Multi Cavity Substrates Manufacturing
What are Multi Cavity Substrates?
Multi-cavity substrates are specialized substrates used in electronics packaging and semiconductor manufacturing. These substrates feature multiple individual cavities or compartments designed to house electronic components such as integrated circuits (ICs), sensors, microelectromechanical systems (MEMS), or other miniaturized devices.
The purpose of multi-cavity substrates is to enable compact and efficient integration of multiple electronic components within a single package. This approach offers several advantages:
- Space Efficiency: By incorporating multiple cavities within a single substrate, multi-cavity substrates help conserve space in electronic assemblies. This is particularly useful in applications where miniaturization is critical, such as mobile devices, wearables, and IoT devices.
- Improved Thermal Management: Multi-cavity substrates may incorporate features such as thermal vias or metal layers for enhanced heat dissipation. Efficient thermal management is crucial for maintaining the reliability and performance of electronic components, especially in high-power applications.
- Reduced Interconnect Lengths: By housing multiple components within close proximity, multi-cavity substrates minimize the lengths of interconnects, which can help reduce parasitic capacitance, inductance, and resistance. This can lead to improved signal integrity and overall performance of the electronic system.
- Enhanced Integration: Multi-cavity substrates facilitate the integration of heterogeneous components, allowing designers to combine different types of devices within a single package. This versatility enables the development of complex electronic systems with diverse functionality.
- Streamlined Manufacturing: Integrating multiple components into a single substrate simplifies the manufacturing process by reducing the number of individual parts and assembly steps required. This can lead to cost savings and improved production efficiency.
Multi-cavity substrates are commonly used in various applications, including microelectronics, RF and microwave systems, automotive electronics, medical devices, aerospace systems, and telecommunications equipment. They are typically fabricated using advanced semiconductor manufacturing techniques such as thin-film deposition, photolithography, and etching processes.
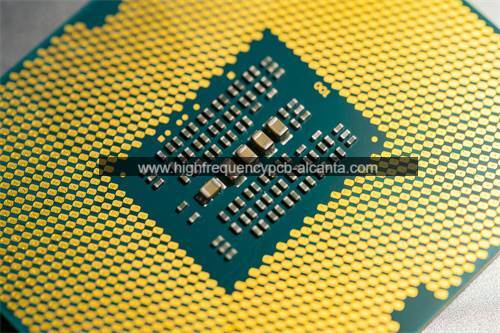
Multi Cavity Substrates Manufacturing
What are the Multi Cavity Substrates Design Guidelines?
Designing multi-cavity substrates requires careful consideration of various factors to ensure optimal performance, reliability, and manufacturability. Here are some general design guidelines for multi-cavity substrates:
- Cavity Layout and Dimension: Determine the layout and dimensions of each cavity based on the size and shape of the components to be housed within them. Ensure adequate spacing between cavities to prevent interference and facilitate assembly.
- Material Selection: Choose substrate materials with appropriate electrical, thermal, and mechanical properties to meet the requirements of the application. Consider factors such as dielectric constant, thermal conductivity, coefficient of thermal expansion (CTE), and mechanical strength.
- Thermal Management: Incorporate features such as thermal vias, metal layers, or heat spreaders to enhance thermal dissipation within the substrate. Ensure efficient heat transfer from hot spots to heat sinks or external cooling systems to prevent overheating and thermal stress.
- Signal Integrity: Minimize signal interference and crosstalk between cavities by optimizing the layout of signal traces, ground planes, and power distribution networks. Use shielding techniques and isolation measures as needed to maintain signal integrity.
- Electromagnetic Compatibility (EMC): Design the substrate to minimize electromagnetic interference (EMI) emissions and susceptibility. Utilize proper grounding and shielding techniques, and comply with EMC standards and regulations applicable to the intended application.
- Manufacturability: Design for ease of manufacturing and assembly by considering factors such as substrate material compatibility with fabrication processes, alignment accuracy of features, and accessibility for testing and inspection.
- Reliability: Enhance substrate reliability by minimizing stress concentrations, avoiding sharp corners or abrupt transitions, and ensuring sufficient margin for thermal expansion and contraction during operation.
- Package Integration: Coordinate the design of the multi-cavity substrate with the overall package design, including compatibility with external interfaces, connectors, and assembly methods. Ensure proper alignment and compatibility with mating components.
- Cost Considerations: Balance design requirements with cost constraints by optimizing material usage, manufacturing processes, and complexity of features. Consider trade-offs between performance, reliability, and cost to achieve the desired balance.
- Simulation and Prototyping: Validate the design through computer-aided design (CAD) simulations, finite element analysis (FEA), and prototyping to assess performance, reliability, and manufacturability before mass production.
By following these design guidelines, engineers can develop multi-cavity substrates that meet the specific requirements of their applications while ensuring robust performance, reliability, and manufacturability.
What is the Multi Cavity Substrates Fabrication Process?
The fabrication process for multi-cavity substrates involves several steps, including substrate material preparation, patterning, etching, metallization, assembly, and testing. Below is an overview of the typical fabrication process for multi-cavity substrates:
- Substrate Material Selection: Choose a substrate material with suitable properties such as electrical insulation, thermal conductivity, mechanical strength, and compatibility with fabrication processes. Common substrate materials include ceramics (e.g., alumina or aluminum nitride) and organic substrates (e.g., FR-4 or polyimide).
- Substrate Preparation: Prepare the substrate material by cleaning and planarizing its surface to ensure uniformity and cleanliness. This step is crucial for achieving proper adhesion and patterning of subsequent layers.
- Patterning: Use photolithography or other patterning techniques to define the layout of the cavities, signal traces, vias, and other features on the substrate surface. A photoresist layer is applied and exposed to UV light through a mask, followed by development to remove the exposed areas and reveal the desired pattern.
- Etching: Etch away the exposed areas of the substrate using wet or dry etching processes, depending on the material and desired features. Etching selectively removes material to create the cavities and features defined in the patterned photoresist layer.
- Metallization: Deposit metal layers onto the substrate surface to form conductive traces, bond pads, and vias. Techniques such as physical vapor deposition (PVD) or sputtering are commonly used to deposit metal films with precise thickness and conductivity.
- Dielectric Layer Deposition: Apply dielectric layers (e.g., silicon dioxide or polyimide) over the metallized substrate to insulate and protect the conductive traces and components. These dielectric layers may also serve as planarization layers to smoothen the surface for subsequent processing steps.
- Additional Processing: Depending on the design requirements, additional processing steps such as surface finishing, laser drilling, or laser ablation may be performed to fine-tune the substrate’s properties and features.
- Assembly: Assemble electronic components, such as integrated circuits (ICs), sensors, or MEMS devices, into the cavities of the substrate using die attach and wire bonding or flip-chip bonding techniques. Encapsulate the components with a protective material (e.g., epoxy resin) if necessary.
- Testing and Quality Assurance: Conduct electrical, thermal, and mechanical testing to ensure the functionality, reliability, and performance of the fabricated multi-cavity substrates. Quality assurance measures may include visual inspection, electrical continuity testing, thermal cycling, and environmental testing.
- Packaging and Final Inspection: Package the multi-cavity substrates into their final form, such as trays or tape-and-reel packaging, suitable for handling and integration into electronic systems. Perform final inspection and quality control checks before shipping the substrates to customers or assembly facilities.
Throughout the fabrication process, stringent process controls and quality assurance measures are implemented to ensure consistency, accuracy, and reliability of the multi-cavity substrates. Collaboration between design engineers, process engineers, and manufacturing personnel is essential to optimize the fabrication process and meet the specific requirements of each application.
How do you manufacture Multi Cavity Substrates?
Manufacturing multi-cavity substrates involves a series of steps that require precision equipment, specialized materials, and expertise in semiconductor manufacturing processes. Here is a detailed outline of the typical manufacturing process:
- Substrate Material Selection: Choose a suitable substrate material based on the application requirements, considering factors such as electrical properties, thermal conductivity, mechanical strength, and compatibility with fabrication processes. Common substrate materials include ceramics (e.g., alumina, aluminum nitride) and organic substrates (e.g., FR-4, polyimide).
- Substrate Preparation:
– Clean the substrate surface to remove contaminants and ensure proper adhesion of subsequent layers.
– Planarize the substrate surface if necessary to achieve uniformity and smoothness.
- Patterning:
– Apply a photoresist layer onto the substrate surface.
– Use photolithography or other patterning techniques to define the layout of cavities, traces, vias, and other features.
– Expose the photoresist layer to UV light through a mask to transfer the desired pattern.
– Develop the photoresist to remove the unexposed areas and reveal the patterned features on the substrate surface.
- Etching:
– Etch away the exposed areas of the substrate using wet or dry etching processes, depending on the substrate material and desired features.
– Etching selectively removes material to create the cavities and features defined in the patterned photoresist layer.
- Metallization:
– Deposit metal layers onto the substrate surface to form conductive traces, bond pads, and vias.
– Use techniques such as physical vapor deposition (PVD), sputtering, or electroplating to deposit metal films with precise thickness and conductivity.
- Dielectric Layer Deposition:
– Apply dielectric layers (e.g., silicon dioxide, polyimide) over the metallized substrate to insulate and protect the conductive traces and components.
– These dielectric layers may also serve as planarization layers to smoothen the surface for subsequent processing steps.
- Additional Processing:
– Perform additional processing steps as needed, such as surface finishing, laser drilling, or laser ablation to fine-tune the substrate’s properties and features.
- Assembly:
– Place electronic components (e.g., ICs, sensors, MEMS devices) into the cavities of the substrate using die attach and wire bonding or flip-chip bonding techniques.
– Encapsulate the components with a protective material (e.g., epoxy resin) if necessary.
- Testing and Quality Assurance:
– Conduct electrical, thermal, and mechanical testing to ensure the functionality, reliability, and performance of the fabricated multi-cavity substrates.
– Perform visual inspection, electrical continuity testing, thermal cycling, and environmental testing as part of quality assurance measures.
- Packaging and Final Inspection:
– Package the multi-cavity substrates into their final form, such as trays or tape-and-reel packaging, suitable for handling and integration into electronic systems.
– Perform final inspection and quality control checks before shipping the substrates to customers or assembly facilities.
Throughout the manufacturing process, strict process controls and quality assurance measures are implemented to ensure consistency, accuracy, and reliability of the multi-cavity substrates. Collaboration between design engineers, process engineers, and manufacturing personnel is essential to optimize the manufacturing process and meet the specific requirements of each application.
How much should Multi Cavity Substrates cost?
The cost of multi-cavity substrates can vary widely depending on several factors, including the substrate material, complexity of design, manufacturing processes, volume of production, and additional features required. Here are some considerations that influence the cost:
- Substrate Material: Different substrate materials have varying costs. For example, ceramic substrates like alumina or aluminum nitride tend to be more expensive than organic substrates like FR-4 or polyimide.
- Design Complexity: The complexity of the substrate design, including the number and size of cavities, the density of features, and the precision required for manufacturing, can impact the cost. More intricate designs may require specialized equipment and processes, which can increase manufacturing expenses.
- Manufacturing Processes: The choice of manufacturing processes, such as photolithography, etching, metallization, and assembly techniques, can affect costs. Some processes may be more time-consuming or require expensive equipment, contributing to higher manufacturing costs.
- Volume of Production: Economies of scale play a significant role in determining the cost of multi-cavity substrates. Higher volumes typically lead to lower unit costs due to efficiencies in production, materials procurement, and overhead expenses.
- Additional Features: Additional features such as thermal management solutions, advanced packaging techniques, or customization options may add to the overall cost of the substrates.
- Supplier and Location: The choice of supplier and their location can influence costs due to differences in labor rates, overhead expenses, and supply chain logistics.
- Quality and Reliability Requirements: Meeting stringent quality and reliability standards may entail additional testing, inspection, and quality control measures, which can impact the overall cost of the substrates.
Given these factors, it is challenging to provide a precise cost estimate for multi-cavity substrates without specific details about the project requirements. Typically, it’s recommended to consult with substrate manufacturers or suppliers to obtain customized quotes based on your exact specifications and volume needs. Additionally, conducting a thorough cost analysis considering all relevant factors is essential to ensure the competitiveness and cost-effectiveness of the final product.
What is the Multi Cavity Substrates Base Material?
The base material for multi-cavity substrates can vary depending on the specific requirements of the application and the desired properties of the substrate. Common materials used for multi-cavity substrates include:
- Ceramics:
– Alumina (Al2O3): Alumina substrates offer excellent electrical insulation, high thermal conductivity, and mechanical strength. They are commonly used in applications requiring high power dissipation and reliability, such as power electronics and RF/microwave circuits.
– Aluminum Nitride (AlN): Aluminum nitride substrates exhibit high thermal conductivity, low coefficient of thermal expansion (CTE), and good dielectric properties. They are suitable for applications requiring efficient heat dissipation, such as high-frequency RF and power semiconductor devices.
- Organic Substrates:
– FR-4 (Flame Retardant 4): FR-4 is a widely used epoxy-based laminate material reinforced with woven fiberglass. It offers good electrical insulation, mechanical strength, and cost-effectiveness, making it suitable for various consumer electronics and general-purpose applications.
– Polyimide: Polyimide substrates provide excellent thermal stability, flexibility, and resistance to chemicals and radiation. They are commonly used in applications requiring high-temperature operation, such as aerospace, automotive, and medical devices.
- Other Materials:
– Copper: Copper substrates, often used in the form of metal-core printed circuit boards (MCPCBs), offer high thermal conductivity and are ideal for applications requiring efficient heat dissipation, such as LED lighting and power electronics.
– Silicon: Silicon substrates are used in MEMS (Microelectromechanical Systems) applications due to their compatibility with semiconductor fabrication processes and integrated circuitry.
The choice of base material depends on factors such as electrical properties, thermal conductivity, mechanical strength, dimensional stability, cost, and compatibility with manufacturing processes. Designers typically select the substrate material that best suits the specific requirements of their application while considering factors such as power dissipation, signal integrity, reliability, and cost-effectiveness.
Which companies manufacture Multi Cavity Substrates?
Manufacturing multi-cavity substrates is a complex process that requires specialized equipment, technology, and experience. Currently, many well-known semiconductor manufacturers and electronic packaging companies offer production services for multi-cavity substrates. These companies include Delta Electronics from Taiwan, Murata Manufacturing Co., Ltd. from Japan, Samsung Electronics from South Korea, Micron Technology from the United States, and Omron Electronics from Germany. These companies have advanced manufacturing equipment and processes, as well as extensive experience and technical knowledge, enabling them to meet the needs of various application fields.
Our company is also a professional manufacturer of multi-cavity substrates. We have advanced production equipment and a skilled technical team capable of providing high-quality, customized solutions for multi-cavity substrates. Our manufacturing process strictly follows international standards to ensure product quality and stability. We value communication and collaboration with customers, tailoring multi-cavity substrate designs to meet their specific requirements and providing professional technical support and after-sales service. We are committed to delivering the highest quality products and services to our customers, achieving win-win cooperation, and mutual development together.
What are the 7 qualities of good customer service?
Good customer service is essential for building positive relationships with customers and fostering loyalty to a business. Here are seven qualities of good customer service:
- Responsiveness: Good customer service involves being prompt and responsive to customer inquiries, requests, and concerns. Customers appreciate receiving timely assistance and solutions to their problems, whether it’s through phone, email, live chat, or in-person interactions.
- Empathy: Empathy is the ability to understand and empathize with customers’ perspectives, feelings, and needs. Good customer service representatives listen actively, show genuine concern, and strive to address customers’ issues with compassion and understanding.
- Clear Communication: Effective communication is essential for providing good customer service. Clear, concise, and courteous communication helps avoid misunderstandings, ensures customers understand the information provided, and fosters a positive interaction experience.
- Problem-Solving Skills: Good customer service involves having strong problem-solving skills to address customers’ concerns and resolve issues effectively. Customer service representatives should be resourceful, proactive, and empowered to find solutions that meet customers’ needs and expectations.
- Professionalism: Professionalism encompasses displaying courtesy, respect, and professionalism in all customer interactions. Good customer service representatives maintain a positive attitude, remain calm under pressure, and uphold company values and policies while assisting customers.
- Consistency: Consistency is key to delivering good customer service across all touchpoints and interactions. Customers expect consistent levels of service quality, responsiveness, and reliability, regardless of the channel or department they engage with.
- Follow-Up and Feedback: Good customer service involves following up with customers to ensure their issues are resolved satisfactorily and to gather feedback on their experience. Proactively seeking feedback helps identify areas for improvement and demonstrates a commitment to continuous improvement and customer satisfaction.
By embodying these qualities, businesses can provide exceptional customer service that enhances customer satisfaction, loyalty, and advocacy, ultimately contributing to long-term success and growth.
FAQs (Frequently Asked Questions)
What is an embedded slot PCB?
An embedded slot PCB refers to a printed circuit board (PCB) that contains embedded slots or channels within its design. These slots are used for specific purposes such as accommodating connectors, components, or other structures within the PCB itself.
What are the advantages of embedded slot PCBs?
Embedded slot PCBs offer several advantages including space optimization, improved signal integrity, enhanced cooling, and better component integration.
What are the design considerations for embedded slot PCBs?
Design considerations for embedded slot PCBs include determining the position and size of slots, ensuring signal integrity, managing thermal issues, considering manufacturability, ensuring mechanical stability, and planning for testing and maintenance.
What materials are used in embedded slot PCBs?
The base material for embedded slot PCBs is typically a laminate composed of fiberglass reinforced with epoxy resin (FR-4). However, alternative materials may be used for specialized applications.
How are embedded slot PCBs manufactured?
The manufacturing process for embedded slot PCBs involves steps such as design, material selection, lamination, drilling, embedding slots, copper plating, circuit patterning, surface finishing, component assembly, soldering, testing, and final inspection.
What are some common applications of embedded slot PCBs?
Embedded slot PCBs are used in a variety of applications across industries such as electronics, telecommunications, automotive, aerospace, medical devices, and industrial automation.
What factors affect the cost of embedded slot PCBs?
The cost of embedded slot PCBs depends on factors such as design complexity, number of layers, materials used, quantity ordered, manufacturing processes involved, and additional services required.
Which companies manufacture embedded slot PCBs?
Many PCB manufacturing companies produce embedded slot PCBs, including well-known names like Foxconn, TSMC, Hitachi Chemical, Pegatron, and Unimicron, among others.