Minimum Clearance Antenna PCB Manufacturer
Minimum Clearance Antenna PCB Manufacturer,Minimum Clearance Antenna PCBs are specialized circuit boards designed with minimal spacing between antenna elements and other components. These PCBs are optimized for wireless communication devices and antennas, ensuring efficient signal transmission and reception. By reducing clearance between conductive elements, they minimize signal loss and interference, enhancing overall antenna performance. Minimum Clearance Antenna PCBs are crucial in applications requiring compact and integrated antenna designs, such as IoT devices, mobile phones, and smart home technologies. Their precise manufacturing and layout considerations contribute to improved signal strength and reliability in wireless communication systems, supporting the advancement of modern connectivity solutions.
What is a Minimum Clearance Antenna PCB?
A Minimum Clearance Antenna PCB refers to a printed circuit board designed specifically to minimize the clearance distance between conductive elements, such as traces and pads, to achieve compact and efficient antenna designs. This type of PCB is crucial in applications where space is limited, such as in mobile devices, IoT sensors, and small electronic gadgets.
The key feature of a Minimum Clearance Antenna PCB is its ability to tightly integrate antenna structures with other electronic components without compromising performance. This integration reduces the overall size of the device while maintaining reliable signal transmission and reception capabilities.
Design considerations for such PCBs include optimizing trace widths, choosing suitable substrate materials with specific dielectric properties, and carefully planning the layout to minimize electromagnetic interference (EMI) and ensure signal integrity. Advanced manufacturing techniques like precision etching and controlled impedance are often employed to achieve the desired antenna characteristics.
In summary, a Minimum Clearance Antenna PCB is tailored for compact electronics requiring high-performance antenna systems in confined spaces, offering efficient signal handling while meeting stringent design requirements.
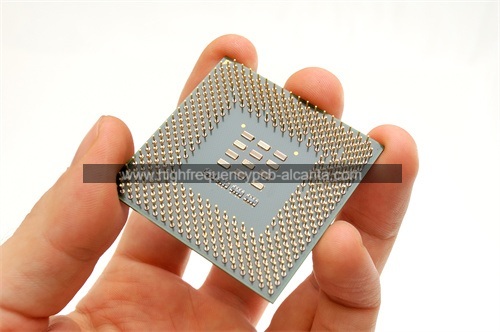
Minimum Clearance Antenna PCB Manufacturer
What are the Minimum Clearance Antenna PCB Design Guidelines?
Designing Minimum Clearance Antenna PCBs involves adhering to specific guidelines to ensure optimal performance and functionality. Here are some key design guidelines:
- Substrate Selection: Choose a substrate material with low dielectric constant (εr) to minimize signal loss and high thermal conductivity for efficient heat dissipation. Common materials include FR4, Rogers RO4003C, and polyimide for flexible PCBs.
- Antenna Placement and Size: Position the antenna elements away from other components to avoid interference. Size the antenna elements according to the operating frequency and desired radiation pattern.
- Trace Width and Impedance Matching: Design antenna traces with appropriate widths to achieve the desired impedance (typically 50 ohms for RF applications). Use controlled impedance techniques to maintain signal integrity and reduce reflections.
- Clearance and Spacing: Maintain minimum clearance distances between antenna traces, pads, and other conductive elements to prevent signal coupling and ensure isolation. This spacing is critical for minimizing electromagnetic interference (EMI).
- Grounding: Implement a solid ground plane beneath the antenna traces to provide shielding and reduce radiation losses. Ensure low impedance connections between the antenna ground and the main PCB ground.
- Via Placement:Place vias strategically to connect antenna traces to the ground plane without affecting signal integrity. Use stitching vias around the antenna to enhance grounding and reduce electromagnetic radiation.
- Radiation Pattern and Efficiency:Simulate and optimize the antenna design to achieve the desired radiation pattern and efficiency. Factors such as antenna shape, feed line design, and matching network optimization play crucial roles.
- Environmental Considerations: Consider the operating environment (temperature, humidity, etc.) and select materials and coatings that offer robust performance under varying conditions.
- Testing and Validation: Perform thorough testing and validation of the PCB prototype to ensure it meets the performance specifications for gain, bandwidth, efficiency, and impedance matching.
By following these guidelines, designers can create Minimum Clearance Antenna PCBs that deliver reliable wireless connectivity and meet the stringent requirements of modern compact electronic devices.
What is the Minimum Clearance Antenna PCB Fabrication Process?
The fabrication process for Minimum Clearance Antenna PCBs involves several key steps to ensure precise construction and optimal performance. Here’s an overview of the typical fabrication process:
- Design Preparation: Begin with a detailed PCB design that includes antenna specifications, layout, and dimensions. Use specialized software for antenna design and PCB layout to ensure accurate placement of components and traces.
- Substrate Selection: Choose a substrate material suitable for RF applications, such as FR4 or high-frequency laminates like Rogers RO4003C. Consider the dielectric constant (εr) and thermal properties to meet design requirements.
- Material Preparation: Prepare the chosen substrate material by cutting it to the required size and cleaning the surface to remove any contaminants that could affect adhesion or conductivity.
- Layer Stacking: If the design requires multilayer PCBs, stack and align the layers with precision. Ensure proper registration of inner layers to maintain signal integrity and minimize impedance variations.
- Copper Cladding: Apply copper foil to both sides of the substrate material through lamination or electrodeposition. The thickness and quality of the copper layer directly impact conductivity and signal transmission capabilities.
- Etching: Use chemical etching or laser ablation techniques to define the antenna traces and other conductive elements on the PCB. Ensure accurate trace widths and spacing according to design specifications to maintain impedance matching and signal integrity.
- Drilling and Vias: Drill holes for component mounting and via connections. Vias are plated with conductive material to establish electrical connections between different layers and ensure proper grounding and signal paths.
- Surface Finish: Apply a suitable surface finish to protect exposed copper traces and pads from oxidation and ensure solderability during component assembly. Common surface finishes include ENIG (Electroless Nickel Immersion Gold), HASL (Hot Air Solder Leveling), or OSP (Organic Solderability Preservatives).
- Masking and Silkscreen: Apply solder mask over non-conductive areas of the PCB to prevent solder bridges and ensure electrical insulation. Silkscreen printing is used to label components and indicate polarity, part numbers, and other necessary information.
- Quality Control: Conduct rigorous inspections and testing throughout the fabrication process to verify dimensional accuracy, layer alignment, trace continuity, and adherence to design specifications. Use automated optical inspection (AOI) and electrical testing to detect any defects or deviations.
- Final Assembly:After fabrication, assemble components onto the PCB using surface mount technology (SMT) or through-hole mounting techniques. Ensure proper alignment and soldering of components to complete the assembly process.
- Testing and Validation: Perform comprehensive testing of the assembled PCB to evaluate antenna performance, including gain, radiation pattern, impedance matching, and efficiency. Validate the PCB’s functionality under various operating conditions to ensure reliability and compliance with design requirements.
By following these fabrication steps meticulously, manufacturers can produce Minimum Clearance Antenna PCBs that meet the demanding performance criteria of modern wireless communication devices and applications.
How do you manufacture a Minimum Clearance Antenna PCB?
Manufacturing a Minimum Clearance Antenna PCB involves a detailed process to ensure precise construction and optimal performance for applications requiring compact, high-efficiency antenna designs. Here’s an expanded overview of the manufacturing process:
- Design Preparation: Begin by creating a detailed PCB design using specialized software tailored for antenna design and PCB layout. Define the antenna specifications, including frequency range, impedance, and radiation pattern requirements. Ensure the layout minimizes the clearance distance between antenna elements and other conductive features to achieve a compact design.
- Substrate Selection: Choose a substrate material that meets the specific requirements of RF applications. Common substrate materials include FR4 for general-purpose PCBs or high-frequency laminates like Rogers RO4003C for enhanced RF performance. Consider the substrate’s dielectric constant (εr), thermal properties, and compatibility with the manufacturing processes.
- Material Preparation: Prepare the substrate material by cutting it to the desired dimensions. Clean the surface thoroughly to remove any contaminants that could affect adhesion or conductivity during subsequent manufacturing steps.
- Layer Stacking: If the PCB design requires multiple layers, stack and align them with precision. Ensure proper registration of inner layers to maintain signal integrity and minimize impedance variations across the PCB.
- Copper Cladding: Apply copper foil to both sides of the substrate material through a lamination process or by electrodeposition. The thickness and quality of the copper layer are critical for conductivity and signal transmission capabilities. Control the copper thickness to match the design specifications for trace widths and impedance requirements.
- Etching: Define the antenna traces and other conductive elements on the PCB by etching away excess copper using chemical etching or laser ablation techniques. Ensure precise trace widths and spacing according to the design specifications to maintain impedance matching and signal integrity throughout the PCB.
- Drilling and Vias: Drill holes in the PCB for component mounting and via connections. Vias are plated with conductive material to establish electrical connections between different layers and ensure proper grounding and signal paths. Carefully place vias around antenna traces to enhance grounding and reduce electromagnetic interference (EMI).
- Surface Finish: Apply a suitable surface finish to protect exposed copper traces and pads from oxidation and ensure solderability during component assembly. Common surface finishes include ENIG (Electroless Nickel Immersion Gold), HASL (Hot Air Solder Leveling), or OSP (Organic Solderability Preservatives). Choose a surface finish that meets the PCB’s performance and environmental requirements.
- Masking and Silkscreen: Apply solder mask over non-conductive areas of the PCB to prevent solder bridges and ensure electrical insulation. Silkscreen printing is used to label components, indicate polarity, and provide essential information such as part numbers and manufacturing date.
- Quality Control: Implement rigorous quality control measures throughout the manufacturing process. Conduct inspections and testing to verify dimensional accuracy, layer alignment, trace continuity, and adherence to design specifications. Use automated optical inspection (AOI) and electrical testing to detect and rectify any defects or deviations promptly.
- Final Assembly: Once the PCB fabrication is complete and passes quality assurance tests, proceed with component assembly. Utilize surface mount technology (SMT) or through-hole mounting techniques to place and solder components onto the PCB. Ensure precise alignment and soldering to maintain the integrity of antenna elements and their connections.
- Testing and Validation: Perform comprehensive testing of the assembled Minimum Clearance Antenna PCB to evaluate antenna performance parameters. Conduct tests for gain, radiation pattern, impedance matching, and overall efficiency under various operating conditions. Validate the PCB’s functionality and reliability to ensure it meets the stringent requirements of the intended application.
By following these manufacturing steps systematically and with attention to detail, manufacturers can produce Minimum Clearance Antenna PCBs that deliver high-performance wireless communication capabilities in compact electronic devices and applications. This process integrates advanced design principles with precise manufacturing techniques to achieve optimal antenna performance and reliability.
How much should a Minimum Clearance Antenna PCB cost?
The cost of a Minimum Clearance Antenna PCB can vary significantly depending on several factors, including design complexity, materials used, production volume, and the manufacturer’s capabilities. Here are some factors that influence the cost:
- Design Complexity: The complexity of the PCB design, especially regarding the antenna layout and integration with other components, can affect costs. More intricate designs may require specialized manufacturing techniques and higher precision, impacting the overall cost.
- Materials:The choice of substrate material and copper thickness significantly influences cost. High-frequency laminates like Rogers RO4003C or specialty materials with enhanced dielectric properties tend to be more expensive than standard FR4.
- Production Volume: Economies of scale apply in PCB manufacturing. Larger production volumes generally lead to lower per-unit costs due to efficiencies in material procurement, production setup, and batch processing.
- Manufacturing Techniques: Specific manufacturing techniques required for Minimum Clearance Antenna PCBs, such as precise etching, controlled impedance, and advanced surface finishes, can contribute to higher costs compared to simpler PCB types.
- Testing and Quality Assurance: Rigorous testing and quality assurance processes, particularly for RF performance validation, add to the overall cost but are crucial to ensuring reliable antenna functionality.
- Supplier and Geographic Location: PCB manufacturing costs can vary based on the supplier’s location, labor costs, and regional economic factors.
In general, the cost of manufacturing a Minimum Clearance Antenna PCB can range from a few dollars per board for basic designs in larger quantities to tens or even hundreds of dollars per board for highly specialized designs with stringent performance requirements. Prototype and low-volume production runs typically incur higher costs per unit due to setup expenses and lower economies of scale.
For a precise cost estimate, it’s advisable to consult with PCB manufacturers or suppliers who can provide quotes based on specific design requirements, production volumes, and material selections. This allows for a tailored assessment considering all relevant factors impacting the final cost.
What is a Minimum Clearance Antenna PCB base material?
The base material used for Minimum Clearance Antenna PCBs plays a crucial role in determining their performance, especially in terms of RF characteristics and signal integrity. Here are some common base materials used for these PCBs:
- FR4 (Flame Retardant 4): FR4 is a widely used substrate material due to its cost-effectiveness and versatility. It’s composed of woven fiberglass cloth with an epoxy resin binder. FR4 has moderate dielectric constant (εr) around 4.0 to 4.8, which is suitable for many RF applications where strict impedance control is not critical.
- Rogers RO4003C:This is a high-frequency laminate designed specifically for RF and microwave applications. It features a ceramic-filled hydrocarbon resin system with low dielectric loss, providing excellent electrical performance at high frequencies. RO4003C typically has a dielectric constant of around 3.38.
- Rogers RO4350B:Another high-frequency laminate from Rogers, RO4350B offers improved thermal stability and lower dissipation factor compared to FR4. It’s suitable for applications requiring higher frequency operation and tighter impedance control.
- Polyimide: Polyimide substrates are used in flexible PCBs where bending or flexibility is required. They offer good thermal stability and can handle higher temperatures compared to standard FR4, making them suitable for applications where environmental factors are a concern.
- Isola IS680: IS680 is a low-loss, low-dielectric-constant laminate designed for high-speed digital and RF/microwave applications. It offers good electrical performance and thermal reliability, making it suitable for advanced PCB designs including Minimum Clearance Antenna PCBs.
When selecting a base material for Minimum Clearance Antenna PCBs, considerations include the operating frequency range, impedance requirements, thermal management needs, and overall performance goals. Higher-frequency applications typically benefit from low-loss materials with stable dielectric properties, such as Rogers laminates, whereas standard FR4 may suffice for lower-frequency designs with less stringent RF requirements.
Which company makes Minimum Clearance Antenna PCBs?
Currently, there are many companies manufacturing Minimum Clearance Antenna PCBs, typically possessing advanced capabilities in RF design and manufacturing to meet the demands for high-frequency, compact size, and excellent signal transmission performance. Major manufacturers include well-known PCB manufacturers such as Rogers Corporation in the United States, Hitachi Chemical in Japan, and LPKF Laser & Electronics in Germany.
Rogers Corporation specializes in high-performance materials and offers a variety of high-frequency PCB substrate materials like RO4003C and RO4350B, ideal for RF and microwave applications, making them suitable for producing Minimum Clearance Antenna PCBs. Hitachi Chemical, with its extensive experience and expertise in high-frequency PCBs, provides a range of advanced PCB materials and solutions.
LPKF Laser & Electronics is renowned for its advanced laser processing technology and expertise in RF design, offering customized PCB manufacturing services, particularly suitable for precision manufacturing of Minimum Clearance Antenna PCBs.
In addition, our company is also capable of manufacturing Minimum Clearance Antenna PCBs. We have advanced PCB design and manufacturing equipment to tailor high-performance RF PCBs according to specific customer requirements. Our production processes adhere strictly to international standards to ensure product quality and reliability. Our professional team possesses extensive RF engineering experience, capable of providing customized solutions to meet customer needs in fields such as communications, satellite navigation, and wireless sensor networks.
Our strengths include rapid response to customer needs, flexible production capabilities, and competitive pricing strategies. Whether for small-scale customization or large-scale production, we deliver high-quality, high-performance Minimum Clearance Antenna PCBs, providing reliable technical support and solutions for our customers’ innovative products.
What are the 7 qualities of good customer service?
Good customer service is characterized by several key qualities that contribute to a positive customer experience and foster customer satisfaction and loyalty. Here are seven important qualities:
- Responsiveness: Good customer service involves promptly addressing customer inquiries, concerns, and requests. This includes timely responses to emails, messages, and phone calls, as well as quick resolution of issues.
- Empathy: Empathy is essential in understanding and acknowledging the customer’s perspective and feelings. Good customer service representatives listen actively, show compassion, and demonstrate a genuine interest in helping resolve customer problems.
- Patience: Patience is crucial when dealing with customers, especially in challenging situations. Customer service professionals should remain calm, composed, and patient, even when faced with frustrated or upset customers.
- Clear Communication: Effective communication is fundamental in providing good customer service. This involves conveying information clearly and concisely, using language that is easy to understand, and ensuring that customers comprehend the information provided.
- Product Knowledge: Good customer service requires a thorough understanding of the products or services offered. Customer service representatives should be knowledgeable enough to answer questions, provide recommendations, and offer solutions based on customer needs.
- Problem-Solving Skills: The ability to effectively resolve customer issues and complaints is a critical aspect of good customer service. This includes identifying the root cause of problems, proposing solutions, and following through to ensure customer satisfaction.
- Professionalism: Professionalism encompasses various aspects, including politeness, respectfulness, and maintaining a positive attitude towards customers. It also involves maintaining confidentiality, adhering to company policies, and representing the brand in a positive light.
By embodying these qualities, businesses can cultivate strong customer relationships, enhance customer loyalty, and differentiate themselves in competitive markets through superior customer service experiences.
FAQs
What are Minimum Clearance Antenna PCBs?
Minimum Clearance Antenna PCBs are specialized printed circuit boards designed with minimal spacing between antenna elements and other conductive features. They are used to achieve compact antenna designs with optimal RF performance.
What are the advantages of Minimum Clearance Antenna PCBs?
These PCBs allow for compact and efficient antenna designs suitable for space-constrained applications. They help minimize signal loss and interference, thereby improving overall antenna performance.
Which industries use Minimum Clearance Antenna PCBs?
Industries such as telecommunications, satellite communications, wireless devices, IoT (Internet of Things), and aerospace often utilize Minimum Clearance Antenna PCBs for their high-frequency communication needs.
What materials are used to manufacture Minimum Clearance Antenna PCBs?
Common materials include high-frequency laminates like Rogers RO4003C or RO4350B, which offer excellent electrical performance and thermal stability necessary for RF applications.
How are Minimum Clearance Antenna PCBs different from standard PCBs?
Minimum Clearance Antenna PCBs are specifically designed to minimize the spacing between antenna elements and other conductive traces, whereas standard PCBs may not prioritize such tight integration for antenna performance.
What factors should be considered when designing Minimum Clearance Antenna PCBs?
Designers need to focus on impedance matching, signal integrity, electromagnetic interference (EMI) mitigation, and thermal management to ensure optimal antenna performance in compact spaces.
How can I ensure the reliability of Minimum Clearance Antenna PCBs?
It’s crucial to work with experienced PCB manufacturers who specialize in RF and high-frequency applications. Rigorous testing, including RF performance testing and quality assurance processes, helps ensure reliability.