Mini Ceramics PCB Manufacturing
Mini Ceramics PCB Manufacturing,Mini Ceramics PCB manufacturing refers to the process of producing small-sized printed circuit boards (PCBs) using ceramic materials. These PCBs are characterized by their compact size and exceptional performance, making them suitable for applications requiring high reliability and precision. The manufacturing process typically involves several steps, including substrate preparation, layering, patterning, and component assembly. Ceramic materials offer advantages such as excellent thermal stability, high mechanical strength, and low dielectric loss, making them ideal for miniaturized electronic devices operating in harsh environments. Mini Ceramics PCBs find applications in various industries, including aerospace, medical devices, and automotive electronics, where space constraints and performance demands are critical. The manufacturing process for Mini Ceramics PCBs requires specialized equipment and expertise to ensure high precision and quality. Overall, Mini Ceramics PCB manufacturing plays a vital role in advancing technology by enabling the development of smaller, more efficient, and reliable electronic devices for diverse applications.
What is a Mini Ceramics PCB?
As of my last update in January 2022, “Mini Ceramics PCB” does not appear to be a widely recognized term in the field of electronics or PCB (Printed Circuit Board) manufacturing. However, it’s possible that it could refer to a specialized type of PCB designed for specific applications or industries.
One interpretation could be that it refers to a small-sized PCB (hence “Mini”) made with ceramics as the base material. Ceramics have different properties compared to traditional PCB materials like fiberglass or epoxy resin. Ceramics offer advantages such as high thermal conductivity, excellent electrical insulation, and resistance to high temperatures. These properties make ceramics suitable for applications where heat dissipation or high-frequency signals are critical, such as in RF (radio frequency) electronics or power electronics.
A “Mini Ceramics PCB” could potentially be used in compact electronic devices where space is limited and where the unique properties of ceramic materials are advantageous. However, without further context or specific information, it’s difficult to provide a definitive explanation of what a “Mini Ceramics PCB” exactly refers to.
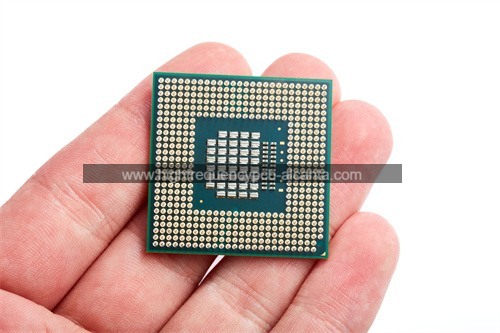
Mini Ceramics PCB Manufacturing
What are the Mini Ceramics PCB Design Guidelines?
Design guidelines for Mini Ceramics PCBs may vary depending on the specific requirements of the application and the characteristics of the ceramic material being used. However, here are some general guidelines that may apply:
- Thermal Management: Ceramic materials have good thermal conductivity, but efficient thermal management is still crucial, especially in applications with high power dissipation. Ensure that the PCB layout allows for proper heat dissipation, possibly including heat sinks or thermal vias.
- Material Selection: Choose ceramic materials with appropriate properties for the intended application, considering factors such as dielectric constant, thermal conductivity, and mechanical strength.
- Signal Integrity: Pay attention to signal integrity issues, such as impedance control, signal routing, and minimizing electromagnetic interference (EMI). High-frequency applications may require controlled impedance traces and careful signal routing to minimize signal degradation.
- Component Placement: Optimize component placement to minimize signal path lengths, reduce parasitic capacitance and inductance, and ensure efficient heat dissipation. Consider the thermal properties of components and their proximity to heat sources.
- Manufacturability: Consider the manufacturability of the PCB design, including factors such as solderability, assembly processes, and compatibility with manufacturing equipment. Consult with PCB manufacturers experienced in working with ceramic materials.
- Environmental Considerations: Take into account the operating environment of the PCB, including temperature extremes, humidity, and exposure to chemicals or other harsh conditions. Choose ceramic materials that are suitable for the intended environmental conditions.
- Reliability: Design the PCB to ensure long-term reliability, considering factors such as mechanical stress, thermal cycling, and reliability testing requirements. Use robust design practices and consider factors that may affect the reliability of ceramic materials, such as thermal expansion coefficients and mechanical stability.
- Testing and Validation: Implement testing and validation procedures to verify the performance and reliability of the Mini Ceramics PCB design under real-world operating conditions. This may include electrical testing, thermal analysis, and reliability testing.
These guidelines provide a starting point for designing Mini Ceramics PCBs, but it’s essential to adapt them to the specific requirements and constraints of each project and consult with experts in ceramic PCB design and manufacturing for best results.
What is the Mini Ceramics PCB Fabrication Process?
The fabrication process for Mini Ceramics PCBs involves several steps, similar to traditional PCB fabrication processes, but with specific considerations for working with ceramic materials. Here’s a general overview of the process:
- Design: The process starts with the PCB design phase, where the circuit layout and component placement are determined. Design software is used to create the PCB layout, considering factors such as signal integrity, thermal management, and manufacturability.
- Material Selection: Choose the appropriate ceramic material for the PCB based on the application requirements and the desired properties such as thermal conductivity, dielectric constant, and mechanical strength.
- Substrate Preparation: Prepare the ceramic substrate by cutting it to the desired size and shape. Ceramics are typically harder and more brittle than traditional PCB materials, so special care may be needed during this step to avoid cracking or damage to the substrate.
- Additive Manufacturing (Optional): In some cases, additive manufacturing techniques such as 3D printing may be used to build up layers of ceramic material to create complex shapes or features on the substrate.
- Printing: Print or deposit conductive traces and vias onto the ceramic substrate using techniques such as screen printing, inkjet printing, or thin-film deposition. Specialized conductive inks or pastes compatible with ceramic materials are used for this purpose.
- Curing: Cure the printed conductive patterns by heating the substrate to a specific temperature in a controlled environment. This process helps to bond the conductive materials to the ceramic substrate and ensure good electrical conductivity.
- Surface Finishing: Apply surface finishes to the PCB to protect the conductive traces and improve solderability. Common surface finishes for ceramic PCBs include gold plating, silver plating, or solder mask coatings.
- Component Assembly: Mount and solder electronic components onto the ceramic PCB using standard assembly techniques. Specialized soldering processes may be required to accommodate the high thermal conductivity of ceramic substrates.
- Testing and Inspection: Perform electrical testing and visual inspection to verify the functionality and quality of the assembled Mini Ceramics PCB. This may include continuity testing, impedance testing, and inspection for defects or irregularities.
- Packaging and Integration: Once the Mini Ceramics PCB has been fabricated and tested, it can be integrated into the final product or assembly, along with other components and subsystems as necessary.
Throughout the fabrication process, it’s essential to follow best practices for working with ceramic materials, including handling precautions to prevent damage or contamination, and to ensure that the finished PCB meets the required performance and reliability specifications for the intended application. Collaboration with experienced PCB manufacturers with expertise in ceramic materials may also be beneficial to ensure successful fabrication of Mini Ceramics PCBs.
How do you manufacture a Mini Ceramics PCB?
Manufacturing a Mini Ceramics PCB involves several steps tailored to the unique properties of ceramic materials. Here’s a detailed overview of the process:
- Substrate Preparation:
– Begin with a ceramic substrate typically made from materials like alumina (Al2O3) or aluminum nitride (AlN). These substrates are available in various thicknesses and sizes.
– Cut the ceramic substrate to the desired dimensions using precision cutting tools. Special care must be taken to avoid chipping or cracking the brittle ceramic material.
- Surface Cleaning:
– Clean the ceramic substrate thoroughly to remove any contaminants or debris that could affect the adhesion of conductive materials and surface finishes.
- Conductive Traces and Pads Deposition:
– Apply conductive traces, pads, and vias onto the ceramic substrate using techniques such as screen printing, inkjet printing, or thin-film deposition.
– Conductive materials compatible with ceramic substrates, such as silver, gold, or copper pastes or inks, are used. These materials are deposited in patterns defined by the PCB design.
- Curing:
– Cure the deposited conductive materials by heating the substrate to a specific temperature in a controlled atmosphere. This process helps to bond the conductive traces and pads to the ceramic substrate, ensuring good electrical conductivity.
- Surface Finishing:
– Apply surface finishes to protect the conductive traces and pads from oxidation and to facilitate soldering during component assembly.
– Common surface finishes for Mini Ceramics PCBs include gold plating, silver plating, or solder mask coatings.
- Component Assembly:
– Mount electronic components onto the ceramic substrate using standard surface mount technology (SMT) or through-hole assembly techniques.
– Specialized soldering processes may be required to accommodate the high thermal conductivity of ceramic substrates. These processes ensure proper bonding between the components and the conductive traces/pads.
- Testing and Inspection:
– Perform electrical testing to verify the functionality and integrity of the Mini Ceramics PCB. This may include continuity testing, impedance testing, and insulation resistance testing.
– Conduct visual inspection to identify any defects or irregularities in the conductive traces, pads, or component solder joints.
- Packaging and Integration:
– Once the Mini Ceramics PCB has passed testing and inspection, it can be integrated into the final product or assembly, along with other components and subsystems.
– The PCB may be encapsulated or packaged to provide additional protection against environmental factors such as moisture, temperature, and mechanical stress.
Throughout the manufacturing process, strict quality control measures should be implemented to ensure that the finished Mini Ceramics PCB meets the required performance and reliability standards for the intended application. Collaboration with experienced PCB manufacturers specializing in ceramic materials is recommended to ensure successful manufacturing of Mini Ceramics PCBs.
How much should a Mini Ceramics PCB cost?
The cost of a Mini Ceramics PCB can vary significantly depending on several factors such as the size, complexity, materials used, quantity ordered, and manufacturing processes involved. Here are some key factors that can influence the cost:
- Material: The type of ceramic material used for the substrate can impact the cost. Higher-performance ceramics such as alumina or aluminum nitride may be more expensive than standard FR-4 or other traditional PCB substrates.
- Design Complexity: The complexity of the PCB design, including the number of layers, fine pitch components, and specialized features such as controlled impedance traces, can affect the manufacturing cost. More complex designs typically require more advanced manufacturing processes and may incur higher costs.
- Manufacturing Processes: The manufacturing processes involved, such as printing, curing, surface finishing, and assembly, contribute to the overall cost. Specialized processes required for working with ceramic materials may also add to the cost.
- Quantity: The quantity of Mini Ceramics PCBs ordered can affect the unit cost. Larger production quantities often result in lower per-unit costs due to economies of scale, while small prototype or low-volume orders may have higher unit costs.
- Quality Standards: Meeting specific quality standards or certifications, such as IPC standards or compliance with industry regulations, may add to the cost of manufacturing.
- Additional Services: Additional services such as testing, inspection, and custom packaging may incur additional costs.
- Supplier Selection: The choice of PCB manufacturer or supplier can impact the cost. Different suppliers may offer varying pricing structures, capabilities, and levels of expertise in working with ceramic materials.
Given these factors, it’s challenging to provide a precise cost estimate without specific details about the Mini Ceramics PCB requirements. However, Mini Ceramics PCBs typically tend to be more expensive than conventional PCBs due to the specialized materials and manufacturing processes involved. It’s recommended to obtain quotes from multiple PCB manufacturers to compare costs and ensure the best value for the desired specifications and quantity.
What is Mini Ceramics PCB base material?
The base material used in Mini Ceramics PCBs is typically a type of ceramic material. Ceramics offer unique properties that make them suitable for certain applications, particularly those requiring high thermal conductivity, excellent electrical insulation, and resistance to high temperatures.
Common ceramic materials used as the base for Mini Ceramics PCBs include:
- Alumina (Al2O3): Alumina is one of the most widely used ceramic materials in PCB manufacturing. It offers excellent thermal conductivity, high mechanical strength, and good electrical insulation properties. Alumina-based PCBs are commonly used in high-power applications and environments with elevated temperatures.
- Aluminum Nitride (AlN): Aluminum nitride is another popular ceramic material for PCB substrates. It has high thermal conductivity, low thermal expansion coefficient, and good electrical insulation properties. AlN-based PCBs are suitable for applications requiring efficient heat dissipation and high-frequency operation, such as RF electronics and power electronics.
- Silicon Nitride (Si3N4): Silicon nitride is known for its high mechanical strength, excellent thermal shock resistance, and good electrical insulation properties. Si3N4-based PCBs are used in demanding applications where reliability and resistance to harsh environmental conditions are essential.
- Beryllium Oxide (BeO): Beryllium oxide offers exceptionally high thermal conductivity, making it ideal for applications requiring efficient heat dissipation. However, it is less commonly used due to health and safety concerns associated with beryllium exposure during manufacturing and handling.
These ceramic materials are available in various grades and formulations to meet specific application requirements. The choice of ceramic material depends on factors such as thermal management needs, electrical performance, mechanical stability, and environmental considerations. Additionally, specialized additives and processing techniques may be employed to further enhance the properties of the ceramic base material for Mini Ceramics PCBs.
Which company makes Mini Ceramics PCB?
The base material of Mini Ceramics PCB is typically ceramic, with common options including alumina and aluminum nitride. These ceramic materials possess excellent thermal conductivity, electrical insulation, and high temperature resistance, making them well-suited for specialized electronic applications such as RF circuits, power electronic devices, and circuits in high-temperature environments. Due to their unique properties, Mini Ceramics PCBs have found widespread use in fields where performance and reliability are paramount.
Regarding which companies manufacture Mini Ceramics PCBs, this depends on market demand and each company’s production capacity and technological expertise. Some well-known electronic component manufacturers and PCB fabricators may offer Mini Ceramics PCBs, along with specialized companies focused on ceramic PCB manufacturing.
Our company also produces Mini Ceramics PCBs. We have advanced production equipment and a skilled technical team capable of manufacturing high-quality Mini Ceramics PCBs. Our engineering team has extensive experience and can provide customized design and manufacturing solutions tailored to our customers’ needs and requirements. We adhere to strict quality management systems to ensure that the Mini Ceramics PCBs we produce meet industry standards and our customers’ specifications. Additionally, we offer flexible production scales and fast delivery cycles to accommodate diverse customer needs.
Whether you require high-performance RF circuits, high-temperature-resistant power electronic devices, or electronic products for other specialized applications, our company can provide you with top-quality Mini Ceramics PCB solutions. We warmly welcome you to contact us to discuss how we can meet your project requirements and to receive professional technical support and services.
What are the 7 qualities of good customer service?
Good customer service is essential for building positive relationships with customers and fostering loyalty. Here are seven qualities that characterize good customer service:
- Responsiveness: Good customer service involves promptly addressing customer inquiries, concerns, and requests. Being responsive shows customers that their needs are valued and that the company is committed to providing assistance in a timely manner.
- Empathy: Empathy involves understanding and acknowledging the customer’s perspective, feelings, and situation. Good customer service representatives demonstrate empathy by actively listening to customers, expressing understanding of their concerns, and showing genuine concern for their well-being.
- Professionalism: Professionalism entails maintaining a courteous and respectful demeanor when interacting with customers. Good customer service representatives are polite, patient, and maintain a positive attitude, even in challenging situations.
- Knowledgeability: Good customer service requires having a thorough understanding of the company’s products, services, policies, and procedures. Customer service representatives should be knowledgeable enough to provide accurate information and assist customers effectively.
- Flexibility: Flexibility involves adapting to the unique needs and preferences of individual customers. Good customer service representatives are willing to accommodate customer requests, offer personalized solutions, and go above and beyond to meet customer expectations.
- Reliability: Reliability means consistently delivering on promises and commitments made to customers. Good customer service involves being dependable and trustworthy, ensuring that customers can rely on the company to fulfill its obligations and provide consistent service quality.
- Problem-solving skills: Good customer service representatives possess strong problem-solving skills to effectively resolve customer issues and concerns. They can identify root causes of problems, propose viable solutions, and follow through until the issue is fully resolved to the customer’s satisfaction.
By embodying these qualities, companies can deliver exceptional customer service experiences that not only meet but exceed customer expectations, leading to increased customer satisfaction, loyalty, and positive word-of-mouth referrals.
FAQs (Frequently Asked Questions)
What are Mini Ceramics PCBs?
Mini Ceramics PCBs are printed circuit boards (PCBs) made from ceramic materials such as alumina or aluminum nitride. These materials offer advantages such as high thermal conductivity, excellent electrical insulation, and resistance to high temperatures.
What are the benefits of using Mini Ceramics PCBs?
Mini Ceramics PCBs offer superior thermal management, making them suitable for applications with high power dissipation or operating in high-temperature environments. They also provide excellent electrical performance, making them ideal for high-frequency applications such as RF circuits.
What applications are Mini Ceramics PCBs used for?
Mini Ceramics PCBs are commonly used in a variety of applications including RF electronics, power electronics, aerospace and defense systems, automotive electronics, and high-temperature environments such as industrial equipment and LED lighting.
How are Mini Ceramics PCBs manufactured?
Mini Ceramics PCBs are manufactured using processes similar to traditional PCB fabrication, with specialized techniques for working with ceramic materials. This includes substrate preparation, conductive trace deposition, curing, surface finishing, component assembly, testing, and inspection.
What factors should be considered when designing Mini Ceramics PCBs?
Design considerations for Mini Ceramics PCBs include thermal management, material selection, signal integrity, component placement, manufacturability, environmental factors, and reliability.
Are Mini Ceramics PCBs more expensive than traditional PCBs?
Mini Ceramics PCBs typically have higher manufacturing costs compared to traditional PCBs due to the specialized materials and processes involved. However, the specific cost depends on factors such as design complexity, material selection, and production volume.
Where can I find manufacturers of Mini Ceramics PCBs?
Manufacturers of Mini Ceramics PCBs include specialized PCB fabricators, electronic component suppliers, and companies with expertise in ceramic materials and PCB manufacturing. Researching online and contacting suppliers directly can help identify suitable manufacturers.