Mixed Dielectric Rogers PCB Manufacturing
Mixed Dielectric Rogers PCB Manufacturing,Mixed Dielectric Rogers PCBs combine different dielectric materials from Rogers Corporation to achieve optimal performance in high-frequency applications. These PCBs are meticulously designed to leverage the unique properties of each material, such as controlled dielectric constants and low loss tangents, thereby ensuring superior signal integrity and reduced electromagnetic interference.
With a blend of Rogers materials like the RO4000 series, RO3000 series, and RO6000 series, Mixed Dielectric Rogers PCBs offer versatility and precision tailored to specific frequency requirements. Whether for wireless communication systems, radar technology, or aerospace applications, these PCBs deliver exceptional performance, reliability, and thermal stability.
Manufactured using advanced processes and equipment, Mixed Dielectric Rogers PCBs undergo stringent quality control measures to meet industry standards and customer specifications. Their ability to handle high power levels, maintain consistent electrical properties, and withstand harsh environments makes them indispensable in the realm of high-frequency electronics.
In essence, Mixed Dielectric Rogers PCBs represent a pinnacle of engineering excellence, empowering cutting-edge technologies with seamless connectivity and unparalleled performance.
What is a Mixed Dielectric Rogers PCB?
A Mixed Dielectric Rogers PCB refers to a printed circuit board (PCB) manufactured using Rogers Corporation’s materials, specifically utilizing multiple dielectric layers with different properties. Rogers Corporation is a renowned manufacturer of high-performance materials commonly used in RF/microwave applications, where signal integrity and high-frequency performance are critical.
In a Mixed Dielectric Rogers PCB, different layers of the PCB may consist of various Rogers materials with distinct dielectric constants, loss tangents, and other electrical properties. This approach allows for tailored impedance control, improved signal integrity, and reduced electromagnetic interference (EMI) in high-frequency circuits.
The choice of Rogers materials for different layers depends on the specific requirements of the PCB design, such as operating frequency, signal speed, power handling, and environmental conditions. By using mixed dielectric layers, designers can optimize the performance of the PCB for the intended application, achieving better signal transmission and minimizing losses.
Overall, Mixed Dielectric Rogers PCBs are commonly used in applications such as wireless communication systems, radar systems, satellite communication, and other high-frequency electronic devices where precision and reliability are paramount.
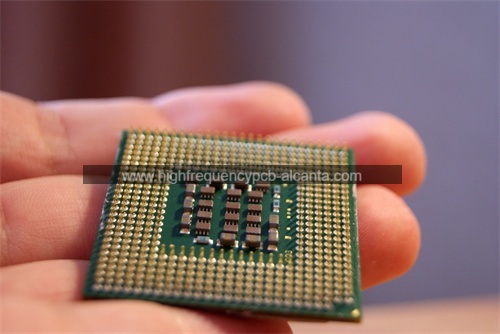
Mixed Dielectric Rogers PCB Manufacturing
What are the PCB Design Guidelines for Mixed Dielectric Rogers PCBs?
When designing a Mixed Dielectric Rogers PCB, several guidelines should be followed to ensure optimal performance and reliability. Here are some key PCB design guidelines:
- Layer Stackup Design: Plan the layer stackup carefully, considering the specific requirements of the design, such as signal integrity, impedance control, and mechanical constraints. Arrange the mixed dielectric layers strategically to achieve the desired electrical properties.
- Material Selection: Choose appropriate Rogers materials for each layer based on their dielectric constants, loss tangents, and other electrical characteristics. Select materials that meet the performance requirements of the circuit and ensure compatibility between layers.
- Impedance Control: Maintain consistent impedance throughout the PCB by carefully controlling trace widths, dielectric thicknesses, and layer-to-layer transitions. Use impedance calculation tools and simulations to verify impedance matching.
- Signal Routing: Route high-frequency signals carefully to minimize losses and signal distortion. Follow best practices for controlled impedance routing, such as using differential pairs, avoiding sharp bends, and maintaining proper spacing between traces.
- Grounding and Power Distribution: Design a robust ground and power distribution network to minimize noise and interference. Use dedicated ground planes and power planes to provide low impedance paths for return currents and reduce crosstalk.
- EMI/EMC Considerations: Implement measures to mitigate electromagnetic interference (EMI) and ensure electromagnetic compatibility (EMC). This may include proper shielding, filtering, and layout techniques to minimize radiated emissions and susceptibility.
- Thermal Management: Consider thermal effects and ensure adequate heat dissipation in the PCB design, especially for high-power components or applications operating in harsh environments. Use thermal vias, heatsinks, and proper component placement to manage heat effectively.
- Design for Manufacturability (DFM): Design the PCB with manufacturing considerations in mind to facilitate cost-effective and reliable production. Follow industry-standard PCB design rules and guidelines to minimize fabrication issues and ensure manufacturability.
- Signal Integrity Analysis: Perform signal integrity analysis using simulation tools to validate the design and predict potential issues such as signal reflections, crosstalk, and timing violations. Adjust the design accordingly to optimize signal integrity performance.
- Testing and Validation: Conduct thorough testing and validation of the PCB design to verify its performance against the design requirements. Use advanced testing techniques such as impedance testing, signal integrity measurements, and high-frequency testing to ensure compliance with specifications.
By adhering to these PCB design guidelines, designers can effectively create Mixed Dielectric Rogers PCBs that meet the stringent requirements of high-frequency applications while ensuring reliable operation and performance.
What is the Mixed Dielectric Rogers PCB Fabrication Process?
The fabrication process for a Mixed Dielectric Rogers PCB involves several steps, similar to the fabrication of other types of printed circuit boards. However, there are specific considerations and techniques involved due to the use of mixed dielectric materials, particularly those provided by Rogers Corporation. Here’s a general outline of the process:
- Design Preparation:
– PCB designers need to carefully plan the layer stackup considering the specific requirements of the circuit, such as impedance control, signal integrity, and RF/microwave performance.
– Choose appropriate Rogers materials for each layer based on their dielectric constants, loss tangents, and other electrical properties.
- Layer Stackup Design:
– Design the layer stackup to incorporate the mixed dielectric materials in the required configuration.
– Consider the order and arrangement of layers to optimize signal transmission and impedance matching.
- Circuit Layout:
– Place components and route traces according to the PCB design requirements, ensuring proper impedance matching and signal integrity.
– Pay close attention to high-frequency routing techniques to minimize signal loss and electromagnetic interference.
- Gerber File Generation:
– Generate Gerber files and other manufacturing documents required for PCB fabrication, ensuring that the design specifications are accurately communicated to the fabricator.
- Material Procurement:
– Procure the required Rogers materials for PCB fabrication, ensuring that the selected materials match the design specifications.
- Preparation of Substrate Materials:
– Prepare the substrate materials, typically fiberglass-reinforced epoxy laminates with copper foil bonded on both sides.
- Lamination:
– Stack the prepared substrate materials along with the Rogers materials according to the layer stackup design.
– Apply heat and pressure to laminate the layers together, forming a solid composite structure.
- Drilling:
– Drill holes for vias and component mounting pads according to the PCB design.
– Use precision drilling equipment to ensure accuracy and consistency.
- Copper Plating:
– Plate the drilled holes with copper to form vias, providing electrical connections between different layers of the PCB.
- Etching:
– Use chemical etching or other techniques to remove excess copper and define the traces and copper features according to the PCB design.
- Surface Finish:
– Apply surface finish to protect the copper traces, prevent oxidation, and facilitate soldering during assembly.
- Quality Control and Testing:
– Conduct thorough quality control checks and testing to ensure that the fabricated PCB meets the design specifications and performance requirements.
- Assembly:
– Mount components onto the PCB using soldering or other assembly techniques, following the assembly instructions provided in the PCB design.
- Final Testing:
– Perform final testing to verify the functionality and performance of the assembled PCB.
Throughout the fabrication process, it’s essential to follow industry standards, manufacturer recommendations, and best practices for handling and processing Rogers materials to ensure the reliability and performance of the Mixed Dielectric Rogers PCB. Additionally, close collaboration between PCB designers and fabricators is crucial to address any specific challenges associated with the use of mixed dielectric materials and achieve optimal results.
How do you Manufacture a Mixed Dielectric Rogers PCB?
Manufacturing a Mixed Dielectric Rogers PCB involves several steps, similar to the fabrication process of standard PCBs. However, there are some specific considerations due to the use of different dielectric materials. Below is an outline of the general manufacturing process:
- Design and Material Selection: Design the PCB layout using specialized software, considering the requirements of the circuit and the specific properties of Rogers Corporation’s materials. Select appropriate Rogers laminates for different layers based on factors such as dielectric constant, loss tangent, and operating frequency.
- Material Preparation: Acquire the chosen Rogers laminates in the required thicknesses and dimensions. These laminates typically come in sheets or panels.
- Preparation of Copper Foils: Prepare copper foils with the required thicknesses for the inner and outer layers of the PCB. These foils are typically laminated onto the Rogers substrates.
- Layer Stacking: Alternate layers of Rogers laminates and copper foils are stacked together according to the PCB design. Depending on the complexity of the PCB, multiple layers may be used.
- Lamination: The layered stack is then subjected to heat and pressure in a lamination press. This process bonds the layers together to form a solid composite structure.
- Drilling: Holes for component leads and vias are drilled into the laminated stack using precision CNC drilling machines. These holes will later be plated to provide electrical connections between layers.
- Copper Plating and Etching: The inner layers of copper are typically plated to increase thickness and ensure uniformity. A chemical etching process removes excess copper, leaving behind the desired copper traces according to the PCB design.
- Through-Hole Plating: Through-holes and vias are plated with conductive material to establish electrical connections between different layers of the PCB.
- Surface Finishing: Apply surface finishes such as HASL (Hot Air Solder Leveling), ENIG (Electroless Nickel Immersion Gold), or OSP (Organic Solderability Preservatives) to protect exposed copper and facilitate soldering.
- Silkscreen Printing: Apply component designators, logos, and other markings using silk screen printing techniques.
- Solder Mask Application: Apply solder mask to cover areas where soldering is not required and to protect the copper traces from environmental factors.
- Routing and Profiling: The PCB is routed to separate individual boards, and its edges are profiled to the desired shape using CNC routing machines.
- Quality Control and Testing: Perform visual inspection, electrical testing, and other quality control measures to ensure the PCB meets specifications and standards.
- Assembly: Components are mounted onto the PCB using surface mount technology (SMT) or through-hole technology (THT), depending on the design requirements.
- Final Inspection: Conduct a final inspection to verify the functionality and integrity of the assembled PCB.
Manufacturing a Mixed Dielectric Rogers PCB requires expertise in handling specialized materials and precise manufacturing processes to ensure the desired electrical performance and reliability.
How much should a Mixed Dielectric Rogers PCB cost?
The cost of a Mixed Dielectric Rogers PCB can vary significantly depending on various factors such as the size of the PCB, the number of layers, complexity of the design, required materials, manufacturing processes involved, quantities ordered, and supplier pricing policies. However, Mixed Dielectric Rogers PCBs generally tend to be more expensive compared to standard FR4 PCBs due to the specialized materials and manufacturing processes involved.
To get an accurate cost estimate for a Mixed Dielectric Rogers PCB, it’s best to consult with PCB manufacturers or suppliers who specialize in Rogers materials and high-frequency PCB fabrication. They can provide quotes based on your specific requirements and quantities needed. Additionally, you may want to consider factors such as lead time, quality assurance measures, and any additional services required, as these can also impact the overall cost.
What is the Mixed Dielectric Rogers PCB Base Material?
The base material used in Mixed Dielectric Rogers PCBs is typically composed of laminates made by Rogers Corporation. Rogers offers a range of high-performance materials specifically designed for RF/microwave applications, which are commonly used as the substrate for Mixed Dielectric PCBs.
Some of the popular base materials from Rogers Corporation for Mixed Dielectric PCBs include:
- RO4000® Series: This series comprises high-frequency laminates with low dielectric loss, making them suitable for applications requiring excellent signal integrity. Examples include RO4003C™, RO4350B™, and RO4835™ laminates.
- RO3000® Series: These laminates are designed for high-frequency applications where consistent electrical performance is crucial. They offer low loss and stable dielectric constant over a wide range of frequencies. Examples include RO3003™ and RO3035™ laminates.
- RO6000® Series: These laminates are engineered for demanding applications requiring high-frequency performance and thermal stability. They offer excellent mechanical properties and are suitable for applications such as aerospace and defense. Examples include RO6010™ and RO6200™ laminates.
- RO4400™ Series: This series features laminates with a ceramic-filled PTFE (Polytetrafluoroethylene) substrate, offering high thermal conductivity and excellent electrical performance at high frequencies.
These base materials provide the necessary electrical properties, such as controlled dielectric constant and low loss tangent, required for high-frequency applications. Mixed Dielectric Rogers PCBs leverage these materials in combination with other dielectric substrates to achieve desired performance characteristics, such as impedance control and signal integrity.
Which company makes Mixed Dielectric Rogers PCBs?
Mixed Dielectric Rogers PCBs are typically produced by professional printed circuit board (PCB) manufacturers who possess specialized equipment, technology, and expertise to meet the requirements of high-frequency circuits. Some of these companies include Rogers Corporation, Taconic, Isola, Arlon, and others. These companies offer various Rogers materials suitable for Mixed Dielectric PCB designs with different frequency and performance requirements.
As a PCB manufacturer, our company is also capable of producing Mixed Dielectric Rogers PCBs. We have advanced production equipment and a skilled technical team to meet customers’ demands for high-performance PCBs. We can provide a range of Rogers materials, including the RO4000 series, RO3000 series, RO6000 series, etc., to meet various application and performance requirements.
Our production process strictly adheres to industry standards and quality management systems to ensure that each PCB possesses excellent electrical performance and reliability. With our team’s extensive experience, we can offer technical support and customized solutions to help customers meet their high-frequency circuit design needs.
Additionally, we offer flexible order processing and timely delivery services to meet customers’ time requirements. We are committed to building long-term partnerships with customers, providing them with high-quality, reliable, and valuable Mixed Dielectric Rogers PCBs.
With our expertise, quality service, and competitive pricing, we are confident in becoming your partner for Mixed Dielectric Rogers PCBs and providing comprehensive support and solutions for your projects.
What are the 7 Qualities of Good Customer Service?
Good customer service is crucial for the success and reputation of any business. Here are seven qualities that define good customer service:
- Responsiveness: Good customer service involves being prompt and proactive in addressing customer inquiries, concerns, or issues. This includes responding to emails, messages, and calls in a timely manner, ensuring customers feel valued and their needs are attended to promptly.
- Empathy: Empathy is the ability to understand and share the feelings of customers. Good customer service representatives listen attentively to customers, acknowledging their concerns, and demonstrating understanding and compassion. Empathy helps build rapport and trust with customers.
- Clarity and Communication: Effective communication is essential in providing good customer service. Customer service representatives should communicate clearly and concisely, using language that is easy for customers to understand. They should provide accurate information, instructions, and updates to ensure customers are well-informed.
- Problem-Solving Skills: Good customer service involves being able to effectively resolve customer problems or issues. Customer service representatives should be resourceful, proactive, and solution-oriented, working to address customer concerns and find satisfactory resolutions. They should also have the authority and flexibility to make decisions to resolve issues promptly.
- Professionalism: Professionalism is key in all interactions with customers. Customer service representatives should maintain a courteous, respectful, and professional demeanor at all times, regardless of the situation or customer behavior. This includes being patient, calm, and diplomatic, even in challenging or stressful situations.
- Consistency: Consistency in service delivery is important for building trust and loyalty with customers. Good customer service should be consistent across all channels and interactions, ensuring that customers receive the same level of quality and attention every time they engage with the business.
- Follow-Up and Feedback: Good customer service doesn’t end with resolving immediate issues; it also involves following up with customers to ensure their satisfaction and gather feedback for improvement. Customer service representatives should check in with customers after resolving issues to ensure their needs were met and invite feedback for continuous improvement. This demonstrates commitment to customer satisfaction and fosters long-term relationships with customers.
By embodying these qualities, businesses can deliver exceptional customer service that not only meets but exceeds customer expectations, leading to increased customer satisfaction, loyalty, and positive word-of-mouth recommendations.
FAQs
What are Mixed Dielectric Rogers PCBs?
Mixed Dielectric Rogers PCBs are printed circuit boards (PCBs) that use a combination of Rogers Corporation’s materials with different dielectric properties in their construction. These PCBs are designed to meet the demands of high-frequency applications where signal integrity and performance are critical.
What are the advantages of using Mixed Dielectric Rogers PCBs?
Mixed Dielectric Rogers PCBs offer several advantages, including improved signal integrity, reduced electromagnetic interference (EMI), enhanced impedance control, and better performance at high frequencies. They are also capable of handling higher power levels and provide excellent thermal stability.
What types of Rogers materials are commonly used in Mixed Dielectric PCBs?
Rogers offers a range of materials suitable for Mixed Dielectric PCBs, including the RO4000 series, RO3000 series, RO6000 series, and more. These materials have varying dielectric constants, loss tangents, and thermal properties, allowing for customized designs to meet specific application requirements.
What applications are Mixed Dielectric Rogers PCBs used for?
Mixed Dielectric Rogers PCBs are commonly used in high-frequency applications such as wireless communication systems, radar systems, satellite communication, aerospace, and defense electronics. They are also found in medical devices, automotive radar systems, and other RF/microwave devices.
How are Mixed Dielectric Rogers PCBs manufactured?
The manufacturing process for Mixed Dielectric Rogers PCBs involves similar steps to standard PCB fabrication but with the use of specialized Rogers materials. It includes design, material selection, layer stacking, lamination, drilling, copper plating, etching, surface finishing, testing, and assembly.
What considerations should be made when designing Mixed Dielectric Rogers PCBs?
Designing Mixed Dielectric Rogers PCBs requires careful consideration of factors such as signal integrity, impedance matching, thermal management, and compatibility with other components. It’s essential to select appropriate Rogers materials and optimize the PCB layout for performance and reliability.
Are Mixed Dielectric Rogers PCBs more expensive than standard FR4 PCBs?
Yes, Mixed Dielectric Rogers PCBs are generally more expensive than standard FR4 PCBs due to the specialized materials and manufacturing processes involved. However, the benefits in terms of performance and reliability often justify the higher cost for applications requiring high-frequency performance.