Minimum Clearance Rogers PCBs Manufacturer
Minimum Clearance Rogers PCBs Manufacturer,Minimum Clearance Rogers PCBs are designed using advanced materials from Rogers Corporation, specifically tailored for high-frequency applications where signal integrity is critical. These PCBs feature minimum clearance between conductive traces to ensure superior performance in environments requiring high precision and reliability, such as aerospace, telecommunications, and automotive radar systems. The use of Rogers materials provides low loss and excellent dielectric constant properties, making these PCBs ideal for demanding RF/microwave applications where minimizing signal degradation is essential. Their robust design and material properties make them a preferred choice for engineers looking for high-performance circuit solutions.
What are Minimum Clearance Rogers PCBs?
Minimum clearance Rogers PCBs refer to printed circuit boards (PCBs) manufactured using Rogers Corporation’s high-performance substrates with specific minimum clearance requirements between conductive traces. Rogers Corporation produces a range of specialty materials optimized for RF/microwave applications, where maintaining signal integrity is crucial.
In RF/microwave PCB design, maintaining proper clearance between conductive traces is essential to prevent signal interference, crosstalk, and other undesirable effects that can degrade performance. Rogers PCBs typically have stringent requirements for minimum clearance to ensure optimal signal transmission and minimal signal loss.
These minimum clearance requirements are determined by factors such as the dielectric constant (εr) and thickness of the substrate material, operating frequency, and the desired level of performance. Designers must adhere to these specifications to ensure that the PCB meets the required performance criteria.
Rogers PCBs are commonly used in applications such as telecommunications, aerospace, defense, automotive radar systems, and high-frequency electronic devices where high performance and reliability are critical.
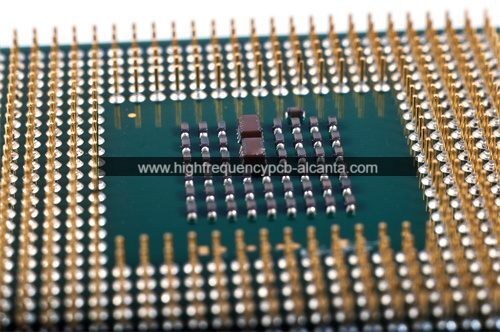
Minimum Clearance Rogers PCBs Manufacturer
What are the PCB Design Guidelines for Minimum Clearance Rogers PCBs?
Designing a PCB with Rogers substrates involves following specific guidelines to ensure optimal performance. Here are some key PCB design guidelines for achieving minimum clearance with Rogers PCBs:
- Understanding Substrate Properties:Familiarize yourself with the properties of the Rogers substrate you are using, including dielectric constant (εr), loss tangent (tan δ), thickness, and thermal properties. These parameters will influence the PCB design.
- Manufacturer’s Recommendations: Refer to the datasheets and application notes provided by Rogers Corporation for specific design guidelines and minimum clearance requirements for the chosen substrate material.
- Trace Width and Spacing: Determine appropriate trace widths and spacing based on the required impedance and minimum clearance specifications. Use PCB design software that allows you to calculate trace width and spacing based on the substrate properties and desired impedance.
- Keepout Zones:Establish keepout zones around critical signal traces to prevent adjacent traces, pads, or components from encroaching on the minimum clearance area. This ensures that there is no risk of electrical interference or short circuits.
- Via Placement: Carefully plan via placement to minimize their impact on signal integrity and to maintain adequate clearance between vias and signal traces. Avoid placing vias too close to high-speed signal traces to prevent signal distortion and impedance mismatch.
- Edge Clearance: Maintain sufficient edge clearance between signal traces and the board edge to prevent signal distortion and ensure manufacturability. The edge clearance should comply with both the substrate manufacturer’s recommendations and the PCB fabrication capabilities.
- Ground Plane Design: Implement a solid ground plane layer beneath signal layers to provide shielding and to minimize electromagnetic interference (EMI). Ensure that there is adequate clearance between signal traces and adjacent ground planes to maintain controlled impedance.
- High-Frequency Considerations: For high-frequency applications, such as RF and microwave circuits, pay special attention to maintaining controlled impedance, minimizing signal reflections, and optimizing signal integrity through proper trace routing and impedance matching techniques.
- Thermal Management: Consider thermal management requirements, especially if the PCB will be subjected to high temperatures or power dissipation. Ensure that clearance requirements are met while accommodating any thermal vias or heat dissipation features.
- Design Rule Checks (DRC): Use design rule checking (DRC) features in your PCB design software to verify that minimum clearance requirements are met throughout the layout. Run DRC checks regularly to identify and address any clearance violations.
By following these PCB design guidelines, you can ensure that your Rogers PCB design meets minimum clearance requirements while optimizing signal integrity, reliability, and manufacturability. Additionally, consulting with experienced RF/microwave PCB designers and manufacturers can provide valuable insights and assistance in achieving optimal performance.
What is the Minimum Clearance Rogers PCB Fabrication Process?
The fabrication process for Rogers PCBs with minimum clearance requirements typically follows standard PCB manufacturing procedures, but with extra attention to maintaining precise dimensions and ensuring the integrity of high-frequency signals. Here’s an overview of the minimum clearance Rogers PCB fabrication process:
- Substrate Selection: Choose the appropriate Rogers substrate material based on the specific requirements of your application, such as dielectric constant, thickness, and temperature stability. Rogers offers a range of high-performance substrates tailored for RF/microwave applications.
- Design Preparation: Prepare the PCB layout using PCB design software, adhering to the minimum clearance guidelines provided by Rogers Corporation and any specific requirements for your application. Pay close attention to trace widths, spacing, keepout zones, and edge clearance to ensure compliance with minimum clearance specifications.
- Gerber File Generation:Generate Gerber files and other manufacturing documentation from the PCB design software. Ensure that the Gerber files accurately represent the layout, including trace geometries, drill locations, and solder mask openings.
- Panelization: Arrange multiple PCB designs into a panel layout for efficient manufacturing. Panelization helps maximize material usage and streamlines the fabrication process.
- Preparation of Substrate Material: Cut the Rogers substrate material to the required panel size using precision cutting equipment. Ensure that the substrate material is clean and free from any contaminants that could affect the fabrication process.
- Copper Cladding: Apply copper foil to both sides of the substrate material using a lamination process. The copper foil thickness should meet the design specifications for trace impedance and conductivity.
- Etching: Use chemical etching or other methods to remove excess copper and define the trace patterns according to the PCB design. Etching is typically performed using acid or alkaline solutions that selectively dissolve the copper, leaving behind the desired trace patterns.
- Drilling:Drill holes for vias, component mounting, and other features using precision drilling equipment. Maintain tight tolerances to ensure alignment with the design specifications.
- Plating and Surface Finish:Plate the drilled holes with copper to establish electrical connections between layers. Apply surface finishes, such as immersion gold, HASL (Hot Air Solder Leveling), or ENIG (Electroless Nickel Immersion Gold), to protect the exposed copper and facilitate soldering.
- Solder Mask Application: Apply solder mask to the PCB surface, leaving openings for solder pads, vias, and other exposed copper areas. The solder mask helps protect the PCB from environmental factors and prevents solder bridges during assembly.
- Silkscreen Printing: Optionally, apply silkscreen printing for component labeling and reference designators. Silkscreen ink is applied to the PCB surface using a stencil-based printing process.
- Final Inspection: Perform a thorough inspection of the fabricated PCBs to verify dimensional accuracy, trace integrity, solder mask coverage, and surface finish quality. Any defects or discrepancies should be addressed before proceeding to assembly.
Following these fabrication steps with meticulous attention to detail and adherence to minimum clearance requirements ensures the successful production of high-quality Rogers PCBs optimized for RF/microwave applications. Working with experienced PCB manufacturers familiar with Rogers substrates can also help ensure the reliability and performance of the fabricated PCBs.
How do you manufacture Minimum Clearance Rogers PCBs?
Manufacturing Minimum Clearance Rogers PCBs requires specialized processes and careful attention to detail to ensure precise dimensions and signal integrity. Here’s a more detailed explanation:
- Material Preparation: Rogers substrates are carefully selected based on their dielectric properties, such as dielectric constant and loss tangent, to meet the specific requirements of the RF/microwave application. The substrate material is cut into panels of the desired size using precision cutting equipment.
- Copper Cladding: Copper foil is laminated onto both sides of the Rogers substrate using heat and pressure. The thickness of the copper foil is selected according to the design requirements for trace impedance and conductivity.
- Etching: The copper is then selectively etched away using chemical etchants to define the conductive traces according to the PCB layout. Etching is typically done using acid or alkaline solutions that dissolve the exposed copper, leaving behind the desired trace patterns.
- Drilling: Precision drilling equipment is used to drill holes for vias, component mounting, and other features. The drill holes must meet tight tolerances to ensure alignment with the design specifications.
- Plating and Surface Finish: The drilled holes are plated with copper to establish electrical connections between layers. Surface finishes such as immersion gold, HASL, or ENIG are applied to protect the exposed copper and facilitate soldering.
- Solder Mask Application: A solder mask is applied to the PCB surface, leaving openings for solder pads, vias, and other exposed copper areas. The solder mask helps protect the PCB from environmental factors and prevents solder bridges during assembly.
- Silkscreen Printing: Silkscreen printing may be used to apply component labels and reference designators to the PCB surface. Silkscreen ink is applied through a stencil-based printing process.
- Final Inspection: The fabricated PCBs undergo a comprehensive inspection process to verify dimensional accuracy, trace integrity, solder mask coverage, and surface finish quality. Any defects or discrepancies are identified and addressed before proceeding to assembly.
- Testing: Finally, the PCBs are subjected to electrical testing to ensure that they meet the required performance specifications. This may include tests for impedance matching, signal integrity, and reliability under operating conditions.
By following these manufacturing steps with precision and attention to detail, manufacturers can produce high-quality Minimum Clearance Rogers PCBs optimized for RF/microwave applications. Collaboration with experienced PCB manufacturers familiar with Rogers substrates can further ensure the reliability and performance of the fabricated PCBs.
How much should Minimum Clearance Rogers PCBs cost?
The cost of Minimum Clearance Rogers PCBs can vary depending on several factors, including the following:
- PCB Size and Complexity:Larger PCBs or those with intricate designs typically cost more to manufacture due to the increased material and production time required.
- Material Selection: Rogers substrates are high-performance materials designed for RF/microwave applications, and they can be more expensive compared to standard FR-4 substrates. The specific Rogers substrate chosen, along with its thickness and dielectric properties, will influence the overall cost.
- Layer Count: The number of layers in the PCB affects the fabrication complexity and, consequently, the cost. Minimum Clearance Rogers PCBs may require multiple layers to accommodate high-frequency signals and maintain signal integrity.
- Trace Density:Higher trace density and tighter minimum clearance requirements may increase manufacturing costs due to the need for more precise etching, drilling, and alignment processes.
- Surface Finish and Additional Features: Surface finishes such as immersion gold or ENIG, as well as additional features like blind and buried vias, impedance control, and controlled depth drilling, can add to the overall cost.
- Quantity:Economies of scale typically apply in PCB manufacturing, meaning that larger order quantities may result in lower per-unit costs. However, small production runs or prototypes may have higher costs per unit.
- Manufacturer and Location:PCB manufacturing costs can vary between different manufacturers and regions. Factors such as labor costs, overheads, and manufacturing capabilities can influence pricing.
To get an accurate cost estimate for Minimum Clearance Rogers PCBs, it’s essential to provide detailed specifications to PCB manufacturers, including PCB dimensions, layer count, material requirements, trace density, surface finish, and desired quantity. Requesting quotes from multiple manufacturers and comparing their offerings can help in finding the best balance between cost and quality for your specific project.
What is the base material used in Minimum Clearance Rogers PCBs?
The base material used in Minimum Clearance Rogers PCBs is typically a high-performance substrate manufactured by Rogers Corporation. Rogers offers a range of specialty materials specifically designed for RF/microwave applications, where maintaining signal integrity is critical. Some of the commonly used base materials for Minimum Clearance Rogers PCBs include:
- RO4000 Series: This series includes high-frequency laminates with a range of dielectric constants (εr) and low-loss tangents (tan δ). It is suitable for high-frequency applications up to microwave frequencies.
- RO3000 Series: Similar to the RO4000 series, the RO3000 series offers high-performance laminates with excellent electrical properties for RF/microwave circuits. These materials are often used in applications requiring low loss and high frequency.
- RO4400 Series: This series includes laminates with ceramic-filled PTFE (Polytetrafluoroethylene) substrates, offering high thermal conductivity and excellent stability over a wide temperature range. It is suitable for high-power applications and circuits operating at elevated temperatures.
- RO6000 Series: The RO6000 series comprises high-performance thermoset composite materials with low dielectric loss and excellent dimensional stability. These materials are suitable for high-frequency and high-speed digital applications.
These base materials offer consistent electrical performance, tight dimensional control, and excellent thermal stability, making them ideal for demanding RF/microwave applications. When designing Minimum Clearance Rogers PCBs, selecting the appropriate base material based on the specific requirements of the application is crucial for achieving optimal performance and reliability.
Which company manufactures Minimum Clearance Rogers PCBs?
Manufacturing Minimum Clearance Rogers PCBs is typically undertaken by professional PCB manufacturing companies. Globally, there are many companies that provide manufacturing services for Minimum Clearance Rogers PCBs. Some well-known companies include Rogers Corporation itself, as well as other specialized PCB manufacturers such as Sanmina, Mouser Electronics, Advanced Circuits, and others. These companies have advanced manufacturing equipment, extensive experience, and professional technical teams to meet the high-quality, high-performance requirements of customers for Minimum Clearance Rogers PCBs.
Our company is also a professional PCB manufacturer with extensive experience and advanced production equipment. Our manufacturing processes adhere to the strictest industry standards, ensuring the production of high-quality Minimum Clearance Rogers PCBs. Our advantages include:
- Professional Team: We have an experienced and skilled engineering team capable of providing professional PCB design and manufacturing advice to customers.
- Advanced Equipment:We use the most advanced PCB manufacturing equipment and technology to produce high-precision, high-quality Minimum Clearance Rogers PCBs.
- Quality Control: We strictly implement a quality management system, controlling every aspect from raw material procurement to production, to ensure that product quality meets customer requirements.
- Customized Services: We can provide customized services according to customers’ specific requirements, including different materials, sizes, layers, surface treatments, etc., to meet their specific needs
- Timely Delivery: We can deliver orders on time, ensuring that customer projects proceed as planned.
Whether it’s small batch production or large-scale orders, we can meet the needs of customers and provide them with high-quality Minimum Clearance Rogers PCB manufacturing services.
What are the 7 qualities of good customer service?
Good customer service is characterized by several key qualities that contribute to a positive customer experience. Here are seven qualities of good customer service:
- Responsiveness: Good customer service involves being responsive to customer inquiries, requests, and concerns in a timely manner. This includes promptly answering phone calls, responding to emails, and addressing customer issues in a timely fashion.
- Empathy: Empathy is essential in customer service. It involves understanding and acknowledging the customer’s feelings, concerns, and needs. Empathetic customer service representatives listen actively, show compassion, and strive to put themselves in the customer’s shoes to provide effective assistance.
- Clear Communication: Clear communication is crucial for effective customer service. Customer service representatives should communicate information clearly and concisely, using language that is easy for customers to understand. They should also actively listen to customers to ensure that they fully understand their needs and concerns.
- Problem-Solving Skills: Good customer service involves having strong problem-solving skills to effectively address customer issues and concerns. Customer service representatives should be resourceful, creative, and proactive in finding solutions to customer problems, even in challenging situations.
- Professionalism: Professionalism is important in customer service interactions. Customer service representatives should conduct themselves in a professional manner at all times, demonstrating courtesy, respect, and professionalism in their interactions with customers.
- Reliability: Reliability is another key quality of good customer service. Customers expect reliable service that is consistent and dependable. This includes delivering on promises, meeting commitments, and following through on customer requests in a reliable manner.
- Personalization:Personalization involves tailoring the customer service experience to meet the individual needs and preferences of each customer. This may include addressing customers by name, offering personalized recommendations or solutions, and providing a customized experience that makes the customer feel valued and appreciated.
By embodying these qualities, businesses can deliver exceptional customer service experiences that build customer loyalty, satisfaction, and trust.
FAQs
What are Minimum Clearance Rogers PCBs?
Minimum Clearance Rogers PCBs are printed circuit boards manufactured using high-performance substrates from Rogers Corporation with specific minimum clearance requirements between conductive traces. They are commonly used in RF/microwave applications where signal integrity is crucial.
Why are Minimum Clearance Rogers PCBs used?
Minimum Clearance Rogers PCBs are used in applications requiring high-frequency signal transmission, such as telecommunications, aerospace, defense, automotive radar systems, and high-frequency electronic devices. They offer excellent electrical performance, low signal loss, and reliable operation at high frequencies.
What are the key features of Minimum Clearance Rogers PCBs?
Key features of Minimum Clearance Rogers PCBs include high dielectric constant (εr), low loss tangent (tan δ), tight dimensional stability, excellent thermal conductivity, and precise impedance control. These features contribute to superior signal integrity and reliability.
What factors influence minimum clearance requirements in Rogers PCB design?
Minimum clearance requirements in Rogers PCB design are influenced by factors such as substrate material properties (dielectric constant, thickness), operating frequency, impedance requirements, signal integrity considerations, and fabrication capabilities.
How are Minimum Clearance Rogers PCBs fabricated?
Fabrication of Minimum Clearance Rogers PCBs involves processes such as substrate preparation, copper cladding, etching, drilling, plating, surface finishing, solder mask application, silkscreen printing, final inspection, and testing. These processes ensure precise dimensions and high-quality PCBs.
What are the benefits of using Minimum Clearance Rogers PCBs?
The benefits of using Minimum Clearance Rogers PCBs include superior signal integrity, reduced signal loss, enhanced performance at high frequencies, improved reliability, and compatibility with demanding RF/microwave applications.
Where can I find a reliable manufacturer for Minimum Clearance Rogers PCBs?
Reliable manufacturers for Minimum Clearance Rogers PCBs include specialized PCB manufacturing companies with expertise in RF/microwave applications, such as Rogers Corporation itself, as well as other reputable PCB manufacturers with experience in high-frequency circuitry and advanced materials. It’s advisable to choose a manufacturer with a proven track record, advanced facilities, and a commitment to quality.