Minimum Spacing PCB Manufacturing
Minimum Spacing PCB Manufacturing,Minimum Spacing PCBs refers to the minimum distance between components on a printed circuit board (PCB). This spacing is a critical factor in PCB design as it directly impacts the performance and reliability of the circuit board. Typically, the spacing is determined by the manufacturer’s technical specifications and industry standards to ensure that there is adequate space between components on the PCB to prevent electrical shorts or other failures.
When designing Minimum Spacing PCBs, engineers must consider various factors including the types of components on the circuit board, package sizes, operating voltages, and more. They also need to consider aspects such as heat dissipation, signal interference, and mechanical stability to ensure the long-term reliability of the PCB.
With advancing technology and market demands, the requirements for Minimum Spacing PCBs are continuously increasing. Smaller packages and higher levels of integration mean that engineers must maintain smaller spacing between components while ensuring that performance and reliability are not compromised.
In summary, Minimum Spacing PCBs are a crucial part of PCB design, directly influencing the performance, reliability, and cost of the circuit board. By carefully considering various factors and adhering to industry standards, engineers can design high-quality PCBs that meet requirements.
What is a Minimum Spacing PCB?
A Minimum Spacing PCB refers to the minimum distance required between two conductive elements on a printed circuit board (PCB). These conductive elements could be traces, pads, or vias. The spacing requirement is critical to prevent electrical interference, crosstalk, or short circuits.
The minimum spacing depends on various factors such as the voltage difference between the conductive elements, the dielectric properties of the PCB material, and environmental conditions. Designers typically follow industry standards and guidelines to determine the appropriate minimum spacing for their specific application.
Exceeding the minimum spacing requirements can ensure reliable operation of the PCB and prevent electrical issues that could compromise the functionality or safety of the electronic device it’s a part of.
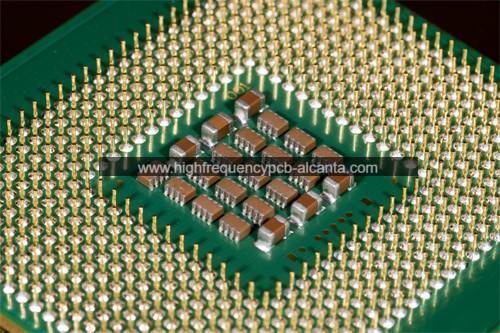
Minimum Spacing PCB Manufacturing
What are the Minimum Spacing PCB Design Guidelines?
Minimum spacing PCB design guidelines are essential for ensuring the integrity and reliability of printed circuit boards. Here are some common guidelines:
- Manufacturer Guidelines: Different PCB manufacturers may have their own specific minimum spacing requirements based on their manufacturing processes and capabilities. It’s crucial to consult the manufacturer’s guidelines and design rules.
- IPC Standards: The Institute for Printed Circuits (IPC) publishes standards such as IPC-2221, which provides guidelines for PCB design, including minimum spacing requirements. IPC standards are widely used in the industry and can serve as a valuable reference.
- Clearances: Minimum spacing guidelines often include clearances between traces, pads, vias, and other conductive elements on the PCB. These clearances help prevent electrical interference, crosstalk, and short circuits. Clearances are typically specified in terms of distance, such as millimeters or mils (1 mil = 0.001 inch).
- Voltage Ratings: The minimum spacing requirements may vary depending on the voltage levels present on the PCB. Higher voltages typically require larger clearances to prevent arcing and breakdown.
- Environmental Factors:Environmental conditions such as humidity, temperature, and altitude can affect the performance of the PCB. Design guidelines may account for these factors to ensure reliable operation under different environmental conditions.
- Signal Integrity: Maintaining proper spacing between signal traces is crucial for preserving signal integrity and minimizing signal degradation. Guidelines for minimum spacing between signal traces help prevent signal distortion and ensure accurate communication between components.
- Creepage and Clearance: Creepage is the distance along the surface of a PCB between two conductors, while clearance is the shortest distance through air between two conductors. These parameters are critical for ensuring safety and preventing electrical arcing, especially in high-voltage applications.
- Compliance with Regulations: Depending on the application, PCB designs may need to comply with regulatory standards such as UL (Underwriters Laboratories) or IEC (International Electrotechnical Commission). These standards may specify minimum spacing requirements to ensure safety and reliability.
By adhering to these guidelines, PCB designers can create layouts that meet the necessary electrical, mechanical, and safety requirements for their specific applications.
What is the Minimum Spacing PCB Fabrication Process?
The minimum spacing PCB fabrication process involves several steps to ensure that the required clearances between conductive elements are maintained during manufacturing. Here’s an overview of the key aspects:
- Design Review: Before fabrication begins, the PCB design undergoes a review process to ensure that it meets the minimum spacing requirements specified by the design guidelines, manufacturer’s capabilities, and industry standards such as IPC.
- Panelization: Multiple PCBs are often fabricated together on a larger panel to optimize production efficiency. During panelization, care must be taken to maintain adequate spacing between individual PCBs and between conductive elements within each PCB.
- Lamination: In multilayer PCBs, the individual layers are laminated together using heat and pressure to form a single integrated board. During lamination, alignment tools and registration marks help ensure that the conductive layers are properly aligned, maintaining the required clearances.
- Drilling: Holes for through-hole components and vias are drilled into the PCB. Precision drilling equipment is used to maintain the required minimum spacing between holes and between holes and other conductive elements.
- Copper Deposition: Conductive copper traces and pads are deposited or etched onto the surface of the PCB. Advanced techniques such as photolithography and chemical etching are used to define the precise patterns while maintaining the minimum spacing requirements.
- Dielectric Layer Application: Insulating dielectric materials are applied between conductive layers to provide electrical isolation and maintain clearances. The thickness and properties of the dielectric layer are critical for achieving the required spacing.
- Surface Finishing: Surface finishes such as solder mask and surface plating are applied to protect the conductive traces and provide solderability. Care is taken to ensure that these finishes do not encroach upon the minimum spacing requirements.
- Quality Control: Throughout the fabrication process, quality control measures are implemented to verify that the minimum spacing requirements are met. Automated optical inspection (AOI) and other testing methods are used to identify any defects or deviations from the design specifications.
By following these steps and employing precision manufacturing techniques, PCB fabricators can ensure that the minimum spacing requirements are maintained, resulting in reliable and compliant circuit boards.
How do you manufacture a Minimum Spacing PCB?
Manufacturing a minimum spacing PCB requires careful attention to detail and adherence to specific processes to ensure that the required clearances between conductive elements are maintained. Here’s a step-by-step overview of how minimum spacing PCBs are manufactured:
- Design Preparation: The PCB design is created or received from the customer. Design software is used to layout the circuitry and specify the minimum spacing requirements between conductive elements such as traces, pads, and vias.
- Material Selection: The appropriate PCB substrate material is selected based on factors such as dielectric constant, thermal properties, and mechanical strength. The material must meet the specifications required to maintain the minimum spacing requirements.
- Preparation of Substrate: The chosen substrate material is prepared for manufacturing. This may involve cutting the material to the required size and applying surface treatments such as cleaning and surface roughening to promote adhesion of the copper layers.
- Copper Cladding: A thin layer of copper is bonded to one or both sides of the substrate using a process such as electroplating or lamination. The thickness of the copper layer is determined by the design requirements and manufacturing capabilities.
- Photoresist Application: A layer of photoresist is applied to the surface of the copper layer. The photoresist acts as a mask during the etching process, defining the pattern of the conductive traces and pads while maintaining the required spacing.
- Exposure and Development: The PCB design is transferred onto the photoresist layer using a photomask and exposure to UV light. The exposed photoresist is then developed, leaving behind a pattern that corresponds to the desired conductive traces and pads.
- Etching: The exposed copper areas not protected by the developed photoresist are etched away using an etchant solution. This process defines the conductive traces and pads on the PCB while maintaining the minimum spacing specified in the design.
- Strip and Clean: The remaining photoresist is stripped away, leaving behind the copper traces and pads. The PCB is thoroughly cleaned to remove any residues from the etching process and prepare it for further processing.
- Drilling: Holes for through-hole components and vias are drilled into the PCB using precision drilling equipment. Care is taken to ensure that the drilling process does not violate the minimum spacing requirements between holes and between holes and other conductive elements.
- Surface Finish: Surface finishes such as solder mask and surface plating are applied to protect the copper traces and provide solderability. These finishes must be applied with precision to avoid encroaching upon the minimum spacing requirements.
- Quality Control: Throughout the manufacturing process, quality control measures are implemented to verify that the minimum spacing requirements are met. Automated optical inspection (AOI) and other testing methods are used to identify any defects or deviations from the design specifications.
By following these steps and employing precision manufacturing techniques, PCB manufacturers can produce minimum spacing PCBs that meet the required specifications for reliability and performance.
How much should a Minimum Spacing PCB cost?
The cost of a minimum spacing PCB can vary significantly depending on various factors such as:
- Board Size: Larger PCBs typically cost more due to the increased material and manufacturing time required.
- Layer Count: Multilayer PCBs with more layers are generally more expensive than single or double-layer boards because of the additional manufacturing steps and materials involved.
- Complexity of Design: PCBs with intricate designs, fine pitch components, and dense routing patterns may require more advanced manufacturing processes and specialized equipment, leading to higher costs.
- Material Selection: The choice of substrate material can affect the cost of the PCB. High-performance materials with specific properties such as high temperature resistance or low dielectric loss tend to be more expensive.
- Minimum Spacing Requirements: Meeting tight minimum spacing requirements may necessitate more precise manufacturing processes and tighter tolerances, which can increase the cost of fabrication.
- Surface Finish and Coating: Different surface finishes and coatings can be applied to the PCB for protection and functionality, and the choice of finish can impact the cost.
- Volume: Economies of scale apply to PCB manufacturing, meaning that larger production volumes typically result in lower per-unit costs. Ordering larger quantities can help reduce the cost per PCB.
- Manufacturer: Different PCB manufacturers may have varying pricing structures based on their capabilities, equipment, and overhead costs.
As a rough estimate, the cost of a minimum spacing PCB can range from a few dollars for simple designs to several hundred dollars or more for complex, high-performance boards. For an accurate cost estimate, it’s best to consult with PCB manufacturers and provide them with detailed specifications of the design requirements.
What is Minimum Spacing PCB base material?
The base material of a minimum spacing PCB refers to the substrate material upon which the conductive traces and components are mounted. The choice of base material is crucial as it affects the electrical performance, mechanical strength, and reliability of the PCB. Here are some common base materials used for minimum spacing PCBs:
- FR-4: FR-4 (Flame Retardant 4) is the most commonly used substrate material for PCBs. It is a composite material made of woven fiberglass cloth impregnated with an epoxy resin binder. FR-4 offers good electrical insulation properties, dimensional stability, and affordability, making it suitable for a wide range of applications.
- High-Temperature FR-4: For applications that require increased thermal performance, high-temperature FR-4 variants are available. These materials have enhanced thermal properties, allowing the PCB to withstand higher operating temperatures without degrading performance.
- Polyimide (PI): Polyimide is a high-performance substrate material known for its excellent thermal stability, chemical resistance, and mechanical strength. It is commonly used in flexible PCBs and applications requiring extreme temperatures, such as aerospace and automotive electronics.
- Rogers Materials: Rogers Corporation produces a range of high-frequency circuit materials specifically designed for RF and microwave applications. These materials offer low dielectric loss, consistent electrical properties, and tight dimensional stability, making them suitable for high-frequency designs with strict minimum spacing requirements.
- Metal Core: Metal core PCBs feature a metal substrate, typically aluminum or copper, which provides excellent thermal conductivity. These PCBs are used in applications requiring efficient heat dissipation, such as LED lighting, power electronics, and automotive systems.
- Ceramic: Ceramic substrates offer superior thermal conductivity and electrical insulation properties compared to traditional organic substrates. They are often used in high-power applications, RF/microwave circuits, and environments with extreme temperatures.
- PTFE (Polytetrafluoroethylene): PTFE-based materials such as Teflon® offer low dielectric constant and loss, making them suitable for high-frequency applications requiring minimal signal distortion. PTFE substrates are commonly used in microwave PCBs and antennas.
The choice of base material depends on factors such as the operating environment, frequency of operation, thermal requirements, and cost considerations. Designers typically select a material that best meets the performance requirements of their specific application while staying within budget constraints.
Which company makes Minimum Spacing PCB?
Many companies are capable of producing Minimum Spacing PCBs, including large enterprises specializing in electronics manufacturing, small PCB factories, and technology companies focused on specific fields. These companies typically possess advanced manufacturing equipment, stringent quality control systems, and experienced engineering teams when producing Minimum Spacing PCBs. Some well-known PCB manufacturers include Foxconn, European enterprises, and North American companies like Advanced Circuits.
As for our company, we are also capable of manufacturing Minimum Spacing PCBs. As a professional PCB manufacturer, we have advanced production equipment and a skilled technical team to meet various Minimum Spacing requirements for PCB manufacturing. Our manufacturing process strictly follows industry standards and customer requirements to ensure the production of high-quality and reliable PCB products.
Our manufacturing capabilities cover various types of PCBs, including single-sided, double-sided, multilayer, as well as rigid, flexible, and rigid-flex PCBs. We can flexibly adjust the production process according to customer design requirements and technical specifications to produce PCB products that meet Minimum Spacing requirements.
Additionally, we place a strong emphasis on quality management, with strict quality control systems and comprehensive testing equipment to ensure that every PCB meets design specifications and customer expectations. We also offer flexible order quantities and fast delivery cycles to meet customers’ time and cost requirements.
In summary, our company has the capability to manufacture Minimum Spacing PCBs and is committed to providing customers with high-quality, reliable PCB solutions to meet their various application needs.
What are the 7 qualities of good customer service?
Good customer service is essential for building strong relationships with customers and ensuring their satisfaction. Here are seven qualities that characterize good customer service:
- Responsiveness: Good customer service involves being attentive and responsive to customers’ needs and inquiries in a timely manner. Responding promptly to customer queries, requests for assistance, and feedback demonstrates a commitment to addressing their concerns efficiently.
- Empathy: Empathy is the ability to understand and share the feelings of others. Good customer service representatives empathize with customers’ concerns and frustrations, demonstrating genuine care and concern for their well-being. This helps to build trust and rapport with customers.
- Clear Communication: Effective communication is crucial for providing good customer service. Customer service representatives should communicate clearly and concisely, using language that is easy for customers to understand. They should listen actively to customers’ questions and concerns and provide accurate and helpful responses.
- Problem-solving Skills: Good customer service involves being proactive in resolving customers’ issues and concerns. Customer service representatives should possess strong problem-solving skills, identifying and addressing problems quickly and effectively to ensure customer satisfaction.
- Professionalism: Professionalism encompasses a range of behaviors, including courtesy, respect, and integrity. Good customer service representatives maintain a professional demeanor at all times, treating customers with courtesy and respect and upholding ethical standards in their interactions.
- Product Knowledge: Good customer service requires a thorough understanding of the products or services being offered. Customer service representatives should be knowledgeable about the features, benefits, and usage of the products or services they are supporting, enabling them to provide accurate information and assistance to customers.
- Follow-up and Follow-through: Good customer service extends beyond the initial interaction. Customer service representatives should follow up with customers to ensure that their concerns have been addressed satisfactorily and follow through on any commitments made during the interaction. This demonstrates a commitment to customer satisfaction and helps to build long-term relationships with customers.
By embodying these qualities, organizations can deliver exceptional customer service that fosters loyalty, enhances reputation, and drives business success.
FAQs
What is a Minimum Spacing PCB?
A Minimum Spacing PCB refers to a printed circuit board where the distance between two conductive elements, such as traces, pads, or vias, is minimized to meet specific design requirements while ensuring electrical integrity and reliability.
Why is Minimum Spacing important in PCB design?
Minimum spacing is crucial for preventing electrical interference, crosstalk, and short circuits on the PCB. It helps maintain electrical isolation between conductive elements and ensures reliable operation of the electronic device.
How is Minimum Spacing determined in PCB design?
Minimum spacing requirements are determined based on factors such as the voltage difference between conductive elements, the dielectric properties of the PCB material, environmental conditions, and industry standards or guidelines.
What are the consequences of violating Minimum Spacing requirements?
Violating Minimum Spacing requirements can lead to electrical issues such as signal distortion, short circuits, and component damage. It can compromise the functionality, reliability, and safety of the electronic device.
What are some common industry standards for Minimum Spacing in PCB design?
Industry standards such as IPC-2221 provide guidelines for Minimum Spacing in PCB design. These standards specify minimum clearances between different conductive elements based on various factors including voltage levels, material properties, and environmental conditions.
How do PCB manufacturers ensure Minimum Spacing requirements are met during fabrication?
PCB manufacturers use precision manufacturing processes, advanced equipment, and quality control measures to ensure that Minimum Spacing requirements are met during fabrication. This includes careful attention to detail in processes such as etching, drilling, and surface finishing.