MW2000 Materials PCB Manufacturer
MW2000 Materials PCB Manufacture,MW2000 Materials PCBs utilize advanced materials known for their high thermal conductivity and excellent electrical properties. These PCBs are designed to handle high-frequency signals and power efficiently, making them ideal for applications in RF/microwave communication systems, radar systems, and aerospace electronics. MW2000 Materials PCBs offer low loss tangent and stable dielectric constant across a wide range of frequencies, ensuring reliable signal transmission and minimal signal distortion. They are crucial in industries where precise signal integrity and high-performance reliability are paramount. MW2000 Materials PCBs are engineered with precision to meet stringent requirements for high-speed data transfer and electromagnetic compatibility (EMC).
What is MW2000 Materials PCB?
MW2000 Materials PCB refers to a type of high-frequency printed circuit board (PCB) substrate known for its excellent performance in microwave and RF applications. These PCBs are designed to meet the stringent requirements of modern communication systems, radar systems, satellite communications, and other high-frequency electronic devices.
MW2000 Materials PCBs are typically characterized by their low dielectric constant (εr) and low dissipation factor (Df), which ensure minimal signal loss and high signal integrity at high frequencies. They are often made from high-performance materials like PTFE (Polytetrafluoroethylene) or similar fluoropolymer-based substrates, which offer excellent electrical properties and stability across a wide temperature range.
In addition to their electrical properties, MW2000 Materials PCBs are also engineered to provide good mechanical strength and dimensional stability, crucial for maintaining performance under varying environmental conditions. Their design may include features like controlled impedance traces, which are essential for ensuring signal integrity in high-speed data transmission.
Manufacturers of MW2000 Materials PCBs adhere to stringent quality standards and utilize advanced fabrication techniques to produce boards with precise layer alignment and fine conductor patterns. These PCBs are used in applications demanding high reliability, high frequency operation, and consistent performance over extended periods.
Overall, MW2000 Materials PCBs are integral to the advancement of technologies requiring high-frequency signal processing, making them a preferred choice in industries where performance and reliability are critical considerations.
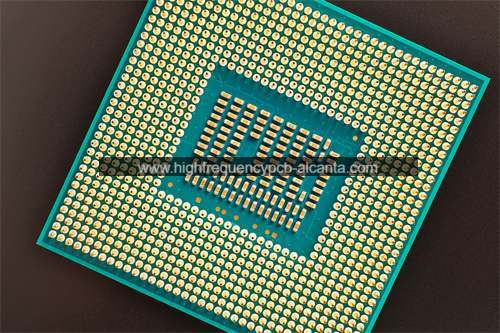
MW2000 Materials PCB Manufacturer
What are the MW2000 Materials PCB Design Guidelines?
Designing MW2000 Materials PCBs involves adhering to specific guidelines to ensure optimal performance and reliability in high-frequency applications. Here are some key design guidelines for MW2000 Materials PCBs:
- Material Selection: Choose high-performance materials with low dielectric constant (εr) and low dissipation factor (Df), typically based on PTFE (Polytetrafluoroethylene) or similar fluoropolymer substrates like Rogers RO4000 series. These materials provide excellent electrical properties needed for high-frequency signals.
- Layer Stackup: Design a layer stackup that minimizes signal loss and cross-talk. Maintain controlled impedance by carefully selecting the thickness and spacing of PCB layers.
- Transmission Line Design: Use controlled impedance transmission lines to match the characteristic impedance required by your high-frequency signals. This ensures minimal signal reflections and maintains signal integrity.
- Routing and Signal Integrity: Route high-frequency traces as short and direct as possible to minimize losses. Avoid sharp bends and use gradual curves with appropriate trace widths to maintain impedance consistency.
- Grounding: Implement a solid ground plane to provide a low impedance return path for high-frequency signals. Separate analog and digital ground planes if necessary and ensure proper grounding techniques to minimize noise and interference.
- Component Placement: Place critical components close to each other to minimize trace lengths and reduce parasitic effects. Follow best practices for component orientation and spacing to maintain signal integrity.
- Thermal Management: Consider thermal management strategies, especially if the PCB operates at high power levels. Design for adequate heat dissipation and ensure the substrate material can handle thermal stresses.
- Manufacturability: Consult with PCB manufacturers experienced in handling high-frequency materials like MW2000. Ensure the design can be feasibly fabricated with high precision and meets the manufacturer’s capabilities.
- Testing and Validation: Perform signal integrity simulations and testing to verify the design meets performance requirements. Validate the PCB design against electrical specifications and environmental conditions expected during operation.
By following these design guidelines, designers can optimize MW2000 Materials PCBs for high-frequency applications, ensuring reliable performance and minimizing signal degradation.
What is the MW2000 Materials PCB Fabrication Process?
The fabrication process for MW2000 Materials PCBs, designed for high-frequency applications, involves several specialized steps to ensure precise construction and optimal electrical performance. Here’s an overview of the typical fabrication process:
- Material Preparation: The process begins with selecting high-performance materials suitable for high-frequency applications, such as PTFE (Polytetrafluoroethylene)-based substrates like Rogers RO4000 series or similar fluoropolymer materials. These materials have low dielectric constant (εr) and low dissipation factor (Df), critical for minimizing signal loss at high frequencies.
- Preparation of Substrate Layers: Layers of the chosen substrate material are prepared and cut to the required dimensions. The substrate layers may include copper foil laminated to both sides to form the conductive layers.
- Copper Foil Preparation: Copper foil sheets are cleaned and treated to ensure good adhesion to the substrate material. The copper thickness and surface roughness are controlled to meet the design specifications for impedance control and signal integrity.
- Layer Stackup: The prepared substrate layers and copper foils are stacked according to the designed layer stackup. This stackup includes alternating layers of substrate material and conductive copper foils, with specific layer thicknesses and configurations to achieve the desired impedance characteristics.
- Lamination: The layered stack is then laminated together under heat and pressure using a hydraulic press or vacuum lamination process. This step bonds the substrate layers and copper foils into a single rigid structure, ensuring good electrical and mechanical properties.
- Drilling: After lamination, precision CNC (Computer Numerical Control) drilling machines are used to create holes for vias and component mounting pads. The drill holes must be accurately positioned to maintain signal integrity and ensure proper alignment with the PCB design.
- Copper Plating: Copper plating is applied to the walls of the drilled holes to form conductive vias that connect different layers of the PCB. This process involves several steps, including cleaning, activation, electroless copper deposition, and electroplating to build up the required thickness of copper.
- Circuit Patterning: A photoresist material is applied to the surface of the PCB and exposed to UV light through a photomask that defines the circuit pattern. After exposure and development, the unwanted copper is etched away using chemical solutions, leaving behind the desired conductive traces and pads.
- Surface Finish: The exposed copper surfaces are coated with a surface finish to protect them from oxidation and ensure solderability during assembly. Common surface finishes for MW2000 Materials PCBs include immersion gold (ENIG), immersion silver, or OSP (Organic Solderability Preservatives).
- Quality Control: Throughout the fabrication process, quality control measures are implemented to verify dimensional accuracy, layer alignment, copper thickness, and adherence to design specifications. Electrical testing may include checks for impedance control and continuity of conductive paths.
- Final Inspection: Once fabrication is complete, the finished PCBs undergo final inspection to ensure they meet customer requirements and industry standards for high-frequency performance and reliability.
By following these steps, manufacturers can produce MW2000 Materials PCBs that offer excellent electrical characteristics, reliability, and performance in demanding high-frequency applications such as telecommunications, radar systems, and satellite communications.
How do you manufacture MW2000 Materials PCBs?
Manufacturing MW2000 Materials PCBs involves a specialized process tailored for high-frequency applications. Here’s a detailed overview of how MW2000 Materials PCBs are manufactured:
- Material Selection: Choose high-performance materials suitable for high-frequency applications, typically based on PTFE (Polytetrafluoroethylene) or similar fluoropolymer substrates like Rogers RO4000 series. These materials offer low dielectric constant (εr) and low dissipation factor (Df) to minimize signal loss at high frequencies.
- Preparation of Substrate: Cut the substrate material into panels or sheets of the required size and thickness. Clean and prepare the substrate surfaces to ensure they are free from contaminants that could affect bonding and electrical performance.
- Copper Foil Preparation:Prepare thin sheets of copper foil with controlled thickness and surface roughness. The copper foil will be laminated to the substrate to form conductive layers.
- Layer Stackup Design: Design the layer stackup based on the PCB requirements, including the number of layers, thickness of each layer, and the arrangement of substrate and copper foil layers. Considerations include impedance control, signal routing, and mechanical stability.
- Lamination: Assemble the prepared substrate layers and copper foils into a layered stack. Use heat and pressure in a laminating press or vacuum lamination process to bond the layers together into a solid, rigid structure. This step is crucial for achieving good electrical and mechanical properties.
- Drilling: Use precision CNC (Computer Numerical Control) drilling machines to drill holes through the layered stack for vias and component mounting pads. Ensure accurate positioning and alignment of drill holes according to the PCB design specifications.
- Copper Plating: Apply a series of chemical processes to metallize the walls of the drilled holes and create conductive vias that connect different layers of the PCB. This typically involves cleaning, surface activation, electroless copper deposition, and electroplating to build up the required thickness of copper.
- Circuit Patterning: Apply a layer of photoresist material over the surface of the PCB. Expose the photoresist to UV light through a photomask that defines the circuit pattern. Develop the exposed photoresist to remove the unwanted areas, leaving behind the desired conductive traces and pads.
- Etching: Use chemical etchants to selectively remove the exposed copper from the PCB surface, leaving the circuit pattern defined by the photoresist. Rinse and neutralize the PCB to stop the etching process and clean the surface.
- Surface Finish: Apply a surface finish to the exposed copper traces and pads to protect them from oxidation and ensure solderability during assembly. Common surface finishes for MW2000 Materials PCBs include immersion gold (ENIG), immersion silver, or OSP (Organic Solderability Preservatives).
- Quality Control: Throughout the manufacturing process, implement rigorous quality control measures to verify dimensional accuracy, layer alignment, copper thickness, and adherence to design specifications. Perform electrical testing to check impedance control, continuity of conductive paths, and other critical parameters.
- Final Inspection: Conduct a final inspection of the finished PCBs to ensure they meet customer requirements and industry standards for high-frequency performance and reliability. This includes visual inspection, electrical testing, and sometimes reliability testing under simulated operating conditions.
By following these steps, manufacturers can produce MW2000 Materials PCBs that meet the stringent requirements of high-frequency applications, providing excellent electrical performance, reliability, and durability in telecommunications, radar systems, and other advanced electronic devices.
How much should an MW2000 Materials PCB cost?
The cost of MW2000 Materials PCBs can vary significantly based on several factors including size, complexity, quantity, material specifications, and manufacturing processes involved. Here are some general factors that influence the cost:
- Material Cost: MW2000 Materials PCBs are typically made from high-performance substrates like PTFE (Polytetrafluoroethylene) or similar fluoropolymer materials, which are more expensive than standard FR4 materials due to their superior electrical properties.
- Layer Count and Complexity: The number of layers in the PCB, along with its complexity in terms of routing, impedance control requirements, and fine pitch components, can impact the cost. More layers and complex designs require more precise manufacturing processes.
- Surface Finish and Special Processes: The choice of surface finish (e.g., immersion gold, immersion silver) and any additional special processes (e.g., controlled impedance, blind/buried vias) will add to the overall cost.
- Quantity: Economies of scale apply in PCB manufacturing. Larger quantities typically reduce the cost per unit due to better utilization of manufacturing resources and bulk material purchasing.
- Turnaround Time: Expedited production schedules or quick-turn services may incur higher costs due to prioritized manufacturing and logistics.
- Quality and Certification Requirements: Compliance with specific quality standards (e.g., IPC standards) and certifications (e.g., ISO 9001) may impact the cost, as these require additional quality control measures and documentation.
Given these factors, it’s challenging to provide a precise cost without specific details about the PCB design, quantities required, and additional requirements. As a rough estimate, MW2000 Materials PCBs can range from tens to hundreds of dollars per square inch, depending on the complexity and specifications. For accurate pricing, it’s best to consult with PCB manufacturers who specialize in high-frequency materials and provide detailed quotations based on your specific requirements.
What is MW2000 Materials PCB base material?
MW2000 Materials PCBs are typically based on high-performance substrates that offer excellent electrical properties suitable for high-frequency applications. The base material for MW2000 Materials PCBs often includes:
- PTFE (Polytetrafluoroethylene): Also known by the brand name Teflon, PTFE-based materials are widely used for high-frequency PCBs due to their low dielectric constant (εr) and low dissipation factor (Df). These properties minimize signal loss and maintain signal integrity at high frequencies.
- Fluoropolymer-based Substrates: Besides pure PTFE, there are various fluoropolymer-based substrates available, such as materials in the Rogers RO4000 series. These substrates are engineered to provide stable electrical performance over a wide range of frequencies and temperatures.
- High-Frequency Laminate Materials: MW2000 Materials PCBs are composed of laminates that may include layers of PTFE or similar fluoropolymer materials with copper foils laminated to them. The choice of laminate materials depends on specific electrical and mechanical requirements of the PCB design.
These base materials are selected for their ability to offer low loss tangent, excellent dielectric constant control, and thermal stability, making them ideal for applications in telecommunications, radar systems, aerospace, and other high-frequency electronic devices where signal integrity is critical.
Which company makes MW2000 Materials PCBs?
MW2000 Materials PCBs are typically manufactured by specialized high-frequency PCB manufacturers equipped with advanced technology and equipment to meet stringent requirements for high-frequency applications. Some well-known manufacturers include Rogers Corporation in the United States and Panasonic Corporation in Japan. These companies have extensive experience and technological expertise in the high-frequency PCB field, offering a range of high-performance material options such as PTFE-based materials and other fluoropolymer substrates for producing MW2000 Materials PCBs.
As for our company, we are also capable of producing MW2000 Materials PCBs with the requisite technical capabilities and manufacturing facilities to meet customer demands. We specialize in the research and development as well as manufacturing of high-frequency PCBs, backed by advanced production lines and an experienced engineering team. Our manufacturing processes adhere strictly to international standards to ensure product quality and stability. We employ advanced materials and processes, including PTFE and other high-performance fluoropolymer-based materials, to ensure that MW2000 Materials PCBs exhibit excellent electrical performance and reliability in high-frequency environments.
Our company is committed to providing customized solutions tailored to meet specific customer requirements for MW2000 Materials PCBs. Whether in telecommunications, radar systems, aerospace, or other high-frequency applications, we deliver high-quality products and professional technical support. We prioritize effective communication and collaboration with our clients to ensure each project achieves optimal technical and commercial outcomes.
In summary, as a specialized high-frequency PCB manufacturer, our company is capable of producing MW2000 Materials PCBs and strives to deliver reliable solutions and continuous support through innovation and quality assurance.
What are the 7 qualities of good customer service for MW2000 Materials PCBs?
Good customer service for MW2000 Materials PCBs, or any product, typically involves several key qualities that enhance client satisfaction and build strong relationships. Here are seven qualities of good customer service specifically for MW2000 Materials PCBs:
- Expertise and Knowledge: Customer service representatives should have deep knowledge about MW2000 Materials PCBs, including their applications, specifications, and manufacturing processes. They should be able to provide accurate information and technical advice to assist customers effectively.
- Responsiveness: Timely responses to customer inquiries and requests are crucial. Whether through email, phone, or in-person interactions, promptness demonstrates commitment to customer needs and helps in resolving issues swiftly.
- Communication Skills: Clear and effective communication is essential. Customer service personnel should be able to explain technical details in a way that is understandable to customers, ensuring clarity in discussions about specifications, pricing, lead times, and any other relevant information.
- Problem-solving Ability: Ability to identify and resolve customer issues efficiently is key. Whether addressing technical queries, handling complaints, or coordinating solutions for production or delivery challenges, effective problem-solving enhances customer satisfaction.
- Reliability and Consistency: Consistently meeting commitments and delivering on promises fosters trust. This includes adhering to production schedules, providing accurate product information, and ensuring on-time delivery of MW2000 Materials PCBs.
- Customer Focus: Putting the customer’s needs first is fundamental. Understanding their requirements, preferences, and expectations helps in tailoring solutions that meet or exceed their expectations, leading to long-term satisfaction and loyalty.
- Follow-up and Support: Providing ongoing support after the sale is critical. This includes post-sales assistance, technical support, and addressing any issues or concerns that arise after the MW2000 Materials PCBs have been delivered. Regular follow-ups also demonstrate commitment to customer satisfaction.
By embodying these qualities, companies can enhance their customer service for MW2000 Materials PCBs, ensuring positive experiences that contribute to customer loyalty and business growth.
FAQs about MW2000 Materials PCBs
What are MW2000 Materials PCBs?
MW2000 Materials PCBs are high-frequency printed circuit boards designed for applications requiring excellent electrical performance at high frequencies. They are typically made from materials like PTFE (Polytetrafluoroethylene) or similar fluoropolymer substrates known for low dielectric constant and low loss tangent.
What are the key advantages of MW2000 Materials PCBs?
MW2000 Materials PCBs offer superior electrical properties such as low loss tangent and stable dielectric constant over a wide range of frequencies. This makes them ideal for high-frequency applications where signal integrity and minimal loss are critical.
What industries use MW2000 Materials PCBs?
MW2000 Materials PCBs are commonly used in telecommunications, radar systems, satellite communications, aerospace, and other high-frequency electronic devices. They are essential where reliable signal transmission and high-performance characteristics are required.
What are the typical applications of MW2000 Materials PCBs?
Applications include RF (Radio Frequency) communication systems, microwave circuits, antenna systems, radar systems, and high-speed data transmission equipment. They are chosen for their ability to maintain signal integrity and reduce interference at high frequencies.
How are MW2000 Materials PCBs manufactured?
MW2000 Materials PCBs are manufactured using specialized processes that involve selecting high-performance substrate materials, such as PTFE or fluoropolymer-based laminates. These substrates are laminated with copper foils, drilled, and etched to create the required circuit patterns and vias.
What are the factors to consider when designing MW2000 Materials PCBs?
Design considerations include impedance control, signal routing for minimal loss, thermal management, and the selection of appropriate surface finishes. These factors ensure the PCB meets performance requirements in high-frequency environments.
Where can I buy MW2000 Materials PCBs?
MW2000 Materials PCBs can be purchased from specialized PCB manufacturers and suppliers that offer high-frequency PCBs. Companies like Rogers Corporation and Panasonic Corporation are known for producing these materials and PCBs.