Mini Led Pcb Manufacturing
Mini Led Pcb Manufacturing,Mini LED PCBs represent the forefront of display technology, offering unparalleled brightness, color accuracy, and contrast in various electronic applications. These PCBs are meticulously designed to accommodate Mini LEDs, which are smaller and more densely packed than traditional LEDs. Their compact size allows for higher pixel density, enabling the creation of stunningly sharp and detailed images in displays such as televisions, monitors, and digital signage. Mini LED PCBs excel in providing precise control over individual pixels, resulting in enhanced image quality and dynamic range. With advanced thermal management solutions, Mini LED PCBs efficiently dissipate heat, ensuring reliable performance and longevity. Customizable to specific design requirements, Mini LED PCBs offer versatility and adaptability for various display applications. As the demand for high-resolution, immersive displays continues to grow, Mini LED PCBs emerge as a key technology driving the evolution of next-generation visual experiences.
What is a Mini LED PCB?
A Mini LED PCB (Printed Circuit Board) is a type of circuit board specifically designed to accommodate Mini LEDs, which are smaller versions of traditional light-emitting diodes (LEDs). Mini LEDs are characterized by their smaller size and higher density, allowing for more precise control over brightness, color, and contrast in display applications.
The Mini LED PCB typically features a densely packed array of solder pads or contacts where the Mini LEDs are mounted. These PCBs are engineered to ensure efficient heat dissipation and electrical connectivity for the Mini LEDs. They may also include additional circuitry for controlling the LEDs, such as drivers or controllers.
Mini LED technology is often used in high-end displays, including televisions, monitors, and digital signage, where precise control over individual pixels is desired for enhanced image quality, brightness, and energy efficiency.
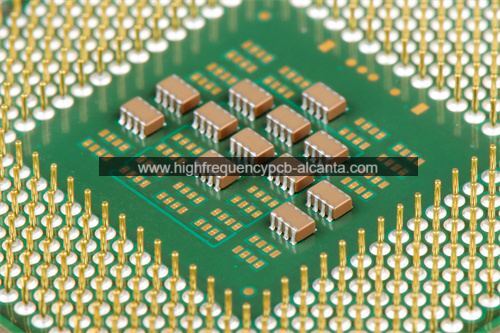
Mini Led Pcb Manufacturing
What are the Mini LED PCB Design Guidelines?
The Mini LED PCB design guidelines typically cover the following aspects:
- Layout Design: Ensure a compact and uniform layout of Mini LEDs to maximize display performance and brightness uniformity. Avoid placing too many circuit components around Mini LEDs to prevent interference with heat dissipation and optical performance.
- Thermal Management: Design the PCB to ensure effective heat dissipation for Mini LEDs, for example, by adding heat sinks or thermal vias. Optimize PCB materials and layer structure to enhance thermal conductivity.
- Electrical Connectivity: Ensure stable and reliable electrical connections between Mini LEDs and the PCB to avoid signal distortion or disconnection. Use appropriate soldering techniques and materials to ensure secure solder joints.
- Signal Integrity: Address signal integrity issues such as signal interference and reflection for high-speed signal transmission. Optimize PCB routing and layer structure to minimize signal transmission path length and interference.
- Power Management: Ensure stable and reliable power supply for Mini LEDs to avoid brightness and color instability. Consider layout and distribution of power lines to reduce power noise and fluctuations.
- Testing and Debugging: Design the PCB for easy testing and debugging, including adding test points, debugging interfaces, and circuit adjustment space. Ensure easy access to check the status and performance of Mini LEDs.
These guidelines are typically aimed at ensuring that Mini LED PCB designs achieve high-quality, stable, and reliable Mini LED display performance.
What is the Mini LED PCB Fabrication Process?
The Mini LED PCB fabrication process involves several steps:
- Design: The process begins with the design of the Mini LED PCB using specialized software. Engineers create a layout that includes the placement of Mini LEDs, electrical connections, and other components.
- Substrate Preparation: A substrate material, often fiberglass-reinforced epoxy laminate known as FR-4, is prepared. The substrate is typically in the form of a thin sheet or panel.
- Surface Preparation: The surface of the substrate is cleaned and prepared for the next steps, which may involve processes like chemical cleaning, rinsing, and drying to remove any contaminants.
- Layer Formation: Copper layers are deposited onto the substrate through processes such as electroplating or chemical vapor deposition (CVD). These copper layers form the conductive traces and pads for the Mini LEDs and other components.
- Photoresist Application: A layer of photoresist material is applied onto the copper surface. Photoresist is sensitive to light and is used to create a pattern on the copper layer.
- Exposure and Development: The photoresist layer is exposed to UV light through a photomask, which contains the desired pattern for the PCB. The exposed photoresist is then developed, revealing the copper areas that will remain after etching.
- Etching: The uncovered copper areas are etched away using an etchant solution, leaving behind the desired copper traces and pads based on the pattern defined by the photoresist.
- Strip and Clean: The remaining photoresist is stripped away, leaving behind the copper traces and pads on the substrate. The PCB is then cleaned to remove any residues from the etching and stripping processes.
- Through-hole Plating (if applicable): If the design includes through-holes for component mounting, they are plated with copper using processes like electroplating to ensure electrical connectivity between layers.
- Surface Finish: A surface finish is applied to protect the copper traces and pads from oxidation and to improve solderability. Common surface finishes include immersion gold, HASL (Hot Air Solder Leveling), and ENIG (Electroless Nickel Immersion Gold).
- Final Inspection: The finished Mini LED PCB undergoes visual inspection and electrical testing to ensure it meets quality standards and specifications.
- Assembly: Once the PCBs pass inspection, they can be assembled with Mini LEDs, other components, and connectors to create finished Mini LED display modules or products.
Each of these steps requires precision and careful control to ensure the Mini LED PCBs meet the required specifications for performance and reliability.
How do you manufacture a Mini LED PCB?
Manufacturing a Mini LED PCB involves several key steps:
- Design: The process begins with the design of the Mini LED PCB using specialized software such as CAD (Computer-Aided Design) software. Engineers create a layout that includes the placement of Mini LEDs, electrical connections, and other components.
- Material Selection: Select the appropriate substrate material for the PCB. FR-4 is a common choice due to its durability and electrical properties. Choose copper foil for the conductive layers.
- Preparation of Substrate: Cut the substrate material to the desired size and shape. Clean the substrate surface to remove any contaminants that could affect adhesion and conductivity.
- Copper Cladding: Laminate a thin layer of copper foil onto one or both sides of the substrate. This copper foil will form the conductive traces and pads for the Mini LEDs and other components.
- Photoresist Application: Apply a layer of photoresist material onto the copper-clad substrate using a process such as spin coating or spray coating.
- Exposure and Development: Use a photomask to expose the photoresist to UV light, creating a pattern that defines the circuit traces and pads. Develop the photoresist to remove the unexposed areas, leaving behind the patterned photoresist mask.
- Etching: Etch away the exposed copper using an etchant solution, leaving behind the desired copper traces and pads on the substrate. Rinse and neutralize the PCB to stop the etching process.
- Stripping: Remove the remaining photoresist from the PCB surface using a solvent or stripping solution.
- Surface Finishing: Apply a surface finish to protect the exposed copper traces and pads from oxidation and to improve solderability. Common surface finishes include HASL (Hot Air Solder Leveling), immersion gold, and ENIG (Electroless Nickel Immersion Gold).
- Drilling: Use a precision drilling machine to drill holes for through-hole components or vias that connect different layers of the PCB.
- Plating (if required): Plate the drilled holes with a conductive material such as copper to ensure electrical connectivity between layers.
- Final Inspection: Inspect the finished Mini LED PCB for defects, ensuring that all traces, pads, and holes meet design specifications.
- Assembly: Once the PCBs pass inspection, they can be assembled with Mini LEDs, other surface-mount components, and connectors to create finished Mini LED display modules or products.
Throughout the manufacturing process, strict quality control measures are implemented to ensure that the Mini LED PCBs meet the required specifications for performance, reliability, and durability.
How much should a Mini LED PCB cost?
The cost of a Mini LED PCB can vary significantly depending on various factors such as:
- Complexity of the design: More complex designs with densely packed Mini LEDs, intricate traces, and advanced features will typically cost more to manufacture.
- Size of the PCB: Larger PCBs generally require more materials and production time, leading to higher costs.
- Quantity ordered: Larger production runs usually result in lower per-unit costs due to economies of scale. Conversely, smaller quantities may have higher unit costs.
- Quality of materials: The choice of materials, such as the substrate type and surface finish, can impact the cost. Higher quality materials may command a higher price.
- Manufacturing processes: Certain fabrication processes, such as advanced multilayer construction, specialized coatings, or tight tolerances, can increase manufacturing costs.
- Manufacturer’s pricing structure: Different PCB manufacturers have varying pricing structures based on factors like overhead costs, labor rates, and profit margins.
As a rough estimate, Mini LED PCBs could range from a few dollars for simple designs in larger quantities to tens or even hundreds of dollars for complex designs or premium materials. For an accurate cost estimate, it’s best to consult with PCB manufacturers or suppliers directly, providing them with your specific design requirements, desired quantity, and any other relevant details. They can then provide a detailed quote based on your project specifications.
What is Mini LED PCB base material?
The base material used for Mini LED PCBs is typically similar to that of traditional PCBs. The most common base material is a type of fiberglass-reinforced epoxy laminate known as FR-4.
FR-4 consists of layers of woven fiberglass cloth impregnated with an epoxy resin binder. This material offers excellent electrical insulation properties, good dimensional stability, and moderate heat resistance, making it suitable for various electronic applications, including Mini LED PCBs.
In addition to FR-4, there are other base materials available for PCB fabrication, such as FR-1, FR-2, FR-3, and more advanced materials like metal core PCBs (MCPCBs) or ceramic PCBs. However, FR-4 is widely used in the industry due to its balance of performance, cost-effectiveness, and availability.
The choice of base material depends on factors such as the application requirements, thermal management needs, and budget considerations.
Which company makes Mini LED PCBs?
Currently, there are many companies specialized in the manufacturing of Mini LED PCBs. These companies include well-known electronics manufacturers, PCB fabricators, and firms focusing on LED technology. Some prominent names such as LG, Samsung, Huawei, Philips, Sony, among others, have deep expertise and production experience in the field of Mini LED technology.
In the PCB manufacturing sector, notable companies like Foxconn, TSMC, European Circuits (EPCB), and others have accumulated rich experience and technology in the production of Mini LED PCBs.
Our company also manufactures Mini LED PCBs. As a professional electronic manufacturing service provider, we possess advanced production equipment and extensive experience to meet various demands for Mini LED PCBs. With a dedicated engineering team, we can customize production according to customer design requirements while ensuring product quality and delivery schedules. Our production processes adhere strictly to international standards to ensure that our products meet industry requirements and customer expectations.
In addition to Mini LED PCBs, we offer one-stop electronic manufacturing solutions, including PCB design, component procurement, assembly, and testing services. Whether customers require small-batch rapid prototypes or large-scale mass production, we can provide high-quality, reliable products and services to contribute to the success of their projects.
In summary, our company has the technical expertise, production capacity, and professional team required for manufacturing Mini LED PCBs. We can meet various customer demands for Mini LED PCBs and provide high-quality electronic manufacturing solutions to our customers.
What are the 7 qualities of good customer service?
Good customer service is essential for building positive relationships with customers and fostering loyalty. Seven qualities of good customer service include:
- Responsiveness: Responding promptly to customer inquiries, concerns, and requests demonstrates that you value their time and are committed to addressing their needs in a timely manner.
- Empathy: Showing empathy involves understanding and acknowledging the customer’s feelings, perspectives, and situations. It helps create a supportive and personalized experience that can alleviate frustration and build trust.
- Professionalism: Maintaining professionalism in all interactions with customers instills confidence and trust in your organization. This includes being courteous, respectful, and maintaining a positive attitude even in challenging situations.
- Knowledgeability: Having thorough knowledge about your products or services, as well as company policies and procedures, enables you to provide accurate information and effectively assist customers with their inquiries and issues.
- Accessibility: Making your services easily accessible to customers through various channels such as phone, email, chat, or in-person support demonstrates your commitment to meeting their needs and preferences.
- Reliability: Consistently delivering on promises and commitments, such as fulfilling orders on time, providing accurate information, and resolving issues effectively, builds trust and reliability with customers.
- Problem-solving skills: Demonstrating effective problem-solving skills allows you to address customer concerns and resolve issues efficiently. It involves identifying root causes, offering solutions, and following up to ensure customer satisfaction.
By embodying these qualities, businesses can create positive customer experiences, strengthen relationships, and foster customer loyalty and advocacy.
FAQs
What are Mini LED PCBs?
Mini LED PCBs are printed circuit boards specifically designed to accommodate Mini LEDs, which are smaller versions of traditional LEDs. These PCBs are used in various display applications, offering enhanced brightness, color accuracy, and contrast.
What are the advantages of Mini LED PCBs?
Mini LED PCBs offer several advantages, including higher pixel density, improved brightness and contrast, enhanced color accuracy, and energy efficiency. They also allow for finer control over individual pixels, resulting in better image quality.
What are the applications of Mini LED PCBs?
Mini LED PCBs find applications in high-end displays such as televisions, monitors, digital signage, and automotive displays. They are also used in applications requiring precise lighting control, such as backlighting for keyboards and indicator lights.
How are Mini LED PCBs different from traditional LED PCBs?
Mini LED PCBs differ from traditional LED PCBs mainly in the size and density of the LEDs used. Mini LEDs are smaller in size and can be densely packed on the PCB, allowing for higher resolution and improved performance in display applications.
What factors should be considered when designing Mini LED PCBs?
Designing Mini LED PCBs requires considerations such as Mini LED placement, thermal management, electrical connectivity, signal integrity, and power management. These factors ensure optimal performance, reliability, and longevity of the display.