MIS Package Substrate Manufacturer
MIS Package Substrate Manufacturer,MIS Package Substrate is a multi-layer integrated services (MIS) packaging substrate designed for high-performance electronic components. Utilizing advanced materials and manufacturing processes, it delivers excellent thermal management and electrical performance, suitable for high-density and complex circuit layouts. MIS Package Substrate typically integrates high-density interconnect technologies, supporting various packaging and chip integration methods such as BGA and CSP, to meet modern electronic devices’ requirements for miniaturization, high-speed signal transmission, and reliability. Widely applied in telecommunications, computing, consumer electronics, and automotive electronics, it provides crucial support and reliability for a variety of high-performance applications.
What is MIS Package Substrate?
A MIS (Mitsubishi Interconnect Substrate) Package Substrate refers to a specialized type of substrate used in semiconductor packaging. Mitsubishi Electric Corporation manufactures these substrates, which are known for their high reliability and performance in electronic devices. MIS substrates are designed to provide excellent thermal management, electrical insulation, and mechanical support for semiconductor chips and other electronic components. They are crucial in applications where heat dissipation and signal integrity are critical, such as in power modules, RF (Radio Frequency) devices, and high-performance computing.
These substrates are typically made using advanced ceramic materials and manufacturing processes to ensure precise dimensional control and consistent performance. They often feature integrated circuit patterns, vias, and metallization layers tailored to specific electrical and thermal requirements. MIS Package Substrates play a vital role in enhancing the overall functionality and reliability of electronic devices by providing a stable platform for semiconductor integration and interconnection.
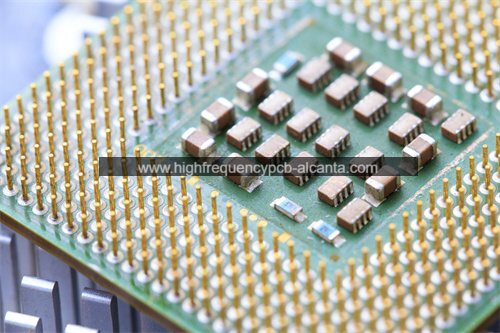
MIS Package Substrate Manufacturer
What are MIS Package Substrate Design Guidelines?
Design guidelines for MIS (Mitsubishi Interconnect Substrate) Package Substrates typically include several key considerations to ensure optimal performance and reliability. Here are some common guidelines:
- Material Selection: Choose appropriate ceramic materials (such as alumina or aluminum nitride) based on thermal conductivity, coefficient of thermal expansion (CTE), and dielectric properties to match the requirements of the application.
- Layer Configuration: Design the substrate with the necessary number of layers to accommodate signal routing, power distribution, and thermal management. Consider the layer stack-up carefully to minimize signal interference and optimize thermal dissipation.
- Signal Integrity: Ensure controlled impedance for high-speed signal lines by carefully designing trace widths, spacing, and via structures. Use impedance calculation tools to verify signal integrity requirements.
- Thermal Management: Incorporate thermal vias and heat sinks strategically to enhance heat dissipation from active components. Place critical components in areas with adequate airflow or thermal paths.
- Mechanical Considerations: Design the substrate to withstand mechanical stresses during handling and operation. Ensure adequate support for components and consider the substrate’s mechanical strength to prevent warping or cracking.
- Manufacturability: Optimize the design for manufacturability by considering the capabilities of the fabrication process (such as lithography, metallization, and bonding). Minimize complexity where possible to reduce production costs and improve yield.
- Reliability: Ensure the substrate design meets reliability standards for temperature cycling, mechanical shock, and vibration. Perform simulations and testing to validate the design under expected operating conditions.
- Interconnection Technology: Choose appropriate bonding and interconnection methods (such as wire bonding, flip-chip bonding, or soldering) based on the specific requirements of the semiconductor devices and the substrate material.
- Environmental Considerations:Consider environmental factors such as humidity, chemical exposure, and thermal cycling in the substrate design to ensure long-term reliability and performance stability.
By following these design guidelines, engineers can optimize the performance, reliability, and manufacturability of MIS Package Substrates for various electronic applications, ranging from consumer electronics to automotive and industrial systems.
What is the MIS Package Substrate Fabrication Process?
The fabrication process of MIS (Mitsubishi Interconnect Substrate) Package Substrates typically involves several key steps to create a reliable and functional substrate for semiconductor packaging. Here’s an overview of the general fabrication process:
- Substrate Material Selection: The process begins with selecting the appropriate ceramic material, such as alumina (Al2O3) or aluminum nitride (AlN), based on the application’s thermal, electrical, and mechanical requirements.
- Substrate Preparation: The ceramic substrate material is prepared by cutting it into the desired size and shape, followed by surface preparation to ensure cleanliness and smoothness for subsequent processing steps.
- Green Sheet Production (LTCC or HTCC): For LTCC (Low Temperature Co-Fired Ceramic) or HTCC (High Temperature Co-Fired Ceramic) substrates, ceramic powders are mixed with binders and solvents to form a slurry. This slurry is cast into thin sheets (green sheets) using a doctor blade or tape-casting process. Each green sheet contains circuit patterns, vias, and other features.
- Layer Stacking and Lamination:Multiple green sheets, each with specific circuit patterns and vias, are stacked in the desired sequence to form a multilayer structure. The layers are aligned precisely to ensure accurate registration of vias and interconnections. The stacked green sheets are then laminated under controlled pressure and temperature to bond them into a monolithic structure.
- Via Formation: After lamination, via holes are punched, drilled, or laser-ablated through the stacked layers where electrical connections (vias) are needed between different layers. These vias will later be filled with conductive materials to establish electrical continuity.
- Metallization and Conductor Patterning: Conductive materials, such as thick-film pastes or thin-film deposition techniques (e.g., sputtering, evaporation), are used to deposit metal layers on the substrate surfaces. These metal layers form circuit traces, bonding pads, and other interconnect features according to the substrate design.
- Firing (Sintering): The substrate undergoes a firing process in a controlled atmosphere kiln. During firing, the green sheets and deposited materials undergo chemical and physical transformations, resulting in densification and bonding of the ceramic layers. For HTCC, firing temperatures are higher to achieve denser and more robust substrates suitable for high-temperature applications.
- Surface Finishing: After firing, the substrate surface may undergo additional processing steps such as polishing, planarization, or applying protective coatings to ensure smoothness, cleanliness, and protection against environmental factors.
- Quality Control and Testing: Throughout the fabrication process, stringent quality control measures are implemented to verify dimensions, material properties, and electrical performance. Substrates are tested for reliability under various environmental conditions (temperature cycling, humidity, mechanical stress) to ensure they meet specified standards.
- Assembly and Packaging: Once fabricated and tested, MIS Package Substrates are ready for assembly with semiconductor chips, passive components, and other electronic devices using appropriate bonding techniques (e.g., wire bonding, flip-chip bonding, soldering). This assembly process completes the integration of electronic components into the final electronic module or system.
By following these steps, manufacturers can produce MIS Package Substrates that offer high reliability, thermal performance, and electrical connectivity for a wide range of electronic applications, including automotive, telecommunications, and industrial equipment.
How do you manufacture a MIS Package Substrate?
Manufacturing a MIS (Mitsubishi Interconnect Substrate) Package Substrate involves a series of systematic processes designed to achieve precise dimensions, reliable electrical connections, and optimal thermal management. Here’s a detailed outline of the manufacturing process:
- Material Selection: Choose ceramic materials like alumina (Al2O3) or aluminum nitride (AlN) based on thermal conductivity, coefficient of thermal expansion (CTE), and dielectric properties suitable for the application’s requirements.
- Substrate Preparation: Cut the ceramic material into the desired shape and size blanks. Clean and prepare the substrate surfaces to ensure they are free from contaminants.
- Green Sheet Production (LTCC or HTCC):
– LTCC: Mix ceramic powders with binders and solvents to form a slurry. Cast the slurry into thin green sheets using tape-casting or doctor-blade techniques.
– HTCC: Prepare ceramic powders with binders and form them into sheets. Stack and laminate these sheets to form the substrate body.
- Layer Stacking and Lamination: Arrange multiple green sheets in the desired layer sequence, aligning them precisely to ensure proper registration of vias and interconnects. Apply heat and pressure to laminate the green sheets into a monolithic structure.
- Via Formation: Punch, drill, or laser-ablate holes through the laminated stack where vias are required for electrical connections between layers.
- Metallization and Conductor Patterning: Deposit conductive materials (e.g., thick-film pastes, thin-film deposition) onto the substrate surfaces to create circuit traces, bonding pads, and other interconnect features according to the substrate design.
- Firing (Sintering):
– LTCC: Fire the substrate in a controlled atmosphere kiln at lower temperatures (typically below 1000°C) to densify the ceramic layers and activate the conductive materials.
– HTCC: Fire at higher temperatures (above 1000°C) to achieve denser ceramic layers suitable for high-temperature applications.
- Surface Finishing: After firing, perform post-processing steps such as polishing, planarization, or applying protective coatings to enhance surface smoothness and protect against environmental factors.
- Quality Control and Testing: Conduct rigorous quality checks throughout the manufacturing process to verify dimensional accuracy, material integrity, and electrical performance. Test substrates for reliability under various conditions (temperature cycling, humidity, mechanical stress).
- Assembly and Packaging: Once validated, assemble MIS Package Substrates with semiconductor chips, passive components, and other electronic devices using appropriate bonding methods (e.g., wire bonding, flip-chip bonding, soldering).
By meticulously following these manufacturing steps, MIS Package Substrates are produced to meet stringent performance requirements for applications in automotive, telecommunications, aerospace, and industrial electronics, providing robust electrical connectivity and effective thermal management.
How much should a MIS Package Substrate cost?
The cost of a MIS (Mitsubishi Interconnect Substrate) Package Substrate can vary widely depending on several factors, including:
- Material: The type of ceramic material used (e.g., alumina, aluminum nitride) and its quality significantly impacts cost. Higher purity and specific properties required for thermal conductivity and electrical insulation can increase material costs.
- Complexity: The complexity of the substrate design, including the number of layers, density of vias, and intricacy of metallization patterns, affects manufacturing costs. More complex designs typically require more processing steps and higher precision, which can increase costs.
- Size and Thickness: Larger substrates or those with specific thickness requirements may incur higher material and processing costs due to increased material usage and handling complexity.
- Manufacturing Process: The fabrication method (e.g., LTCC, HTCC) and the level of automation or manual labor involved in substrate production influence costs. HTCC substrates, which require higher firing temperatures and more precise manufacturing processes, generally cost more than LTCC substrates.
- Volume and Order Size: Economies of scale apply—larger production volumes often result in lower per-unit costs due to efficiencies in material procurement, manufacturing setup, and process optimization.
- Additional Features: Optional features such as special surface finishes, customized metallization schemes, or advanced testing and qualification procedures can add to the overall cost.
- Supplier and Market Conditions: Pricing can also vary based on the supplier’s pricing strategy, market demand, and competitive landscape within the industry.
To provide a specific cost estimate, it would typically require a detailed assessment of the substrate’s specifications, volume requirements, and supplier quotations. Generally, MIS Package Substrates are considered a significant investment in electronic packaging due to their high performance, reliability, and specialized manufacturing processes.
What is MIS Package Substrate base material?
The base material used for MIS (Mitsubishi Interconnect Substrate) Package Substrates typically consists of advanced ceramic materials. Two common types of ceramic materials used as base materials for MIS substrates are:
- Alumina (Al2O3):
– Alumina ceramic substrates are widely used due to their excellent electrical insulation properties, high thermal conductivity (compared to other ceramics), and good mechanical strength.
– They are suitable for a wide range of applications, including those requiring high-frequency operation and thermal management.
- Aluminum Nitride (AlN):
– Aluminum nitride is known for its exceptional thermal conductivity, even higher than alumina, making it ideal for applications requiring efficient heat dissipation.
– AlN substrates offer good electrical insulation properties and are often chosen for high-power applications, RF devices, and other heat-sensitive electronic components.
These ceramic materials are selected based on the specific requirements of the application, such as thermal management, electrical insulation, mechanical strength, and dimensional stability. They undergo precise manufacturing processes to form the substrate body, including shaping, lamination of green sheets (for LTCC or HTCC processes), via formation, metallization, firing (sintering), and surface finishing. This results in a robust substrate that supports the integration and interconnection of semiconductor chips and other electronic components in various high-performance applications.
Which company makes MIS Package Substrates?
MIS (Mitsubishi Interconnect Substrate) Package Substrates are produced by Mitsubishi Electric Corporation. Mitsubishi Electric Corporation is a global leader in manufacturing electronic and electrical equipment, with expertise in semiconductor technology and packaging. MIS Package Substrates are a crucial component of their packaging technology, used primarily in the manufacture of high-performance electronic devices and modules.
Our company also manufactures similar MIS Package Substrates. As a company focused on electronic packaging technology, we have advanced manufacturing equipment and a skilled technical team capable of providing high-quality ceramic substrates and packaging solutions. We select premium ceramic materials such as alumina and aluminum nitride to ensure excellent electrical insulation, thermal conductivity, and mechanical strength in our products. Our manufacturing process adheres strictly to international standards, including precise lamination, accurate via formation, high-temperature firing, and other processes to ensure each product meets our customers’ technical and quality requirements.
In addition to traditional LTCC (Low Temperature Co-Fired Ceramic) and HTCC (High Temperature Co-Fired Ceramic) manufacturing technologies, we also offer customized design and processing services tailored to specific customer needs. Whether in telecommunications, automotive, medical, or industrial sectors, we provide innovative solutions to optimize product performance and cost-effectiveness for our customers.
Through continuous technological innovation and quality management, we strive to be your trusted partner, delivering reliable MIS Package Substrates and exceptional customer service. If you would like to learn more about our capabilities and products, or explore potential collaborations, please feel free to contact us. We are committed to serving you with dedication and expertise.
What are the qualities of good customer service?
Good customer service is characterized by several key qualities that contribute to a positive experience for customers. Here are some essential qualities:
- Responsiveness: Being prompt in addressing customer inquiries, concerns, and requests demonstrates respect for their time and shows that their needs are a priority.
- Empathy: Showing empathy involves understanding and acknowledging the customer’s emotions and perspectives. It involves listening actively and responding with compassion and understanding.
- Clear Communication:Effective communication is crucial. This includes providing clear and concise information, actively listening to customers to understand their needs, and ensuring that messages are conveyed accurately.
- Knowledgeability: Having a deep understanding of the products or services offered allows customer service representatives to provide accurate information, answer questions, and offer relevant solutions.
- Problem-Solving Skills: Being able to resolve issues and address problems efficiently demonstrates competence and shows customers that their concerns are taken seriously and will be resolved effectively.
- Professionalism: Maintaining a professional demeanor and attitude, even in challenging situations, helps build trust and confidence with customers.
- Adaptability: Being adaptable means being flexible and able to adjust to different customer needs and preferences. It involves finding solutions that meet individual customer requirements.
- Positive Attitude: A positive attitude can greatly impact the customer’s experience. It involves being friendly, optimistic, and proactive in assisting customers.
- Consistency: Providing consistent service across all interactions and channels ensures that customers receive a reliable and cohesive experience every time they engage with the company.
- Follow-Up: Following up with customers after resolving an issue or completing a transaction shows commitment to their satisfaction and allows for feedback and further assistance if needed.
By embodying these qualities, companies can build strong customer relationships, enhance loyalty, and differentiate themselves in competitive markets.
FAQs
What is an MIS Package Substrate?
An MIS Package Substrate is a specialized ceramic substrate used in semiconductor packaging. It provides a stable platform for mounting semiconductor chips and components, offering features like electrical insulation, thermal management, and reliable interconnections.
What are the advantages of using MIS Package Substrates?
MIS Package Substrates offer several advantages including high thermal conductivity, excellent electrical insulation, mechanical durability, and compatibility with various packaging technologies. They are suitable for applications requiring efficient heat dissipation and reliable electrical performance.
What are the typical applications of MIS Package Substrates?
These substrates are used in a wide range of applications such as automotive electronics, telecommunications equipment, industrial machinery, aerospace systems, and power modules. They are particularly valued in high-power and high-frequency electronic devices.
What materials are used to manufacture MIS Package Substrates?
Common materials include alumina (Al2O3) and aluminum nitride (AlN). Alumina is known for its high mechanical strength and good electrical properties, while aluminum nitride offers superior thermal conductivity, making it suitable for high-power applications.
What are the different manufacturing processes for MIS Package Substrates?
Manufacturing processes can include LTCC (Low Temperature Co-Fired Ceramic) and HTCC (High Temperature Co-Fired Ceramic) techniques. These involve steps such as green sheet preparation, layer stacking, via formation, metallization, and firing (sintering) to achieve the desired substrate properties.
How do MIS Package Substrates compare to other types of substrates?
Compared to organic substrates like FR4 (Fiberglass-Reinforced Epoxy), MIS Package Substrates offer higher thermal conductivity, better mechanical stability, and enhanced reliability at higher operating temperatures. They are often chosen for demanding electronic applications.
What considerations are important when selecting MIS Package Substrates?
Key factors include thermal conductivity, coefficient of thermal expansion (CTE) matching with semiconductor materials, dimensional stability, electrical insulation properties, and compatibility with assembly processes like wire bonding or flip-chip bonding.