Mini LED PCB Fabrication
Mini LED PCB Fabrication,Mini LED PCBs are specialized circuit boards designed to accommodate miniaturized Light Emitting Diodes (LEDs) with high density and precision. These PCBs feature densely packed LED arrays, often with fine pitch and high-resolution placements to achieve uniform light distribution and enhance display performance. They are engineered with advanced thermal management to dissipate heat efficiently, ensuring longevity and reliability of the LEDs. Mini LED PCBs find applications primarily in high-definition displays, where they enable brighter, more vibrant images with improved contrast and energy efficiency. Their compact design and robust construction make them integral to next-generation display technologies across various industries.
What is a Mini LED PCB?
A Mini LED PCB (Printed Circuit Board) is a specialized type of circuit board designed to accommodate Mini LEDs, which are significantly smaller than traditional LEDs. These Mini LEDs are used to create more precise and efficient lighting and display solutions. The Mini LED technology is characterized by its high brightness, better contrast, and energy efficiency, making it particularly suitable for modern applications such as high-definition televisions, advanced computer monitors, and premium mobile devices.
The structure of a Mini LED PCB is tailored to handle the dense packing of Mini LEDs, which can be as small as 0.2 mm. This high density allows for more individual LEDs to be used in a given area, enhancing the display’s resolution and overall performance. The PCB must be designed to manage the heat generated by these numerous LEDs, which involves using materials with high thermal conductivity, such as aluminum or copper substrates, and incorporating thermal vias and heat sinks.
Manufacturing a Mini LED PCB involves precise techniques to ensure that the Mini LEDs are accurately placed and soldered onto the board. This often requires advanced surface-mount technology (SMT) and careful inspection to prevent defects that could affect the performance of the final product. Additionally, the PCB design must support the complex driving electronics necessary to control the Mini LEDs, which includes integrated circuits (ICs) that manage brightness, color accuracy, and synchronization.
In summary, a Mini LED PCB is a crucial component in modern display and lighting technologies, providing the foundation for high-performance and energy-efficient solutions. Its design and manufacturing involve advanced materials and techniques to support the unique requirements of Mini LED technology.
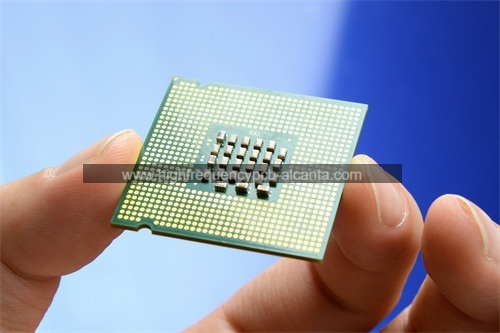
Mini LED PCB Fabrication
What are the Mini LED PCB Design Guidelines?
Designing a Mini LED PCB involves several specific guidelines to ensure optimal performance and reliability. Here are some key guidelines:
- Substrate Material: Choose a substrate material with good thermal conductivity, such as aluminum or copper. These materials help in efficiently dissipating heat generated by Mini LEDs.
- Thermal Management: Implement thermal vias and heat sinks to enhance thermal management. Thermal vias help in transferring heat from the LEDs to the PCB substrate and then to the external environment.
- Component Placement: Ensure precise placement of Mini LEDs on the PCB. The placement affects light uniformity and heat dissipation. Use automated assembly techniques for accurate positioning.
- Electrical Routing: Plan for efficient electrical routing to minimize impedance and signal loss. High-frequency signals associated with Mini LED drivers require controlled impedance traces.
- Power Supply: Design a stable and efficient power supply circuitry. Ensure adequate power delivery to the Mini LEDs and associated control electronics.
- Protection Circuitry:Incorporate protection circuitry such as over-voltage protection and reverse polarity protection to safeguard the Mini LEDs and other components from damage.
- Manufacturability: Design the PCB with manufacturability in mind. Consider the capabilities of PCB assembly processes, such as pick-and-place machines for Mini LED placement.
- Testing and Inspection: Plan for testing and inspection procedures to verify the functionality and quality of the Mini LED PCBs. Automated optical inspection (AOI) can help detect soldering defects and placement errors.
- Environmental Considerations: Consider environmental factors such as humidity and temperature variations. Design the PCB to withstand environmental stresses and ensure long-term reliability.
- Compliance and Standards: Ensure compliance with relevant industry standards and regulations, such as RoHS (Restriction of Hazardous Substances) and EMC (Electromagnetic Compatibility) standards.
By adhering to these design guidelines, engineers can create Mini LED PCBs that deliver optimal performance, reliability, and longevity in applications ranging from high-resolution displays to advanced lighting systems.
What is the Mini LED PCB Fabrication Process?
The fabrication process of Mini LED PCBs involves several precise steps to ensure the proper assembly of components and the creation of a functional circuit board. Here’s a generalized overview of the Mini LED PCB fabrication process:
- Design and Layout: The process begins with designing the PCB layout using specialized CAD (Computer-Aided Design) software. Engineers lay out the positions of Mini LEDs, control electronics, thermal vias, heat sinks, and other components according to the design requirements.
- Material Selection: Select appropriate materials for the PCB substrate based on thermal conductivity and electrical performance requirements. Aluminum or copper substrates are commonly used due to their excellent thermal properties.
- Preparation of Substrate: Prepare the substrate material by cleaning and applying a thin layer of dielectric material if needed. This dielectric layer helps in insulating the conductive layers that will be added later.
- Layer Deposition:Use techniques such as sputtering or electroplating to deposit thin layers of conductive material (typically copper) onto the substrate. These layers form the traces and pads that will connect the Mini LEDs and other components.
- Photoresist Application: Apply a layer of photoresist material over the conductive layers. Photoresist is sensitive to light and is used to create the pattern of the PCB traces and pads.
- Exposure and Development: Use a UV light source to expose the photoresist through a photomask that defines the PCB’s circuit pattern. After exposure, the unexposed photoresist is washed away in a developing solution, leaving behind the patterned photoresist.
- Etching: Etch away the exposed copper (or other conductive material) using chemical etchants. The photoresist acts as a mask, protecting the areas of copper that form the desired circuit pattern. Once etched, the remaining photoresist is removed.
- Drilling:Drill holes for vias and component mounting pads using precision drilling machines. These holes will facilitate electrical connections between different layers of the PCB and allow components to be mounted.
- Surface Finish: Apply a surface finish to protect exposed copper and facilitate soldering. Common surface finishes include HASL (Hot Air Solder Leveling), ENIG (Electroless Nickel Immersion Gold), or OSP (Organic Solderability Preservatives).
- Solder Mask Application: Apply solder mask over the entire PCB surface, except for the areas where electrical connections (pads) need to be exposed for soldering components. Solder mask protects the PCB from environmental factors and prevents unintended electrical connections.
- Silkscreen Printing: Optionally, apply silkscreen printing for labeling component outlines, reference designators, and other markings on the PCB surface. This helps during assembly and testing phases.
- Component Assembly: Use automated pick-and-place machines to accurately place Mini LEDs, ICs, resistors, capacitors, and other components onto their designated pads on the PCB. The components are soldered onto the pads using reflow soldering techniques.
- Testing and Inspection: Conduct electrical testing and visual inspection to ensure that all components are properly soldered, and there are no defects in the PCB. Automated optical inspection (AOI) and functional testing are commonly used.
- Final Packaging:After testing and inspection, cut the PCB panels into individual boards if necessary. Prepare the PCBs for final assembly into their respective products or systems.
- Quality Assurance: Implement quality control measures throughout the fabrication process to ensure consistency and reliability of the Mini LED PCBs.
Each step in the Mini LED PCB fabrication process requires precision and adherence to standards to produce high-quality PCBs suitable for advanced display and lighting applications.
How do you manufacture a Mini LED PCB?
Manufacturing a Mini LED PCB involves a series of meticulous steps to ensure the board meets performance and reliability standards. Here’s a detailed outline of the manufacturing process:
- Design and Layout: Begin by creating a detailed PCB layout using CAD software. Place Mini LEDs, control electronics, thermal management features, and other components according to the design specifications.
- Material Selection: Choose a suitable substrate material such as aluminum or copper based on thermal conductivity requirements. Select high-quality dielectric materials for insulation and optimal electrical performance.
- Substrate Preparation: Clean and prepare the substrate material to ensure it is free from contaminants. Apply a thin layer of dielectric material if necessary to insulate conductive layers.
- Conductive Layer Deposition: Deposit thin layers of conductive material (typically copper) onto the substrate through processes like sputtering or electroplating. These layers form the circuit traces and pads that will connect components.
- Photoresist Application: Apply a layer of photoresist over the conductive layers. Photoresist will define the pattern of the PCB traces and pads.
- Exposure and Development: Use UV light to expose the photoresist through a photomask that defines the PCB pattern. Develop the exposed photoresist to reveal the underlying conductive layers.
- Etching: Etch away the exposed copper using chemical etchants, leaving behind the desired circuit pattern defined by the photoresist.
- Drilling: Precision drill holes for vias and component mounting pads using CNC drilling machines. These holes facilitate electrical connections between layers and provide mounting points for components.
- Surface Finish: Apply a surface finish such as HASL (Hot Air Solder Leveling), ENIG (Electroless Nickel Immersion Gold), or OSP (Organic Solderability Preservatives) to protect exposed copper and facilitate soldering.
- Solder Mask Application: Apply solder mask over the PCB surface, leaving openings for component pads. Solder mask protects the PCB from environmental factors and prevents solder bridges during assembly.
- Silkscreen Printing: Optionally, apply silkscreen printing for component outlines, reference designators, and other markings to aid in assembly and testing.
- Component Assembly: Use automated pick-and-place machines to accurately position Mini LEDs, ICs, resistors, capacitors, and other components onto their designated pads. Components are then soldered onto the PCB through reflow soldering.
- Testing and Inspection: Conduct electrical tests (e.g., continuity, impedance) and visual inspections to verify proper component placement and solder connections. Automated optical inspection (AOI) ensures quality and detects defects.
- Finalization: Cut PCB panels into individual boards if necessary. Prepare the Mini LED PCBs for integration into final products or systems.
- Quality Assurance: Implement stringent quality control measures throughout the manufacturing process to ensure reliability and performance consistency of the Mini LED PCBs.
By following these steps with precision and attention to detail, manufacturers can produce Mini LED PCBs that meet the high standards required for advanced display and lighting applications.
How much should a Mini LED PCB cost?
The cost of a Mini LED PCB can vary widely depending on several factors such as size, complexity, materials used, quantity ordered, and manufacturing processes involved. However, to give you a rough estimate:
- Basic Mini LED PCB: For a simple Mini LED PCB without complex features, the cost could range from $1 to $10 per square inch.
- High-End Mini LED PCB:For advanced Mini LED PCBs with features like high-density Mini LED placement, specialized substrates (e.g., aluminum or copper), advanced thermal management (e.g., metal core PCBs), and precise manufacturing tolerances, the cost can range from $10 to $50 or more per square inch.
- Volume Discounts:Ordering larger quantities typically reduces the per-unit cost due to economies of scale.
- Additional Costs: Consider additional costs such as tooling fees, setup charges, and testing/quality assurance procedures, which can impact the overall cost.
- Customization and Complexity: Customized designs, special requirements (e.g., specific certifications), and additional features (e.g., multilayer PCBs, advanced surface finishes) will also affect the cost.
It’s important to obtain quotes from multiple PCB manufacturers to get a more accurate estimate tailored to your specific requirements. Factors like the manufacturer’s location and capabilities also play a role in pricing. Additionally, consider the total cost of ownership, including factors such as reliability, lead times, and support provided by the PCB manufacturer.
What is Mini LED PCB base material?
The base material used for Mini LED PCBs is crucial for achieving optimal thermal management, electrical performance, and overall reliability. Here are the common base materials used:
- Metal Core PCB (MCPCB): This is the most widely used base material for Mini LED PCBs. MCPCBs typically have a metal core (usually aluminum or copper) as the base layer, which provides excellent thermal conductivity. The metal core helps to efficiently dissipate heat generated by the Mini LEDs, thereby preventing overheating and ensuring reliable operation.
- Aluminum Substrate: Aluminum-based PCBs are lightweight and offer good thermal conductivity. They are cost-effective and suitable for applications where moderate thermal management is required.
- Copper Substrate: Copper-based PCBs provide even higher thermal conductivity compared to aluminum. They are used in applications where superior heat dissipation capabilities are needed, such as high-power Mini LED applications.
- Composite Materials: Some Mini LED PCBs may use composite materials that combine different substrates or include additional layers for specific performance requirements. For instance, fiberglass-reinforced materials with a metal core layer can provide both mechanical strength and thermal conductivity.
The choice of base material depends on factors such as the power density of the Mini LEDs, thermal management requirements, mechanical strength needed for the application, and cost considerations. Manufacturers often select the base material based on these factors to ensure the Mini LED PCB meets performance standards and reliability requirements.
Which company makes Mini LED PCBs?
Many companies have expertise and technological advantages in manufacturing Mini LED PCBs worldwide. For example, electronic manufacturing companies and PCB manufacturers like Mitsubishi Electric in Japan, Luxshare Precision in Taiwan, Samsung Electronics in South Korea, and leading intelligent manufacturing enterprises in mainland China have accumulated rich experience and technical capabilities in the development and application of Mini LED technology.
If our company also wants to enter the field of Mini LED PCB manufacturing, we need to have the following capabilities and advantages:
- Technical R&D Capability: Our company should have a strong technical team, including circuit design engineers, PCB designers, thermal management experts, etc. They need to master the design principles and technical details of Mini LED PCBs to provide customized designs according to customer requirements.
- Manufacturing Equipment and Processes: The company needs to invest in advanced manufacturing equipment and process flows, such as high-precision PCB processing equipment, SMT placement machines, reflow soldering ovens, etc., to ensure the production of high-quality Mini LED PCBs.
- Quality Control and Certification: To ensure product quality and compliance with international standards, the company should establish a strict quality control system, including inspection of raw materials, process control during production, and testing and certification of final products.
- Cost Control and Supply Chain Management: Cost control is crucial in manufacturing Mini LED PCBs. The company needs to effectively manage the supply chain to ensure stable supply of raw materials at reasonable procurement costs, optimize production processes, and reduce manufacturing costs.
- Customer Service and Technical Support: The company should provide excellent customer service and technical support, work closely with customers to understand their needs, and provide customized solutions. Timely response to customer inquiries and feedback helps build strong partnerships.
In summary, although the competition in the field of Mini LED PCB manufacturing is fierce, our company can establish a foothold in the market by continuously improving technical capabilities, ensuring quality assurance, and providing excellent customer service. By producing high-performance and reliable Mini LED PCBs, we can support and safeguard the products of our customers effectively.
What are the 7 qualities of good customer service?
Good customer service is characterized by several key qualities that enhance customer satisfaction and build strong relationships. Here are seven essential qualities:
- Responsiveness:Good customer service involves being prompt and proactive in addressing customer inquiries, concerns, and requests. This includes responding quickly to emails, phone calls, and messages, and taking swift action to resolve issues.
- Empathy: Empathy is crucial in understanding and acknowledging the customer’s feelings, concerns, and perspectives. It involves listening actively, showing genuine concern, and putting oneself in the customer’s shoes to provide appropriate assistance and support.
- Clarity: Effective communication is essential for good customer service. Clearly conveying information, instructions, and solutions helps customers understand and navigate through their issues or questions easily.
- Professionalism:Maintaining a professional demeanor at all times, whether in written or verbal communication, is key. This includes being courteous, respectful, and maintaining a positive attitude even in challenging situations.
- Knowledgeability: Good customer service representatives are knowledgeable about their products, services, and company policies. They should be able to provide accurate information, answer questions confidently, and offer helpful advice or recommendations.
- Problem-solving skills: Being able to effectively identify, analyze, and resolve customer issues or complaints is a critical aspect of good customer service. This involves being resourceful, proactive, and persistent in finding solutions that meet the customer’s needs.
- Personalization: Tailoring interactions to the specific needs and preferences of each customer enhances the customer experience. This includes remembering customer preferences, past interactions, and personalizing recommendations or solutions accordingly.
By embodying these qualities, companies can deliver exceptional customer service that not only meets but exceeds customer expectations, leading to increased customer loyalty, positive word-of-mouth, and sustainable business growth.
FAQs
What are Mini LED PCBs?
Mini LED PCBs are specialized printed circuit boards designed to accommodate Mini LEDs, which are smaller and more densely packed than traditional LEDs. They are used primarily in high-resolution displays and advanced lighting applications.
What are the advantages of Mini LED PCBs?
Mini LED PCBs offer several advantages, including higher brightness, better contrast ratios, improved energy efficiency, and enhanced color accuracy compared to conventional LED technologies. They also support finer pixel pitches, leading to sharper images in displays.
How are Mini LED PCBs different from regular PCBs?
Mini LED PCBs differ from regular PCBs primarily in their design and manufacturing requirements. They are optimized for thermal management to handle the heat dissipation from densely packed Mini LEDs. They also require precise placement and control electronics to manage individual Mini LEDs effectively.
What applications are Mini LED PCBs used in?
Mini LED PCBs are used in various applications such as high-definition televisions (HDTVs), gaming monitors, virtual reality (VR) headsets, automotive displays, and high-end signage. They are also becoming popular in backlighting for LCD panels.
What factors should be considered when designing Mini LED PCBs?
Design considerations for Mini LED PCBs include thermal management (using materials with high thermal conductivity), precise placement of Mini LEDs for uniform lighting, electrical routing for signal integrity, and integration of control electronics for brightness and color control.
How can Mini LED PCBs enhance display performance?
Mini LED PCBs contribute to enhanced display performance by offering higher brightness levels, improved contrast ratios for deeper blacks, wider color gamut capabilities, and better HDR (High Dynamic Range) performance. They enable manufacturers to achieve more vibrant and lifelike visuals.
Are Mini LED PCBs cost-effective?
While Mini LED technology can initially involve higher costs due to specialized manufacturing and materials, advancements are reducing costs over time. The long-term benefits, such as energy efficiency and improved performance, often justify the investment in Mini LED PCBs for premium display applications.