(MIS)Molded Interconnect Substrate
(MIS)Molded Interconnect Substrate Manufacturer,Mixed dielectric Rogers PCBs are a specialized type of printed circuit board (PCB) that utilizes multiple layers with varying dielectric constants, often incorporating Rogers materials. Rogers Corporation is renowned for its high-frequency laminate materials, which offer excellent electrical performance at microwave and RF frequencies. In Mixed Dielectric Rogers PCBs, layers with different dielectric constants are strategically stacked to meet the specific impedance requirements of high-frequency signals while maintaining signal integrity and minimizing signal loss. This approach allows for precise control of impedance throughout the PCB, enabling efficient transmission of high-frequency signals with minimal distortion. Mixed Dielectric Rogers PCBs find applications in various high-frequency electronic devices, such as telecommunications equipment, radar systems, satellite communications, and high-speed data transmission systems. The use of Rogers materials ensures exceptional performance, reliability, and stability, making Mixed Dielectric Rogers PCBs a preferred choice for demanding applications in the aerospace, defense, telecommunications, and automotive industries.
What is a Molded Interconnect Substrate (MIS)?
A Molded Interconnect Substrate (MIS) is a type of substrate used in electronics manufacturing, primarily in the production of compact electronic devices such as smartphones, tablets, and wearables. It combines the functions of a substrate, which provides structural support and electrical connections for electronic components, with the ability to integrate three-dimensional (3D) circuitry.
MIS typically consists of a thermoplastic material, such as liquid crystal polymer (LCP) or polyethylene terephthalate (PET), that is molded into the desired shape. Conductive traces and vias are then formed directly onto the substrate using techniques like laser ablation, printing, or plating. This allows for the creation of complex circuit patterns in a single manufacturing step, eliminating the need for separate circuit boards and interconnects.
The advantages of MIS include reduced size and weight, improved electrical performance due to shorter interconnect lengths, and enhanced design flexibility. By integrating circuitry directly into the substrate, MIS enables the creation of more compact and lightweight electronic devices with improved functionality and reliability.
Overall, MIS technology plays a crucial role in the development of miniaturized and high-performance electronic products, driving innovation in various industries including consumer electronics, automotive, healthcare, and aerospace.
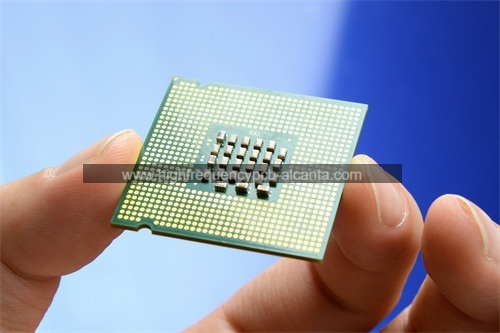
(MIS)Molded Interconnect Substrate Manufacturer
What are the Molded Interconnect Substrate (MIS) Design Guidelines?
Molded Interconnect Substrate (MIS) design guidelines help ensure the successful implementation of MIS technology in electronic devices. Here are some common design guidelines:
- Substrate Material Selection: Choose appropriate thermoplastic materials such as liquid crystal polymer (LCP) or polyethylene terephthalate (PET) that offer suitable mechanical properties, thermal stability, and compatibility with manufacturing processes.
- Circuit Layout and Design: Optimize the layout and design of the circuitry to minimize signal interference, impedance mismatches, and parasitic capacitance. Use techniques like impedance matching, controlled impedance routing, and proper grounding to improve signal integrity.
- Component Placement: Strategically place components on the MIS to minimize the overall footprint and ensure efficient routing of electrical connections. Consider the thermal characteristics of components to prevent overheating and maintain reliability.
- Trace Width and Spacing: Follow recommended trace width and spacing guidelines to achieve proper signal transmission and avoid signal degradation due to impedance mismatch or crosstalk.
- Via Design and Placement: Design vias carefully to ensure reliable electrical connections between layers of the MIS. Use techniques like blind vias, buried vias, and microvias to reduce signal distortion and improve routing density.
- Alignment and Tolerances: Maintain tight tolerances during the manufacturing process to ensure accurate alignment of layers and precise registration of circuit features. This helps prevent electrical shorts and ensures consistent performance.
- Encapsulation and Protection: Encapsulate the MIS with a protective layer or conformal coating to safeguard against environmental factors such as moisture, dust, and mechanical stress. This enhances the durability and reliability of the device.
- Testing and Quality Control: Implement rigorous testing procedures to validate the functionality and performance of the MIS-based electronic device. Conduct electrical testing, thermal cycling, and reliability testing to identify and address any issues early in the design process.
By adhering to these design guidelines, engineers can effectively harness the capabilities of MIS technology to develop compact, high-performance electronic devices with improved functionality and reliability.
What is the Molded Interconnect Substrate (MIS) Fabrication Process?
The fabrication process of Molded Interconnect Substrate (MIS) involves several key steps to create a three-dimensional (3D) substrate with integrated circuitry. Here’s a typical fabrication process:
- Substrate Preparation: The process starts with the preparation of a thermoplastic substrate material, such as liquid crystal polymer (LCP) or polyethylene terephthalate (PET). The substrate is typically in the form of a flat sheet or film.
- Molding: The prepared substrate material is molded into the desired shape using injection molding or compression molding techniques. The mold defines the final shape and features of the MIS, including any surface contours and recesses for components.
- Surface Preparation:After molding, the surface of the substrate is prepared for the application of conductive traces and vias. This may involve cleaning, surface activation, and the application of adhesion-promoting treatments to ensure proper adhesion of the conductive materials.
- Conductive Traces Formation: Conductive traces are formed on the surface of the substrate using various techniques such as laser ablation, printing (screen printing, inkjet printing), or plating. These traces define the electrical pathways for connecting components and carrying signals.
- Via Formation: Vias, which are holes drilled or formed through the substrate, are created to establish electrical connections between different layers of the MIS. Depending on the complexity of the design, vias can be formed using laser drilling, mechanical drilling, or chemical etching techniques.
- Component Attachment: Electronic components such as integrated circuits (ICs), resistors, capacitors, and LEDs are attached to the surface of the MIS using surface mount technology (SMT) or other bonding methods. The components are positioned and soldered onto the conductive traces to establish electrical connections.
- Encapsulation: Once all components are attached and the electrical connections are made, the MIS may be encapsulated with a protective layer or conformal coating to enhance durability and reliability. This layer also provides insulation against environmental factors such as moisture, dust, and mechanical stress.
- Testing and Inspection: The fabricated MIS undergoes rigorous testing and inspection to verify functionality, electrical continuity, and reliability. This may include electrical testing, thermal cycling, visual inspection, and other quality control measures to ensure the MIS meets performance specifications.
By following these fabrication steps, manufacturers can produce Molded Interconnect Substrates that enable the integration of complex circuitry into compact and lightweight electronic devices, driving innovation in various industries.
How do you manufacture a Molded Interconnect Substrate (MIS)?
Manufacturing a Molded Interconnect Substrate (MIS) involves a series of steps to create a substrate with integrated circuitry. Here’s a general overview of the manufacturing process:
- Substrate Material Selection: Choose a suitable thermoplastic material such as liquid crystal polymer (LCP) or polyethylene terephthalate (PET) for the substrate. The material should have good mechanical properties, thermal stability, and compatibility with manufacturing processes.
- Molding: The substrate material is molded into the desired shape using techniques like injection molding or compression molding. The mold defines the final shape and features of the MIS, including any surface contours and recesses for components.
- Surface Preparation: After molding, the surface of the substrate is prepared for the application of conductive traces and vias. This may involve cleaning, surface activation, and the application of adhesion-promoting treatments to ensure proper adhesion of the conductive materials.
- Conductive Traces Formation: Conductive traces are formed on the surface of the substrate using techniques such as laser ablation, printing (screen printing, inkjet printing), or plating. These traces define the electrical pathways for connecting components and carrying signals.
- Via Formation: Vias, which are holes drilled or formed through the substrate, are created to establish electrical connections between different layers of the MIS. Depending on the complexity of the design, vias can be formed using laser drilling, mechanical drilling, or chemical etching techniques.
- Component Attachment: Electronic components such as integrated circuits (ICs), resistors, capacitors, and LEDs are attached to the surface of the MIS using surface mount technology (SMT) or other bonding methods. The components are positioned and soldered onto the conductive traces to establish electrical connections.
- Encapsulation: Once all components are attached and the electrical connections are made, the MIS may be encapsulated with a protective layer or conformal coating to enhance durability and reliability. This layer also provides insulation against environmental factors such as moisture, dust, and mechanical stress.
- Testing and Inspection: The fabricated MIS undergoes rigorous testing and inspection to verify functionality, electrical continuity, and reliability. This may include electrical testing, thermal cycling, visual inspection, and other quality control measures to ensure the MIS meets performance specifications.
By following these manufacturing steps, companies can produce Molded Interconnect Substrates that enable the integration of complex circuitry into compact and lightweight electronic devices, driving innovation in various industries.
How much should a Molded Interconnect Substrate (MIS) cost?
The cost of a Molded Interconnect Substrate (MIS) can vary widely depending on factors such as the complexity of the design, the materials used, the manufacturing processes involved, and the volume of production. Generally, MIS tend to be more expensive than traditional printed circuit boards (PCBs) due to their specialized fabrication techniques and the integration of three-dimensional (3D) circuitry.
For a basic MIS design with simple circuitry and low volume production, the cost could range from a few dollars to tens of dollars per unit. However, for more complex MIS designs with advanced features, high-performance materials, and larger production volumes, the cost per unit could be significantly higher.
It’s essential for manufacturers to carefully consider the cost implications at each stage of the MIS development and production process, including substrate material selection, fabrication techniques, component sourcing, testing, and quality control. By optimizing the design and manufacturing processes, companies can help minimize costs while ensuring the MIS meets performance requirements and reliability standards.
Ultimately, the cost of a Molded Interconnect Substrate will be determined by a combination of factors, and it’s important for manufacturers to balance cost considerations with the desired functionality, performance, and reliability of the final product.
What is the Molded Interconnect Substrate (MIS) base material?
The base material used for Molded Interconnect Substrates (MIS) is typically a thermoplastic polymer. Two common materials used for MIS substrates are:
- Liquid Crystal Polymer (LCP): LCP is a high-performance thermoplastic with excellent mechanical, electrical, and thermal properties. It offers good dimensional stability, high temperature resistance, low moisture absorption, and high dielectric strength, making it well-suited for MIS applications.
- Polyethylene Terephthalate (PET): PET is another thermoplastic polymer commonly used as a substrate material for MIS. It is known for its high strength, stiffness, and chemical resistance. PET substrates are often used in applications where cost-effectiveness and ease of processing are priorities.
Both LCP and PET substrates can be molded into complex shapes and feature integrated circuitry, making them suitable for the production of compact and lightweight electronic devices. The choice between LCP and PET depends on factors such as performance requirements, cost considerations, and compatibility with manufacturing processes.
Which company makes Molded Interconnect Substrate (MIS)?
Molded Interconnect Substrates (MIS) are a type of technology that can be manufactured by multiple companies. These companies are typically electronics manufacturers or suppliers of electronic components, possessing specialized manufacturing facilities and technical teams to produce MIS. For example, well-known electronic manufacturing companies, printed circuit board (PCB) manufacturers, and specialized MIS manufacturers may all offer MIS products.
As for our company, we have advanced manufacturing equipment and technology to produce Molded Interconnect Substrates. Our manufacturing process combines advanced material processing techniques with precise manufacturing processes to ensure the production of high-quality, high-performance MIS products.
Our manufacturing process typically includes the following steps:
- Substrate Material Selection: We choose high-quality thermoplastic polymers as the substrate material for MIS, such as Liquid Crystal Polymer (LCP) or Polyethylene Terephthalate (PET), to ensure the product has excellent mechanical properties, thermal stability, and electrical performance.
- Molding Manufacturing: We use advanced injection molding or compression molding technology to shape the substrate material into the desired form, including complex three-dimensional structures and surface features.
- Conductive Trace Formation: We employ precise manufacturing processes to form conductive traces on the substrate surface, which can involve techniques such as laser cutting, printing, or plating, ensuring conductivity and reliability.
- Via Formation: We create vias in the substrate using techniques such as drilling or chemical etching to establish electrical connections between different layers.
- Component Installation: We use Surface Mount Technology (SMT) or other bonding methods to install electronic components onto the surface of the MIS, ensuring correct component placement and reliable electrical connections.
- Encapsulation Protection: Finally, we may encapsulate the MIS with a protective layer or coating to shield the product from environmental influences, enhancing its durability and reliability.
Through our company’s professional manufacturing capabilities and rigorous quality control standards, we can produce high-quality Molded Interconnect Substrates that meet customer requirements, providing customized solutions and meeting the design needs of various electronic devices.
What are the 7 qualities of good customer service?
Good customer service is characterized by several key qualities that contribute to a positive experience for customers. Here are seven qualities of good customer service:
- Responsiveness: Good customer service involves being prompt and attentive to customer inquiries, requests, and concerns. Responding to customers in a timely manner demonstrates respect for their time and shows that their needs are valued.
- Empathy: Empathy involves understanding and acknowledging the feelings, perspectives, and needs of customers. Effective customer service representatives demonstrate empathy by actively listening to customers, expressing understanding of their concerns, and showing genuine care and concern for their well-being.
- Clear Communication: Clear communication is essential for providing good customer service. Customer service representatives should communicate information in a clear, concise, and understandable manner, avoiding jargon or technical language that may confuse customers. They should also ensure that customers understand the information provided and are aware of any next steps or actions required.
- Problem-Solving Skills: Good customer service involves effectively addressing customer issues, concerns, and complaints. Customer service representatives should possess strong problem-solving skills to identify and resolve customer problems in a timely and efficient manner. They should be proactive in finding solutions and taking ownership of customer issues until they are satisfactorily resolved.
- Professionalism: Professionalism is crucial for creating a positive impression and building trust with customers. Customer service representatives should conduct themselves in a professional manner at all times, demonstrating courtesy, respect, and integrity in their interactions with customers. They should also adhere to company policies and procedures while representing the organization positively.
- Flexibility: Good customer service requires flexibility and adaptability to meet the diverse needs and preferences of customers. Customer service representatives should be willing to accommodate customer requests, preferences, and special circumstances whenever possible. They should also be open to feedback and willing to adjust their approach to better serve customers.
- Follow-Up and Follow-Through: Good customer service extends beyond the initial interaction with customers. Customer service representatives should follow up with customers to ensure that their needs have been met and their issues have been resolved satisfactorily. They should also follow through on any promises or commitments made to customers, demonstrating reliability and accountability.
By embodying these qualities, organizations can deliver exceptional customer service experiences that foster loyalty, satisfaction, and positive word-of-mouth recommendations.
FAQs (Frequently Asked Questions)
What is a Molded Interconnect Substrate (MIS)?
A Molded Interconnect Substrate (MIS) is a type of substrate used in electronics manufacturing that integrates both structural support and electrical circuitry into a single component. It allows for the creation of compact and lightweight electronic devices with complex three-dimensional (3D) circuitry.
How is an MIS different from a traditional printed circuit board (PCB)?
Unlike traditional PCBs, which consist of separate layers of substrate and conductive traces, MIS integrates circuitry directly into the substrate material. This allows for more compact designs, reduced weight, and improved electrical performance.
What are the advantages of using MIS in electronic devices?
Some advantages of using MIS include reduced size and weight of electronic devices, improved electrical performance due to shorter interconnect lengths, enhanced design flexibility, and the ability to integrate complex 3D circuitry.
What materials are commonly used for MIS?
Common materials used for MIS substrates include liquid crystal polymer (LCP) and polyethylene terephthalate (PET). These thermoplastic polymers offer good mechanical properties, thermal stability, and compatibility with manufacturing processes.
What are the key manufacturing processes involved in producing MIS?
The manufacturing process for MIS typically involves substrate molding, conductive trace formation, via formation, component attachment, encapsulation, and testing. These processes may vary depending on the specific design requirements and production techniques used.
What types of electronic devices commonly use MIS?
MIS technology is used in a wide range of electronic devices, including smartphones, tablets, wearables, automotive electronics, medical devices, and more. Any device that can benefit from compact size, lightweight design, and integrated circuitry may utilize MIS.
What considerations should be taken into account when designing with MIS?
When designing with MIS, factors such as substrate material selection, circuit layout and design, component placement, trace width and spacing, via design and placement, alignment and tolerances, and encapsulation and protection should be carefully considered to ensure optimal performance and reliability.
Are there any limitations or challenges associated with using MIS?
While MIS offers many benefits, there may be challenges related to cost, design complexity, manufacturing processes, and compatibility with existing technologies. It’s important for designers and manufacturers to address these challenges through careful planning and innovation.