Multilayer Ceramic PCB Manufacturing
Multilayer Ceramic PCB Manufacturing,Multilayer Ceramic PCBs (Printed Circuit Boards) represent a pinnacle of electronic engineering, integrating layers of advanced ceramic material to achieve exceptional performance and reliability. Unlike traditional PCBs, Multilayer Ceramic PCBs utilize ceramic substrates, typically alumina (Al2O3) or aluminum nitride (AlN), renowned for their high thermal conductivity, electrical insulation, and mechanical stability.
These PCBs are meticulously engineered for demanding applications in aerospace, automotive, telecommunications, and military sectors, where reliability and performance are paramount. Their construction involves stacking and laminating multiple ceramic layers, intricately patterning conductive traces, and integrating vias for interconnectivity.
Multilayer Ceramic PCBs excel in high-frequency, high-power, and harsh environment conditions, offering superior thermal management, signal integrity, and resistance to temperature fluctuations and moisture. With their exceptional electrical properties and robust construction, Multilayer Ceramic PCBs provide a foundation for cutting-edge electronic devices that push the boundaries of innovation and reliability in modern technology.
What is a Multilayer Ceramic PCB?
A Multilayer Ceramic PCB (Printed Circuit Board) is a type of circuit board that incorporates layers of ceramic material instead of the traditional fiberglass epoxy substrate used in standard PCBs.
In a Multilayer Ceramic PCB, the layers of ceramic are laminated together with conductive traces to form a sandwich-like structure. These layers can range from just a few to dozens or more, depending on the complexity of the circuit design.
The main advantage of using ceramic as the substrate material is its excellent electrical properties, including high insulation resistance, low dielectric loss, and stability over a wide range of temperatures. This makes Multilayer Ceramic PCBs particularly suitable for applications requiring high reliability and performance in harsh environments, such as aerospace, automotive, and military electronics.
Additionally, Multilayer Ceramic PCBs can offer improved thermal management compared to traditional PCBs, as ceramic has much higher thermal conductivity than epoxy-based materials. This property allows for efficient heat dissipation, which is critical for many high-power electronic devices.
Overall, Multilayer Ceramic PCBs are chosen for their superior electrical performance, reliability, and thermal properties, especially in demanding applications where standard PCBs may not meet the requirements. However, they tend to be more expensive and have limitations in terms of design flexibility compared to traditional PCBs.
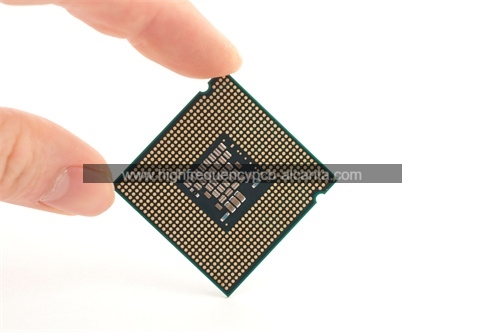
Multilayer Ceramic PCB Manufacturing
What are the Multilayer Ceramic PCB Design Guidelines?
Here are some general design guidelines for Multilayer Ceramic PCBs:
- Layer Stackup: Plan the layer stackup carefully, considering factors such as signal integrity, power distribution, and thermal management. Typically, the inner layers are used for power and ground planes, while signal traces are routed on outer layers.
- Signal Integrity:Minimize signal distortion by maintaining controlled impedance for high-speed signal traces. Ensure proper spacing between signal traces and ground planes to minimize crosstalk and interference.
- Thermal Management: Design the PCB to efficiently dissipate heat generated by components. Utilize thermal vias to transfer heat from components to inner layers or external heat sinks.
- Component Placement: Optimize component placement to minimize signal path lengths and reduce parasitic capacitance and inductance. Place critical components closer to each other and ensure adequate clearance from high-voltage components.
- Routing: Route traces carefully to avoid sharp corners and excessive bends, which can lead to signal degradation. Use wide traces for high-current paths and maintain proper clearance between traces to prevent short circuits.
- Grounding: Implement a solid ground plane to provide a low-impedance return path for signals and reduce electromagnetic interference. Use multiple vias to connect ground planes across different layers.
- Power Distribution: Ensure proper power distribution by using wide power traces and minimizing voltage drops. Distribute power evenly across the PCB to prevent localized heating and voltage fluctuations.
- Decoupling Capacitors: Place decoupling capacitors strategically near power pins of ICs to filter out noise and provide stable power supply voltages.
- Testing Points: Include test points for easy debugging and testing during the manufacturing and assembly process.
- Manufacturability: Consider manufacturability aspects such as minimum feature sizes, aspect ratios, and material limitations during the design phase to avoid issues during fabrication.
- Reliability: Design the PCB to withstand thermal cycling, mechanical stress, and other environmental factors to ensure long-term reliability.
- Compliance: Ensure compliance with relevant industry standards and regulations, such as IPC standards for PCB design and RoHS directives for materials and manufacturing processes.
By following these guidelines, designers can create Multilayer Ceramic PCBs that meet performance, reliability, and manufacturability requirements for various applications.
What is the Multilayer Ceramic PCB Fabrication Process?
The fabrication process for Multilayer Ceramic PCBs involves several steps, including layer preparation, material lamination, drilling, plating, etching, solder mask application, surface finish, and final inspection. This process requires precision and expertise to produce high-quality Multilayer Ceramic PCBs.
How do you manufacture a Multilayer Ceramic PCB?
Manufacturing a Multilayer Ceramic PCB involves several steps, which are generally more complex compared to traditional PCB manufacturing processes due to the use of ceramic materials. Here’s an overview of the typical manufacturing process:
- Design: The process starts with the design of the PCB using specialized CAD (Computer-Aided Design) software. Designers create the layout considering the specific requirements of the circuit and the characteristics of ceramic materials.
- Material Selection: Select the appropriate ceramic material for the PCB based on factors such as dielectric constant, thermal conductivity, and mechanical strength. Common ceramic materials used include alumina (Al2O3) and aluminum nitride (AlN).
- Layer Preparation: Cut the ceramic sheets to the required dimensions for the PCB layers. These layers may be green (unfired) or pre-fired, depending on the specific manufacturing process.
- Screen Printing: Apply conductive paste containing metals such as silver or gold onto the ceramic layers using screen printing or other deposition techniques. These conductive patterns form the traces and pads for component attachment.
- Layer Stacking: Assemble the ceramic layers along with any additional layers such as dielectric or metal layers into a stack, aligning the conductive traces between layers to form the desired circuit configuration.
- Lamination: Subject the layered stack to high pressure and temperature in a lamination process to bond the layers together. This process typically involves sintering the ceramic layers to achieve strong adhesion and electrical continuity.
- Via Formation: Drill holes or laser ablate vias through the stacked layers to provide electrical connections between different layers. These vias are filled with conductive material to establish interlayer connections.
- Surface Finishing: Apply surface finishes such as gold plating or solder mask to protect the exposed conductive traces and pads and facilitate soldering during component assembly.
- Component Assembly: Mount electronic components onto the PCB using surface mount technology (SMT) or through-hole technology (THT), depending on the design requirements and component sizes.
- Testing: Perform electrical testing and inspection to ensure that the manufactured PCB meets the specified performance criteria and quality standards.
- Final Inspection and Packaging: Conduct a final inspection of the assembled PCBs to verify functionality and quality before packaging and shipping to customers.
The manufacturing process for Multilayer Ceramic PCBs requires specialized equipment and expertise due to the unique properties of ceramic materials and the complexity of the layering and bonding processes involved.
How much should a Multilayer Ceramic PCB cost?
The cost of a Multilayer Ceramic PCB can vary significantly depending on several factors, including the following:
- Number of Layers: The more layers the PCB has, the higher the cost typically is due to increased material and manufacturing complexity.
- Size and Thickness: Larger and thicker PCBs require more material and may involve additional processing steps, leading to higher costs.
- Material Type: The choice of ceramic material can impact the cost. Some materials, such as alumina (Al2O3) and aluminum nitride (AlN), may be more expensive than others.
- Complexity of Design: PCBs with intricate designs, dense routing, and advanced features such as controlled impedance or blind/buried vias will generally cost more to manufacture.
- Quantity: Economies of scale apply, so larger production runs typically result in lower per-unit costs.
- Manufacturing Technology:The specific manufacturing processes and technologies used can influence the cost. For example, laser drilling for vias or high-precision alignment processes may increase costs.
- Surface Finishes and Additional Features: Certain surface finishes, such as gold plating, and additional features like impedance matching or specialized testing requirements can add to the cost.
- Supplier and Location: The pricing policies of PCB manufacturers and their geographical location can also affect the overall cost.
As a rough estimate, Multilayer Ceramic PCBs can range from several dollars to hundreds of dollars per square inch, depending on the factors mentioned above. For precise pricing, it’s best to consult with PCB manufacturers and provide detailed specifications of your design for a quotation.
What is Multilayer Ceramic PCB base material?
The base material used in Multilayer Ceramic PCBs is primarily ceramic. Specifically, alumina (Al2O3) and aluminum nitride (AlN) are two common types of ceramic materials used in Multilayer Ceramic PCBs. These ceramics offer excellent electrical properties, high thermal conductivity, and mechanical stability, making them suitable for demanding electronic applications.
Alumina (Al2O3) is widely used in Multilayer Ceramic PCBs due to its high dielectric strength, thermal conductivity, and chemical resistance. It is suitable for applications requiring high reliability and stability over a wide temperature range.
Aluminum nitride (AlN) is another ceramic material increasingly used in Multilayer Ceramic PCBs, particularly in high-power and high-frequency applications. AlN offers even higher thermal conductivity than alumina, making it ideal for applications requiring efficient heat dissipation.
Both alumina and aluminum nitride can be fabricated into thin sheets or tapes, which are then processed to create the layers of the Multilayer Ceramic PCB. These ceramic layers are stacked together with conductive traces and vias to form the complete PCB structure.
Which company makes Multilayer Ceramic PCB?
Several companies specialize in producing Multilayer Ceramic PCBs (Printed Circuit Boards), including Murata Manufacturing Co., Ltd., Kyocera Corporation, and NGK Insulators, Ltd. These companies have extensive reputations and experience in the electronics industry, offering various types and specifications of Multilayer Ceramic PCBs to meet the needs of different application fields.
As a company dedicated to electronics manufacturing, our company is also capable of producing Multilayer Ceramic PCBs. We have advanced manufacturing equipment and technology, as well as an experienced engineering team, capable of designing and producing high-quality Multilayer Ceramic PCBs that meet customer requirements.
Our production process follows strict quality control standards to ensure that each Multilayer Ceramic PCB has stable performance and reliability. We can customize the number of layers, dimensions, materials, surface treatments, and other characteristics of the PCB according to customer requirements, providing complete technical support and after-sales service.
Whether customers need Multilayer Ceramic PCBs for aerospace, automotive electronics, medical devices, or communication applications, we can provide them with tailored solutions. We are committed to establishing long-term partnerships with customers, delivering high-quality, high-performance electronic product solutions, and achieving mutual success.
What are the 7 qualities of good customer service?
Good customer service is essential for businesses to maintain customer satisfaction and loyalty. Seven qualities of good customer service include:
- Responsiveness: Respond promptly to customer inquiries, concerns, and requests. Customers appreciate timely assistance and solutions to their problems.
- Empathy: Show empathy and understanding towards customers’ needs and concerns. Listening attentively and demonstrating empathy helps build rapport and trust with customers.
- Reliability: Deliver on promises and commitments made to customers. Consistency and reliability in service delivery build confidence and loyalty among customers.
- Professionalism: Conduct interactions with customers in a professional manner. This includes being courteous, respectful, and knowledgeable about products or services.
- Effective Communication: Communicate clearly and effectively with customers, both verbally and in writing. Provide information in a manner that is easy to understand and address any questions or concerns promptly.
- Problem-solving Skills: Demonstrate strong problem-solving skills to resolve customer issues and complaints effectively. Take ownership of problems and work towards finding satisfactory solutions for customers.
- Personalization: Tailor the service experience to meet the individual needs and preferences of each customer. Personalizing interactions shows customers that their business is valued and enhances their overall experience.
By embodying these qualities, businesses can create positive interactions with customers, foster loyalty, and build a reputation for excellent customer service.
FAQs (Frequently Asked Questions)
What is a Multilayer Ceramic PCB?
A Multilayer Ceramic PCB is a type of printed circuit board that utilizes layers of ceramic material instead of the traditional fiberglass epoxy substrate. It offers superior electrical properties, thermal conductivity, and reliability compared to standard PCBs.
What are the advantages of Multilayer Ceramic PCBs?
Multilayer Ceramic PCBs offer excellent electrical insulation, high thermal conductivity, stability over a wide temperature range, and resistance to harsh environments. They are ideal for applications requiring high reliability and performance.
What are the common applications of Multilayer Ceramic PCBs?
Multilayer Ceramic PCBs are used in a variety of industries, including aerospace, automotive, military, telecommunications, and medical devices. They are suitable for high-power, high-frequency, and harsh environment applications.
How are Multilayer Ceramic PCBs manufactured?
The manufacturing process involves cutting ceramic sheets to size, applying conductive traces and vias using screen printing or deposition techniques, stacking and laminating the layers together, drilling or laser ablation for vias, surface finishing, component assembly, and testing.
What are the key considerations for designing Multilayer Ceramic PCBs?
Design considerations include layer stackup, signal integrity, thermal management, component placement, routing, grounding, power distribution, decoupling capacitors, testing points, manufacturability, and compliance with industry standards.
What factors affect the cost of Multilayer Ceramic PCBs?
The cost varies depending on factors such as the number of layers, size and thickness, material type, complexity of design, quantity, manufacturing technology, surface finishes, additional features, and supplier.
Where can I purchase Multilayer Ceramic PCBs?
Multilayer Ceramic PCBs can be purchased from specialized PCB manufacturers or suppliers that offer custom fabrication services. It’s important to choose a reputable supplier with experience in producing high-quality Multilayer Ceramic PCBs.