Minimum Trace&Clearance PCB Manufacturing
Minimum Trace&Clearance PCB Manufacturing,Minimum Trace & Clearance PCBs are specialized printed circuit boards designed with the smallest allowable width for conductive traces and the tiniest permissible gap between traces or other elements. These PCBs are essential for applications where space is at a premium or where signal integrity is paramount. By optimizing the use of available space and ensuring reliable electrical performance, Minimum Trace & Clearance PCBs enable the design of high-density circuits and high-frequency systems. They are commonly used in industries such as telecommunications, aerospace, automotive, and consumer electronics. Designing and manufacturing these PCBs require careful attention to detail, adherence to industry standards, and utilization of advanced fabrication techniques. The resulting PCBs offer benefits such as maximizing space utilization, improving signal integrity, reducing electromagnetic interference, and enabling the miniaturization of electronic devices. Overall, Minimum Trace & Clearance PCBs play a crucial role in pushing the boundaries of electronic design and innovation.
What is a Minimum Trace&Clearance PCB?
A Minimum Trace and Clearance PCB (Printed Circuit Board) refers to the smallest width for traces (conducting paths) and the smallest gap between traces or between a trace and any other object (clearance) allowed in the design of a PCB.
This specification is crucial in PCB design because it affects the electrical performance and reliability of the circuit. The trace width and clearance are typically determined by the requirements of the components used in the circuit, the electrical characteristics of the signals being carried, and manufacturing constraints.
Designing with minimum trace and clearance specifications can be important for high-density applications where space is limited, or for high-frequency circuits where signal integrity is critical. However, it’s essential to balance the need for compactness with ensuring that the electrical performance and reliability of the circuit are not compromised. If traces are too narrow or clearance is too small, it can lead to issues such as signal degradation, crosstalk, and even electrical shorts.
Manufacturers and designers need to adhere to industry standards and guidelines to ensure that the PCB design meets the required trace width and clearance specifications while still achieving the desired performance and reliability. These standards may vary depending on the specific application and the technology being used in the PCB fabrication process.
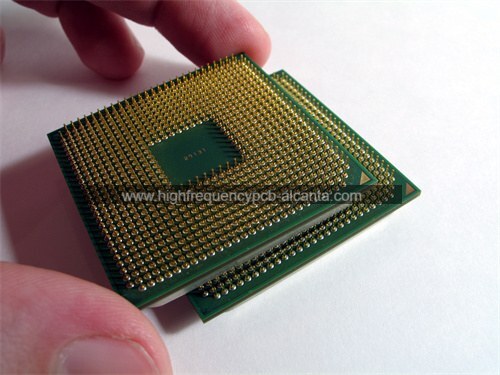
Minimum Trace&Clearance PCB Manufacturing
What are the Minimum Trace&Clearance PCB Design Guidelines?
The minimum trace and clearance PCB design guidelines vary depending on factors such as the manufacturing process, the specific requirements of the components and signals in the circuit, and industry standards. However, here are some general guidelines commonly followed:
- Manufacturing Process Constraints: The minimum trace width and clearance should be in line with the capabilities of the PCB fabrication process being used. Consult with the manufacturer to determine the limitations and capabilities of their process.
- Signal Integrity Requirements: Ensure that the trace width and clearance meet the signal integrity requirements of the circuit. Factors such as signal frequency, impedance matching, and signal integrity standards (such as USB, HDMI, or Ethernet) will influence the trace and clearance specifications.
- Voltage and Current Requirements: Consider the voltage and current levels in the circuit when determining trace width and clearance. Higher voltages and currents may require wider traces and larger clearances to prevent arcing or electrical breakdown.
- Environmental Factors: Take into account environmental conditions such as temperature, humidity, and vibration. These factors can affect the reliability of the PCB and may influence the minimum trace and clearance requirements.
- Industry Standards: Refer to relevant industry standards and guidelines for PCB design, such as those provided by the IPC (Association Connecting Electronics Industries). These standards often specify minimum trace widths, clearances, and other design parameters based on the application and technology used.
- Design for Manufacturability (DFM): Design the PCB with manufacturability in mind. Avoid overly tight spacing between traces and components that may be difficult or costly to fabricate.
- Margin for Error: Provide a margin of safety when determining trace width and clearance to account for variations in manufacturing tolerances and environmental conditions.
- Simulation and Testing: Use simulation tools and conduct testing to verify the electrical performance and reliability of the PCB design, including the chosen trace width and clearance.
By following these guidelines and considering the specific requirements of your design and manufacturing process, you can ensure that your PCB design meets the necessary minimum trace and clearance specifications for optimal performance and reliability.
What is the Minimum Trace&Clearance PCB Fabrication Process?
The minimum trace and clearance PCB fabrication process involves several steps to ensure that the designed trace widths and clearances are accurately implemented during manufacturing. Here’s a general overview of the process:
- Design Verification: Before fabrication begins, the PCB design is carefully reviewed to ensure that the trace widths and clearances meet the required specifications. Design verification may involve using specialized software tools to check for compliance with industry standards and design rules.
- Photoresist Application: The fabrication process typically starts with the application of a photoresist material onto a copper-clad substrate. The substrate is typically made of materials like FR-4 (flame-retardant fiberglass epoxy laminate) or other suitable materials.
- Exposure and Development: A photomask containing the circuit pattern is placed over the photoresist-coated substrate. The substrate is then exposed to ultraviolet (UV) light, which passes through the mask, exposing the photoresist in the desired pattern. After exposure, the substrate is developed to remove the unexposed photoresist, leaving behind the patterned photoresist layer.
- Etching: The substrate is then subjected to an etching process, typically using chemicals such as ferric chloride or ammonium persulfate. The etchant removes the exposed copper, leaving behind the patterned copper traces that correspond to the circuit design. The etching process must be controlled precisely to ensure that the trace widths are accurately maintained.
- Strip Resist: After etching, any remaining photoresist is stripped away from the substrate using solvents or other methods, leaving behind the patterned copper traces on the substrate surface.
- Drilling:Holes are drilled into the substrate at locations specified by the PCB design, typically using automated drilling machines. These holes are used for through-hole component insertion and for establishing electrical connections between different layers of the PCB in the case of multilayer boards.
- Plating and Surface Finishing: To improve the conductivity and protect the copper traces, the PCB may undergo a plating process. This involves depositing a thin layer of metal (such as tin, gold, or silver) onto the exposed copper surfaces. Surface finishing techniques such as hot air leveling (HASL), electroless nickel immersion gold (ENIG), or immersion silver may also be applied depending on the desired performance and requirements of the PCB.
- Quality Control and Testing: Throughout the fabrication process, quality control measures are implemented to ensure that the fabricated PCBs meet the required specifications. Testing methods such as electrical continuity testing, impedance testing, and visual inspection are commonly used to verify the integrity and quality of the finished PCBs.
By following these steps carefully and maintaining tight process controls, PCB manufacturers can achieve the minimum trace and clearance specifications required by the design, ensuring the electrical performance and reliability of the finished PCBs.
How do you manufacture a Minimum Trace&Clearance PCB?
Manufacturing a Minimum Trace & Clearance PCB requires careful attention to detail and precision throughout the fabrication process to ensure that the designed specifications are met. Here’s a step-by-step guide on how to manufacture such a PCB:
- Design Preparation: Start with a PCB design that meets the desired trace widths and clearances. Use PCB design software to create the layout, ensuring that the traces and clearances comply with the specifications required for the application.
- Material Selection: Choose high-quality PCB substrate materials that are suitable for achieving the desired trace and clearance specifications. Common materials include FR-4, which is a flame-retardant fiberglass epoxy laminate.
- Photoresist Application: Apply a layer of photoresist material onto the substrate surface. This photoresist layer will be used to define the pattern of the copper traces on the PCB.
- Exposure and Development: Place a photomask containing the desired circuit pattern over the photoresist-coated substrate. Expose the substrate to UV light, which passes through the mask, exposing the photoresist in the pattern of the traces. After exposure, develop the substrate to remove the unexposed photoresist, leaving behind the patterned photoresist layer.
- Etching: Subject the substrate to an etching process using chemicals such as ferric chloride or ammonium persulfate. The etchant removes the exposed copper, leaving behind the patterned copper traces on the substrate surface. Control the etching process carefully to ensure that the trace widths are accurate and consistent.
- Strip Resist: Remove any remaining photoresist from the substrate using solvents or other stripping methods. This step exposes the copper traces for further processing.
- Drilling: Use precision drilling equipment to drill holes into the substrate at locations specified by the PCB design. These holes are used for through-hole component insertion and for establishing electrical connections between different layers of the PCB in the case of multilayer boards.
- Plating and Surface Finishing: Plate the exposed copper traces with a thin layer of metal (such as tin, gold, or silver) to improve conductivity and protect against oxidation. Apply surface finishing techniques such as hot air leveling (HASL), electroless nickel immersion gold (ENIG), or immersion silver to enhance the performance and durability of the PCB.
- Quality Control and Testing: Conduct thorough quality control checks and testing throughout the manufacturing process to ensure that the PCB meets the required specifications. This may include electrical continuity testing, impedance testing, and visual inspection of the finished PCBs.
- Final Inspection and Packaging: Once manufacturing is complete, inspect the finished PCBs for any defects or inconsistencies. Package the PCBs according to the requirements of the customer or end application, ensuring that they are protected during shipping and handling.
By following these steps carefully and maintaining strict quality control measures, manufacturers can produce Minimum Trace & Clearance PCBs that meet the desired specifications for electrical performance and reliability.
How much should a Minimum Trace&Clearance PCB cost?
The cost of a Minimum Trace & Clearance PCB can vary widely depending on several factors, including:
- Size and Complexity: The physical size and complexity of the PCB design significantly influence the cost. Larger PCBs with more intricate layouts and densely packed components generally cost more to manufacture.
- Number of Layers: The number of layers in the PCB affects the manufacturing process complexity and material cost. Multilayer PCBs typically cost more than single or double-layer boards.
- Material Selection: The choice of materials, such as substrate type and surface finish, can impact the cost. High-quality materials or specialized materials may increase the overall cost of the PCB.
- Trace Width and Clearance: PCBs with tighter trace widths and clearances may require more precise manufacturing processes, which can contribute to higher costs.
- Manufacturing Volume: Economies of scale apply in PCB manufacturing, meaning that larger production quantities often result in lower per-unit costs. However, smaller production runs may incur higher setup and tooling costs.
- Manufacturing Technology:Advanced manufacturing technologies, such as HDI (High-Density Interconnect) or flexible PCB fabrication, may involve higher costs compared to standard processes.
- Lead Time: Urgent orders or short lead times may incur additional charges for expedited manufacturing and shipping.
- Supplier and Location: PCB fabrication costs can vary between different manufacturers and regions. Factors such as labor costs, overheads, and equipment investments can influence pricing.
As a rough estimate, the cost of a Minimum Trace & Clearance PCB can range from a few dollars for simple designs with basic requirements to hundreds or even thousands of dollars for complex, high-density PCBs with stringent specifications. For accurate pricing, it’s best to consult with PCB manufacturers or suppliers and provide detailed specifications of your design. They can provide quotes based on your specific requirements and volume.
What is Minimum Trace&Clearance PCB base material?
The base material for Minimum Trace & Clearance PCBs is typically chosen based on its electrical properties, mechanical strength, thermal characteristics, and cost-effectiveness. One of the most commonly used materials for PCB substrates is FR-4 (Flame Retardant-4), which is a type of fiberglass epoxy laminate.
FR-4 offers several desirable properties for PCB fabrication:
- Electrical Insulation: FR-4 provides excellent electrical insulation properties, which are essential for preventing short circuits between adjacent traces or layers.
- Mechanical Strength: FR-4 is relatively rigid and offers good mechanical strength, allowing it to withstand the stresses and strains encountered during PCB fabrication, assembly, and use.
- Thermal Stability: FR-4 exhibits good thermal stability, which is important for maintaining the integrity of the PCB at elevated temperatures encountered during soldering and operation.
- Cost-Effectiveness: FR-4 is widely available and relatively inexpensive compared to other high-performance substrate materials, making it a cost-effective choice for many PCB applications.
While FR-4 is commonly used for most PCB applications, other materials may be selected for specific requirements. For example, high-frequency applications may require substrates with low dielectric loss and low signal dispersion, leading to the use of materials such as Rogers Corporation’s RO4000 series or Isola’s I-Tera MT laminate. Similarly, flexible PCBs may use materials such as polyimide (PI) or liquid crystal polymer (LCP) for their flexibility and durability.
Ultimately, the choice of base material for Minimum Trace & Clearance PCBs depends on factors such as the specific requirements of the application, the desired electrical performance, mechanical constraints, and cost considerations.
Which company makes Minimum Trace&Clearance PCB?
Many PCB manufacturing companies are capable of producing PCBs that meet the minimum trace and clearance requirements. These companies include globally recognized manufacturers as well as specialized manufacturers focusing on high-performance and high-density PCBs. For example, companies like Sanmina, Flex, Jabil, as well as domestic companies like BYD Electronics and TSMC have the capability to produce PCBs that meet the minimum trace and clearance standards.
As for our company, we have advanced manufacturing equipment and technology to meet the strict requirements of customers for minimum trace and clearance PCBs. Our manufacturing process is designed in strict accordance with international standards and customer requirements to ensure the highest quality and performance of our products.
Our company’s strengths include:
- Advanced Manufacturing Equipment: We have advanced PCB production lines and manufacturing equipment to achieve high-precision circuit patterns and minimal clearance requirements.
- Rich Experience: We have an experienced team of engineers and technical staff who can provide professional technical support and advice to ensure smooth PCB design and manufacturing processes.
- Quality Assurance: We strictly adhere to quality management systems, conducting rigorous quality control at every stage from raw material procurement to production and delivery, ensuring that our products meet the highest quality standards.
- Customized Services: We provide customized solutions to meet the specific needs and requirements of our customers, ensuring that our products meet their minimum trace and clearance PCB requirements.
In conclusion, our company has the technical expertise, experience, and efficient production capacity to produce high-quality PCB products that meet the minimum trace and clearance standards, and we provide comprehensive technical support and services to our customers.
What are the 7 qualities of good customer service?
Good customer service is essential for building strong relationships with customers and ensuring satisfaction and loyalty. Here are seven qualities that characterize good customer service:
- Responsiveness:Good customer service involves promptly addressing customer inquiries, concerns, and requests. Being responsive means acknowledging customer communications in a timely manner and providing assistance or solutions promptly.
- Empathy: Empathy is the ability to understand and relate to the customer’s feelings, perspectives, and needs. Good customer service representatives demonstrate empathy by actively listening to customers, showing understanding, and expressing genuine concern for their issues or challenges.
- Professionalism: Professionalism is crucial in customer service interactions. It involves maintaining a courteous and respectful demeanor, communicating clearly and effectively, and adhering to company policies and standards. Professionalism instills confidence in customers and fosters trust in the company’s ability to resolve their issues.
- Knowledgeability: Good customer service representatives possess thorough knowledge of the company’s products, services, policies, and procedures. They can provide accurate information, answer questions, and offer relevant advice or recommendations to assist customers effectively.
- Adaptability: Customer service situations can vary widely, and good representatives are adaptable and flexible in their approach. They can adjust their communication style and problem-solving strategies to suit the individual needs and preferences of each customer.
- Proactiveness: Good customer service involves being proactive in identifying and addressing customer needs and issues before they escalate. Proactive representatives anticipate potential problems, offer proactive solutions or assistance, and follow up to ensure customer satisfaction.
- Problem-solving Skills: Effective problem-solving skills are essential for resolving customer issues and concerns efficiently. Good customer service representatives can analyze problems, identify root causes, and implement effective solutions that meet the customer’s needs and expectations.
By embodying these qualities, businesses can deliver exceptional customer service experiences that leave a positive impression on customers and contribute to long-term success and loyalty.
FAQs (Frequently Asked Questions)
What are Minimum Trace & Clearance PCBs?
Minimum Trace & Clearance PCBs refer to printed circuit boards designed with the smallest allowable width for conductive traces and the smallest permissible gap between traces or between a trace and any other object.
Why are Minimum Trace & Clearance PCBs important?
These PCBs are crucial for applications where space is limited or where signal integrity is critical, such as high-density circuits or high-frequency designs. They help optimize the use of available space and ensure reliable electrical performance.
What factors determine the minimum trace width and clearance for a PCB?
The minimum trace width and clearance are determined by factors such as the requirements of the components used in the circuit, the electrical characteristics of the signals being carried, manufacturing constraints, and industry standards.
What are the challenges of designing and manufacturing Minimum Trace & Clearance PCBs?
Challenges may include ensuring signal integrity, preventing crosstalk, avoiding electrical shorts, and balancing the need for compactness with maintaining performance and reliability.
Which industries commonly use Minimum Trace & Clearance PCBs?
These PCBs are used in a wide range of industries, including telecommunications, aerospace, automotive, medical devices, consumer electronics, and industrial automation.
What are some design guidelines for Minimum Trace & Clearance PCBs?
Design guidelines include adhering to industry standards, considering signal integrity requirements, selecting appropriate materials, and conducting thorough testing and simulation.
How do manufacturers ensure that Minimum Trace & Clearance PCBs meet specifications?
Manufacturers utilize advanced fabrication techniques, precise etching processes, and rigorous quality control measures to ensure that the PCBs meet the required trace width and clearance specifications.