Minimum Spacing PCB Manufacturer
Minimum Spacing PCB Manufacturer,Minimum Spacing PCBs are meticulously designed circuit boards where the distance between conductive elements like traces and pads is minimized for compactness and efficiency. These boards are crucial in modern electronics, enabling higher component density and enhanced performance in applications requiring precision and miniaturization. Achieving such tight spacing demands advanced manufacturing techniques and materials that ensure signal integrity, reliability, and compliance with stringent design specifications. Minimum Spacing PCBs are used in a wide range of industries, from consumer electronics to aerospace, where space-saving and high-performance capabilities are paramount.
What is a Minimum Spacing PCB?
A Minimum Spacing PCB (Printed Circuit Board) refers to a design where the distance between conductive elements, such as traces and pads, is minimized to achieve higher component density and efficient use of board space. This type of PCB design is crucial in modern electronics where miniaturization is a key goal.
The spacing between conductive elements is governed by electrical and manufacturing considerations. Electrically, close spacing can affect impedance, capacitance, and crosstalk between traces, which must be carefully managed to maintain signal integrity and prevent interference. From a manufacturing perspective, tighter spacing requires precise control during fabrication processes like etching, solder mask application, and assembly to avoid shorts or other defects.
Advantages of Minimum Spacing PCBs include compact size, reduced signal loss due to shorter trace lengths, and often improved performance in high-frequency applications. However, designing such PCBs requires expertise in layout optimization, consideration of thermal management to avoid overheating, and adherence to industry standards to ensure reliability and compatibility with manufacturing processes.
In summary, Minimum Spacing PCBs play a critical role in the development of compact and high-performance electronic devices, balancing electrical requirements with manufacturing feasibility to achieve optimal results.
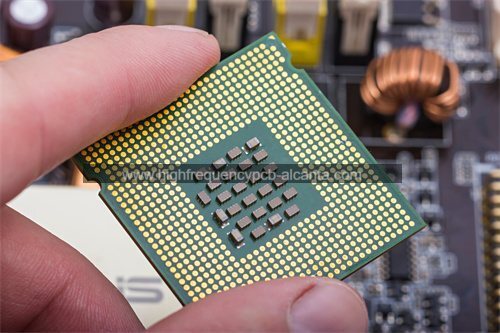
Minimum Spacing PCB Manufacturer
What are the Minimum Spacing PCB Design Guidelines?
Minimum spacing PCB design guidelines ensure that the printed circuit board meets electrical and manufacturing requirements while optimizing space and performance. Here are some key guidelines typically followed in designing Minimum Spacing PCBs:
- Manufacturing Constraints: Understand the capabilities of the PCB fabrication process regarding minimum trace width, minimum annular ring (for vias and pads), and minimum spacing between traces and pads. These constraints vary based on the PCB manufacturer’s capabilities and the chosen PCB technology (e.g., standard FR4, high-frequency materials).
- Clearance Rules: Define minimum clearance rules for different voltage levels and signal types to prevent electrical interference, crosstalk, and potential short circuits. For instance, high-voltage traces require larger clearance to avoid arcing.
- Trace Width and Spacing: Determine appropriate trace widths based on current-carrying capacity and impedance requirements. Minimize spacing between traces to optimize board space, but ensure adequate separation to maintain isolation and prevent unintended coupling.
- Via Design:Optimize via size and placement to minimize impedance discontinuities and ensure adequate clearance from nearby traces and pads. Consider via stub length and ensure it meets signal integrity requirements, especially in high-frequency designs.
- Component Placement: Strategically place components to minimize trace lengths, reduce signal loss, and optimize thermal management. Consider thermal dissipation requirements and ensure adequate spacing for heat dissipation components like heat sinks.
- Design Rules Check (DRC): Use design rule checks provided by PCB design software to validate spacing, clearance, and other design constraints before manufacturing. This helps catch potential issues early in the design process.
- High-Speed Design Considerations: For high-frequency signals, adhere to strict impedance control guidelines, ensure consistent dielectric properties across the board, and use controlled impedance routing where necessary.
- Stack-Up Design: Define PCB stack-up carefully to optimize signal integrity, thermal management, and manufacturability. Consider layer-wise spacing and dielectric materials to achieve desired electrical performance.
- Compliance with Standards: Follow industry standards and guidelines such as IPC-2221 for generic printed board design and IPC-2226 for HDI (High Density Interconnect) PCBs to ensure reliability, manufacturability, and compatibility with assembly processes.
- Documentation and Communication: Document design rules clearly in the PCB design documentation to facilitate communication with PCB manufacturers and ensure consistent production quality.
By adhering to these minimum spacing PCB design guidelines, designers can achieve compact, reliable, and high-performance PCB layouts that meet both electrical and manufacturing requirements effectively.
What is the Minimum Spacing PCB Fabrication Process?
The Minimum Spacing PCB fabrication process involves several steps to ensure that the designed PCB layout meets the specified spacing requirements while maintaining electrical integrity and manufacturability. Here’s an overview of the typical fabrication process focusing on minimum spacing considerations:
- Design Input: Receive the PCB design files from the designer, which include the PCB layout with defined trace widths, clearances, pad sizes, via specifications, and stack-up details. These files are typically in Gerber format or other CAD formats supported by PCB fabrication software.
- Pre-Production Checks: Perform a Design for Manufacturability (DFM) review to check the design against manufacturing capabilities. Verify that minimum spacing rules are adhered to according to the chosen PCB fabrication process (e.g., etching capabilities, solder mask alignment, drill tolerances).
- Material Selection: Choose appropriate laminate materials based on the PCB stack-up requirements. Different materials have varying dielectric constants and thermal properties that impact minimum spacing considerations, especially in high-frequency and high-power applications.
- Layer Alignment and Registration: Align and register the layers of the PCB stack-up accurately. This ensures that the conductive layers (traces and planes) are correctly positioned relative to each other to maintain controlled impedance and ensure that minimum spacing requirements are met across all layers.
- Etching Process: Use chemical etching or other methods to selectively remove copper from the substrate according to the PCB design. The etching process must maintain precise control to achieve the specified trace widths and maintain the required spacing between adjacent traces and pads.
- Drilling and Via Formation:Drill holes for vias and through-hole components according to specified drill sizes and minimum annular ring requirements. Vias are plated to connect conductive layers, and the drilling process must ensure adequate spacing from nearby traces and other vias to prevent shorts.
- Solder Mask Application: Apply solder mask over the PCB surface except where electrical connections (pads and vias) are required. The solder mask helps protect the PCB from environmental factors, prevents solder bridges during assembly, and defines minimum spacing around conductive features.
- Surface Finish: Apply a surface finish such as HASL (Hot Air Solder Leveling), ENIG (Electroless Nickel Immersion Gold), or OSP (Organic Solderability Preservative) to protect exposed copper surfaces and ensure reliable solder joints during assembly. The choice of surface finish can affect minimum spacing requirements due to its thickness and electrical properties.
- Quality Assurance: Perform quality checks throughout the fabrication process to verify dimensional accuracy, adherence to minimum spacing guidelines, and overall PCB integrity. Automated optical inspection (AOI) and other testing methods help detect defects early and ensure compliance with design specifications.
- Final Inspection and Packaging: Inspect the finished PCBs for any defects or deviations from design specifications. Once approved, package the PCBs securely for shipping to the customer or further assembly processes.
Throughout the Minimum Spacing PCB fabrication process, close attention is paid to maintaining design integrity, ensuring electrical performance, and adhering to the defined spacing rules to achieve a high-quality, reliable printed circuit board suitable for its intended application.
How do you manufacture a Minimum Spacing PCB?
Manufacturing a Minimum Spacing PCB involves following a meticulous process that ensures the PCB design’s tight spacing requirements are met while maintaining electrical integrity and manufacturability. Here’s a step-by-step outline of how you manufacture such a PCB:
- Design Preparation: Start with a well-prepared PCB design that includes tight spacing specifications for traces, pads, vias, and other conductive elements. The design should adhere to industry standards and manufacturing capabilities.
- Material Selection: Choose the appropriate laminate material and substrate thickness based on the PCB stack-up requirements. Select materials with suitable dielectric properties and thermal conductivity to support the high-density layout and ensure signal integrity.
- Pre-Production Checks: Conduct a thorough Design for Manufacturability (DFM) review to verify that the design complies with manufacturing capabilities. Check for minimum spacing requirements against the chosen PCB fabrication process (e.g., etching resolution, drill tolerances).
- Gerber File Generation: Generate Gerber files and other necessary documentation from the PCB design software. These files define the PCB layout, including trace routing, pad sizes, solder mask openings, and other critical dimensions.
- Film Generation: Create photo tools or films from the Gerber files. These films are used in the PCB manufacturing process to transfer the PCB design onto the copper-clad laminate.
- Lamination:Start with the copper-clad laminate and clean its surface thoroughly. Then, apply dry film resist or liquid photoresist to both sides of the laminate. Expose the resist to UV light through the photo tools to transfer the PCB pattern onto the resist.
- Etching: Use chemical etching to remove unwanted copper from the laminate, leaving behind the circuit traces and pads as defined by the resist pattern. Control the etching process carefully to achieve precise trace widths and maintain minimum spacing between adjacent traces and pads.
- Drilling: Drill holes for vias and through-hole components using precision drilling machines. Ensure that drill sizes and positions align with the design specifications, and maintain adequate clearance around drilled holes to avoid unintended contact with adjacent traces or pads.
- Surface Finishing: Apply a suitable surface finish to protect exposed copper surfaces and ensure good solderability. Common surface finishes include HASL (Hot Air Solder Leveling), ENIG (Electroless Nickel Immersion Gold), and OSP (Organic Solderability Preservative). The choice of surface finish should consider its impact on minimum spacing and electrical performance.
- Solder Mask Application: Apply solder mask over the PCB surface, leaving openings only where electrical connections (pads, vias) are required. The solder mask helps prevent solder bridges during assembly and protects the PCB from environmental factors.
- Silkscreen Printing: Optionally, apply a silkscreen layer to print component designators, polarity markings, and other identifiers on the PCB surface. Ensure that silkscreen markings do not violate minimum spacing requirements or cover critical areas.
- Testing and Inspection: Conduct electrical testing and inspection to verify the PCB’s functionality and adherence to design specifications. Use automated optical inspection (AOI) and other testing methods to detect defects, ensure trace continuity, and confirm minimum spacing compliance.
- Quality Assurance: Perform final inspection and quality checks to ensure that the manufactured PCB meets all requirements for minimum spacing, dimensional accuracy, and overall quality. Address any identified issues before proceeding to packaging and shipping.
- Packaging: Package the finished PCBs securely to protect them during transit and handling. Label packages appropriately with traceability information and handling instructions for customers or further assembly processes.
By carefully following these steps and maintaining rigorous quality control throughout the manufacturing process, manufacturers can successfully produce Minimum Spacing PCBs that meet stringent design requirements for high-density, high-performance electronic applications.
How much should a Minimum Spacing PCB cost?
The cost of a Minimum Spacing PCB can vary significantly depending on several factors:
- Complexity of Design:The more complex the PCB design in terms of number of layers, trace density, and spacing requirements, the higher the manufacturing cost. Minimum spacing designs often require more precise manufacturing processes and may involve additional steps to ensure quality and compliance.
- Materials Used: The choice of laminate material, substrate thickness, and surface finish affects the cost. High-frequency materials or specialized laminates may cost more than standard FR4, impacting the overall PCB cost.
- Manufacturing Process: Different PCB fabrication processes (e.g., standard PCB, HDI – High Density Interconnect, flexible PCB) have varying costs. HDI PCBs, which are common in high-density designs requiring minimum spacing, typically cost more due to their advanced manufacturing techniques.
- Batch Size: Larger production runs generally reduce the cost per unit due to economies of scale. Smaller batch sizes may incur higher costs per unit as fixed costs are spread over fewer units.
- Lead Time: Expedited manufacturing services often come with higher costs. Standard lead times are typically more cost-effective compared to rush orders.
- Additional Services: Optional services such as impedance control, special finishes (e.g., gold plating), and testing (e.g., electrical testing, AOI) can add to the overall cost.
As a rough estimate, for a standard 2-layer Minimum Spacing PCB with typical specifications (FR4 material, standard lead time, basic surface finish), you might expect prices to start around $10 to $50 per square inch for small quantities. However, prices can vary significantly based on the factors mentioned above. For more complex designs (e.g., multilayer, HDI) with tighter spacing requirements, the cost can be substantially higher.
To get an accurate cost estimate, it’s recommended to consult with PCB manufacturers or use online PCB quotation tools that allow you to input your specific design parameters and receive a tailored quote based on current market prices and manufacturing capabilities. This helps ensure you get a precise estimate based on your exact requirements for Minimum Spacing PCB fabrication.
What is Minimum Spacing PCB base material?
The base material used for Minimum Spacing PCBs, like other types of printed circuit boards, plays a critical role in ensuring electrical performance, mechanical durability, and manufacturability. Here are some common base materials used for Minimum Spacing PCBs:
- FR4 (Flame Retardant 4): FR4 is the most widely used base material for PCBs due to its cost-effectiveness, good electrical insulation properties, and mechanical strength. It consists of woven fiberglass cloth impregnated with epoxy resin. FR4 is suitable for standard PCB applications with moderate to tight spacing requirements.
- High-Frequency Materials:For applications requiring high-speed signal transmission or RF (Radio Frequency) circuits, high-frequency materials such as PTFE (Polytetrafluoroethylene) or ceramic-filled laminates are used. These materials offer low dielectric loss, high thermal conductivity, and stable electrical properties over a wide frequency range.
- Flexible and Rigid-Flex Materials: Flexible PCBs use polyimide or polyester films as base materials due to their flexibility and durability. Rigid-flex PCBs combine rigid FR4 sections with flexible materials, offering design flexibility and space savings in compact electronic devices.
- Metal Core Materials: Metal core PCBs (MCPCBs) use a metal substrate (typically aluminum or copper) as the base material, offering excellent thermal conductivity. They are used in applications requiring efficient heat dissipation, such as LED lighting and power electronics.
- Specialized Materials: Depending on specific application requirements, PCBs may use specialized materials such as Rogers laminates (high-frequency, low-loss materials), ceramic substrates (for high-temperature applications), or high-performance laminates optimized for impedance control and signal integrity.
When selecting the base material for a Minimum Spacing PCB, factors such as dielectric constant, thermal properties, mechanical strength, cost, and manufacturability must be considered. The choice of base material directly impacts the PCB’s electrical performance, reliability, and ability to meet tight spacing requirements without compromising quality. It’s essential to work closely with PCB designers and manufacturers to select the most suitable material based on the application’s specific needs and performance criteria.
Which company makes Minimum Spacing PCB?
There are many companies that manufacture Minimum Spacing PCBs, typically specialized PCB manufacturers with advanced manufacturing equipment and extensive experience to meet the demands of high-density circuit board designs. These companies can produce not only standard FR4 PCBs but also specialized materials and complex processes to meet the needs of different industries and applications.
Our company, as a professional PCB manufacturer, is capable of producing Minimum Spacing PCBs that meet stringent design requirements. Here are our capabilities and strengths:
- Advanced Manufacturing Equipment: We have advanced PCB manufacturing equipment, including high-precision chemical etching machines, precision drilling equipment, and automated surface treatment lines. These machines enable us to precisely control PCB trace widths, spacing, and hole sizes to meet design specifications.
- Expert Technical Team: Our company boasts an experienced technical team comprising PCB design engineers, manufacturing engineers, and quality control experts. They conduct comprehensive design reviews and process optimizations to ensure optimal electrical performance and reliability during PCB production.
- Wide Range of Material Choices: We offer a wide selection of substrate materials, including standard FR4, high-frequency materials like PTFE, special metal substrates such as aluminum-based boards, and flexible materials such as polyimide and polyester films for flexible PCBs. We recommend the most suitable materials based on specific customer requirements.
- Strict Quality Control: We implement rigorous quality management systems, including automated optical inspection (AOI), electrical testing, and final inspection at every stage of production. These measures enable us to promptly detect and rectify any potential manufacturing defects, ensuring stable and reliable PCB quality delivered to customers.
- Customization Services: We provide flexible customization services, adjusting production processes and service offerings according to specific customer requirements. Whether it’s small-batch rapid delivery or large-scale production, we can meet customer demands with competitive pricing and superior service.
In summary, as a professional PCB manufacturer equipped with advanced facilities, extensive experience, and stringent quality control, we have the capability to produce Minimum Spacing PCBs that meet high standards of quality and reliability. We are committed to collaborating with customers to drive technological innovation and enhance market competitiveness.
What are the 7 qualities of good customer service?
Good customer service is characterized by several key qualities that contribute to a positive customer experience and foster customer satisfaction and loyalty. Here are seven qualities of good customer service:
- Responsiveness: Responding promptly to customer inquiries, concerns, and requests is essential. Customers appreciate timely assistance and solutions to their issues without unnecessary delays.
- Empathy: Showing empathy means understanding and acknowledging the customer’s emotions and concerns. It involves listening actively, demonstrating understanding, and expressing genuine concern for the customer’s situation.
- Clear Communication: Effective communication is crucial in customer service. Clear and concise communication helps ensure that customers understand the information provided, such as product details, policies, and solutions to their problems.
- Knowledgeability: Good customer service representatives possess a deep understanding of the products or services they support. They are knowledgeable about features, functionalities, and troubleshooting methods, enabling them to provide accurate and helpful information to customers.
- Professionalism: Maintaining a professional demeanor in interactions with customers is important. This includes being courteous, respectful, and maintaining a positive attitude even when dealing with challenging situations.
- Problem-solving Skills: Strong problem-solving skills are essential in customer service roles. Effective representatives can identify issues, analyze them accurately, and offer appropriate solutions or escalate to higher levels of support when needed.
- Personalization:Providing personalized service involves treating each customer as an individual with unique needs and preferences. This may include remembering customer preferences, addressing them by name, and tailoring solutions to fit their specific situation.
By embodying these qualities, organizations can deliver exceptional customer service that not only resolves immediate issues but also builds long-term relationships with customers based on trust, satisfaction, and loyalty.
FAQs
What are Minimum Spacing PCBs used for?
Minimum Spacing PCBs are crucial in electronics where compact design and reliable electrical performance are required, such as in consumer electronics, aerospace applications, and medical devices.
How can I ensure my Minimum Spacing PCB design meets industry standards?
Ensuring compliance with industry standards involves thorough design verification, adherence to design guidelines, and potentially consulting with experts in PCB manufacturing.
What materials are used in Minimum Spacing PCB fabrication?
Common materials include FR-4 (fiberglass-reinforced epoxy), flexible materials like polyimide, and specialized materials for high-frequency applications.
How long does it take to manufacture Minimum Spacing PCBs?
Manufacturing times vary depending on complexity and order size, typically ranging from a few days for prototypes to several weeks for larger production runs.
What testing procedures are used for Minimum Spacing PCBs?
Testing often includes electrical tests (e.g., continuity testing), visual inspection, and sometimes more specialized tests like impedance testing for high-frequency circuits.
What are the advantages of Minimum Spacing PCBs over traditional PCBs?
Minimum Spacing PCBs allow for more compact designs, reduce electrical interference, and improve overall reliability and performance in electronic devices.