Module Substates Manufacturer
Module Substates Manufacturer,Module Substrates are foundational elements in electronic module assembly, providing a platform for integrating various components. These substrates support the mounting of chips, connectors, and other electronic modules, facilitating efficient assembly and electrical connections. Composed of multiple layers including insulators, conductors, and metal layers, Module Substrates ensure reliable electrical pathways and thermal management. Their design accommodates diverse module configurations, catering to the specific requirements of different electronic applications. Module Substrates play a crucial role in optimizing space utilization and performance in electronic modules for industries such as telecommunications, automotive, and consumer electronics, where compact design and reliability are essential.
In the domain of electronics and PCB engineering, a module substrate acts as the foundational platform for the integration and connection of electronic components. It provides structural integrity and facilitates electrical pathways between these components. Module substrates are typically fabricated from materials like fiberglass epoxy (FR-4), ceramics, or flexible polyimide, chosen based on the specific requirements of the application.
Integral to the design and production of electronic modules such as ICs, memory modules, and RF modules, module substrates ensure the necessary mechanical robustness and electrical connectivity for component functionality. They offer a mounting surface for components and incorporate intricate patterns of conductive traces and vias, generated through processes like etching, drilling, and plating, to efficiently route electrical signals.
In essence, module substrates are indispensable in ensuring the performance, reliability, and manufacturability of electronic modules. Hence, careful consideration of their design and selection is essential for PCB engineers and designers striving to enhance functionality and effectiveness in electronic systems.
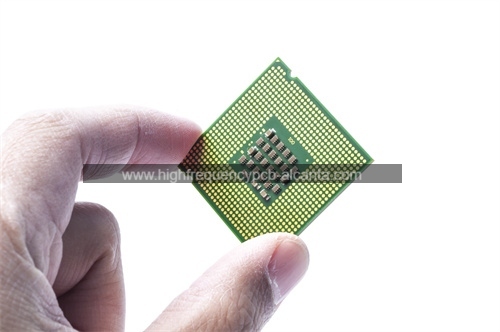
Module Substates Manufacturer
What are the functions of module substrates?
Module substrates, commonly known as Printed Circuit Boards (PCBs), are integral components that wield a profound impact on the operational intricacies of electronic devices. Their functionalities span a spectrum, including:
Structural Fortification: Module substrates serve as a robust underpinning for electronic components, ensuring the overall stability and resilience of the module or device.
Facilitation of Component Interweaving: PCBs adeptly facilitate the establishment of electrical connections among a diverse array of electronic components, orchestrating a seamless flow of signals and power.
Guidance of Signal Prowess: The substrate orchestrates the systematic routing of signals across distinct segments of the board, fostering a precise and efficient information flow within the electronic circuit.
Pivotal Power Nexus: PCBs serve as a central hub for the judicious distribution of power to disparate components, guaranteeing a consistent and stable operation of the entire electronic system.
Efficient Thermal Dissipation: Module substrates play a pivotal role in dissipating heat by providing strategic surfaces for heat sinks, thermal vias, and other cooling mechanisms. This is imperative for averting overheating and preserving the reliability of electronic components.
Seamless Integration of Passive Components: Resistors, capacitors, and other passive components seamlessly integrate onto the substrate, culminating in a streamlined overall footprint of the electronic device.
Harmonization of Electromagnetic Compatibility (EMC): Well-designed module substrates assume a crucial role in managing electromagnetic interference (EMI), ensuring stringent adherence to electromagnetic compatibility standards.
Synchronized Automated Assembly: Module substrates are meticulously crafted to facilitate a seamless manufacturability through automated assembly processes, serving as a linchpin for large-scale production.
Strategic Spatial Optimization: By accommodating dual-sided component mounting and offering multilayer configurations, module substrates contribute to the strategic utilization of space within electronic devices.
Expedited Facilitation of Testing and Debugging: The arrangement of components and traces on the substrate expedites testing and debugging processes, simplifying the identification and resolution of issues.
In essence, module substrates wield an indispensable role in the realm of electronic devices, providing a dynamic platform for the physical amalgamation and interconnection of electronic components while adeptly navigating diverse engineering considerations such as electrical performance, thermal management, and manufacturability.
What are the different types of module substrates?
Module substrates, commonly known as Printed Circuit Boards (PCBs), present a diverse array of types meticulously designed to meet the intricate demands of electronic device design. The tapestry of module substrates encompasses:
Single-Sided PCBs: Disclosing components and copper traces on a solitary side, these boards serve well in straightforward electronic applications.
Double-Sided PCBs: Hosting components and copper traces on both surfaces, these boards facilitate a higher density of components and intricate circuit designs.
Multilayer PCBs: Encompassing multiple strata of copper traces interspersed with insulating material, these substrates provide an augmented level of complexity and capabilities for sophisticated electronic devices.
Rigid PCBs: Epitomizing the conventional form, rigid PCBs furnish a sturdy foundation for electronic components.
Flexible PCBs (FPCBs): Endowed with flexibility for bending or twisting, these boards prove adept for applications grappling with spatial constraints or dynamic requirements.
Rigid-Flex PCBs: Converging attributes of both rigid and flexible PCBs, these substrates offer flexibility in designated sections while upholding structural rigidity.
High-Frequency PCBs: Precision-engineered to navigate signals at elevated frequencies, these substrates play a pivotal role in applications such as telecommunications and wireless technologies.
Metal Core PCBs (MCPCBs): Equipped with a metal core to bolster heat dissipation, these boards find suitability in applications with high power or exacting thermal management.
Ceramic PCBs: Leveraging a ceramic substrate, these boards showcase excellent thermal conductivity, rendering them ideal for high-temperature applications.
Aluminum PCBs: Harnessing an aluminum base, these boards excel in efficient heat dissipation and are frequently harnessed in LED applications.
Hybrid PCBs: Fusing diverse substrate materials or types, hybrid PCBs emerge as bespoke solutions meticulously tailored to meet specific performance or application requisites.
Thick Copper PCBs: Showcasing robust copper layers, these boards enhance their capacity to handle higher currents while ensuring improved thermal performance.
In essence, the diverse spectrum of module substrates caters to a broad spectrum of applications, affording engineers the latitude to discern the most fitting option based on parameters like circuit intricacy, flexibility prerequisites, thermal considerations, and the nuanced demands of specific applications.
How do module substrates differ from PCBs?
The terms “module substrates” and “Printed Circuit Boards (PCBs)” are often used interchangeably, but they can have nuanced differences based on context. In a broader sense:
PCBs (Printed Circuit Boards): This term serves as a comprehensive category covering a diverse range of boards employed in electronic circuits. PCBs can vary from single-sided to multilayered configurations, providing the fundamental platform for mounting and interconnecting electronic components in various applications.
Module Substrates: This term may be employed with a specific emphasis on boards used within modular electronic components or systems. The inclusion of “module” suggests a focus on the structural and interconnecting aspects of the board within a modular framework, where self-contained units can be integrated into larger systems.
In summary, while all module substrates are inherently PCBs, the choice of terminology might be influenced by the context or the particular application’s modular nature. The distinction, if any, is often subtle and may depend on the intended emphasis or specificity in communication. Clarifying the context helps ensure accurate understanding and communication.
What are the manufacturing technologies of module substrates?
The realm of module substrate manufacturing is a tapestry woven with diverse technologies, each meticulously tailored to sculpt an array of boards attuned to specific electronic applications. This varied manufacturing landscape for module substrates encompasses:
Printed Circuit Board (PCB) Fabrication: This foundational process involves shaping the base PCB using materials like fiberglass-reinforced epoxy laminates. A conductive layer, typically copper, is delicately applied to the substrate, and a precision-driven photolithography process defines the intricate circuit pattern.
Surface Mount Technology (SMT): Deployed for the intricate task of placing and soldering electronic components directly onto the surface of the module substrate, SMT emerges as the artisan of assembling smaller and lighter components, amplifying overall circuit density.
Through-Hole Technology (THT): THT, a methodical art, entails delicately inserting component leads through holes in the module substrate and orchestrating a symphony of soldering on the opposing side, particularly harmonious for larger components, rendering mechanical stability.
Multilayer Lamination: This ballet of manufacturing choreography involves the harmonious lamination of multiple single or double-sided boards, a fusion conducted with heat and pressure, giving rise to the crescendo of complex circuits seamlessly integrated within a compact space.
Screen Printing: A meticulous artist’s brushstroke, screen printing is harnessed to delicately apply solder paste onto the module substrate. This artistry ensures the precise placement of the paste on designated areas before the grand performance of component placement, a crucial prelude to the subsequent soldering act.
Reflow Soldering: The ballet of controlled heating takes center stage, transforming the module substrate adorned with components and solder paste. This performance unfolds a spectacle of molten solder, gracefully creating robust and reliable connections between components and the substrate.
Wave Soldering: A choreography designed for through-hole components, this method involves the graceful passage of the module substrate over a wave of molten solder, a waltz wherein solder adheres to the exposed metal leads, crafting solder joints with finesse.
Copper Plating: The metallurgical dance of electroplating copper onto the module substrate emerges as a symphony enhancing conductivity and elevating the adhesive embrace of components.
Stencil Printing: The precision of stencil printing, akin to an artist’s precision with a palette knife, ensures the accurate deposition of solder paste onto specific areas of the module substrate, an artistry essential for the subsequent soldering crescendo.
Advanced Material Deposition: A technological sonnet, involving techniques like chemical vapor deposition (CVD) or physical vapor deposition (PVD), unveils a canvas for applying thin films or coatings on specialized module substrates.
Selective Surface Finish: A curated exhibition, this process unfolds with the selective application of specific surface finishes, be it the richness of gold plating or the protective embrace of immersion tin, fostering enhanced conductivity or safeguarding against corrosion.
Together, these manufacturing masterpieces contribute to the orchestration of module substrates, each a unique symphony of characteristics finely tuned to meet the nuanced requirements of electronic devices and systems.
What are the main structures and production technologies of module substrates?
Module substrates, with their diverse applications in electronic devices, exhibit a range of structures and are manufactured using a variety of production technologies. Let’s explore the main structures and the corresponding production methodologies:
Single-Sided Module Substrates:
Structure: Components and copper traces reside on a single side of the substrate.
Production Technology: Standard PCB fabrication techniques, involving processes like etching, drilling, and soldering.
Double-Sided Module Substrates:
Structure: Components and copper traces are distributed on both sides of the substrate.
Production Technology: Similar to single-sided substrates, with additional steps for aligning and connecting components on both surfaces.
Multilayer Module Substrates:
Structure: Multiple layers of copper traces separated by insulating material.
Production Technology: Lamination of multiple single or double-sided boards, employing advanced PCB fabrication methods.
Rigid Module Substrates:
Structure: A solid and inflexible board.
Production Technology: Standard PCB fabrication processes, utilizing rigid material choices.
Flexible Module Substrates (FPCBs):
Structure: Flexible and bendable for space-constrained or dynamic applications.
Production Technology: Incorporates flexible materials like polyimide, with specialized fabrication processes ensuring flexibility.
Rigid-Flex Module Substrates:
Structure: Combines rigid and flexible areas in a single substrate.
Production Technology: Requires processing both rigid and flexible materials, often involving additional lamination steps.
High-Frequency Module Substrates:
Structure: Engineered for high-frequency signal handling.
Production Technology: Uses specialized materials with low dielectric constants and advanced fabrication techniques to minimize signal loss.
Metal Core Module Substrates (MCPCBs):
Structure: Includes a metal core for enhanced heat dissipation.
Production Technology: Involves integrating a thermally conductive metal core, typically aluminum or copper, into the substrate.
Ceramic Module Substrates:
Structure: Utilizes a ceramic substrate for superior thermal conductivity.
Production Technology: Employ specialized processes for working with ceramics, such as tape casting or thick-film printing.
Aluminum Module Substrates:
Structure: Features an aluminum base for efficient heat dissipation.
Production Technology: Incorporates an aluminum layer into the substrate using techniques suitable for metal substrates.
Hybrid Module Substrates:
Structure: Integrates different substrate materials for specific performance requirements.
Production Technology: Varied fabrication processes tailored to the combination of materials employed.
Thick Copper Module Substrates:
Structure: Utilizes thicker copper layers for improved current handling and thermal performance.
Production Technology: Requires specialized processes to deposit thicker copper layers onto the substrate.
These diverse production technologies collectively contribute to the creation of module substrates, each uniquely tailored to meet the specific demands of electronic devices and systems.
Frequently Asked Questions (FAQs)
What advantages are associated with flexible module substrates (FPCBs)?
Flexible module substrates offer advantages such as space efficiency, reduced weight, increased design flexibility, and enhanced reliability, especially in applications with dynamic or curved surfaces.
How do metal core module substrates (MCPCBs) differ from standard PCBs?
Metal core module substrates feature a thermally conductive metal core, typically aluminum or copper, which enhances heat dissipation and thermal management compared to standard PCBs.
What distinguishes rigid and flexible module substrates?
Rigid module substrates are firm and inflexible, providing stability and mechanical support. In contrast, flexible module substrates are pliable and adaptable, making them suitable for applications with space constraints or dynamic requirements.
What challenges are commonly encountered in the manufacturing of module substrates?
Challenges include achieving high-density interconnections, ensuring precise alignment of components, effective management of thermal dissipation, and meeting stringent quality standards and regulatory requirements.
How can the reliability of module substrates be ensured in electronic designs?
Reliability is assured through thorough testing, rigorous quality control processes, adherence to industry standards and specifications, careful material selection, and collaboration with experienced module substrate manufacturers.
Conclusion
In summary, the domain of module substrates, or Printed Circuit Boards (PCBs), plays a pivotal role in the intricate tapestry of electronic devices. Their adaptable structures, spanning from single-sided configurations to multilayered complexities, and from rigid compositions to flexible designs, cater to a wide array of application nuances. The manufacturing processes, encompassing a spectrum of techniques including conventional PCB fabrication and specialized methods such as lamination and surface mount technology, underscore the industry’s agility in meeting diverse requirements.
The selection of module substrates involves a meticulous evaluation of factors like size, weight, electrical performance, and environmental considerations. Flexible module substrates (FPCBs) emerge as a distinctive choice, offering spatial efficiency and heightened reliability in applications characterized by dynamism.
Metal core module substrates (MCPCBs), featuring thermally conductive cores, carve a niche for themselves by providing superior heat dissipation capabilities, making them particularly suited for applications demanding stringent thermal management. The dichotomy between rigid and flexible substrates lies in their mechanical attributes, with rigid counterparts offering stability and their flexible counterparts providing adaptability.
The manufacturing journey is not without its challenges, with the need to address issues like achieving high-density interconnections, ensuring meticulous component alignment, and managing thermal dissipation effectively. Overcoming these hurdles necessitates a steadfast commitment to rigorous testing, unwavering adherence to quality standards, and collaborative efforts with seasoned manufacturers.
In the realm of electronic design, the linchpin is the reliability of module substrates. This reliability is meticulously crafted through stringent testing protocols, rigorous quality control measures, unwavering compliance with industry standards, scrupulous material selection, and symbiotic partnerships with seasoned manufacturers.
In essence, the universe of module substrates unfolds as a vibrant canvas where technological strides, diverse structural paradigms, and intricate manufacturing intricacies converge to meet the ever-evolving demands of electronic devices. Navigating this dynamic landscape requires a nuanced understanding of the types, functions, and manufacturing intricacies of module substrates, making it an indispensable knowledge domain for engineers, designers, and enthusiasts alike.