Multilayer Ceramic Substrates Manufacturer
Multilayer Ceramic Substrates Manufacturer,Multilayer Ceramic Substrates (MLCs) are advanced materials used extensively in electronics for their superior thermal, electrical, and mechanical properties. These substrates consist of multiple layers of ceramic material bonded together with conductive traces, forming a dense, integrated structure. MLCs offer excellent thermal management, low dielectric constant, and high reliability, making them ideal for high-frequency applications in telecommunications, radar systems, and automotive electronics. They provide precise control over signal routing and impedance matching, crucial for modern electronic designs requiring compact size and high performance. MLCs contribute significantly to the miniaturization and efficiency of electronic devices across various industries.
What are Multilayer Ceramic Substrates?
Multilayer Ceramic Substrates are circuit boards made from multiple layers of ceramic materials, widely used in electronic devices. Compared to traditional PCBs, these substrates offer higher thermal stability, corrosion resistance, and electrical insulation, making them suitable for operation in high-temperature and harsh environments.
These substrates are typically manufactured using Low Temperature Co-Fired Ceramic (LTCC) or High Temperature Co-Fired Ceramic (HTCC) technology. The LTCC process allows the substrate to be sintered at lower temperatures, enabling the embedding of circuits and components, reducing size, and improving performance. The HTCC process is suitable for applications requiring higher thermal endurance, such as automotive electronics and aerospace equipment.
The manufacturing process of multilayer ceramic substrates involves multiple layering, pressing, and sintering steps. Each layer can contain different conductive and insulating materials, providing design flexibility. Their high-frequency characteristics make them particularly important in RF and microwave circuits, supporting high-frequency signal transmission.
Additionally, multilayer ceramic substrates have excellent electromagnetic compatibility (EMC), effectively reducing electromagnetic interference (EMI), and enhancing the stability and reliability of devices. As a result, they are widely used in communication, medical, automotive, military, and aerospace fields. In summary, due to their superior performance and versatility, multilayer ceramic substrates have become an indispensable component in modern electronic devices.
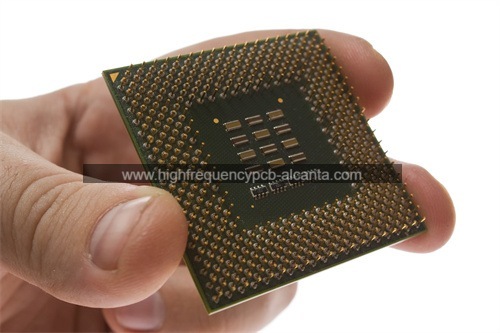
Multilayer Ceramic Substrates Manufacturer
What are the Multilayer Ceramic Substrates Design Guidelines?
Here are some key design guidelines for Multilayer Ceramic Substrates:
- Layer Configuration: Carefully plan the number and arrangement of layers to optimize electrical performance and thermal management. Ensure adequate spacing between conductive traces.
- Trace Width and Spacing: Define trace widths and spacing based on current-carrying capacity and impedance requirements. Use wider traces for higher currents and maintain consistent spacing to minimize crosstalk.
- Via Design: Use vias to connect different layers effectively. Consider blind or buried vias for compact designs, but ensure they meet the substrate’s thermal and electrical performance criteria.
- Material Selection: Choose appropriate ceramic materials based on application requirements, including thermal conductivity, dielectric constant, and thermal expansion coefficient.
- Thermal Management:Integrate thermal vias or heat sinks if necessary to dissipate heat from high-power components, ensuring reliable operation under varying temperatures.
- Component Placement: Strategically place components to minimize signal path lengths and avoid interference. Consider the mechanical stresses during the sintering process.
- Electromagnetic Shielding: Design for effective electromagnetic compatibility (EMC) by incorporating shielding layers where necessary, particularly in RF applications.
- Manufacturing Tolerances: Be aware of manufacturing tolerances for dimensions and alignment, and design features accordingly to ensure reliability and yield.
- Testing and Validation: Include test pads and access points for impedance and signal integrity testing. Plan for thorough validation to ensure performance meets specifications.
- Design Software: Utilize specialized design software for multilayer substrates to simulate electrical performance and optimize layout.
By following these guidelines, designers can enhance the performance, reliability, and manufacturability of multilayer ceramic substrates in various applications.
What is the Multilayer Ceramic Substrates Fabrication Process?
The fabrication process for Multilayer Ceramic Substrates typically involves several key steps:
- Material Preparation: Ceramic powders, such as alumina or other dielectric materials, are mixed with binders and additives to create a paste or slurry.
- Tape Casting: The prepared ceramic paste is spread into thin layers, known as green tapes, using a tape-casting process. This ensures uniform thickness and smooth surfaces.
- Layering: The green tapes are stacked together in the desired configuration, with conductive patterns (typically made from metal pastes) printed onto the layers where necessary.
- Punching Vias: Holes for vias are punched into the stacked layers to allow electrical connections between different layers.
- Lamination: The layered assembly is then laminated under heat and pressure to bond the layers together while maintaining alignment.
- Drying: The laminated assembly is dried to remove any residual moisture from the green tapes, preparing them for sintering.
- Sintering: The dried assembly is sintered in a controlled atmosphere furnace at high temperatures. This process densifies the ceramic material and hardens the structure, while also curing the conductive patterns.
- Trimming and Finishing: After sintering, the edges of the substrate are trimmed, and any additional features such as vias may be further processed. Surface finishing may include polishing or coating as needed.
- Testing and Inspection: The final product undergoes electrical testing and inspection to ensure it meets design specifications and quality standards.
- Packaging: Once tested, the multilayer ceramic substrates are packaged for shipment or integration into electronic devices.
This fabrication process allows for high precision and flexibility in designing multilayer ceramic substrates suitable for various high-performance applications.
How do you manufacture Multilayer Ceramic Substrates?
Manufacturing Multilayer Ceramic Substrates involves several detailed steps:
- Material Selection: Choose appropriate ceramic materials, such as alumina or other dielectric ceramics, based on the required electrical and thermal properties.
- Preparation of Ceramic Paste: Mix the ceramic powders with binders, plasticizers, and solvents to create a uniform paste or slurry suitable for tape casting.
- Tape Casting:Spread the ceramic paste onto a flat surface to form thin sheets (green tapes) using a controlled casting process. This ensures consistent thickness and surface quality.
- Printing Conductive Patterns: Use screen printing or other techniques to apply metal pastes (such as silver or copper) onto the green tapes where electrical connections are needed.
- Punching Vias: Punch holes into the green tapes to create vias that allow electrical connections between different layers.
- Layer Stacking:Carefully stack the printed green tapes in the desired configuration, ensuring proper alignment of the conductive patterns and vias.
- Lamination: Laminate the stacked assembly under heat and pressure to bond the layers together, ensuring that the vias are aligned for connectivity.
- Drying: Dry the laminated assembly to remove moisture, preparing it for the next step.
- Sintering: Sinter the dried assembly in a furnace at high temperatures, which densifies the ceramic material, bonds the layers, and cures the metal patterns.
- Trimming and Finishing: Trim the edges of the sintered substrate and perform any necessary finishing processes, such as surface polishing or additional coatings.
- Testing and Inspection: Conduct electrical and dimensional tests to verify that the substrates meet specified performance standards and quality requirements.
- Packaging:Package the finished multilayer ceramic substrates for delivery or integration into electronic devices.
This systematic approach ensures high precision, performance, and reliability in multilayer ceramic substrates used in advanced electronic applications.
How much should Multilayer Ceramic Substrates cost?
The cost of Multilayer Ceramic Substrates can vary widely based on several factors, including:
- Material Type: Different ceramic materials (e.g., alumina, zirconia) have varying costs.
- Complexity: The complexity of the design, including the number of layers, vias, and printed circuit patterns, can influence pricing.
- Size and Thickness: Larger and thicker substrates typically cost more due to increased material and processing time.
- Volume: Larger production runs often result in lower per-unit costs due to economies of scale.
- Manufacturing Process: The specific fabrication methods used (e.g., LTCC vs. HTCC) can also affect costs.
Generally, multilayer ceramic substrates can range from a few dollars to several hundred dollars per unit, depending on the factors mentioned. For precise pricing, it’s best to consult with manufacturers or suppliers directly, as they can provide quotes based on specific project requirements.
What is Multilayer Ceramic Substrates base material?
The base materials used for Multilayer Ceramic Substrates typically include:
- Alumina (Al₂O₃): This is the most commonly used ceramic material due to its excellent electrical insulation, thermal stability, and mechanical strength.
- Zirconia (ZrO₂): Known for its high toughness and thermal resistance, zirconia is used in applications requiring enhanced durability.
- Silicon Nitride (Si₃N₄): This material offers good thermal shock resistance and low thermal conductivity, making it suitable for high-performance applications.
- Other Dielectric Ceramics: Various formulations of ceramic materials can be used based on specific requirements, including tailored dielectric constants and thermal properties.
These materials are chosen based on their performance characteristics, including thermal conductivity, dielectric constant, and mechanical strength, which are crucial for the substrate’s functionality in electronic applications.
Which company makes Multilayer Ceramic Substrates?
Many companies specialize in manufacturing Multilayer Ceramic Substrates, including well-known manufacturers of electronic materials and components. These companies typically possess advanced production processes and technologies, enabling them to offer high-performance ceramic substrates to meet diverse application needs.
For example, companies like Kyocera, Murata, and NGK Insulators are leaders in the development and production of multilayer ceramic substrates. Kyocera is renowned for its high-quality ceramic materials and technologies, widely used in communications, automotive electronics, and medical devices. Murata focuses on the production of multilayer ceramic capacitors and other electronic components, committed to providing innovative solutions for customers. NGK Insulators has extensive experience in high-temperature ceramic substrates, particularly in aerospace and military applications.
In addition to these large companies, there are also several small to medium-sized enterprises that concentrate on specific markets, offering customized multilayer ceramic substrate solutions to meet particular customer needs.
Our company also manufactures multilayer ceramic substrates, equipped with advanced production equipment and mature process flows. Our manufacturing process includes precise ceramic material formulation, accurate lamination techniques, and high-temperature sintering processes, ensuring the high performance and reliability of the final products. We can provide ceramic substrates in various sizes, thicknesses, and layers according to specific customer requirements to suit a wide range of applications.
Throughout the production process, we emphasize material selection and process control to ensure that the ceramic substrates achieve optimal performance in electrical insulation, thermal stability, and mechanical strength. Our multilayer ceramic substrates find applications in communications, automotive, medical, industrial, and consumer electronics, helping customers achieve efficient designs and reliable product performance.
In summary, our company is dedicated to providing high-quality multilayer ceramic substrates to meet the needs of modern electronic devices. If you are interested in our products or have specific project requirements, please feel free to contact us, and we will be happy to provide you with solutions.
What are the 7 qualities of good customer service?
Good customer service is characterized by several key qualities, including:
- Responsiveness: Quick and timely responses to customer inquiries and issues demonstrate attentiveness and respect for their time.
- Empathy: Understanding and acknowledging customers’ feelings and perspectives helps build rapport and trust, making customers feel valued.
- Knowledgeability: Staff should possess in-depth knowledge about products or services to provide accurate information and effective solutions.
- Patience: Handling inquiries and complaints with patience, especially in challenging situations, ensures customers feel heard and respected.
- Clear Communication: Providing clear, concise, and jargon-free information helps customers understand the solutions offered and makes interactions smoother.
- Consistency: Delivering reliable and uniform service across all interactions creates a dependable experience, fostering customer loyalty.
- Follow-Up: Checking in with customers after resolving an issue shows commitment to their satisfaction and helps identify any further needs or concerns.
These qualities contribute to a positive customer experience, enhancing satisfaction and loyalty.
FAQs
What are Multilayer Ceramic Substrates?
Multilayer Ceramic Substrates are circuit boards made from multiple layers of ceramic materials, designed for high-performance applications in electronics.
What materials are used in Multilayer Ceramic Substrates?
Common materials include alumina, zirconia, and silicon nitride, chosen for their electrical insulation, thermal stability, and mechanical strength.
What are the advantages of using Multilayer Ceramic Substrates?
Advantages include excellent thermal conductivity, high dielectric strength, resistance to high temperatures, and reduced electromagnetic interference (EMI).
In what applications are these substrates used?
They are used in telecommunications, automotive electronics, aerospace, medical devices, and RF/microwave applications.
What is the manufacturing process for Multilayer Ceramic Substrates?
The process involves material preparation, tape casting, printing conductive patterns, stacking layers, lamination, drying, sintering, and finishing.
How are Multilayer Ceramic Substrates different from traditional PCBs?
They offer better thermal performance, higher reliability, and improved electrical characteristics compared to traditional printed circuit boards (PCBs).
What factors affect the cost of Multilayer Ceramic Substrates?
Costs are influenced by material type, substrate complexity, size, thickness, production volume, and specific manufacturing processes used.
Can Multilayer Ceramic Substrates be customized?
Yes, they can be customized in terms of size, layer configuration, and conductive patterns to meet specific application requirements.
What are the thermal properties of Multilayer Ceramic Substrates?
They typically have high thermal conductivity and can withstand extreme temperatures, making them suitable for high-power applications.