Minimum Clearance LED Circuit Board Manufacturer
Minimum Clearance LED Circuit Board Manufacturer,Minimum Clearance LED Circuit Boards are specialized PCBs designed with minimal spacing between LED components and conductive traces. These boards are essential for high-density LED applications, ensuring efficient use of space and precise electrical routing. By minimizing clearance distances, they reduce signal interference and maximize light output efficiency, enhancing overall performance. Minimum Clearance LED Circuit Boards are crucial in applications requiring compact LED arrays, such as display panels, signage, and automotive lighting. Their design facilitates optimal thermal management and electrical reliability, contributing to long-term durability and consistent illumination in various lighting environments.
What is a Minimum Clearance LED Circuit Board (PCB)?
A Minimum Clearance LED Circuit Board (PCB) is a printed circuit board specifically designed for LED applications, characterized by a compact layout and optimized electrical performance. This type of PCB is commonly used in space-constrained devices, such as portable electronics and lighting systems, allowing for minimized component spacing without compromising electrical functionality.
When designing Minimum Clearance LED PCBs, several key factors are considered. Firstly, the electrical spacing must meet industry standards to ensure safety and stability, preventing short circuits or signal interference. Secondly, thermal management is crucial, as LEDs generate heat during operation. The PCB design must incorporate effective heat-dissipating materials and pathways to ensure that LEDs operate within safe temperature ranges, extending their lifespan.
Additionally, minimum clearance design requires precise routing techniques to avoid electromagnetic interference (EMI) and crosstalk. During manufacturing, high-precision etching and printing technologies are employed to achieve small spacings and high-density layouts, ensuring the reliability and performance of the PCB.
In summary, Minimum Clearance LED Circuit Boards play an important role in modern electronic products, addressing the increasing demand for slim designs. They are widely used in smartphones, tablets, LED lighting, and other high-tech devices.
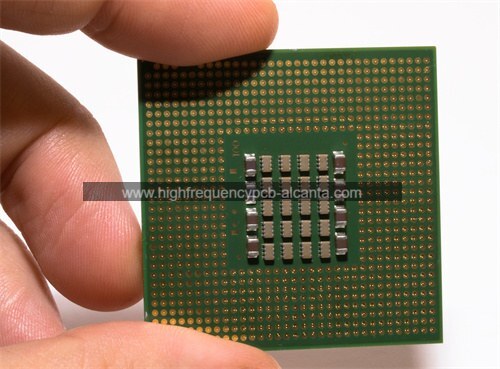
Minimum Clearance LED Circuit Board Manufacturer
What are the Minimum Clearance LED Circuit Board (PCB) Design Guidelines?
Here are some key design guidelines for Minimum Clearance LED Circuit Boards (PCBs):
- Electrical Spacing: Ensure that the minimum electrical clearance between traces meets industry standards to prevent short circuits and signal interference. This typically depends on the voltage levels used.
- Thermal Management:Incorporate thermal vias and heat sinks to dissipate heat generated by LEDs. Use materials with good thermal conductivity, such as copper or aluminum substrates, to manage heat effectively.
- Component Placement: Arrange components to minimize the distance between them while maintaining sufficient clearance for soldering and servicing. Ensure that heat-sensitive components are placed away from heat-generating LEDs.
- Trace Width Calculation: Use appropriate trace widths to handle the current load of the LEDs, considering factors such as temperature rise and PCB thickness. Refer to IPC-2221 standards for trace width calculations.
- Layer Stackup: Consider using multilayer PCBs if high-density designs are required. This can help in routing power and ground planes effectively, improving signal integrity and reducing noise.
- Signal Integrity: Minimize trace lengths and avoid sharp bends to reduce signal loss and electromagnetic interference (EMI). Use differential pairs if needed for high-speed signals.
- Manufacturing Tolerances: Design with the manufacturer’s capabilities in mind. Specify minimum feature sizes and spacing that align with the PCB fabrication processes, considering tolerances for etching and drilling.
- Testing and Validation:Plan for test points and design for manufacturability (DFM) to ensure that the PCB can be tested efficiently during production.
- Environmental Considerations: Choose materials that can withstand the operating environment, including temperature extremes and humidity. Consider conformal coatings for additional protection.
By following these guidelines, designers can create efficient, reliable Minimum Clearance LED PCBs that meet the demands of modern applications.
What is the Minimum Clearance LED Circuit Board (PCB) Fabrication Process?
The fabrication process for Minimum Clearance LED Circuit Boards (PCBs) involves several key steps:
- Design and Layout: Using PCB design software, the circuit layout is created with precise specifications for trace widths, spacing, and component placements, adhering to minimum clearance guidelines.
- Gerber File Generation: Once the design is complete, Gerber files are generated. These files contain the necessary data for manufacturing, including layer information, drill locations, and solder mask.
- Material Selection: Appropriate materials are chosen based on thermal and electrical requirements. Common substrates include FR-4, aluminum, or copper for enhanced thermal management.
- Photo-engraving: A photosensitive layer is applied to the substrate. The Gerber files are used to expose this layer, creating a pattern of the circuit layout.
- Etching: The unexposed areas of the copper are etched away using chemical solutions, leaving only the desired copper traces.
- Drilling: Holes for through-hole components and vias are drilled with precision to ensure proper alignment and clearance.
- Plating: The drilled holes are plated with copper to create electrical connections between different layers of the PCB, if applicable.
- Solder Mask Application:A solder mask layer is applied to protect the copper traces and prevent solder bridging during assembly. This layer is selectively removed from pad areas where components will be soldered.
- Silkscreen Printing: Component designators and other markings are printed onto the PCB surface for identification purposes.
- Final Inspection:The PCB undergoes visual and automated inspection processes to check for defects, ensuring that it meets design specifications.
- Cutting and Routing: The PCBs are then cut from the larger panel, and any necessary routing is performed to separate individual boards.
- Testing: Before delivery, the PCBs are tested for electrical integrity and functionality, ensuring they meet performance standards.
This fabrication process results in high-quality Minimum Clearance LED PCBs ready for assembly into final products.
How do you manufacture a Minimum Clearance LED Circuit Board (PCB)?
Manufacturing a Minimum Clearance LED Circuit Board (PCB) involves several key steps, ensuring precision and quality throughout the process:
- Design Creation:Begin with designing the PCB layout using CAD software. The design should adhere to minimum clearance guidelines for traces and components to optimize space while maintaining functionality.
- Gerber File Preparation: Generate Gerber files from the design. These files detail the layout, including copper layers, drill holes, and solder mask areas, serving as the blueprint for manufacturing.
- Material Selection: Choose appropriate substrate materials based on thermal and electrical needs. Common options include FR-4, aluminum, or copper-based materials for better heat dissipation.
- Photoresist Application: Coat the substrate with a photosensitive material. This layer will be used to create the circuit pattern during exposure.
- Exposure:Use the Gerber files to expose the photoresist to UV light, creating a negative image of the circuit layout. This step defines where copper will remain after etching.
- Development: After exposure, the photoresist is developed, removing the unexposed areas and leaving a protective layer on the desired copper traces.
- Etching: Submerge the board in an etching solution that removes the exposed copper, leaving only the intended circuit traces.
- Drilling: Precisely drill holes for through-hole components and vias. This step is critical for maintaining the minimum clearance requirements.
- Copper Plating: For multilayer PCBs, plate the drilled holes with copper to establish connections between layers.
- Solder Mask Application: Apply a solder mask to protect the copper traces and prevent solder bridging. The mask is selectively removed from areas where components will be soldered.
- Silkscreen Printing: Print identification markings, such as component designators, on the surface of the PCB.
- Cutting and Routing: Cut the PCB from the panel and perform any necessary routing to achieve the final shape.
- Inspection and Testing: Conduct visual and automated inspections to ensure quality. Perform electrical testing to verify functionality.
- Final Assembly: After passing inspection, the PCBs are ready for assembly into end products.
By following these steps, manufacturers can produce high-quality Minimum Clearance LED PCBs tailored to specific applications.
How much should a Minimum Clearance LED Circuit Board (PCB) cost?
The cost of a Minimum Clearance LED Circuit Board (PCB) can vary significantly based on several factors:
- Material Type: The choice of substrate (e.g., FR-4, aluminum, or copper) affects pricing, with specialized materials generally costing more.
- Board Complexity: More complex designs with intricate routing, multiple layers, and minimum clearance requirements will increase manufacturing costs.
- Quantity: Higher production volumes typically lower the cost per unit due to economies of scale.
- Size:Larger boards usually incur higher material and processing costs.
- Finishing Options: Additional features like surface finishes (e.g., ENIG, HASL), solder mask colors, and silkscreen can add to the cost.
- Turnaround Time: Faster delivery times may lead to increased costs.
On average, the price for a Minimum Clearance LED PCB can range from $1 to $20 per square inch, depending on these factors. For precise pricing, it’s best to obtain quotes from PCB manufacturers based on specific design requirements.
What is a Minimum Clearance LED Circuit Board (PCB) base material?
A Minimum Clearance LED Circuit Board (PCB) base material refers to the substrate used to support and electrically connect the components on the PCB. The choice of base material is crucial for performance, especially in LED applications where thermal management is important. Common base materials include:
- FR-4:A widely used fiberglass epoxy material that offers good electrical insulation and thermal stability. It’s cost-effective but may not provide the best thermal performance for high-power LEDs.
- Aluminum Substrate: Known for its excellent thermal conductivity, aluminum substrates help dissipate heat effectively, making them ideal for high-power LED applications.
- Copper Substrate: Provides even better thermal management than aluminum and is used in applications where heat dissipation is critical.
- Ceramic Substrate: Offers high thermal conductivity and electrical insulation, suitable for high-performance applications but typically at a higher cost.
- Flexible Materials: In some designs, flexible substrates may be used to create lightweight, bendable PCBs, although these may have different thermal properties.
Selecting the right base material is essential to ensure reliability, longevity, and optimal performance of Minimum Clearance LED PCBs.
Which company makes Minimum Clearance LED Circuit Boards (PCB)?
Many companies specialize in manufacturing Minimum Clearance LED Circuit Boards (PCBs), typically possessing advanced manufacturing technologies and expertise to meet high precision and performance requirements. Here are some well-known PCB manufacturers that provide Minimum Clearance LED PCB production services:
- Bantek Electronics: Bantek has extensive experience in PCB manufacturing, particularly for LED lighting and consumer electronics applications. They offer a variety of substrate options, including FR-4 and aluminum, to meet customer needs for thermal management and electrical performance.
- LCSC: LCSC is an online platform for electronic components and PCB manufacturing, offering rapid prototyping and mass production services. Their flexible manufacturing capabilities allow them to accommodate various minimum clearance design requirements.
- JLCPCB: As a large PCB manufacturer, JLCPCB is known for its cost-effectiveness and fast delivery. They support multilayer PCBs and special substrates suitable for LED applications.
- Giant Technology: Giant specializes in high-frequency and high-performance PCB manufacturing, particularly for LED lighting and RF applications. Their processes meet stringent size and performance standards.
- QZ Technology:This company provides LED PCB solutions, focusing on heat dissipation performance and electrical reliability, offering customized PCB design and manufacturing services.
Our company also has the capability to produce Minimum Clearance LED Circuit Boards (PCBs). We have advanced production equipment and an experienced technical team, providing high-quality PCB manufacturing services. Our advantages include:
- Customized Design: We can design PCBs based on specific customer requirements, including minimum clearance specifications, thermal solutions, and special substrate selections.
- Variety of Substrate Options: We offer multiple substrate choices, including FR-4, aluminum, and copper, ensuring that different applications’ thermal management and electrical performance needs are met.
- High Precision Manufacturing: Our manufacturing processes strictly adhere to international standards, ensuring PCB dimensional accuracy and quality stability.
- Fast Delivery: We provide expedited delivery options, capable of completing prototypes and mass production in a short timeframe to meet urgent customer needs.
- Comprehensive After-sales Service: We value customer feedback and needs, providing professional technical support and after-sales service to promptly resolve any issues encountered during use.
Through these advantages, our company is committed to becoming a trusted manufacturing partner for customers, fulfilling the application requirements of Minimum Clearance LED Circuit Boards across various fields.
What are the 7 qualities of good customer service?
Here are seven qualities of good customer service:
- Responsiveness: Quick and efficient responses to customer inquiries and issues demonstrate attentiveness and respect for their time.
- Empathy: Understanding and acknowledging customers’ feelings and concerns helps build rapport and trust, making customers feel valued.
- Clear Communication: Providing clear, concise, and accurate information helps prevent misunderstandings and ensures customers know what to expect.
- Knowledge: Well-trained staff who understand the products or services can provide accurate information and solve problems effectively.
- Patience: Taking the time to listen to customers and address their needs without rushing shows commitment to customer satisfaction.
- Professionalism: Maintaining a courteous and respectful demeanor, even in challenging situations, reflects positively on the company and fosters a positive customer experience.
- Follow-up: Checking in with customers after resolving an issue shows dedication to their satisfaction and can help strengthen customer loyalty.
FAQs
What is a Minimum Clearance LED PCB?
A Minimum Clearance LED PCB is a printed circuit board designed specifically for LED applications, featuring tightly packed components and traces to optimize space while ensuring electrical performance and thermal management.
Why is minimum clearance important in LED PCBs?
Minimum clearance is crucial to prevent short circuits, reduce electromagnetic interference (EMI), and ensure reliable operation of densely packed components, especially in high-density applications.
What materials are typically used for Minimum Clearance LED PCBs?
Common materials include FR-4, aluminum substrates for better thermal management, and copper substrates for high-performance applications.
How do you manage heat dissipation in Minimum Clearance LED PCBs?
Effective heat dissipation can be managed through thermal vias, heat sinks, and the use of materials with high thermal conductivity to ensure that LEDs operate within safe temperature ranges.
Can Minimum Clearance LED PCBs be manufactured in different sizes?
Yes, Minimum Clearance LED PCBs can be produced in various sizes and shapes according to the specific requirements of the application and design.
What is the typical lead time for manufacturing Minimum Clearance LED PCBs?
Lead times can vary based on complexity and volume, but standard manufacturing typically ranges from a few days to a few weeks. Expedited services may be available for urgent needs.
What are the typical costs associated with Minimum Clearance LED PCBs?
Costs can vary widely based on factors such as material choice, complexity, size, and quantity. It’s best to obtain quotes from manufacturers for accurate pricing.