Millimeter Wave Circuit Board Manufacturer
Millimeter Wave Circuit Board Manufacturer,Millimeter Wave Circuit Boards are specialized PCBs designed to operate at millimeter wave frequencies, typically ranging from 30 GHz to 300 GHz. These boards are engineered to handle high-frequency signals with minimal loss and interference, making them essential for applications such as 5G communications, radar systems, and advanced satellite technology. Made from materials with low dielectric losses and high-frequency laminates, millimeter wave circuit boards ensure precise signal transmission and excellent performance. Their design includes features like fine-pitch traces and optimized impedance control, which are critical for maintaining signal integrity and reliability in high-speed, high-frequency environments.
What is Millimeter Wave Circuit Board?
A millimeter wave circuit board is designed to handle and operate within the millimeter wave frequency range, which spans from 30 GHz to 300 GHz. These high frequencies are used in advanced communication systems, including 5G technology, satellite communications, radar systems, and other applications requiring high data rates and precision.
Millimeter wave circuit boards are characterized by their ability to manage signal integrity and minimize losses at these high frequencies. To achieve this, they often use specialized materials with low dielectric losses and high dielectric constants, such as ceramic substrates or advanced composites. These materials help to reduce signal attenuation and maintain high performance in transmitting and receiving signals.
Designing millimeter wave circuit boards involves addressing several key challenges. Firstly, the propagation characteristics of millimeter waves require precise control over trace geometry and impedance to ensure efficient signal transmission. This often means using high-resolution manufacturing techniques to create fine line patterns and precise component placements.
Additionally, thermal management becomes crucial, as millimeter wave circuits can generate significant heat that must be dissipated effectively to prevent performance degradation or damage. Advanced thermal management solutions, such as heat sinks or thermal vias, are often integrated into the board design.
Overall, millimeter wave circuit boards are critical for enabling the next generation of high-speed wireless communication and advanced radar systems, driving innovation in various high-tech industries.
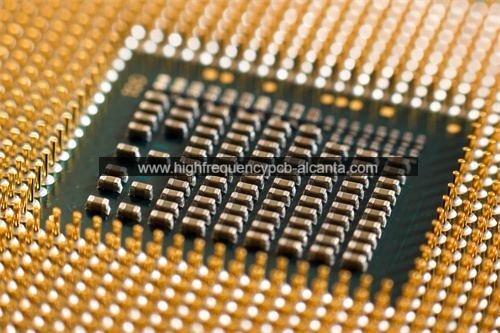
Millimeter Wave Circuit Board Manufacturer
What are the Millimeter Wave Circuit Board Design Guidelines?
Designing millimeter wave circuit boards requires careful consideration of several critical guidelines to ensure optimal performance and reliability. Here are some key design guidelines:
- Material Selection: Choose high-quality substrates with low dielectric loss and stable dielectric constant. Materials such as advanced ceramics or high-frequency laminates are commonly used to minimize signal attenuation and maintain signal integrity.
- Impedance Control: Maintain precise control over impedance to prevent signal reflections and ensure efficient signal transmission. Use specialized impedance calculation tools and design techniques to achieve the desired impedance values for transmission lines and components.
- Trace Design: Design traces with precise geometries to handle high-frequency signals effectively. This includes using narrow, well-defined traces and ensuring consistent trace widths and spacing. Avoid sharp corners and angles, which can cause signal distortion and loss.
- Layer Stack-Up: Carefully plan the layer stack-up to manage signal integrity and minimize interference. This includes properly spacing signal layers, ground planes, and power planes to reduce crosstalk and signal coupling.
- Thermal Management: Integrate effective thermal management solutions to dissipate heat generated by high-frequency signals. Use heat sinks, thermal vias, or other cooling mechanisms to prevent overheating and ensure reliable performance.
- Component Placement: Position components strategically to minimize signal path lengths and reduce parasitic effects. Ensure that components are placed to avoid excessive signal loss or interference and allow for adequate heat dissipation.
- Via Design: Use vias judiciously, as they can introduce inductance and signal loss. Optimize via size and placement to minimize their impact on signal integrity, and consider using blind or buried vias if appropriate.
- Simulation and Testing: Perform thorough simulations and testing throughout the design process to validate performance and identify potential issues. Use advanced simulation tools to analyze signal integrity, thermal performance, and other critical factors.
By adhering to these guidelines, designers can create millimeter wave circuit boards that meet the high performance and reliability requirements of advanced communication and radar applications.
What is the Millimeter Wave Circuit Board Fabrication Process?
The fabrication process for millimeter wave circuit boards involves several specialized steps to ensure that the final product meets the high-frequency performance requirements. Here’s a general overview of the fabrication process:
- Design and Layout:The process begins with designing the circuit board using CAD (Computer-Aided Design) software. This involves defining the circuit layout, trace patterns, impedance requirements, and component placements. The design is optimized for millimeter wave frequencies, taking into account factors such as trace width, spacing, and layer stack-up.
- Material Preparation:Select and prepare high-frequency laminate materials or substrates that have low dielectric loss and stable dielectric properties. Common materials include advanced ceramics or high-frequency epoxy laminates. The materials are cut to size and prepared for further processing.
- Layer Deposition: Deposit a thin layer of metal, typically copper, onto the substrate using techniques such as sputtering or chemical vapor deposition (CVD). This metal layer forms the conductive traces and pads for the circuit board.
- Photoresist Application: Apply a photoresist layer to the metalized substrate. This light-sensitive material will protect areas of the metal layer during etching. The photoresist is then exposed to ultraviolet (UV) light through a photomask that defines the circuit pattern.
- Etching:Develop the exposed photoresist to reveal the metal pattern underneath. Then, use etching chemicals to remove the unwanted metal, leaving behind the desired circuit pattern. This step creates the conductive traces, pads, and vias.
- Layer Bonding: If the circuit board design includes multiple layers, stack and bond the layers together using high-temperature laminating processes. Ensure proper alignment and adhesion between layers to maintain signal integrity and mechanical strength.
- Via Drilling: Drill holes for vias, which are used to connect different layers of the circuit board. Precision drilling is critical to avoid damage to the substrate and ensure proper via placement and alignment.
- Plating and Coating: Plate the drilled vias and exposed metal surfaces with additional layers of copper to ensure good electrical conductivity and create a reliable connection between layers. Apply protective coatings, such as solder mask or conformal coating, to shield the circuit board from environmental damage and improve durability.
- Inspection and Testing: Conduct thorough inspections and tests to verify the circuit board’s performance. This includes electrical testing to check for continuity, impedance, and signal integrity, as well as visual inspections to detect any defects or inconsistencies.
- Final Processing: Cut and shape the circuit board to its final dimensions. Add any additional features, such as mounting holes or connectors, as required by the design. Perform final quality checks to ensure that the board meets all specifications and performance criteria.
By following these steps, manufacturers produce millimeter wave circuit boards that meet the demanding requirements of high-frequency applications, ensuring reliable performance in advanced communication and radar systems.
How Do You Manufacture Millimeter Wave Circuit Board?
Manufacturing millimeter wave circuit boards involves a series of specialized steps tailored to handle high-frequency signals effectively. Here’s a detailed overview of the manufacturing process:
- Design and Specifications: Start with a detailed design phase using CAD software to create the circuit board layout. This includes specifying trace geometries, impedance control, and component placements tailored for millimeter wave frequencies. The design is optimized for minimizing signal loss and maintaining high performance.
- Material Selection: Choose high-frequency substrates with low dielectric loss and stable dielectric constants, such as advanced ceramics or specialized high-frequency laminates. These materials are crucial for ensuring that the circuit board can handle millimeter wave signals efficiently.
- Substrate Preparation: Cut the selected substrate material to the required size. This involves ensuring the material is free from contaminants and properly prepared for further processing.
- Copper Deposition: Apply a thin layer of copper onto the substrate. Techniques such as sputtering or chemical vapor deposition (CVD) are used to ensure a uniform and high-quality metal layer. This copper layer will form the circuit’s conductive traces and pads.
- Photoresist Application: Coat the copper layer with a photoresist film. This light-sensitive material protects areas of the copper during the etching process. The photoresist is exposed to UV light through a photomask that defines the circuit pattern, then developed to reveal the copper areas that will remain.
- Etching: Use chemical etching to remove the unprotected copper, leaving behind the desired circuit pattern. This step defines the conductive traces and pads based on the exposed pattern.
- Layer Bonding (if applicable): For multilayer boards, stack and bond the layers together. This involves applying adhesive layers between the substrates and using high-pressure, high-temperature lamination processes to ensure proper adhesion and alignment of the layers.
- Via Drilling: Drill precise holes (vias) through the board for electrical connections between different layers. This step requires high-precision drilling equipment to ensure accurate placement and minimal damage to the substrate.
- Plating and Coating:Plate the vias and any exposed copper with additional layers of copper to ensure good electrical conductivity. Apply protective coatings, such as solder mask or conformal coatings, to protect the circuit board from environmental factors and enhance durability.
- 10. Inspection and Testing: Conduct comprehensive inspections and tests to verify the circuit board’s performance. This includes electrical testing for continuity and impedance, as well as visual inspections for defects or inconsistencies. Testing ensures that the board meets the required specifications for millimeter wave applications.
- Final Processing:Trim and cut the circuit board to its final size. Add any necessary features, such as mounting holes or connectors. Perform final quality checks to ensure the board’s compliance with design specifications and performance standards.
By following these steps, manufacturers produce millimeter wave circuit boards capable of handling high-frequency signals with precision and reliability, essential for advanced communication and radar systems.
How Much Should Millimeter Wave Circuit Board Cost?
The cost of millimeter wave circuit boards can vary significantly based on several factors. Here’s a detailed breakdown of the cost considerations:
- Material Costs: Millimeter wave circuit boards typically use specialized high-frequency materials like advanced ceramics or high-frequency laminates. These materials are more expensive than standard FR-4 substrates due to their superior dielectric properties and performance at high frequencies. Material costs can range from $50 to $200 per square meter, depending on the specific type and quality.
- Board Complexity: The complexity of the board design impacts cost. Boards with intricate trace patterns, tight tolerances, and high-density interconnects (HDI) require advanced manufacturing techniques and increased labor, leading to higher costs. Simple designs may cost less, while complex multi-layer boards or those with high-density features can significantly increase the price.
- Size and Quantity: The size of the board affects material usage and processing time. Larger boards or those requiring multiple layers will be more expensive. Additionally, manufacturing costs can be influenced by order quantity; larger production runs typically reduce the per-unit cost due to economies of scale.
- Fabrication Techniques: Specialized fabrication techniques such as precision etching, high-accuracy drilling, and advanced plating can add to the cost. These techniques are necessary to ensure signal integrity and performance at millimeter wave frequencies, but they also increase production costs.
- Prototyping vs. Production: Prototyping costs are generally higher per unit compared to mass production. Prototypes require additional setup, testing, and validation, which can drive up costs. Production runs benefit from optimized processes and economies of scale, reducing the per-unit cost.
- Additional Features: Any additional features, such as complex thermal management solutions, advanced coatings, or custom components, will impact the overall cost. These features add to the complexity of the manufacturing process and can increase the final price.
- Testing and Quality Assurance: Thorough testing and quality assurance are essential for millimeter wave circuit boards to ensure they meet performance standards. The cost of extensive testing, including electrical performance and reliability assessments, is factored into the overall price.
In general, millimeter wave circuit boards can cost anywhere from $100 to $500 or more per square meter, depending on the aforementioned factors. Custom or highly specialized boards may exceed this range. It’s essential to work closely with manufacturers to get accurate quotes based on specific requirements and production volumes.
What is Millimeter Wave Circuit Board Base Material?
The base material for millimeter wave circuit boards is crucial in determining the board’s performance at high frequencies. These materials are chosen for their ability to handle millimeter wave signals with minimal loss and distortion. Here’s an overview of common base materials used for millimeter wave circuit boards:
- Ceramic Substrates: Ceramic materials, such as alumina (Al2O3) or barium titanate (BaTiO3), are often used for millimeter wave circuit boards due to their high dielectric constants and low dielectric losses. These materials provide excellent performance in terms of signal integrity and thermal management. They are particularly suitable for high-frequency applications but can be more expensive and brittle compared to other materials.
- High-Frequency Laminates: Specialized laminates, such as those made from hydrocarbon-based materials or PTFE (polytetrafluoroethylene), are commonly used in millimeter wave circuit boards. PTFE-based laminates, like those from Rogers Corporation, offer low dielectric loss and stable dielectric constants, which are essential for maintaining signal integrity at high frequencies.
- Glass Epoxy Laminates: These are commonly used in lower-frequency applications but can also be used for millimeter wave circuits if they are specifically formulated to handle high frequencies. They generally have higher dielectric losses compared to ceramics or PTFE laminates but can be suitable for less demanding millimeter wave applications.
- Metal Core Materials: Metal cores are used in some high-power millimeter wave applications for their thermal conductivity. These materials typically have a metal base layer (like aluminum or copper) with a dielectric layer on top. The metal core helps dissipate heat generated by high-frequency signals, improving the board’s reliability and performance.
- Advanced Composite Materials: These materials combine different substances to achieve desired properties, such as low dielectric loss and high thermal conductivity. Advanced composites may include combinations of ceramics, polymers, and metal layers tailored to specific millimeter wave applications.
- Flexible Materials: For applications requiring flexibility or conformability, flexible base materials like flexible laminates (e.g., polyimide) can be used. While not as common for high-frequency applications, flexible materials may be utilized in specific scenarios where conformal designs are required.
The choice of base material depends on various factors, including the specific frequency range, required performance characteristics, and cost considerations. Each material offers unique advantages and trade-offs, so selecting the appropriate base material is critical for achieving optimal performance in millimeter wave circuit boards.
Which Company Makes Millimeter Wave Circuit Board?
Many companies specialize in manufacturing millimeter wave circuit boards, with several renowned for their expertise in high-frequency applications. Here are some prominent manufacturers:
- Rogers Corporation:Rogers is a well-known supplier of high-frequency circuit board materials, particularly for millimeter wave applications. Their product line includes high-performance substrate materials such as RO4350B, RO4003C, and RO3003, widely used in communications, radar, and other high-frequency applications.
- DuPont: DuPont offers a range of high-frequency circuit board materials, including their renowned RCC (Rogers Ceramic Composite) series. These materials are known for their low dielectric loss and high dielectric constant, suitable for millimeter wave applications.
- Panasonic: Panasonic provides a broad range of circuit board materials, including those for high-frequency applications. Their high-frequency substrates are used in communication and radar systems, meeting the stringent requirements of millimeter wave applications.
- Arlon Electronic Materials: Arlon specializes in high-frequency materials and custom solutions. Their substrate materials are used in high-frequency and millimeter wave applications, offering excellent signal integrity and low loss characteristics.
- Teflon (PTFE) Materials: PTFE substrate materials, available from companies like Rogers, are widely used in millimeter wave circuit board designs due to their superior electrical performance and low dielectric loss.
Our company also manufactures millimeter wave circuit boards, offering the following features:
- High-Performance Materials: We use specialized high-frequency materials such as high-dielectric-constant ceramic substrates and PTFE (polytetrafluoroethylene) substrates. These materials effectively reduce signal loss and ensure high-frequency signal integrity.
- 2. Precision Manufacturing: We employ advanced manufacturing technologies to ensure high precision and performance in our circuit boards. This includes precise etching of traces, lamination processes, and high-accuracy drilling.
- Custom Solutions: We provide customized design and manufacturing services tailored to clients’ specific needs, including various layer counts, complex trace patterns, and specialized thermal management designs.
- Rigorous Testing: Our millimeter wave circuit boards undergo rigorous testing before delivery to ensure stable and reliable performance in high-frequency applications.
- Comprehensive Support: We offer full support from design to production, helping to address various challenges in millimeter wave circuit board design and application.
Whether for communication, radar, or other high-frequency applications, our company provides millimeter wave circuit boards that meet the highest standards and fulfill diverse customer requirements.
What are the 7 Qualities of Good Customer Service?
Good customer service is essential for building strong relationships with customers and ensuring their satisfaction. Here are seven key qualities of excellent customer service:
- Responsiveness: Good customer service is characterized by prompt and timely responses to customer inquiries, complaints, and requests. Customers value quick resolutions and feel appreciated when their concerns are addressed without unnecessary delays.
- Empathy: Understanding and empathizing with customers’ feelings and experiences is crucial. Showing genuine care and concern for their issues helps build trust and demonstrates that the company values their perspective.
- Knowledge and Expertise: Providing accurate and relevant information is essential. Customer service representatives should be well-trained and knowledgeable about the company’s products, services, and policies to offer informed assistance and solutions.
- Effective Communication:Clear and concise communication is key to good customer service. This includes active listening, using simple and understandable language, and ensuring that customers fully comprehend the information or instructions provided.
- Patience: Handling customers with patience, especially in challenging situations, helps in diffusing tension and providing effective solutions. Patience ensures that representatives can address customer concerns thoroughly and professionally.
- Consistency: Delivering a consistent level of service across all customer interactions helps build reliability and trust. Customers should receive the same high-quality service regardless of the channel or representative they interact with.
- Follow-Up: Good customer service involves following up to ensure that issues have been resolved to the customer’s satisfaction. This shows that the company is committed to continuous improvement and values customer feedback.
These qualities collectively contribute to creating a positive and memorable customer experience, fostering loyalty and enhancing the company’s reputation.
FAQs about Millimeter Wave Circuit Board
What is the frequency range for Millimeter Wave Circuit Boards?
Millimeter Wave Circuit Boards are designed for frequencies from 30 GHz to 300 GHz.
What materials are used in Millimeter Wave Circuit Boards?
High-frequency laminates, metal cores, and sometimes ceramic substrates are used.
How can I choose the right Millimeter Wave Circuit Board for my application?
Consider factors such as frequency requirements, thermal management, and design complexity.
What is the typical lead time for Millimeter Wave Circuit Board manufacturing?
Lead times vary based on complexity and quantity, but it usually ranges from a few weeks to several months.
What testing is performed on Millimeter Wave Circuit Boards?
Electrical tests, signal integrity tests, and performance validation are common.