Minimum Pad Clearance PCB manufacturingy.
Minimum Pad Clearance PCB Manufacturing,Minimum Pad Clearance PCBs are printed circuit boards (PCBs) that feature carefully designed spacing between soldering pads to prevent unintended electrical connections and solder bridging during assembly. These PCBs adhere to specific industry standards and guidelines, ensuring optimal performance and reliability in electronic devices.
In Minimum Pad Clearance PCB design, engineers meticulously determine the minimum allowable distance between adjacent pads based on factors such as the manufacturing process, component size, and operational requirements. This precision helps to mitigate the risk of short circuits and other electrical issues, enhancing the overall functionality and longevity of the electronic device.
Manufacturing Minimum Pad Clearance PCBs involves advanced fabrication techniques and quality control measures to maintain the specified pad clearances. Designers and manufacturers collaborate closely to ensure that the PCBs meet the highest standards of quality and performance.
Overall, Minimum Pad Clearance PCBs play a crucial role in modern electronics by providing a robust and dependable platform for integrating electronic components while minimizing the risk of electrical failures and malfunctions.
What is a Minimum Pad Clearance PCB?
A Minimum Pad Clearance PCB refers to the minimum allowable distance between pads on a printed circuit board (PCB). Pads are the areas of exposed copper where electronic components are soldered onto the PCB.
The minimum pad clearance is an important parameter in PCB design because it ensures that there is enough space between adjacent pads to prevent unintended electrical connections (short circuits) or solder bridging during assembly.
The specific minimum pad clearance required can vary depending on factors such as the manufacturing process, the size of the components being soldered, and the operating environment of the PCB. Designers typically adhere to industry standards and guidelines to determine appropriate pad clearances for their PCB designs.
Ensuring an adequate pad clearance is essential for the reliable operation and assembly of electronic devices. Insufficient pad clearance can lead to electrical problems, manufacturing defects, and ultimately, product failures.
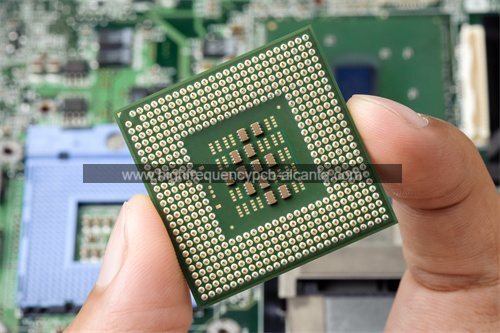
Minimum Pad Clearance PCB Manufacturing
What are the Minimum Pad Clearance PCB Design Guidelines?
The minimum pad clearance PCB design guidelines refer to recommendations and rules that designers should follow when determining the spacing between pads on a printed circuit board (PCB). These guidelines help ensure reliable electrical connections, prevent short circuits, and facilitate successful PCB assembly. Here are some common minimum pad clearance PCB design guidelines:
- Manufacturer Guidelines:Different PCB manufacturers may have specific requirements for minimum pad clearance based on their manufacturing processes and capabilities. Designers should consult the manufacturer’s guidelines to ensure compliance.
- IPC Standards:The Institute for Printed Circuits (IPC) publishes standards such as IPC-2221, which provides guidelines for PCB design including minimum pad clearances. Designers often reference IPC standards for best practices in PCB design.
- Component Datasheets:Manufacturers provide datasheets for electronic components, which often include recommended footprint patterns and pad layouts. Designers should follow these recommendations to ensure proper spacing between pads.
- Design Software Rules:PCB design software often includes design rule checks (DRCs) that allow designers to set minimum pad clearance rules. Designers can configure these rules to enforce minimum pad clearance requirements during the design process.
- Application Requirements:The specific application and environmental conditions of the PCB can influence minimum pad clearance requirements. For example, high-voltage applications may require larger pad clearances to prevent arcing.
- Assembly Process Constraints:Consideration should be given to the assembly process, including soldering methods and equipment capabilities. Adequate pad clearance facilitates soldering and reduces the risk of solder bridging during assembly.
- Signal Integrity Considerations:In high-speed digital designs, signal integrity can be affected by the spacing between pads, especially for differential pairs and high-frequency signals. Designers should balance pad clearance requirements with signal integrity considerations.
- Thermal Considerations:Adequate pad clearance can also aid in thermal management by providing space for heat dissipation and preventing heat buildup between components.
By adhering to these guidelines, designers can optimize the layout of PCB pads to ensure reliable electrical connections, manufacturability, and performance of electronic devices.
What is the Minimum Pad Clearance PCB Fabrication Process?
The minimum pad clearance in the PCB fabrication process refers to the minimum allowable distance between pads during the manufacturing of the printed circuit board. This parameter is critical for ensuring that the PCB can be manufactured accurately and reliably. Here’s a brief overview of how the minimum pad clearance is managed during the PCB fabrication process:
- Design Phase:During the PCB design phase, designers specify the minimum pad clearance according to the requirements of the project, industry standards, and the capabilities of the PCB manufacturer. This information is included in the PCB design files.
- Preparation of Manufacturing Files:Once the PCB design is complete, the design files are prepared for manufacturing. This involves converting the design into Gerber files, which contain all the necessary information for PCB fabrication, including the pad clearances.
- Manufacturing Process: The manufacturing process begins with the fabrication of the PCB using the Gerber files. This typically involves several steps, including imaging the PCB layers onto copper-clad laminate, etching away excess copper, drilling holes for component mounting, and applying solder mask and silkscreen.
- Quality Control:Throughout the manufacturing process, quality control measures are implemented to ensure that the PCB meets the specified design requirements, including the minimum pad clearance. Automated optical inspection (AOI) and other inspection techniques may be used to verify that the pad clearances are within tolerance.
- Final Inspection:Once the PCB fabrication is complete, a final inspection is conducted to verify the overall quality of the PCB, including the pad clearances. Any deviations from the specified pad clearances are identified and addressed as needed.
- Documentation:Documentation of the manufacturing process, including the pad clearances, is typically provided to the customer along with the finished PCBs. This documentation serves as a record of compliance with the design requirements.
Overall, managing the minimum pad clearance during the PCB fabrication process involves careful coordination between the design team and the manufacturing facility to ensure that the finished PCBs meet the required specifications for reliable performance in electronic devices.
How do you manufacture a Minimum Pad Clearance PCB?
Manufacturing a minimum pad clearance PCB involves following specific steps in the fabrication process to ensure that the pads are created with the required spacing between them. Here’s an overview of the manufacturing process for a minimum pad clearance PCB:
- Design Phase:During the design phase, the minimum pad clearance is specified by the PCB designer based on project requirements, industry standards, and manufacturing capabilities. Design software is used to create the PCB layout, including the placement and spacing of pads.
- Gerber File Preparation: Once the PCB design is complete, it is converted into Gerber files, which contain all the necessary information for PCB fabrication. The Gerber files include data on pad sizes, shapes, and clearances.
- Material Preparation:The fabrication process begins with the preparation of the base material, typically fiberglass-reinforced epoxy laminate known as FR-4. The material is cleaned and prepared for the subsequent manufacturing steps.
- Copper Cladding: Copper foil is laminated onto the surface of the base material. This forms the conductive layers of the PCB. The thickness of the copper foil is chosen based on the current-carrying requirements of the PCB.
- Photoresist Application:A layer of photoresist is applied to the surface of the copper-clad laminate. The photoresist is sensitive to ultraviolet light and is used to create the pattern for the PCB traces and pads.
- Exposure and Development:The Gerber files are used to create a photomask, which is used to expose the photoresist to UV light. The areas of the photoresist that are exposed to light harden, while the unexposed areas remain soft. The soft areas are then washed away, leaving behind the pattern of traces and pads.
- Etching:The exposed copper is etched away using an acidic solution, leaving behind the desired pattern of conductive traces and pads. The etching process is carefully controlled to ensure that the minimum pad clearance is maintained.
- Drilling:Holes are drilled in the PCB for through-hole components and vias. The drilling process must be precise to ensure that the holes are properly aligned with the pads.
- Surface Finish:The exposed copper surfaces are coated with a surface finish to protect them from oxidation and facilitate soldering. Common surface finishes include HASL (Hot Air Solder Leveling), ENIG (Electroless Nickel Immersion Gold), and OSP (Organic Solderability Preservatives).
- Final Inspection:Once the PCB fabrication is complete, the finished boards undergo a final inspection to ensure that the minimum pad clearance and other specifications are met. Automated optical inspection (AOI) and other quality control measures may be used to verify the accuracy of the PCBs.
By following these steps carefully and adhering to the specified minimum pad clearance, manufacturers can produce PCBs that meet the required design criteria for reliable performance in electronic devices.
How much should a Minimum Pad Clearance PCB cost?
The cost of manufacturing a minimum pad clearance PCB can vary depending on several factors, including the complexity of the design, the size of the board, the number of layers, the quantity ordered, and the chosen PCB manufacturer. Generally, PCB fabrication costs are influenced by the following factors:
- Design Complexity:Complex designs with intricate layouts, smaller pad sizes, and tighter tolerances may require more advanced manufacturing processes and therefore incur higher costs.
- Board Size:Larger PCBs typically require more materials and processing time, leading to higher manufacturing costs compared to smaller boards.
- Number of Layers:Multi-layer PCBs, which contain multiple layers of conductive traces separated by insulating layers, are more expensive to manufacture than single-layer or double-layer boards due to the additional processing steps involved.
- Quantity Ordered:PCB manufacturers often offer volume discounts for larger quantities of PCBs ordered. Ordering in bulk can help reduce the cost per unit.
- Turnaround Time:Expedited fabrication services typically incur higher costs compared to standard turnaround times. If quick turnaround is required, it may come at an additional cost.
- Material Selection:The choice of materials, such as the substrate material and surface finish, can impact the overall cost of PCB fabrication.
- Additional Services:Additional services such as electrical testing, panelization, and special packaging may incur extra charges.
- Manufacturer Pricing: Different PCB manufacturers have varying pricing structures and capabilities. It’s essential to obtain quotes from multiple manufacturers to compare costs and services.
As for the specific cost of manufacturing a minimum pad clearance PCB, it’s challenging to provide an exact figure without knowing the details of the project. However, you can typically expect the cost to range from a few dollars for simple designs to tens or even hundreds of dollars for more complex or specialized requirements. It’s advisable to consult with PCB manufacturers and provide them with detailed specifications to obtain accurate cost estimates for your project.
What is the Minimum Pad Clearance PCB base material?
The choice of base material for a minimum pad clearance PCB depends on various factors such as the application, operating environment, desired electrical properties, and manufacturing process. However, one of the most commonly used base materials for PCBs is FR-4 (Flame Retardant 4).
FR-4 is a type of fiberglass-reinforced epoxy laminate that offers excellent mechanical strength, thermal stability, and electrical insulation properties. It is widely used in the electronics industry due to its affordability, availability, and compatibility with standard PCB fabrication processes.
FR-4 is available in various thicknesses and grades to accommodate different design requirements. It provides a stable substrate for mounting electronic components and forming conductive traces. Additionally, FR-4 is compatible with various surface finishes and soldering processes commonly used in PCB assembly.
While FR-4 is the most common choice for base material, other materials such as high-frequency laminates (e.g., Rogers materials), metal core PCBs, and flexible substrates may be used for specific applications that require special electrical or mechanical properties.
Ultimately, the selection of the base material for a minimum pad clearance PCB should be based on a careful evaluation of the project requirements, including thermal management, signal integrity, and cost considerations. Consulting with PCB manufacturers and materials suppliers can help determine the most suitable base material for your specific application.
Which company manufactures Minimum Pad Clearance PCBs?
Minimum pad clearance PCBs are typically manufactured by specialized PCB manufacturing companies. Some of the companies that produce such PCBs include Foxconn, JLCPCB, Shenzhen Xingming Electronics, Shenzhen ZHONGLIYI Technology, Proto Labs in the United States, and Eurocircuits in Italy.
As a professional PCB manufacturing company, our company has the capability to produce minimum pad clearance PCBs. We have advanced equipment and technologies to meet various complex PCB manufacturing requirements. Our engineering team is highly experienced and capable of devising the best production plans according to the design requirements of our customers.
Our manufacturing process strictly adheres to industry standards and quality management systems to ensure that the produced PCBs meet the requirements and expectations of our customers. We can provide customized solutions to meet the specific requirements of our customers for minimum pad clearance PCBs.
Whether it’s small-scale production or large-scale orders, we can provide services at competitive prices and deliver high-quality products. We focus on communication and collaboration with our customers to ensure that their needs are met in a timely manner. Additionally, we provide technical support and after-sales service to ensure that our customers can confidently choose us as their PCB manufacturing partner.
What are the 7 qualities of good customer service?
Good customer service is characterized by several key qualities that help to ensure positive interactions and experiences for customers. Here are seven qualities of good customer service:
- Responsiveness:Good customer service involves being attentive and responsive to customers’ needs, inquiries, and concerns in a timely manner. Responding promptly to customer inquiries and providing assistance when needed demonstrates attentiveness and care.
- Empathy:Empathy is the ability to understand and share the feelings of others. Good customer service involves showing empathy towards customers by listening to their concerns, acknowledging their emotions, and demonstrating understanding and compassion.
- Clarity:Clear communication is essential for good customer service. Providing clear and concise information, instructions, and explanations helps customers understand the products or services offered, as well as any processes or procedures involved.
- Professionalism: Professionalism involves maintaining a courteous, respectful, and professional demeanor when interacting with customers. This includes being polite, patient, and maintaining a positive attitude, even in challenging situations.
- Problem-solving skills:Good customer service representatives possess strong problem-solving skills and are able to effectively address and resolve customers’ issues or complaints. They actively listen to customers, identify the root cause of the problem, and work towards finding a satisfactory solution.
- Reliability:Reliable customer service involves consistently delivering on promises and commitments made to customers. This includes providing accurate information, delivering products or services on time, and following through on any resolutions or actions promised to customers.
- Personalization: Personalized customer service involves tailoring interactions and solutions to meet the specific needs and preferences of individual customers. Taking the time to understand customers’ unique circumstances, preferences, and preferences can enhance the customer experience and build loyalty.
By embodying these qualities, businesses can cultivate strong relationships with their customers, foster trust and loyalty, and ultimately drive customer satisfaction and retention.
FAQs
What is minimum pad clearance in PCB design?
Minimum pad clearance refers to the minimum allowable distance between pads on a printed circuit board (PCB). It ensures that there is enough space between adjacent pads to prevent unintended electrical connections or solder bridging during assembly.
Why is minimum pad clearance important in PCB design?
Minimum pad clearance is important because it helps prevent short circuits and solder bridging, ensuring reliable electrical connections and assembly of electronic components on the PCB.
How is minimum pad clearance determined in PCB design?
Minimum pad clearance is determined based on factors such as the manufacturing process, component size, and industry standards. Designers typically refer to manufacturer guidelines, IPC standards, and component datasheets to determine appropriate pad clearances.
What are the consequences of insufficient pad clearance?
Insufficient pad clearance can lead to electrical problems such as short circuits or solder bridging during assembly. This can result in product failures or malfunctions.
What are the industry standards for minimum pad clearance?
Industry standards such as IPC-2221 provide guidelines for minimum pad clearances in PCB design. These standards may vary depending on factors such as the type of component, soldering process, and operating environment.
Can minimum pad clearance be adjusted for specific applications?
Yes, minimum pad clearance can be adjusted based on the requirements of specific applications. Designers may need to consider factors such as high voltage, high frequency, or thermal management requirements when determining pad clearances.
What are some best practices for ensuring proper minimum pad clearance?
Best practices for ensuring proper minimum pad clearance include consulting manufacturer guidelines, IPC standards, and component datasheets; conducting thorough design reviews; and performing design rule checks (DRCs) using PCB design software.
Are there any limitations to reducing minimum pad clearance?
Yes, there are limitations to reducing minimum pad clearance, as excessively small clearances can increase the risk of solder bridging and manufacturing defects. Designers must balance the need for compact PCB layouts with the requirements for reliable assembly and operation.