Mixed Dielectric PCB Manufacturing.
Mixed Dielectric PCB Manufacturing,Mixed dielectric PCB is a type of printed circuit board (PCB) design that combines materials with different dielectric constants. This design leverages the advantages of various materials to meet specific circuit requirements. By using multiple dielectric materials on the same PCB, mixed dielectric PCBs enable finer signal control and noise suppression. For instance, materials with different dielectric constants can be employed in areas where isolation between high-frequency and low-frequency signals is necessary to enhance signal integrity and performance. Moreover, mixed dielectric PCBs facilitate differential signal transmission between different layers, enabling more intricate circuit designs. Widely applied in fields such as communications, RF, medical, and industrial control, this design offers greater flexibility and performance advantages, allowing electronic devices to adapt to evolving market demands and technological challenges.
What is a Mixed Dielectric PCB?
A Mixed Dielectric PCB, also known as a hybrid dielectric PCB, is a type of printed circuit board (PCB) that incorporates multiple dielectric materials within its construction. Dielectric materials are insulating materials that separate conductive layers within a PCB, preventing electrical short circuits and controlling signal propagation.
In a Mixed Dielectric PCB, different areas or layers of the board may use different dielectric materials depending on the specific requirements of those areas. This approach allows designers to tailor the electrical properties of different parts of the PCB to optimize performance.
Some common reasons for using mixed dielectric materials in PCB design include:
- Controlled Impedance: Different dielectric materials have different permittivity values (also known as dielectric constants). By using materials with different permittivity values in different areas of the PCB, designers can control the impedance of specific signal traces to match the requirements of high-speed digital signals.
- Signal Integrity: Mixed dielectric PCBs can help manage signal integrity by minimizing signal distortion and loss caused by impedance mismatches and signal reflections.
- Thermal Management: Certain dielectric materials may have better thermal conductivity properties than others. By using materials with higher thermal conductivity in areas of the PCB where heat dissipation is critical, designers can improve thermal management.
- Mechanical Strength: Different dielectric materials may offer varying degrees of mechanical strength and rigidity. By using materials with appropriate mechanical properties in different areas of the PCB, designers can ensure the board meets the required structural requirements.
- Cost Optimization: Mixed dielectric PCBs allow designers to balance performance requirements with cost considerations by using more expensive high-performance dielectric materials only where necessary, while using less expensive materials elsewhere.
Overall, the use of mixed dielectric materials in PCB design provides flexibility and optimization opportunities to meet the diverse requirements of modern electronic devices. However, it also adds complexity to the manufacturing process and may require careful consideration of material compatibility, fabrication techniques, and design trade-offs.
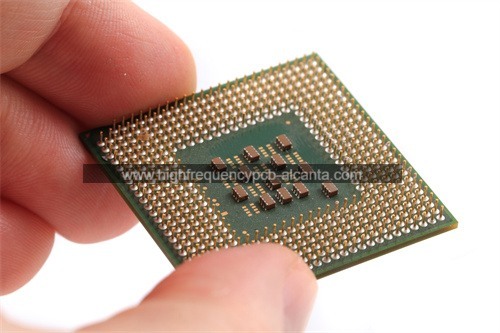
Mixed dielectric PCB manufacturing
What are the Mixed Dielectric PCB Design Guidelines?
Mixed Dielectric PCB design involves specific guidelines to ensure optimal performance and reliability. Here are some key guidelines:
- Material Selection: Choose dielectric materials with appropriate permittivity (dielectric constant) values for different areas of the PCB to control impedance and signal integrity.
- Layer Arrangement: Plan the layer stackup carefully, placing high-performance dielectric materials where they are most needed for controlled impedance, signal integrity, and thermal management.
- Impedance Matching: Design controlled impedance traces using appropriate widths and layer configurations based on the dielectric materials used. Ensure consistency in impedance throughout the signal paths.
- Signal Routing: Route high-speed signal traces on layers with dielectric materials offering consistent and low-loss characteristics to minimize signal distortion and reflections.
- Thermal Considerations: Place components generating heat strategically on the PCB and use dielectric materials with good thermal conductivity in these areas to enhance heat dissipation and prevent hot spots.
- Mechanical Stability: Utilize dielectric materials with adequate mechanical strength and rigidity in areas where mechanical stability is crucial, such as mounting points for connectors and heavy components.
- Compatibility Testing: Verify compatibility between different dielectric materials to prevent issues such as delamination or material degradation during fabrication and operation.
- Manufacturing Constraints: Consider manufacturing capabilities and limitations when designing mixed dielectric PCBs, ensuring that fabrication processes can handle the chosen materials and layer configurations effectively.
- Cost Optimization: Balance performance requirements with cost considerations by using high-performance dielectric materials judiciously, focusing them where they offer the most significant benefits.
- Simulation and Prototyping: Use simulation tools to validate the design and verify performance metrics such as impedance matching and signal integrity. Prototyping and testing are essential to confirm the design’s functionality and reliability before mass production.
Following these guidelines ensures that a mixed dielectric PCB meets performance requirements while addressing thermal, mechanical, and manufacturing considerations effectively.
What is the Mixed Dielectric PCB Fabrication Process?
The fabrication process for a Mixed Dielectric PCB is similar to that of a standard PCB, with some additional considerations due to the use of multiple dielectric materials. Here’s an overview of the fabrication process for a Mixed Dielectric PCB:
- Design Preparation: The PCB design is created using specialized PCB design software. Designers specify the layer stackup, including the types and locations of different dielectric materials.
- Material Selection: Choose appropriate dielectric materials based on the design requirements, considering factors such as permittivity, thermal conductivity, and mechanical properties.
- Layer Stackup Preparation: Prepare the layer stackup by laminating alternating layers of conductive copper foil and dielectric material. The sequence and types of dielectric materials used depend on the specific design requirements.
- Copper Cladding: Apply copper cladding to both sides of the dielectric layers using methods such as electroplating or lamination.
- Circuit Patterning: Use photolithography or other etching techniques to define the conductive traces on the copper layers, creating the desired circuit pattern.
- Via Drilling: Drill holes (vias) through the PCB to establish electrical connections between different layers. Special care may be needed to ensure proper alignment and insulation in areas where different dielectric materials meet.
- Via Filling (Optional): Fill vias with conductive or non-conductive material to enhance electrical conductivity, thermal dissipation, or mechanical stability, depending on the design requirements.
- Surface Finish: Apply a surface finish to protect the copper traces and ensure solderability, using techniques such as electroless nickel immersion gold (ENIG), hot air solder leveling (HASL), or immersion tin/silver.
- Inspection and Testing: Inspect the fabricated PCB for defects, including shorts, opens, and other manufacturing issues. Conduct electrical testing to verify the integrity of the circuitry and impedance matching.
- Assembly: If necessary, assemble the PCB with components using techniques such as surface-mount technology (SMT) or through-hole mounting.
- Final Inspection: Perform a final inspection to ensure the assembled PCB meets quality standards and functional requirements.
- Packaging and Shipping: Package the PCBs for protection during transportation and deliver them to the end users or assembly facilities.
Throughout the fabrication process, careful attention is paid to ensure proper alignment, compatibility between different dielectric materials, and adherence to design specifications to produce high-quality Mixed Dielectric PCBs.
How do you manufacture a Mixed Dielectric PCB?
Manufacturing a Mixed Dielectric PCB involves several steps similar to those used in standard PCB manufacturing, with additional considerations for handling multiple dielectric materials. Here’s an overview of the manufacturing process for a Mixed Dielectric PCB:
- Design Preparation: The PCB design is created or provided by the customer using PCB design software. Designers specify the layer stackup and the types of dielectric materials to be used in different regions of the board.
- Material Selection: Choose appropriate dielectric materials based on the design requirements, considering factors such as permittivity, thermal conductivity, mechanical properties, and compatibility with other materials in the stackup.
- Layer Stackup Preparation: Prepare the layer stackup by laminating alternating layers of conductive copper foil and dielectric material. The sequence and types of dielectric materials used depend on the specific design requirements.
- Copper Cladding: Apply copper foil to both sides of the dielectric layers using methods such as electroplating or lamination. The copper serves as the conductive layer for routing electrical signals.
- Circuit Patterning: Use photolithography or other etching techniques to define the conductive traces on the copper layers, creating the desired circuit pattern. This involves applying a photoresist layer, exposing it to UV light through a mask, developing the pattern, and etching away the unwanted copper.
- Via Drilling: Drill holes (vias) through the PCB to establish electrical connections between different layers. Special care may be needed to ensure proper alignment and insulation in areas where different dielectric materials meet.
- Via Filling (Optional): Fill vias with conductive or non-conductive material to enhance electrical conductivity, thermal dissipation, or mechanical stability, depending on the design requirements.
- Surface Finish: Apply a surface finish to protect the copper traces and ensure solderability. Common surface finishes include electroless nickel immersion gold (ENIG), hot air solder leveling (HASL), or immersion tin/silver.
- Inspection and Testing: Inspect the fabricated PCB for defects, including shorts, opens, and other manufacturing issues. Conduct electrical testing to verify the integrity of the circuitry and impedance matching.
- Assembly (if applicable): If necessary, assemble the PCB with components using techniques such as surface-mount technology (SMT) or through-hole mounting.
- Final Inspection: Perform a final inspection to ensure the assembled PCB meets quality standards and functional requirements.
- Packaging and Shipping: Package the PCBs for protection during transportation and deliver them to the end users or assembly facilities.
Throughout the manufacturing process, careful attention is paid to ensure proper alignment, compatibility between different dielectric materials, and adherence to design specifications to produce high-quality Mixed Dielectric PCBs.
How much should a Mixed Dielectric PCB cost?
The cost of a Mixed Dielectric PCB can vary significantly depending on various factors, including the following:
- Board Size and Complexity: Larger boards with more intricate designs and a higher number of layers will generally cost more to manufacture.
- Material Selection: The choice of dielectric materials can greatly impact the cost. Higher-performance materials with specific properties such as high thermal conductivity or low dielectric loss tend to be more expensive.
- Layer Count: The number of layers in the PCB stackup affects fabrication complexity and cost. Mixed Dielectric PCBs with multiple layers may incur higher manufacturing expenses.
- Surface Finish and Copper Weight: Different surface finishes and copper weights have different costs associated with them. For example, ENIG (Electroless Nickel Immersion Gold) tends to be more expensive than HASL (Hot Air Solder Leveling), and thicker copper layers increase material costs.
- Manufacturing Technology: Advanced manufacturing techniques such as laser drilling, sequential lamination, or controlled impedance processing may add to the overall cost.
- Quality Standards and Testing: Compliance with specific quality standards and extensive testing procedures can increase manufacturing costs.
- Order Quantity: Typically, larger production runs result in lower per-unit costs due to economies of scale. However, prototype or small-batch production runs may have higher per-unit costs.
- Lead Time: Shorter lead times often incur additional charges, while longer lead times may offer cost savings.
Given these variables, it’s challenging to provide a precise figure for the cost of a Mixed Dielectric PCB without specific details about the design, materials, and production requirements. It’s advisable to consult with PCB manufacturers or suppliers to obtain accurate cost estimates based on your project’s specifications.
What is Mixed Dielectric PCB base material?
The base material used in Mixed Dielectric PCBs can vary depending on the specific design requirements and performance considerations. Typically, these PCBs incorporate a combination of different dielectric materials to optimize electrical, thermal, and mechanical properties in various areas of the board.
Common dielectric materials used in Mixed Dielectric PCBs include:
- FR-4 (Flame Retardant 4): FR-4 is a widely used epoxy-based laminate material with fiberglass reinforcement. It offers good electrical insulation properties, mechanical strength, and cost-effectiveness, making it suitable for many applications.
- High-Speed/High-Frequency Materials: For areas of the PCB requiring controlled impedance and low signal loss at high frequencies, specialized high-speed or high-frequency materials may be used. These materials often have lower dielectric constants and reduced signal loss compared to standard FR-4.
- Rogers and Taconic Materials: Manufacturers such as Rogers Corporation and Taconic offer a range of high-performance laminates specifically designed for RF/microwave applications. These materials may feature low loss tangent, stable dielectric constants, and excellent high-frequency performance.
- Polyimide (PI) and Liquid Crystal Polymer (LCP): Polyimide and LCP are flexible dielectric materials used in flexible PCBs or rigid-flex PCBs. They offer excellent thermal stability, flexibility, and resistance to harsh environments.
- Thermally Conductive Materials: In areas of the PCB requiring enhanced thermal management, thermally conductive dielectric materials may be used. These materials offer improved heat dissipation properties compared to standard FR-4, helping to mitigate hot spots and prevent thermal issues.
- Metal Core Materials: For applications requiring high thermal conductivity and rigidity, Metal Core PCBs (MCPCBs) use a metal core, typically aluminum or copper, as the base material. Dielectric layers are laminated onto the metal core to provide electrical insulation and signal routing.
The selection of base materials in Mixed Dielectric PCBs depends on factors such as signal integrity requirements, thermal management needs, mechanical constraints, and cost considerations. Designers carefully evaluate these factors to choose the most appropriate combination of dielectric materials for optimal performance and reliability.
Which company makes Mixed Dielectric PCBs?
Many companies are capable of manufacturing Mixed Dielectric PCBs. These companies include PCB manufacturers and electronic assembly service providers worldwide, such as Foxconn, JLCPCB, Eurocircuits, and Sunstone Circuits in the United States. These companies possess the technical expertise and resources required to produce Mixed Dielectric PCBs.
Our company is also capable of producing Mixed Dielectric PCBs, offering customized electronic solutions to our clients. We have advanced manufacturing equipment and a skilled technical team to meet clients’ requirements for complex designs, high performance, and reliability. Our manufacturing processes strictly adhere to international standards, ensuring product quality and performance stability.
Our strengths lie in:
- Technical Expertise: We have an experienced engineering team capable of providing professional technical support and design suggestions to ensure that Mixed Dielectric PCB designs meet clients’ requirements.
- Production Capacity: With fully equipped facilities and advanced production lines, we can efficiently manufacture various types of PCBs, including multilayer, high-density, high-frequency, and rigid-flex PCBs.
- Quality Control: We implement a rigorous quality management system, controlling every aspect from raw material procurement to production, inspection, and testing, to ensure stable and reliable product quality.
- Customer Service: We value communication and collaboration with our clients, actively listening to their needs and providing timely technical support and after-sales service to help them achieve project success.
No matter what our clients’ needs are, we can provide customized solutions for Mixed Dielectric PCBs, offering reliable support and assurance for their projects.
Qualities of Good Customer Service:
Qualities of good customer service include:
- Excellent Communication Skills: Good customer service representatives have strong verbal and written communication skills. They listen actively to customers, ask relevant questions, and provide clear and concise responses.
- Empathy and Understanding: Empathizing with customers and understanding their concerns and needs is crucial for providing effective customer service. It helps build rapport and trust, leading to more positive interactions.
- Patience and Calmness: Dealing with customers who may be frustrated or upset requires patience and the ability to remain calm under pressure. Good customer service representatives handle difficult situations with professionalism and composure.
- Product Knowledge: Having a deep understanding of the company’s products or services allows customer service representatives to provide accurate information and solutions to customer inquiries and issues.
- Problem-Solving Skills: Effective problem-solving skills enable customer service representatives to address customer concerns efficiently and find appropriate solutions to resolve issues.
- Adaptability and Flexibility: Customer service representatives should be adaptable and flexible to meet the diverse needs of customers. They should be able to adjust their approach based on the situation and customer preferences.
- Positive Attitude: A positive and enthusiastic attitude can go a long way in creating a pleasant customer experience. Good customer service representatives approach interactions with a can-do attitude and a willingness to help.
- Timeliness and Responsiveness: Responding promptly to customer inquiries and resolving issues in a timely manner demonstrates respect for the customer’s time and contributes to overall satisfaction.
- Attention to Detail: Paying attention to the details of customer interactions ensures that no important information or requests are overlooked, leading to thorough and satisfactory resolutions.
- Follow-Up and Follow-Through: Following up with customers after resolving their issues or inquiries shows commitment to their satisfaction. Following through on promises and commitments builds trust and credibility.
Overall, good customer service involves a combination of interpersonal skills, product knowledge, problem-solving abilities, and a genuine desire to help customers. It’s about creating positive experiences and building long-term relationships with customers.
FAQs (Frequently Asked Questions)
What are Mixed Dielectric PCBs?
Mixed Dielectric PCBs are printed circuit boards that incorporate multiple dielectric materials within their construction. These materials are strategically chosen to optimize electrical, thermal, and mechanical properties for specific areas of the PCB.
What are the advantages of using Mixed Dielectric PCBs?
Mixed Dielectric PCBs offer advantages such as optimized signal integrity, controlled impedance, improved thermal management, and enhanced mechanical stability. By using different dielectric materials, designers can tailor the PCB’s performance to meet the requirements of various applications.
Where are Mixed Dielectric PCBs commonly used?
Mixed Dielectric PCBs are used in a wide range of applications, including high-speed digital circuits, RF/microwave systems, power electronics, automotive electronics, aerospace, and telecommunications.
What factors should be considered when designing Mixed Dielectric PCBs?
Important factors to consider include signal integrity requirements, thermal management needs, mechanical stability, material compatibility, cost considerations, and manufacturing feasibility.
How do Mixed Dielectric PCBs differ from standard PCBs?
Unlike standard PCBs, which typically use a single dielectric material throughout, Mixed Dielectric PCBs utilize multiple dielectric materials in different areas of the board to achieve specific performance goals.
What are some common dielectric materials used in Mixed Dielectric PCBs?
Common dielectric materials include FR-4, high-speed laminates, Rogers and Taconic materials for RF/microwave applications, polyimide (PI), liquid crystal polymer (LCP), and thermally conductive materials.
How are Mixed Dielectric PCBs manufactured?
The manufacturing process for Mixed Dielectric PCBs involves similar steps to standard PCB fabrication, including layer stackup preparation, material selection, circuit patterning, via drilling, surface finishing, inspection, and testing. However, special attention is given to handling multiple dielectric materials and ensuring compatibility between them.
What are the cost considerations for Mixed Dielectric PCBs?
The cost of Mixed Dielectric PCBs depends on factors such as board size, complexity, material selection, layer count, surface finish, manufacturing technology, quality standards, order quantity, and lead time.
Can any PCB manufacturer produce Mixed Dielectric PCBs?
While many PCB manufacturers can produce Mixed Dielectric PCBs, specialized knowledge and expertise may be required to handle the complexities associated with multiple dielectric materials and their interactions.
Where can I find more information about Mixed Dielectric PCBs?
For more information, you can consult with PCB manufacturers, electronic design engineers, industry publications, online forums, and technical resources dedicated to PCB design and fabrication.