Mitsubishi BT PCB Manufacturer
Mitsubishi BT PCB Manufacturer,Mitsubishi BT PCBs represent the pinnacle of engineering excellence, meticulously crafted to meet the exacting standards of Mitsubishi Electric Corporation’s Bipolar Transistor (BT) technology. These printed circuit boards serve as the backbone of Mitsubishi’s BT systems, seamlessly integrating with the intricate network of electronic components to deliver unparalleled performance and reliability.
Engineered with precision and care, Mitsubishi BT PCBs feature advanced thermal management solutions to dissipate heat efficiently, ensuring optimal operating conditions even in the most demanding environments. Their high-frequency signal integrity and robust power distribution networks guarantee seamless communication and power delivery, essential for the smooth operation of BT systems across various applications.
Crafted from high-quality substrate materials and utilizing state-of-the-art manufacturing processes, Mitsubishi BT PCBs embody durability and longevity, capable of withstanding the rigors of industrial use while maintaining peak performance. Whether in industrial automation, telecommunications, or automotive systems, Mitsubishi BT PCBs stand as a testament to innovation, quality, and reliability, driving forward technological advancement with every circuit connection.
What is a Mitsubishi BT PCB?
A Mitsubishi BT PCB, in its most general sense, likely refers to a Printed Circuit Board (PCB) used in Mitsubishi BT (Bipolar Transistor) systems or devices. A PCB is a crucial component in electronic devices, providing mechanical support and electrical connections for various electronic components.
In the context of Mitsubishi BT, it may specifically denote a PCB designed and manufactured by Mitsubishi Electric Corporation for their Bipolar Transistor-based systems or equipment. These PCBs are engineered to meet the specific requirements and standards of Mitsubishi’s BT technology, ensuring reliability, efficiency, and compatibility with Mitsubishi’s products.
These PCBs likely undergo rigorous testing and quality control measures to ensure they meet Mitsubishi’s standards for performance and durability. They may feature specialized circuitry, layouts, and components tailored to the needs of Mitsubishi’s BT systems, optimizing their functionality and longevity.
Mitsubishi’s BT PCBs may be utilized in a wide range of applications, including industrial automation, power electronics, telecommunications, and more. They play a crucial role in the operation of Mitsubishi’s BT devices, facilitating the flow of electrical signals and power within the system.
Overall, a Mitsubishi BT PCB represents a key component in Mitsubishi’s BT technology ecosystem, embodying the company’s commitment to innovation, quality, and reliability in the field of electronics and electrical engineering.
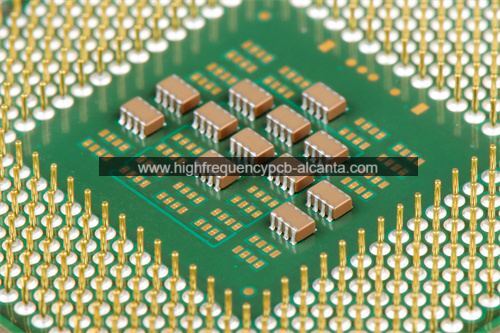
Mitsubishi BT PCB Manufacturer
What are the Mitsubishi BT PCB Design Guidelines?
Mitsubishi Electric Corporation provides specific design guidelines for PCBs used in their BT (Bipolar Transistor) systems to ensure optimal performance, reliability, and compatibility. While the exact guidelines may vary depending on the specific application and product, some general principles commonly included in Mitsubishi BT PCB design guidelines could be:
- Thermal Management: Ensuring proper thermal management to dissipate heat generated by the BT components on the PCB. This may involve incorporating thermal vias, heatsinks, or specific copper plane configurations to efficiently transfer heat away from critical components.
- High-Frequency Signal Integrity: Maintaining signal integrity for high-frequency signals by minimizing signal loss, reflections, and crosstalk. This may involve controlled impedance traces, proper grounding techniques, and careful routing to reduce signal distortion.
- Component Placement: Strategically placing components on the PCB to minimize signal interference, thermal coupling, and electromagnetic interference (EMI). Critical components such as BT transistors, capacitors, and inductors should be placed according to Mitsubishi’s recommendations to optimize performance and reliability.
- Power Distribution:Designing robust power distribution networks to ensure stable and reliable power delivery to all components on the PCB. This may involve proper trace width and thickness calculations, decoupling capacitor placement, and minimizing voltage drops across the board.
- EMI/EMC Compliance: Ensuring compliance with electromagnetic interference (EMI) and electromagnetic compatibility (EMC) standards to minimize interference with other electronic devices and ensure proper operation in diverse environments. This may involve implementing shielding techniques, proper grounding, and filtering components to suppress EMI.
- Mechanical Considerations: Taking into account mechanical constraints and assembly requirements to ensure the PCB can be effectively integrated into Mitsubishi BT systems or devices. This may involve adhering to specific form factors, mounting hole placements, and clearance requirements.
- Reliability and Durability: Designing the PCB to withstand environmental stresses, mechanical shocks, and thermal cycling to ensure long-term reliability and durability in demanding applications. This may involve selecting high-quality materials, robust fabrication processes, and adherence to industry standards for reliability testing.
These are just some general aspects that Mitsubishi Electric Corporation might consider in their BT PCB design guidelines. Actual guidelines may be more detailed and specific to particular products or applications, reflecting Mitsubishi’s commitment to delivering high-performance, reliable solutions in the field of electronics and electrical engineering.
What is the Mitsubishi BT PCB Fabrication Process?
The fabrication process for Mitsubishi BT (Bipolar Transistor) PCBs likely follows standard industry practices with potential variations to meet Mitsubishi’s specific requirements for performance and reliability. While the exact process may vary depending on factors such as the complexity of the PCB design and manufacturing facilities used, a general overview of the fabrication process could include the following steps:
- Design Preparation:The fabrication process begins with the preparation of the PCB design files. Mitsubishi engineers or designers create the PCB layout using specialized CAD (Computer-Aided Design) software, taking into account the specific requirements and guidelines for BT systems.
- Material Selection: Mitsubishi may specify the type of substrate material and laminate stackup to be used for the PCB based on factors such as thermal conductivity, dielectric properties, and mechanical strength. Common materials include FR-4 (Fire Retardant 4) epoxy laminate for standard applications and specialized materials for high-frequency or high-power applications.
- Panelization:Multiple PCBs are often fabricated simultaneously on a single larger panel to improve efficiency and reduce manufacturing costs. The individual PCB designs are arranged on the panel according to Mitsubishi’s specifications, taking into account factors such as spacing, routing channels, and fiducial marks.
- Preparation of Copper Clad Laminate: The chosen substrate material is coated with a layer of copper on one or both sides, forming a copper clad laminate. Mitsubishi may specify the thickness and copper weight (measured in ounces per square foot) based on the electrical and thermal requirements of the BT system.
- Photoresist Application: A layer of photoresist material is applied to the copper surface of the laminate. The PCB design pattern is then transferred onto the photoresist layer using a process called photolithography, typically involving exposure to UV light through a photomask.
- Etching: The exposed areas of the copper layer are chemically etched away, leaving behind the desired copper traces and pads as defined by the PCB design. Mitsubishi may employ advanced etching techniques to achieve precise trace widths and tolerances required for BT systems.
- Drilling: Holes are drilled into the PCB for through-hole components and vias. Mitsubishi may use automated drilling equipment capable of high precision to ensure accurate hole placement and alignment with the PCB design.
- Plating and Surface Finish: The drilled holes and exposed copper surfaces are plated with additional copper to improve conductivity and then coated with a surface finish to protect against oxidation and facilitate soldering. Common surface finishes include HASL (Hot Air Solder Leveling), ENIG (Electroless Nickel Immersion Gold), and OSP (Organic Solderability Preservative).
- Solder Mask Application: A layer of solder mask is applied over the copper traces and pads to insulate them from environmental factors and prevent solder bridges during assembly. The solder mask is cured and then selectively removed to expose areas for soldering.
- Silkscreen Printing: Mitsubishi may include component designators, logos, and other identifying information on the PCB using silkscreen printing. This information helps assembly technicians identify components and ensure proper orientation during assembly.
- Testing and Inspection: Each PCB undergoes rigorous testing and inspection to verify electrical continuity, dimensional accuracy, and adherence to Mitsubishi’s specifications. Automated testing equipment may be used to perform electrical tests, while visual inspection ensures the quality of solder joints and surface finishes.
- Routing and Singulation: After testing and inspection, the larger panel containing multiple PCBs is routed into individual boards, each representing a finished Mitsubishi BT PCB. Mitsubishi may use automated routing equipment to separate the PCBs with precision while minimizing waste material.
- Packaging and Shipping: The finished PCBs are packaged according to Mitsubishi’s specifications and prepared for shipment to assembly facilities where they will be integrated into BT systems or devices. Packaging may include protective materials to prevent damage during transit.
Throughout the fabrication process, Mitsubishi likely employs strict quality control measures to ensure the reliability and performance of their BT PCBs. This may include adherence to industry standards such as IPC (Association Connecting Electronics Industries) specifications, as well as internal quality assurance protocols specific to Mitsubishi’s manufacturing facilities. By following a comprehensive fabrication process, Mitsubishi can produce high-quality BT PCBs tailored to the requirements of their BT systems, ensuring optimal performance and reliability in diverse applications.
How do you manufacture a Mitsubishi BT PCB?
Manufacturing a Mitsubishi BT (Bipolar Transistor) PCB involves a series of steps tailored to meet Mitsubishi’s specific requirements for performance, reliability, and compatibility with their BT systems. While exact details may vary based on factors such as the complexity of the PCB design and Mitsubishi’s internal processes, a general overview of the manufacturing process could include the following steps:
- Design Preparation: Mitsubishi engineers or designers create the PCB layout using specialized CAD (Computer-Aided Design) software, following Mitsubishi’s design guidelines and specifications for BT systems. This includes determining the placement of components, routing of traces, and consideration of thermal management requirements.
- Material Selection: Mitsubishi selects the appropriate substrate material and laminate stackup for the PCB based on factors such as thermal conductivity, dielectric properties, and mechanical strength. Common materials include FR-4 (Fire Retardant 4) epoxy laminate for standard applications and specialized materials for high-frequency or high-power applications.
- Panelization: Multiple PCBs are often fabricated simultaneously on a single larger panel to improve efficiency and reduce manufacturing costs. Mitsubishi arranges the individual PCB designs on the panel according to their specifications, considering factors such as spacing, routing channels, and fiducial marks.
- Printing: Mitsubishi uses advanced printing techniques to transfer the PCB design onto the copper-clad laminate. This may involve processes such as photolithography, where a photoresist layer is applied to the copper surface and exposed to UV light through a photomask to define the desired circuit pattern.
- Etching: The exposed areas of the copper layer are chemically etched away, leaving behind the desired copper traces and pads as defined by the PCB design. Mitsubishi may employ precise etching techniques to achieve the required trace widths and tolerances for BT systems.
- Drilling: Holes are drilled into the PCB for through-hole components and vias. Mitsubishi uses automated drilling equipment capable of high precision to ensure accurate hole placement and alignment with the PCB design.
- Plating and Surface Finish: The drilled holes and exposed copper surfaces are plated with additional copper to improve conductivity and then coated with a surface finish to protect against oxidation and facilitate soldering. Common surface finishes include HASL (Hot Air Solder Leveling), ENIG (Electroless Nickel Immersion Gold), and OSP (Organic Solderability Preservative).
- Solder Mask Application: A layer of solder mask is applied over the copper traces and pads to insulate them from environmental factors and prevent solder bridges during assembly. Mitsubishi ensures uniform coverage and precise alignment of the solder mask using automated processes.
- Silkscreen Printing: Mitsubishi includes component designators, logos, and other identifying information on the PCB using silkscreen printing. This information helps assembly technicians identify components and ensure proper orientation during assembly.
- Testing and Inspection: Each PCB undergoes rigorous testing and inspection to verify electrical continuity, dimensional accuracy, and adherence to Mitsubishi’s specifications. Automated testing equipment may be used to perform electrical tests, while visual inspection ensures the quality of solder joints and surface finishes.
- Routing and Singulation: After testing and inspection, the larger panel containing multiple PCBs is routed into individual boards, each representing a finished Mitsubishi BT PCB. Mitsubishi uses automated routing equipment to separate the PCBs with precision while minimizing waste material.
- Packaging and Shipping: The finished PCBs are packaged according to Mitsubishi’s specifications and prepared for shipment to assembly facilities where they will be integrated into BT systems or devices. Mitsubishi ensures proper handling and protection of the PCBs during transit to prevent damage.
Throughout the manufacturing process, Mitsubishi employs strict quality control measures to ensure the reliability and performance of their BT PCBs. This includes adherence to industry standards such as IPC (Association Connecting Electronics Industries) specifications, as well as internal quality assurance protocols specific to Mitsubishi’s manufacturing facilities. By following a comprehensive manufacturing process, Mitsubishi can produce high-quality BT PCBs tailored to the requirements of their BT systems, ensuring optimal performance and reliability in diverse applications.
How much should a Mitsubishi BT PCB cost?
The cost of a Mitsubishi BT (Bipolar Transistor) PCB can vary significantly depending on several factors, including the complexity of the design, the materials used, the manufacturing processes involved, and the quantity ordered.
- Complexity of Design: PCBs with complex designs, such as those with dense circuitry, high-layer counts, or specialized features like impedance control or blind/buried vias, typically cost more to manufacture due to the increased complexity and precision required during fabrication.
- Materials Used:The choice of substrate material, copper thickness, surface finish, and other materials can influence the cost of the PCB. High-performance materials or specialized laminates designed for specific applications may incur higher costs compared to standard FR-4 materials.
- Manufacturing Processes: Advanced manufacturing processes such as HDI (High-Density Interconnect), laser drilling, or sequential lamination may increase the manufacturing cost of the PCB due to the specialized equipment and expertise required.
- Quantity Ordered: Economies of scale often apply in PCB manufacturing, meaning that larger production runs typically result in lower per-unit costs. Ordering PCBs in higher quantities can help reduce the cost per unit due to efficiencies in materials usage, setup, and production.
- Additional Services: Additional services such as PCB assembly, testing, conformal coating, and custom packaging may incur extra costs depending on the specific requirements of the project.
Given these factors, it’s challenging to provide a precise cost estimate for a Mitsubishi BT PCB without knowing the specific details of the design and manufacturing requirements. However, as a rough estimate, the cost of a Mitsubishi BT PCB could range from tens to hundreds of dollars per unit for small to medium-sized orders, with costs decreasing for larger quantities.
What is Mitsubishi BT PCB base material?
The base material used for Mitsubishi BT (Bipolar Transistor) PCBs can vary depending on the specific requirements of the application and the performance characteristics desired by Mitsubishi Electric Corporation. However, it’s likely that Mitsubishi utilizes a range of high-quality substrate materials tailored to meet the stringent demands of their BT systems.
One commonly used base material for PCBs, including those designed for high-power and high-frequency applications like Mitsubishi BT systems, is FR-4 (Fire Retardant 4) epoxy laminate. FR-4 is a widely used substrate material known for its excellent electrical insulation properties, mechanical strength, and thermal stability. It consists of a woven fiberglass reinforcement impregnated with an epoxy resin binder, providing a robust foundation for the copper traces and components on the PCB.
In addition to FR-4, Mitsubishi may also utilize specialized materials for specific applications within their BT systems. For example, they might employ high-frequency laminate materials with enhanced dielectric properties for RF (Radio Frequency) circuitry, or high-temperature substrates capable of withstanding elevated operating temperatures in power electronics applications.
Mitsubishi likely selects base materials based on factors such as thermal conductivity, dielectric constant, dissipation factor, mechanical properties, and reliability requirements. By choosing the appropriate base material, Mitsubishi can ensure that their BT PCBs meet the performance, reliability, and longevity standards demanded by their customers in various industries and applications.
Which company makes Mitsubishi BT PCBs?
Mitsubishi BT PCBs are typically manufactured by Mitsubishi Electric Corporation or its authorized partners. As a leading electronics company, Mitsubishi Electric is committed to developing and manufacturing various electronic devices and systems, including printed circuit boards (PCBs) for its BT technology. Mitsubishi Electric has extensive experience and expertise in PCB manufacturing, capable of designing and producing high-quality PCBs that meet the requirements of its BT systems.
As a PCB manufacturing company, we also have the capability to produce Mitsubishi BT PCBs. We have advanced manufacturing equipment and technology, as well as an experienced engineering team, capable of producing PCBs that comply with Mitsubishi’s BT system standards according to customer requirements and specifications. Our manufacturing process strictly follows industry standards and quality management systems to ensure that each PCB has reliability, performance, and durability.
Our manufacturing capabilities include, but are not limited to, the following aspects:
- PCB design: Our engineering team has extensive design experience, able to design PCBs according to customer-provided requirements and specifications to meet the performance and layout requirements of Mitsubishi BT systems.
- Material selection: We collaborate with high-quality material suppliers to provide various types of substrate materials, including FR-4, high-frequency materials, etc., to meet the specific requirements of Mitsubishi BT systems.
- Manufacturing process: We utilize advanced manufacturing processes and equipment, including automated printing, drilling, chemical etching, and surface treatment, to ensure the production of high-quality PCBs.
- Quality control: We strictly adhere to quality management systems, including rigorous inspections and testing at each manufacturing stage, to ensure that each PCB meets specification requirements.
- Customer support:We provide a professional customer support team capable of responding to customer needs and inquiries promptly, as well as providing technical support and solutions.
Through our manufacturing capabilities and experience, we can provide customers with high-quality, reliable, and cost-effective Mitsubishi BT PCBs that meet the requirements and expectations of their BT systems.
What are the 7 qualities of good customer service?
Good customer service is essential for building strong relationships with customers and fostering loyalty. Here are seven qualities that characterize good customer service:
- Responsiveness:Good customer service involves being attentive and responsive to customer inquiries, concerns, and feedback in a timely manner. This means promptly addressing customer needs and providing assistance when required.
- Empathy: Empathy is the ability to understand and share the feelings of customers. Good customer service representatives listen actively, show genuine concern for customers’ issues, and strive to put themselves in the customer’s shoes to better address their needs.
- Clear Communication: Effective communication is crucial in customer service. Good customer service representatives communicate clearly and concisely, using language that is easy for customers to understand. They provide relevant information, answer questions comprehensively, and avoid jargon or technical terms that may confuse customers.
- Knowledgeability: Good customer service representatives possess a thorough understanding of the products or services they are supporting. They are knowledgeable about features, benefits, and troubleshooting procedures, allowing them to provide accurate and helpful assistance to customers.
- Professionalism: Professionalism encompasses a range of behaviors, including courtesy, respect, and integrity. Good customer service representatives maintain a professional demeanor at all times, remaining calm and composed, even in challenging situations. They treat customers with respect and courtesy, regardless of the circumstances.
- Problem-Solving Skills: Good customer service involves effectively resolving customer issues and complaints. Customer service representatives should be adept at identifying problems, analyzing situations, and offering practical solutions or alternatives to address customer concerns.
- Follow-Up: Good customer service doesn’t end with the resolution of a customer’s immediate issue. It includes following up with customers to ensure that their needs have been met and that they are satisfied with the outcome. Follow-up communication can help build trust and demonstrate a commitment to customer satisfaction.
By embodying these qualities, businesses can deliver exceptional customer service experiences that not only meet but exceed customer expectations, leading to increased customer loyalty and positive brand reputation.
FAQs
What are Mitsubishi BT PCBs?
Mitsubishi BT PCBs are printed circuit boards designed and manufactured specifically for use in Mitsubishi Electric Corporation’s Bipolar Transistor (BT) systems. These PCBs play a crucial role in facilitating the flow of electrical signals and power within BT systems.
What are the key features of Mitsubishi BT PCBs?
Mitsubishi BT PCBs are engineered to meet the specific requirements and standards of Mitsubishi’s BT technology. They may incorporate features such as optimized thermal management, high-frequency signal integrity, robust power distribution networks, and compatibility with Mitsubishi’s BT components and systems.
What materials are used in Mitsubishi BT PCBs?
Mitsubishi BT PCBs may utilize high-quality substrate materials such as FR-4 epoxy laminate or specialized materials tailored to meet the performance and reliability requirements of BT systems. Copper traces, solder mask, and surface finishes are also key components of Mitsubishi BT PCBs.
How are Mitsubishi BT PCBs manufactured?
The manufacturing process for Mitsubishi BT PCBs typically involves steps such as design preparation, material selection, printing, etching, drilling, plating, surface finishing, solder mask application, silkscreen printing, testing, inspection, routing, and packaging. Mitsubishi follows stringent quality control measures to ensure the reliability and performance of their BT PCBs.
What are the applications of Mitsubishi BT PCBs?
Mitsubishi BT PCBs are used in a wide range of applications, including industrial automation, power electronics, telecommunications, automotive systems, and more. They are essential components in Mitsubishi’s BT systems, contributing to the efficiency, reliability, and performance of various electronic devices and equipment.
Where can I purchase Mitsubishi BT PCBs?
Mitsubishi BT PCBs are typically available through Mitsubishi Electric Corporation or its authorized distributors. Customers can inquire about purchasing options, specifications, and pricing directly from Mitsubishi or their authorized partners.
What are the benefits of using Mitsubishi BT PCBs?
Using Mitsubishi BT PCBs offers several benefits, including optimized performance, reliability, and compatibility with Mitsubishi’s BT systems. These PCBs are engineered to meet the stringent requirements of BT technology, ensuring efficient operation and long-term durability in demanding applications.