Multi Cavity PCB Manufacturing
Multi Cavity PCB Manufacturing,Multi-cavity PCBs, or multi-cavity printed circuit boards, are specialized circuit boards designed to accommodate multiple independent circuits within a single board structure. These PCBs feature multiple cavities, or enclosed areas, where individual circuits can be isolated and integrated. Each cavity typically contains its own set of components and circuitry, allowing for complex electronic systems to be consolidated into a compact form factor.
Multi-cavity PCBs are commonly used in various electronic applications where space is limited, and multiple circuits need to be interconnected while maintaining isolation. They offer benefits such as reduced size and weight, simplified assembly processes, and improved signal integrity by minimizing signal crosstalk and interference.
The design and fabrication of multi-cavity PCBs require careful consideration of factors such as cavity layout, signal routing, thermal management, and manufacturing feasibility. Advanced design software and manufacturing techniques are often employed to ensure the reliability, performance, and manufacturability of these complex circuit boards. Overall, multi-cavity PCBs provide a versatile solution for integrating multiple circuits into a single, efficient electronic system.
What is a Multi-cavity PCB?
A Multi-cavity PCB (Printed Circuit Board) is a type of PCB design where multiple individual circuit cavities are incorporated into a single board. Each cavity typically contains its own set of components and circuits, which are isolated from each other on the board. These cavities may be interconnected through traces or vias on the board, allowing for communication or interaction between the different circuits.
Multi-cavity PCBs are commonly used in applications where space is limited, and multiple independent circuits need to be integrated into a single board. This design approach helps to reduce the overall size of the electronic system while maintaining functionality. It’s often employed in complex electronic devices such as smartphones, tablets, IoT devices, and various other consumer electronics where miniaturization is crucial.
Designing multi-cavity PCBs requires careful planning to ensure that each cavity is properly isolated to prevent interference between circuits. It also involves consideration of signal integrity, power distribution, thermal management, and manufacturability factors to ensure the reliable operation of the final product.
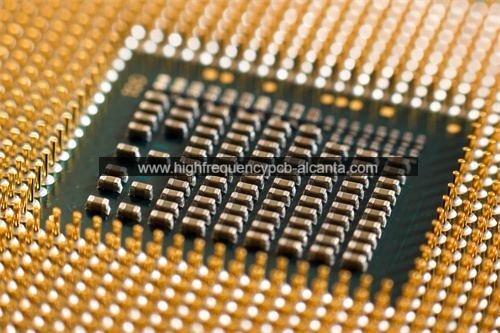
Multi Cavity PCB Manufacturing
What are the Multi-cavity PCB Design Guidelines?
Here are some general design guidelines for multi-cavity PCBs:
- Isolation: Ensure proper isolation between cavities to prevent crosstalk or interference between different circuits. Use adequate spacing, ground planes, and shielding techniques as needed.
- Signal Integrity: Maintain signal integrity by carefully routing high-speed signals and minimizing signal degradation. Pay attention to impedance matching, signal length matching, and avoiding signal reflections.
- Power Distribution: Design an efficient power distribution network to ensure stable and clean power supply to all circuits. Use proper decoupling capacitors, power planes, and routing techniques to minimize voltage drops and noise.
- Thermal Management: Consider thermal management strategies to dissipate heat generated by components within each cavity. Use thermal vias, heat sinks, and proper PCB layout techniques to ensure adequate heat dissipation and prevent overheating.
- Component Placement: Optimize component placement within each cavity to minimize signal path lengths, reduce parasitic effects, and improve overall performance. Consider the thermal impact of component placement on neighboring circuits.
- Manufacturability: Design the PCB layout with manufacturability in mind. Follow industry-standard design rules, maintain proper clearances, and consider the capabilities of your chosen fabrication and assembly processes.
- Testing and Debugging: Include test points, probe access points, and other features to facilitate testing and debugging of the PCB during development and production stages.
- Documentation: Provide comprehensive documentation including schematics, layout files, assembly drawings, and BOM (Bill of Materials) to ensure smooth manufacturing and assembly processes.
- EMC Compliance: Design the PCB layout to meet electromagnetic compatibility (EMC) requirements. Minimize electromagnetic interference (EMI) emissions and susceptibility by following EMC guidelines and standards.
- Flexibility and Scalability: Design the PCB layout to be flexible and scalable, allowing for future modifications, upgrades, or customization of individual cavities without major redesigns.
By following these guidelines, you can ensure the successful design and implementation of multi-cavity PCBs for various electronic applications.
What is the Multi-cavity PCB Fabrication Process?
The fabrication process for multi-cavity PCBs generally follows these steps:
- Design Preparation: Prepare the PCB design layout using PCB design software. This involves creating multiple cavities, placing components, routing traces, and ensuring proper isolation between cavities.
- Gerber File Generation: Generate Gerber files, which contain the necessary information for manufacturing each layer of the PCB, including copper traces, solder mask, and silkscreen layers.
- Material Selection: Choose the appropriate substrate material for the PCB based on factors such as electrical properties, thermal conductivity, and cost. Multi-cavity PCBs often use materials like FR-4, which is a common choice for its balance of performance and affordability.
- Layer Stackup Design: Determine the layer stackup configuration based on the number of cavities, signal requirements, and thermal considerations. The layer stackup defines the arrangement of copper layers, insulating layers, and any additional features such as power or ground planes.
- Inner Layer Processing: Begin the fabrication process by preparing the inner layers of the PCB stackup. This involves cleaning, etching, and laminating copper foil onto the substrate material to create the conductive traces and planes.
- Drilling: Drill holes for vias, component mounting, and interconnections between layers. High-precision drilling equipment is used to create holes with tight tolerances to ensure accurate alignment between layers.
- Through-hole Plating: Coat the drilled holes with a conductive material, typically copper, to establish electrical connections between different layers of the PCB. This process is called through-hole plating or electroplating.
- Outer Layer Processing: Process the outer layers of the PCB stackup by laminating copper foil, applying solder mask to define solderable areas, and adding a silkscreen layer for component labeling and identification.
- Etching and Imaging: Use a photoresist process to define the circuit traces and features on the outer layers of the PCB. Expose the photoresist to UV light through a photomask, develop it to remove unwanted areas, and then etch away the exposed copper to reveal the desired circuit pattern.
- Surface Finish: Apply a surface finish to protect exposed copper surfaces, facilitate soldering, and enhance the overall reliability of the PCB. Common surface finishes include HASL (Hot Air Solder Leveling), ENIG (Electroless Nickel Immersion Gold), and OSP (Organic Solderability Preservatives).
- Testing: Perform electrical testing to verify the integrity and functionality of the fabricated PCB. This may involve continuity testing, impedance testing, and other electrical measurements to ensure that the PCB meets design specifications.
- Final Inspection and Packaging: Inspect the fabricated PCB for any defects or imperfections and perform any necessary rework or repairs. Once validated, the PCBs are packaged and prepared for shipment to the assembly facility or end-user.
Throughout the fabrication process, strict quality control measures are implemented to ensure the reliability and performance of the final multi-cavity PCBs. Collaboration between design engineers and fabrication experts is essential to address any design considerations or manufacturability challenges effectively.
How do you manufacture a Multi-cavity PCB?
Manufacturing a multi-cavity PCB involves several steps, similar to those of a standard PCB fabrication process. Here’s a general overview of how multi-cavity PCBs are manufactured:
- Design Preparation: Create the PCB design layout using PCB design software, incorporating multiple individual cavities into a single board. Ensure proper isolation between cavities and consider factors such as signal integrity, thermal management, and manufacturability.
- Gerber File Generation: Generate Gerber files and other manufacturing data required for fabrication, including drill files, pick-and-place files, and assembly drawings. These files contain the necessary information for manufacturing each layer of the PCB.
- Material Selection: Choose the appropriate substrate material for the PCB based on factors such as electrical properties, thermal conductivity, and cost. Common materials include FR-4 epoxy fiberglass, which provides a good balance of performance and affordability.
- Layer Stackup Design: Determine the layer stackup configuration based on the number of cavities and specific requirements of the design. Define the arrangement of copper layers, insulating layers, and any additional features such as power or ground planes.
- Inner Layer Processing: Begin the fabrication process by preparing the inner layers of the PCB stackup. This typically involves cleaning, etching, and laminating copper foil onto the substrate material to create the conductive traces and planes.
- Drilling: Drill holes for vias, component mounting, and interconnections between layers. High-precision drilling equipment is used to create holes with tight tolerances to ensure accurate alignment between layers.
- Through-hole Plating: Coat the drilled holes with a conductive material, typically copper, to establish electrical connections between different layers of the PCB. This process is called through-hole plating or electroplating.
- Outer Layer Processing: Process the outer layers of the PCB stackup by laminating copper foil, applying solder mask to define solderable areas, and adding a silkscreen layer for component labeling and identification.
- Etching and Imaging: Use a photoresist process to define the circuit traces and features on the outer layers of the PCB. Expose the photoresist to UV light through a photomask, develop it to remove unwanted areas, and then etch away the exposed copper to reveal the desired circuit pattern.
- Surface Finish: Apply a surface finish to protect exposed copper surfaces, facilitate soldering, and enhance the overall reliability of the PCB. Common surface finishes include HASL (Hot Air Solder Leveling), ENIG (Electroless Nickel Immersion Gold), and OSP (Organic Solderability Preservatives).
- Testing: Perform electrical testing to verify the integrity and functionality of the fabricated PCB. This may involve continuity testing, impedance testing, and other electrical measurements to ensure that the PCB meets design specifications.
- Final Inspection and Packaging: Inspect the fabricated PCB for any defects or imperfections and perform any necessary rework or repairs. Once validated, the PCBs are packaged and prepared for shipment to the assembly facility or end-user.
Throughout the manufacturing process, strict quality control measures are implemented to ensure the reliability and performance of the final multi-cavity PCBs. Collaboration between design engineers and manufacturing experts is crucial to address any design considerations or manufacturability challenges effectively.
How much should a Multi-cavity PCB cost?
The cost of a multi-cavity PCB can vary significantly depending on various factors such as the complexity of the design, the number of layers, the size of the board, the materials used, the manufacturing processes involved, and the quantity ordered. Here are some key factors that influence the cost:
- Design Complexity: PCBs with more complex designs, including multiple cavities, intricate routing, and advanced features, typically require more time and resources to manufacture, resulting in higher costs.
- Number of Layers: Multi-cavity PCBs can vary in the number of layers, ranging from simple single-sided or double-sided boards to more complex multi-layer designs. Each additional layer adds to the manufacturing complexity and cost.
- Materials: The choice of substrate material, copper thickness, and surface finish can impact the cost of the PCB. High-performance materials and finishes may incur additional expenses compared to standard options.
- Manufacturing Processes: Certain manufacturing processes, such as HDI (High-Density Interconnect), impedance control, and blind/buried vias, can increase the cost of the PCB due to their complexity and specialized equipment requirements.
- Quantity: Economies of scale apply to PCB manufacturing, meaning that larger production quantities typically result in lower per-unit costs. Ordering larger quantities can help reduce the overall cost per board.
- Lead Time: Rush orders or expedited production schedules may incur additional fees. Planning ahead and allowing for longer lead times can help minimize costs.
- Additional Services: Additional services such as assembly, testing, and quality assurance may be offered by the PCB manufacturer at an extra cost.
It’s essential to obtain quotes from multiple PCB manufacturers and carefully review the pricing breakdown to understand the factors contributing to the overall cost. Additionally, working closely with the manufacturer to optimize the design for cost-effectiveness without compromising quality or performance can help achieve the desired balance between cost and functionality.
What is Multi-cavity PCB base material?
The base material for multi-cavity PCBs is typically chosen based on several factors such as electrical properties, thermal conductivity, mechanical strength, cost-effectiveness, and compatibility with the manufacturing process. One of the most commonly used base materials for PCBs, including multi-cavity PCBs, is FR-4.
FR-4 is a type of epoxy fiberglass material that offers a good balance of performance and affordability. It provides excellent electrical insulation properties, making it suitable for use as the substrate material for PCBs. FR-4 also has good mechanical strength and dimensional stability, which are important for maintaining the integrity of the PCB during fabrication and operation.
Other base materials that may be used for multi-cavity PCBs include:
- High-Temperature FR-4: Similar to standard FR-4, but designed to withstand higher operating temperatures, making it suitable for applications where elevated temperatures are expected.
- Polyimide (PI): Known for its high-temperature resistance and excellent mechanical properties, polyimide is often used in applications requiring flexibility or in environments with extreme temperatures.
- Rogers Materials: Rogers Corporation offers a range of high-performance laminates specifically designed for demanding applications, including multi-cavity PCBs. These materials offer superior electrical performance, low dielectric loss, and excellent thermal conductivity.
- Metal Core: In some cases, multi-cavity PCBs may use a metal core substrate such as aluminum or copper, especially in applications requiring high thermal conductivity or improved heat dissipation.
The choice of base material depends on the specific requirements of the PCB design, including electrical performance, thermal management needs, and cost considerations. It’s essential to select a base material that meets the desired specifications while ensuring compatibility with the manufacturing process and assembly requirements.
Which company makes Multi-cavity PCB?
Multi-cavity PCBs are produced by many PCB manufacturing companies. Some well-known PCB manufacturers include Foxconn, JLCPCB, King Brother, and Wurth Electronics. These companies have advanced production equipment, rich experience, and professional teams to meet various customer needs for multi-cavity PCBs.
Our company can also produce multi-cavity PCBs and has the following advantages:
- Professional Team: We have an experienced and skilled team, including engineers, technicians, and quality control experts. They can provide comprehensive technical support, from design to production, testing, and quality control, ensuring smooth progress at every stage.
- Advanced Equipment: Our company is equipped with advanced production equipment and process technologies, including high-precision drilling machines, automated copper etching machines, surface treatment equipment, and more. These equipment and technologies ensure the production of high-quality, precise multi-cavity PCBs.
- Flexible Production: We can produce multi-cavity PCBs of different specifications, layers, and sizes according to customer requirements. Whether it’s small-batch production or large-scale production, we can meet customer needs.
- Quality Assurance: Quality is our top priority. We have strict quality management systems in place, from raw material procurement to production process control and final product inspection. This ensures that each multi-cavity PCB meets customer requirements and standards.
- Timely Delivery: We are committed to delivering customer orders on time, ensuring that customers can proceed with production and project implementation as planned.
Through the multi-cavity PCBs produced by our company, customers can obtain high-quality, reliable products that meet their application needs, driving the success of their projects. We are willing to cooperate with customers, develop together, and achieve mutual success.
What are the 7 qualities of good customer service?
Good customer service is essential for building strong customer relationships and fostering loyalty. Here are seven qualities of good customer service:
- Responsiveness: Good customer service involves promptly addressing customer inquiries, concerns, and issues. Responding to customer queries in a timely manner demonstrates attentiveness and a commitment to meeting customer needs.
- Empathy: Empathy is the ability to understand and share the feelings of others. Good customer service representatives empathize with customers, acknowledging their concerns and demonstrating compassion. This helps to build trust and rapport with customers.
- Clear Communication: Effective communication is crucial in customer service. Customer service representatives should communicate clearly and concisely, ensuring that customers understand the information provided and feel informed about their options and solutions.
- Problem-Solving Skills: Good customer service involves being proactive in resolving customer problems and addressing their needs. Customer service representatives should have strong problem-solving skills to identify issues, find solutions, and take appropriate action to resolve them.
- Professionalism: Professionalism is key to providing good customer service. Customer service representatives should maintain a positive and respectful attitude, remain calm under pressure, and handle customer interactions with professionalism and integrity.
- Product Knowledge: Good customer service requires a thorough understanding of the products or services offered. Customer service representatives should be knowledgeable about the features, benefits, and usage of the products or services, enabling them to provide accurate information and assistance to customers.
- Follow-Up: Following up with customers after resolving an issue or completing a transaction demonstrates a commitment to customer satisfaction. Good customer service includes checking in with customers to ensure their needs have been met and addressing any further concerns or questions they may have.
By embodying these qualities, businesses can provide exceptional customer service experiences that leave a lasting positive impression on their customers and contribute to long-term success.
FAQs
What is a multi-cavity PCB?
A multi-cavity PCB is a type of printed circuit board that incorporates multiple individual circuit cavities into a single board. Each cavity typically contains its own set of components and circuits, isolated from each other on the board.
What are the advantages of multi-cavity PCBs?
Multi-cavity PCBs offer advantages such as space-saving design, reduced interconnect complexity, improved signal integrity, enhanced thermal management, and simplified assembly processes.
Where are multi-cavity PCBs commonly used?
Multi-cavity PCBs are commonly used in applications where space is limited and multiple independent circuits need to be integrated into a single board. They are often found in smartphones, tablets, IoT devices, consumer electronics, and other compact electronic devices.
How are multi-cavity PCBs designed?
Multi-cavity PCBs are designed using PCB design software, where multiple individual circuit cavities are incorporated into a single board layout. Design considerations include proper isolation between cavities, signal integrity, thermal management, and manufacturability.
What are the key factors to consider when designing multi-cavity PCBs?
Key factors to consider include isolation between cavities to prevent interference, signal integrity for high-speed signals, power distribution, thermal management, component placement, manufacturability, and testing requirements.
What materials are used in multi-cavity PCBs?
Multi-cavity PCBs are typically made using materials such as FR-4 epoxy fiberglass, which offer a good balance of performance and affordability. Other materials like high-temperature FR-4, polyimide, or metal core substrates may also be used depending on specific requirements.
How are multi-cavity PCBs manufactured?
The manufacturing process for multi-cavity PCBs involves steps such as design preparation, material selection, layer stackup design, inner layer processing, drilling, through-hole plating, outer layer processing, etching and imaging, surface finish, testing, and final inspection and packaging.