teams is essential to achieving successful outcomes.
How do you manufacture a MW4000 Materials PCB?
Manufacturing a MW4000 Materials PCB involves several specialized steps tailored to the specific properties and requirements of MW4000 materials. Here’s a generalized outline of the manufacturing process:
- Material Selection: Choose MW4000 materials based on the desired properties such as dielectric constant, thermal conductivity, and mechanical strength. Common MW4000 materials include specialized substrates, copper foils, and dielectric layers.
- Preparation of Substrates: Cut and prepare the substrate materials according to the required dimensions and specifications. This may involve cleaning, surface treatment, and inspection to ensure material quality and consistency.
- Layer Stackup Design: Design the layer stackup configuration based on the PCB’s electrical requirements, including signal integrity, impedance control, and thermal management. Determine the number of layers, copper thickness, and dielectric constants for each layer in the stack.
- Circuit Pattern Imaging: Use photolithography or direct imaging techniques to transfer the circuit patterns onto the substrate materials. This typically involves applying a photoresist layer, exposing it to UV light through a photomask, and developing to reveal the desired circuit patterns.
- Copper Plating: Deposit copper onto the substrate surface to form conductive traces and pads. This may involve electroplating or electroless plating processes to achieve the required thickness and conductivity. Excess copper is then removed through etching, leaving behind the desired circuit patterns.
- Via Formation: Drill holes (vias) through the substrate to create electrical connections between layers. Vias are typically formed using mechanical drilling or laser drilling techniques, followed by through-hole plating to metallize the vias and establish electrical continuity.
- Surface Finish: Apply a surface finish to protect exposed copper surfaces, improve solderability, and prevent oxidation. Common surface finish options for MW4000 Materials PCBs include immersion gold, ENIG (electroless nickel immersion gold), and immersion tin.
- Solder Mask Application: Apply a solder mask over the PCB surface to insulate copper traces and pads, define solderable areas, and protect against environmental factors. Solder mask application is typically done using screen printing or curtain coating techniques, followed by curing to harden the mask.
- Silkscreen Printing:Add identifying information such as component designators, logos, and reference indicators to the PCB surface using silkscreen printing. This information assists during assembly, testing, and troubleshooting processes.
- Testing and Inspection: Conduct thorough testing and inspection of the finished PCBs to verify electrical continuity, signal integrity, dimensional accuracy, and compliance with design specifications. This may include visual inspection, electrical testing, and functional testing.
- Final Finishing and Packaging: Perform any final finishing processes such as edge routing, scoring, or panelization, depending on customer requirements. Package the finished PCBs according to customer specifications and prepare them for shipment.
Throughout the manufacturing process, quality control measures are implemented to ensure that MW4000 Materials PCBs meet the required performance, reliability, and regulatory standards for their intended applications. Collaboration between design engineers, manufacturing technicians, and quality assurance teams is essential to achieving successful outcomes.
How much should a MW4000 Materials PCB cost?
The cost of a MW4000 Materials PCB can vary widely depending on several factors including:
- Material Costs: MW4000 materials may be more expensive than standard PCB materials due to their specialized properties. The cost of the substrate, copper foil, and dielectric materials used in the PCB fabrication process can significantly impact the overall cost.
- Complexity of Design: PCBs with complex designs, multiple layers, fine features, and high-density interconnects typically require more time and resources to manufacture, which can increase the cost.
- Manufacturing Processes: Certain manufacturing processes such as laser drilling, controlled impedance routing, and specialized surface finishes may incur additional costs compared to standard fabrication techniques.
- Quantity: Economies of scale often apply in PCB manufacturing, meaning that larger production quantities typically result in lower per-unit costs. Ordering larger volumes of MW4000 Materials PCBs may lead to cost savings.
- Additional Services: Additional services such as design engineering support, prototyping, testing, and quality assurance may add to the overall cost of the PCBs.
- Supplier and Location: The choice of PCB supplier and their location can also influence the cost. Suppliers with advanced manufacturing capabilities and expertise in working with MW4000 materials may charge higher prices for their services.
- Market Conditions: Market demand, supply chain disruptions, and fluctuations in material prices can all impact the cost of MW4000 Materials PCBs.
As a rough estimate, MW4000 Materials PCBs may cost anywhere from a few dollars to several hundred dollars per unit, depending on the factors mentioned above. For a more accurate cost assessment, it’s advisable to consult with PCB manufacturers or suppliers who specialize in MW4000 materials and provide quotes based on your specific requirements and volume needs.
What is MW4000 Materials PCB base material?
MW4000 Materials PCBs typically utilize advanced base materials tailored to meet the specific requirements of MW4000 materials. While the exact composition may vary depending on the manufacturer and application, these base materials often include specialized substrates and laminates with unique properties such as:
- High Thermal Conductivity: MW4000 Materials PCB base materials may feature high thermal conductivity to efficiently dissipate heat generated during operation, particularly in high-power electronic devices or applications requiring thermal management.
- Low Dielectric Loss: Low dielectric loss is essential for maintaining signal integrity and minimizing signal attenuation in high-frequency applications. MW4000 Materials PCB base materials are engineered to exhibit low dielectric loss properties, enabling efficient transmission of high-speed signals.
- Excellent Electrical Performance: MW4000 Materials PCB base materials are designed to offer excellent electrical performance, including consistent impedance control, low insertion loss, and minimal signal distortion. This ensures reliable operation and high signal fidelity in demanding electronic systems.
- Mechanical Stability: Mechanical stability is crucial to prevent warping, delamination, or mechanical failure of the PCB during assembly, handling, and operation. MW4000 Materials PCB base materials are formulated to provide exceptional mechanical stability and dimensional accuracy, even under harsh environmental conditions.
- Chemical Resistance: MW4000 Materials PCB base materials may possess chemical resistance properties to withstand exposure to corrosive substances, cleaning solvents, and environmental contaminants encountered in industrial or aerospace applications.
- Flame Retardancy: Flame retardancy is important for ensuring the safety of electronic devices, particularly in applications where fire hazards are a concern. MW4000 Materials PCB base materials may incorporate flame-retardant additives or comply with industry standards for fire resistance.
Common types of base materials used for MW4000 Materials PCBs include specialized substrates such as ceramic-filled polymeric materials, thermally conductive laminates, and high-performance resin systems tailored to meet the stringent requirements of MW4000 materials. These base materials are selected and optimized based on the specific performance criteria and environmental conditions of the intended application.
Which company makes MW4000 Materials PCB?
MW4000 Materials PCB is a specific type of circuit board, typically used in high-performance applications that require special materials and processes, such as high-frequency communication, high-speed electronic devices, and military applications. Currently, companies capable of producing such high-performance PCBs are mostly specialized circuit board manufacturers, which typically have advanced manufacturing technology and material development capabilities.
Our Company’s Capabilities and Services:
As a member of the circuit board manufacturing industry, our company has many years of production experience and technological accumulation, fully capable of producing MW4000 Materials PCBs. Here are several key advantages of ours in the production of these boards:
- Advanced Manufacturing Equipment: We have invested in a series of high-end manufacturing equipment, including precision drilling and milling machinery, advanced chemical and physical plating equipment, and sophisticated testing and inspection equipment. These ensure that we can produce complex circuit boards while maintaining high precision and quality.
- Professional Technical Team: We have an experienced team of engineers who have a deep understanding of circuit board design, material science, and manufacturing processes. Team members regularly receive training on the latest technologies to ensure they can address various high-tech challenges encountered in production.
- Strict Quality Control System: We implement a strict quality management system, with detailed quality control at every step from raw material procurement to finished product delivery. We use automated optical inspection equipment and electrical testing equipment to ensure that each PCB meets customer and international standards.
- Optimized Material Selection: To meet the special requirements of MW4000 Materials PCBs, we cooperate with leading material suppliers worldwide to select the highest quality substrates and auxiliary materials. Our supply chain team ensures the quality and stability of these materials.
- Customized Services: We understand that different customers and application fields have varying requirements for circuit boards. Therefore, we provide full-process customized services from design and prototyping to mass production, ensuring that the final product fully meets the specific needs of our customers.
With these advantages and capabilities, our company not only can produce MW4000 Materials PCBs but also can ensure that the produced circuit boards achieve top-level performance, reliability, and durability. If you have a need for such PCBs, please feel free to contact us for more information or a quotation. We look forward to becoming your reliable partner and jointly developing high-performance circuit board solutions that meet your needs.
What are the 7 qualities of good customer service?
Good customer service is characterized by several key qualities that contribute to positive customer experiences and satisfaction. Here are seven qualities often associated with effective customer service:
- Responsiveness: A good customer service team responds promptly to customer inquiries, questions, and concerns. Whether it’s via phone, email, chat, or in person, being available and responsive shows customers that their needs are valued and taken seriously.
- Empathy: Empathy involves understanding and acknowledging the customer’s perspective, feelings, and emotions. Customer service representatives who demonstrate empathy can connect with customers on a personal level, showing that they genuinely care about resolving issues and meeting their needs.
- Clear Communication:Clear communication is essential for ensuring that customers understand the information provided and the steps taken to address their concerns. Customer service representatives should communicate effectively, using language that is easy to understand and avoiding jargon or technical terms when necessary.
- Problem-Solving Skills: Effective problem-solving skills enable customer service representatives to identify issues, analyze root causes, and find appropriate solutions. They should be able to think critically, troubleshoot problems efficiently, and escalate issues as needed to ensure timely resolution.
- Professionalism: Professionalism encompasses qualities such as politeness, respect, and integrity in all interactions with customers. Customer service representatives should maintain a positive and professional demeanor, even in challenging situations, to build trust and confidence with customers.
- Knowledgeability: Customer service representatives should possess a thorough understanding of the products or services offered by the company, as well as company policies, procedures, and resources available to assist customers. Being knowledgeable allows representatives to provide accurate information and helpful guidance to customers.
- Follow-Up and Feedback: Following up with customers after resolving an issue or completing a transaction shows that the company values their feedback and wants to ensure their satisfaction. Good customer service includes seeking feedback, addressing any remaining concerns, and continuously striving to improve the overall customer experience.
By embodying these qualities, businesses can deliver exceptional customer service that fosters loyalty, generates positive word-of-mouth, and contributes to long-term success.
FAQs
What are MW4000 Materials PCBs?
MW4000 Materials PCBs are specialized printed circuit boards designed using MW4000 materials, which offer specific properties tailored for high-performance applications. These materials may include ceramics, polymers, metals, or composites optimized for factors like thermal conductivity, dielectric constant, and mechanical strength.
What are the advantages of MW4000 Materials PCBs?
MW4000 Materials PCBs offer several advantages, including enhanced thermal management, improved signal integrity at high frequencies, excellent mechanical stability, and resistance to environmental factors such as moisture, chemicals, and temperature extremes. These properties make them suitable for demanding applications in industries like aerospace, telecommunications, and medical devices.
What are the typical applications of MW4000 Materials PCBs?
MW4000 Materials PCBs are commonly used in high-frequency communication systems, radar systems, microwave devices, power amplifiers, aerospace electronics, medical imaging equipment, and other high-performance electronic devices where reliability, performance, and durability are critical.
How do MW4000 Materials PCBs differ from standard PCBs?
MW4000 Materials PCBs differ from standard PCBs primarily in the materials used and their specialized properties. MW4000 materials are selected and engineered to meet the specific requirements of high-frequency and high-power applications, offering advantages such as lower loss tangent, higher thermal conductivity, and improved signal integrity compared to standard PCB materials.
Can MW4000 Materials PCBs be manufactured using standard processes?
While MW4000 Materials PCBs require specialized materials and design considerations, they can generally be manufactured using standard PCB fabrication processes with some modifications. However, certain steps such as material selection, layer stackup design, and thermal management may require tailored approaches to optimize performance and reliability.
Are MW4000 Materials PCBs more expensive than standard PCBs?
Due to the use of specialized materials and additional design considerations, MW4000 Materials PCBs may be more expensive than standard PCBs. However, the cost may vary depending on factors such as material composition, complexity of design, manufacturing processes, and production volume.
Where can I find suppliers of MW4000 Materials PCBs?
Suppliers of MW4000 Materials PCBs can be found through online directories, industry trade shows, or by directly contacting specialized PCB manufacturers with expertise in high-frequency and high-performance applications. It’s important to choose a reputable supplier with experience in producing MW4000 Materials PCBs to ensure quality and reliability.