Minimum Trace PCB Manufacturer
Minimum Trace PCB Manufacturer,Minimum Trace PCBs are a specialized type of printed circuit board designed with the narrowest possible conductive traces while still meeting stringent electrical and mechanical requirements. These PCBs are engineered for applications where space optimization is paramount, such as in compact electronic devices like smartphones, wearables, and IoT gadgets.
The design of Minimum Trace PCBs prioritizes efficient use of available space, allowing for increased component density and enhanced functionality in smaller form factors. Achieving narrow trace widths requires precise manufacturing processes and careful attention to signal integrity, impedance control, and thermal management.
Despite the challenges associated with their fabrication, Minimum Trace PCBs offer significant benefits. They enable the creation of smaller and lighter electronic devices without compromising performance, making them ideal for applications where size and weight limitations are critical considerations.
Overall, Minimum Trace PCBs represent the intersection of cutting-edge design, precision engineering, and innovative technology, driving advancements in miniaturization and pushing the boundaries of what’s possible in electronic device design.
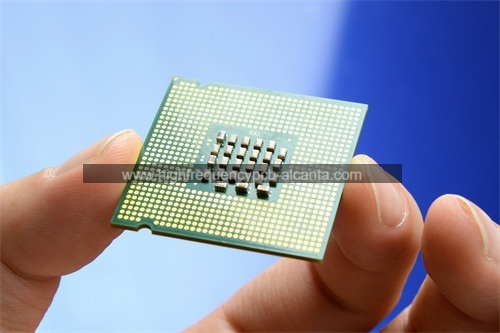
Minimum Trace PCB Manufacturer
What is a Minimum Trace PCB?
A Minimum Trace PCB, or Minimum Trace Printed Circuit Board, is a type of PCB design where the conductive traces (the pathways that carry electrical signals) are made as narrow as possible while still meeting the electrical and mechanical requirements of the circuit. The goal is to minimize the amount of space occupied by traces on the PCB, allowing for more compact and efficient designs.
These PCBs are often used in applications where space is limited, such as in small electronic devices like smartphones, wearables, and IoT devices. By reducing the width of the traces, designers can fit more components onto the PCB, enabling greater functionality in a smaller footprint.
However, designing and manufacturing Minimum Trace PCBs requires careful consideration of factors such as signal integrity, impedance control, and thermal management. Narrow traces can increase resistance and capacitance, affecting signal quality and introducing potential problems like crosstalk and signal distortion. Additionally, manufacturing processes must be precise to ensure that the narrow traces are accurately etched onto the PCB without defects.
Overall, Minimum Trace PCBs offer a balance between space efficiency and performance, making them essential in the development of compact electronic devices.
What are the Minimum Trace PCB Design Guidelines?
Designing a Minimum Trace PCB requires careful consideration of various factors to ensure optimal performance and reliability. Here are some key guidelines:
- Signal Integrity: Maintain signal integrity by keeping traces short and minimizing impedance mismatches. Use controlled impedance traces for high-speed signals to prevent signal degradation.
- Trace Width: Choose the narrowest trace width possible while considering factors such as current carrying capacity, impedance, and manufacturability. Common trace widths range from 4 to 6 mils (0.1 to 0.15 mm) for general signals.
- Clearance and Spacing: Maintain adequate clearance and spacing between traces to prevent electrical interference, crosstalk, and short circuits. Follow manufacturer guidelines for minimum clearance requirements.
- Layer Stackup: Optimize the layer stackup to accommodate the required trace widths while maintaining signal integrity and minimizing signal loss. Consider using additional signal layers for routing dense designs.
- Via Placement: Strategically place vias to minimize signal distortion and impedance changes. Use blind or buried vias when transitioning between layers to reduce signal reflections.
- Power Distribution: Design efficient power distribution networks (PDNs) with low impedance paths to minimize voltage drops and ensure stable power delivery to components. Use wider traces for power and ground lines to reduce resistance.
- Thermal Management: Consider thermal effects of narrow traces, especially in high-power applications. Use wider traces for high-current paths and incorporate thermal vias to dissipate heat efficiently.
- Manufacturability: Ensure that the design is manufacturable within the capabilities of your chosen fabrication process. Check for minimum feature sizes, tolerances, and alignment requirements.
- Design for Testability: Include test points and access points for debugging and testing purposes. Ensure that traces are accessible for probing without hindering signal integrity.
- Documentation: Provide comprehensive documentation including layout guidelines, layer stackup, design rules, and manufacturing notes to facilitate PCB fabrication and assembly.
By adhering to these guidelines, designers can create Minimum Trace PCBs that meet performance requirements while optimizing space utilization and maintaining reliability. However, it’s important to iterate and validate the design through simulations and prototyping to ensure successful implementation.
What is the Minimum Trace PCB Fabrication Process?
The fabrication process for Minimum Trace PCBs follows the standard steps involved in manufacturing printed circuit boards, with a focus on precision and accuracy to produce narrow traces. Here’s an overview of the typical fabrication process:
- Design: Begin with the PCB design using a PCB design software. Designers create the layout, define trace widths, component placement, and routing according to the design requirements and guidelines.
- Preparation of Substrate: The fabrication process starts with a substrate material, typically a rigid laminate such as FR-4 (fiberglass-reinforced epoxy). The substrate is cleaned and prepared for the next steps.
- Layer Alignment and Lamination: For multilayer PCBs, individual layers of substrate with copper foil bonded to them are aligned and then laminated together under heat and pressure. This forms the core laminate stackup.
- Copper Deposition: A thin layer of copper is deposited onto the substrate through a process such as electroplating. This forms the conductive layer that will become the traces and pads on the PCB.
- Photoresist Application: A layer of photoresist is applied to the copper surface. Photoresist is a light-sensitive material that will be used to transfer the PCB pattern onto the copper layer.
- Exposure and Development: The PCB design pattern is transferred onto the photoresist layer using a photographic process. UV light is shone through a mask containing the PCB pattern onto the photoresist-coated copper layer. The exposed photoresist is then developed, leaving behind the patterned photoresist layer.
- Etching: The PCB is submerged in an etchant solution, which removes the unprotected copper not covered by the developed photoresist. This etching process creates the desired traces and pads on the PCB.
- Strip and Clean: The remaining photoresist is stripped away, leaving behind the copper traces and pads on the substrate. The PCB is cleaned to remove any residue from the fabrication process.
- Drilling: Holes are drilled into the PCB for component mounting and vias. Advanced PCBs may use laser drilling for high precision.
- Surface Finish: A surface finish is applied to protect the exposed copper traces and pads from oxidation and improve solderability. Common surface finishes include HASL (Hot Air Solder Leveling), ENIG (Electroless Nickel Immersion Gold), and OSP (Organic Solderability Preservative).
- Silkscreen Printing:Optionally, a silkscreen layer may be applied to add component labels, identifiers, or other markings to the PCB.
- Final Inspection and Testing: The completed PCB undergoes thorough inspection and testing to ensure it meets the design specifications and quality standards.
Throughout the fabrication process, careful attention is paid to maintaining tight tolerances and achieving precise alignment to produce the narrow traces required for Minimum Trace PCBs. Advanced manufacturing techniques and equipment may be employed to achieve the desired level of accuracy and consistency.
How do you manufacture a Minimum Trace PCB?
Manufacturing a Minimum Trace PCB involves several steps, each executed with precision to achieve the narrow trace widths required. Here’s a detailed process:
- Design: Start with a PCB design software, where you define the layout, trace widths, component placement, and routing according to the design requirements and guidelines.
- Material Selection: Choose a substrate material suitable for Minimum Trace PCBs. High-quality materials like FR-4 with fine copper layers are commonly used.
- Preparation of Substrate: Clean and prepare the substrate material. Ensure it’s free from contaminants that could affect the manufacturing process.
- Copper Deposition: Apply a thin layer of copper onto the substrate. This can be done through processes like electroplating to ensure uniformity and precision.
- Photoresist Application: Apply a layer of photoresist onto the copper surface. This photoresist layer will protect the areas of copper that will become the traces and pads.
- Exposure and Development: Use a photographic process to transfer the PCB pattern onto the photoresist layer. UV light is passed through a mask containing the PCB pattern onto the photoresist-coated copper layer. After exposure, the photoresist is developed, revealing the pattern.
- Etching: Submerge the PCB in an etchant solution, which removes the unprotected copper not covered by the developed photoresist. This etching process creates the desired traces and pads on the PCB.
- Strip and Clean: Remove the remaining photoresist, leaving behind the copper traces and pads on the substrate. Clean the PCB to remove any etchant residue or contaminants.
- Drilling:Drill holes into the PCB for component mounting and vias. Utilize precise drilling techniques to ensure accuracy and alignment.
- Surface Finish:Apply a surface finish to protect the exposed copper traces and pads from oxidation and improve solderability. Common surface finishes include HASL, ENIG, and OSP.
- Silkscreen Printing: Optionally, apply a silkscreen layer for component labels, identifiers, or other markings on the PCB.
- Final Inspection and Testing: Thoroughly inspect and test the completed PCB to ensure it meets the design specifications and quality standards. Check for trace continuity, dimensional accuracy, and adherence to electrical parameters.
Throughout the manufacturing process, attention to detail, precise control of parameters, and adherence to design specifications are crucial for producing Minimum Trace PCBs with narrow and accurate traces. Advanced manufacturing technologies and quality assurance measures play a significant role in achieving the desired results.
How much should a Minimum Trace PCB cost?
The cost of a Minimum Trace PCB can vary depending on several factors, including the complexity of the design, the number of layers, the type of substrate material, the trace width and spacing requirements, the quantity ordered, and the chosen PCB manufacturer.
In general, Minimum Trace PCBs tend to be more expensive than standard PCBs due to the increased precision and tighter tolerances required for manufacturing narrow traces. Additionally, factors such as the use of advanced materials, special surface finishes, and additional services like impedance control or blind/buried vias can contribute to the overall cost.
As a rough estimate, the cost of a Minimum Trace PCB can range from a few dollars for simple designs with small quantities to several hundred dollars or more for complex designs with high layer counts and specialized features. It’s essential to obtain quotes from multiple PCB manufacturers to compare prices and ensure that you’re getting the best value for your specific requirements. Additionally, consider factors like lead time, quality assurance, and customer support when choosing a PCB manufacturer.
What is Minimum Trace PCB base material?
The base material for Minimum Trace PCBs is typically a high-quality substrate that provides the necessary mechanical strength, electrical insulation, and thermal properties required for the application. Common base materials used in Minimum Trace PCBs include:
- FR-4: FR-4 (Flame Retardant 4) is the most widely used substrate material for PCBs. It consists of a woven fiberglass cloth impregnated with an epoxy resin binder. FR-4 offers good mechanical strength, dimensional stability, and electrical insulation properties. It is suitable for a wide range of applications and is cost-effective.
- High-Tg FR-4:High-Tg (Glass Transition Temperature) FR-4 is an enhanced version of standard FR-4 with a higher glass transition temperature. It offers improved thermal stability, particularly during soldering and high-temperature operation. High-Tg FR-4 is suitable for applications where elevated temperatures are a concern.
- Polyimide (PI): Polyimide is a high-performance polymer material known for its excellent thermal stability, chemical resistance, and flexibility. Polyimide substrates are commonly used in flexible PCBs and applications where temperature extremes or harsh environments are encountered.
- Rogers: Rogers Corporation produces a range of high-performance laminate materials specifically designed for demanding RF/microwave applications. These materials offer low dielectric constant, low loss tangent, and excellent electrical properties, making them ideal for high-frequency circuits in Minimum Trace PCBs.
- Other Specialty Materials: Depending on the specific requirements of the application, other specialty materials such as PTFE (Polytetrafluoroethylene), ceramic-filled laminates, or metal-core substrates may be used. These materials offer unique properties such as high thermal conductivity, low loss, or high-frequency performance.
The choice of base material depends on factors such as operating environment, frequency of operation, mechanical constraints, and cost considerations. Designers select the appropriate base material to ensure that the Minimum Trace PCB meets the required performance specifications while maintaining reliability and manufacturability.
Which company makes Minimum Trace PCBs?
Minimum Trace PCBs are typically produced by many well-known PCB manufacturing companies, including Foxconn, JLCPCB, and Shenzhen Fute Technology. These companies have advanced manufacturing equipment and extensive experience to meet customers’ demands for precision PCBs.
Our company can also manufacture Minimum Trace PCBs. We have advanced manufacturing equipment and a skilled technical team to meet the requirements for precision PCBs. Here are some capabilities our company can offer:
- Precision Process Control: We have advanced manufacturing equipment and strict process control procedures to achieve precise control of line width, spacing, and hole size to meet the design requirements of Minimum Trace PCBs.
- High-Performance Substrates: We provide a variety of high-performance substrate options, including FR-4, high-Tg FR-4, Polyimide (PI), etc., to meet the requirements of different application environments.
- Surface Finishes: We offer various surface finish options such as HASL, ENIG, OSP, etc., to protect the traces and improve solderability.
- Strict Quality Control: We have a strict quality control system and professional quality inspection team to ensure that each batch of PCBs meets the design requirements and customer expectations.
- Customized Services: We provide customized solutions to personalize designs and manufacturing according to customers’ requirements, meeting various application scenarios’ demands.
With these capabilities and advantages, our company can provide customers with high-quality and reliable Minimum Trace PCBs, meeting customers’ demands for precision PCBs. We are committed to providing customers with high-quality products and services to achieve mutual success.
What are the 7 qualities of good customer service?
Good customer service is essential for building strong relationships with customers and fostering loyalty. Here are seven qualities that characterize excellent customer service:
- Responsiveness: A good customer service team responds promptly to customer inquiries, concerns, and requests. They acknowledge customer communications in a timely manner and strive to provide quick solutions or assistance.
- Empathy: Empathy is crucial in understanding and addressing customers’ emotions and concerns. Good customer service representatives listen actively, show genuine empathy, and put themselves in the customer’s shoes to provide personalized support.
- Clarity: Effective communication is key to good customer service. Clear and concise communication helps customers understand the information provided and ensures that they receive accurate guidance or instructions.
- Professionalism: Professionalism involves maintaining a positive and courteous demeanor while interacting with customers, even in challenging situations. Good customer service representatives remain calm, respectful, and focused on resolving issues professionally.
- Knowledgeability: Customers expect customer service representatives to be knowledgeable about the products or services offered by the company. A good customer service team is well-trained and equipped with the information and skills needed to address customer inquiries and provide accurate assistance.
- Problem-Solving Skills: Good customer service involves effectively identifying and solving customer problems or issues. Customer service representatives should be proactive in finding solutions, thinking critically, and resolving issues to the customer’s satisfaction.
- Consistency: Consistency is essential for building trust and reliability. Good customer service teams strive to deliver consistent experiences across all customer interactions, ensuring that every customer receives the same high level of service regardless of the channel or representative they engage with.
By embodying these qualities, businesses can deliver exceptional customer service experiences that leave a positive impression and foster long-term relationships with customers.
FAQs
What are the benefits of Minimum Trace PCBs?
Minimum Trace PCBs offer advantages such as reduced board size, improved signal integrity, and enhanced thermal management, making them ideal for compact and high-performance electronic devices.
Can Minimum Trace PCBs support high-speed signals?
Yes, properly designed Minimum Trace PCBs can support high-speed signals with minimal signal degradation and electromagnetic interference (EMI).
What factors influence the minimum trace width on a PCB?
Factors such as the current-carrying capacity, impedance requirements, and manufacturing capabilities influence the minimum trace width on a PCB.
How can I optimize my design for Minimum Trace PCB fabrication?
To optimize your design for Minimum Trace PCB fabrication, consider factors such as trace routing, layer stack-up, signal integrity, and manufacturability early in the design process. Working closely with your PCB manufacturer can also help ensure a successful outcome.
What are the limitations of Minimum Trace PCBs?
Limitations of Minimum Trace PCBs include increased susceptibility to manufacturing defects such as shorts and opens, as well as potentially higher fabrication costs compared to standard PCBs. Additionally, extremely narrow traces may be more susceptible to damage during handling or operation.