Military Substrate Manufacturer
Military Substrate Manufacturer,Military substrates are the backbone of modern defense systems, encompassing a diverse range of materials and components meticulously engineered to meet the rigorous demands of military operations. These substrates form the foundation of armored vehicles, aircraft, naval vessels, weapons systems, and communication networks critical to national security. Crafted from high-performance materials such as advanced metals, composites, ceramics, and electronics, military substrates undergo stringent design, manufacturing, and testing processes to ensure durability, reliability, and effectiveness in challenging environments. From bullet-resistant armor to lightweight aircraft components, military substrates play a pivotal role in enhancing mission success, protecting personnel, and maintaining technological superiority on the battlefield. As innovations in materials science and technology continue to advance, military substrates evolve to meet the evolving needs of defense organizations worldwide, driving progress and resilience in the face of emerging threats.
What is a Military Substrate?
“Military substrate” could refer to several things depending on the context:
- Physical Substrate: In a literal sense, it could refer to the physical material or surface upon which military equipment, vehicles, or structures are built or operated. For example, tanks operate on various substrates including soil, sand, gravel, etc.
- Technological Substrate: It could also refer to the underlying technological infrastructure or platform that supports military operations. This might include communication networks, data storage systems, computing architectures, etc.
- Training and Recruitment:In another sense, “military substrate” could refer to the foundational training, education, and recruitment processes that form the basis of a military organization. This includes everything from basic training for soldiers to the selection and development of military leaders.
- Strategic Environment: It might also refer to the broader strategic environment in which military operations take place, encompassing geopolitical factors, alliances, adversaries, and other contextual elements that shape military decision-making.
Without more context, it’s difficult to determine the specific meaning intended.
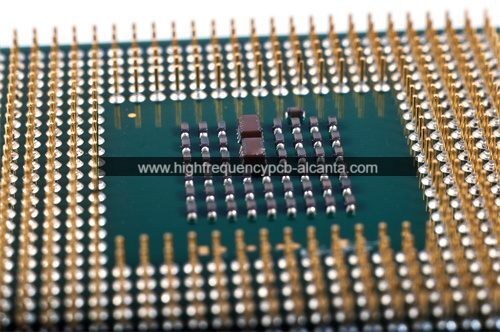
Military Substrate Manufacturer
What are the Military Substrate Design Guidelines?
“Military substrate design guidelines” would likely refer to the set of principles, standards, and specifications used in designing various elements of military equipment, infrastructure, or technology. These guidelines ensure that military assets are built to meet the specific requirements and challenges of military operations.
These guidelines could cover a wide range of topics, including:
- Durability and Reliability: Military equipment needs to withstand harsh environmental conditions, intense usage, and potential enemy actions. Design guidelines would specify requirements for durability, reliability, and ruggedness.
- Performance:Military equipment must perform reliably in a variety of operational scenarios. Guidelines would include specifications for speed, accuracy, range, firepower, mobility, and other performance metrics.
- Compatibility and Interoperability: Military systems often need to work together seamlessly, whether they are from the same service branch or different allied forces. Design guidelines would ensure compatibility and interoperability between various military platforms, systems, and equipment.
- Security: Military systems must be designed with robust security features to protect against cyber threats, espionage, and unauthorized access. Guidelines would include requirements for encryption, authentication, access control, and data protection.
- Maintainability and Repairability: In the field, military equipment needs to be quickly maintained and repaired to minimize downtime. Guidelines would specify design features that facilitate easy maintenance, diagnostics, and repair.
- Size, Weight, and Power (SWaP): Military equipment often needs to be compact, lightweight, and energy-efficient to maximize mobility and operational flexibility. Guidelines would include restrictions and recommendations regarding SWaP characteristics.
- Environmental Considerations: Military operations can have significant environmental impacts. Design guidelines would address considerations such as fuel efficiency, emissions reduction, noise reduction, and compliance with environmental regulations.
These are just a few examples, and the specific design guidelines would vary depending on the type of military equipment or infrastructure being developed.
What is the Military Substrate Fabrication Process?
The “military substrate fabrication process” likely refers to the procedures and techniques involved in manufacturing or constructing the physical components or structures used in military equipment, vehicles, or infrastructure. While the specific process can vary widely depending on the type of substrate being fabricated (metal, composite, electronic, etc.) and the intended application, here is a generalized overview of the fabrication process:
- Design and Planning: The process begins with the design phase, where engineers and designers develop detailed plans and specifications for the substrate based on the requirements of the military application. This may involve computer-aided design (CAD) software and collaboration with military stakeholders.
- Material Selection: The appropriate materials are selected based on factors such as strength, durability, weight, and cost. Military substrates often require materials capable of withstanding harsh environmental conditions and potential combat situations.
- Preparation: Before fabrication begins, the materials are prepared for processing. This may involve cutting, shaping, or otherwise preparing raw materials such as metal sheets, composite panels, or electronic components.
- Fabrication Techniques: The specific fabrication techniques used depend on the type of substrate being produced. Common techniques include welding, machining, casting, forging, molding, 3D printing, and surface treatment processes such as painting or coating.
- Assembly: Once the individual components or parts are fabricated, they are assembled into the final substrate according to the design specifications. This may involve welding, bolting, adhesive bonding, or other joining methods.
- Quality Control: Throughout the fabrication process, quality control measures are implemented to ensure that the substrate meets the required standards and specifications. This may include inspections, testing, and verification of dimensional accuracy, material properties, and structural integrity.
- Finishing and Testing: After assembly, the substrate may undergo finishing processes such as surface treatment, painting, or coating to improve aesthetics, corrosion resistance, or other functional properties. Substrates are then subjected to rigorous testing procedures to verify performance and durability under simulated operational conditions.
- Deployment and Maintenance: Once fabricated and tested, military substrates are deployed for use in military operations. Regular maintenance and inspection procedures are implemented to ensure continued functionality and reliability throughout the substrate’s service life.
Overall, the military substrate fabrication process involves careful planning, precise execution, and stringent quality control measures to produce components and structures that meet the demanding requirements of military applications.
How do you manufacture a Military Substrate?
Manufacturing a military substrate involves a series of steps tailored to the specific requirements of the intended application and the materials involved. Here’s a generalized overview of the manufacturing process:
- Design and Planning: The process starts with detailed design and planning. Military substrates are typically designed to meet specific performance, durability, and reliability requirements. Engineers use computer-aided design (CAD) software to create precise blueprints and specifications.
- Material Selection: The appropriate materials are selected based on the substrate’s intended use. Common materials include metals (such as steel, aluminum, and titanium), composites (such as fiberglass or carbon fiber reinforced polymers), and electronics components. Material selection is crucial to ensure that the substrate can withstand harsh environmental conditions and potential combat situations.
- Preparation: Raw materials are prepared for processing. This may involve cutting, shaping, or otherwise preparing materials into the desired form. For example, metal sheets may be cut to size, composite panels may be molded, and electronic components may be assembled onto circuit boards.
- Fabrication Techniques: The specific fabrication techniques used depend on the materials and design of the substrate. Common techniques include:
– Metal Fabrication: Techniques such as welding, machining, casting, and forging are used to shape and assemble metal components.
– Composite Fabrication: Composites may be fabricated using molding, vacuum bagging, or filament winding techniques.
– Electronic Assembly: Surface mount technology (SMT) or through-hole assembly may be used to assemble electronic components onto printed circuit boards (PCBs).
- Assembly:Once the individual components or parts are fabricated, they are assembled into the final substrate according to the design specifications. This may involve welding, bolting, adhesive bonding, or other joining methods. Assembly processes are carefully controlled to ensure dimensional accuracy and structural integrity.
- Quality Control: Throughout the manufacturing process, quality control measures are implemented to ensure that the substrate meets the required standards and specifications. This may include inspections, testing, and verification of material properties, dimensional accuracy, and performance characteristics.
- Finishing and Testing: After assembly, the substrate may undergo finishing processes such as surface treatment, painting, or coating to improve aesthetics, corrosion resistance, or other functional properties. Substrates are then subjected to rigorous testing procedures to verify performance and durability under simulated operational conditions.
- Deployment and Maintenance: Once manufactured and tested, military substrates are deployed for use in military operations. Regular maintenance and inspection procedures are implemented to ensure continued functionality and reliability throughout the substrate’s service life.
Overall, manufacturing a military substrate requires careful planning, precise execution, and adherence to strict quality control standards to produce components and structures that meet the demanding requirements of military applications.
How much should a Military Substrate cost?
Determining the cost of a military substrate is complex and depends on various factors including its size, complexity, materials, technology involved, and intended purpose. Here are some key considerations that can influence the cost:
- Materials: The cost of raw materials plays a significant role in determining the overall cost of a military substrate. High-performance materials such as specialized metals, advanced composites, or cutting-edge electronic components can be expensive.
- Manufacturing Processes: The manufacturing processes used to fabricate the substrate can impact its cost. Advanced fabrication techniques, intricate assembly methods, and specialized equipment may increase manufacturing costs.
- Design Complexity: The complexity of the substrate’s design influences manufacturing difficulty and cost. Intricate designs with tight tolerances, intricate shapes, or advanced features may require more time and resources to manufacture, leading to higher costs.
- Testing and Certification: Military substrates typically undergo rigorous testing and certification processes to ensure they meet strict performance and quality standards. Testing can add to the overall cost of production.
- Quantity Produced: Economies of scale can affect the cost of military substrates. Producing larger quantities of substrates often reduces per-unit costs due to efficiencies in manufacturing, purchasing, and logistics.
- Research and Development: If the substrate incorporates new technologies or features, costs associated with research and development (R&D) may also factor into the overall cost.
- Logistics and Support: Costs related to logistics, transportation, storage, and ongoing support throughout the substrate’s lifecycle contribute to the total cost of ownership.
- Market Conditions: External factors such as fluctuations in material prices, labor costs, regulatory requirements, and geopolitical conditions can impact the cost of military substrates.
Given these factors, it’s challenging to provide a specific cost for a military substrate without detailed information about its specifications and requirements. Costs can vary widely depending on the specific circumstances and context of the project. In general, military substrates tend to be expensive due to their specialized nature, stringent requirements, and the need for high-quality materials and manufacturing processes.
What is Military Substrate base material?
The term “Military Substrate base material” isn’t standard military terminology, so it’s a bit ambiguous. However, if we’re discussing the base material used in constructing various military equipment, vehicles, or structures, it typically depends on the specific application and requirements.
Here are some common base materials used in military substrates:
- Metals: Metals such as steel, aluminum, titanium, and various alloys are frequently used in military substrates due to their strength, durability, and versatility. Steel is often employed in armored vehicles and structures due to its excellent ballistic resistance, while aluminum and titanium are valued for their lightweight properties in aerospace applications.
- Composites: Composite materials, including fiberglass, carbon fiber reinforced polymers (CFRP), and aramid fibers (e.g., Kevlar), are used to create lightweight, high-strength military substrates. Composites offer advantages such as corrosion resistance, low radar signature, and the ability to be molded into complex shapes.
- Ceramics: Ceramics are utilized in military substrates for their hardness, heat resistance, and ballistic protection properties. Ceramic materials like alumina, silicon carbide, and boron carbide are often incorporated into armor plates and vehicle components to provide enhanced protection against projectiles and explosives.
- Plastics: High-performance plastics and polymers, such as polyethylene (PE) and polyurethane (PU), are employed in military substrates for their lightweight, corrosion resistance, and impact-absorbing properties. Plastics are used in various applications, including vehicle components, protective gear, and electronic enclosures.
- Electronic Components: Military substrates incorporating electronic components often utilize specialized materials such as printed circuit board (PCB) substrates, semiconductor materials (e.g., silicon), and conductive materials (e.g., copper, gold) for wiring and interconnects.
- Textiles: Textile materials such as ballistic nylon, aramid fibers, and high-tenacity polyester are used in military substrates for applications such as protective clothing, tents, and vehicle covers. These materials provide resistance to abrasion, tearing, and ballistic threats.
- Specialized Materials: Depending on the specific requirements of the military substrate, other specialized materials may be employed, including ceramics, rubber compounds, advanced coatings, and nanostructured materials.
The selection of base materials for military substrates depends on factors such as the substrate’s intended use, performance requirements, environmental conditions, weight constraints, and cost considerations. Military engineers carefully evaluate these factors to choose the most suitable materials for each application.
Which company makes Military Substrate?
Many companies specialize in the production of military substrates, with some having extensive experience and expertise in manufacturing high-performance, high-reliability military equipment and technology. These companies typically include defense contractors, military industrial giants, and firms dedicated to research and manufacturing in the military domain. Some well-known defense companies include Lockheed Martin, Boeing, Northrop Grumman, Raytheon Technologies, and General Dynamics, among others.
While our company may not belong to the aforementioned defense giants, we have the capability to manufacture military substrates. Equipped with advanced manufacturing equipment and technology, a professional engineering team, and extensive experience, our company can meet the stringent requirements of military equipment and technology. Our manufacturing processes are carefully designed and strictly adhere to quality control standards to ensure the production of high-quality, reliable military substrates.
Our company possesses comprehensive capabilities in material selection, design development, manufacturing processing, quality testing, and more. We can customize military substrates according to the needs of our customers, including metal substrates, composite substrates, electronic component substrates, and others. We are committed to providing innovative solutions and reliable technical support for military applications.
In addition to manufacturing military substrates, our company also offers complementary services, including technical support, maintenance, and subsequent upgrades and improvements. Our team is dedicated to providing comprehensive support and services to our customers, ensuring the success of their military projects.
In the fiercely competitive defense market, our company will continuously strive to improve our technological capabilities, enhance our innovation capacity, and provide our customers with higher-quality products and services. We will actively respond to the strategic needs of the nation and contribute to national defense construction.
What are the 7 qualities of good customer service?
Good customer service is essential for maintaining customer satisfaction and loyalty. Seven qualities of good customer service include:
- Responsiveness: A good customer service team responds promptly to customer inquiries, concerns, and requests. They acknowledge customer communication in a timely manner and strive to provide assistance or information quickly.
- Empathy: Empathy involves understanding and acknowledging the customer’s emotions, concerns, and needs. A good customer service representative listens actively, demonstrates empathy, and shows genuine concern for the customer’s situation.
- Clarity: Good customer service involves clear communication that is easy for customers to understand. Customer service representatives should provide information, instructions, and explanations clearly and concisely, avoiding technical jargon or confusing language.
- Professionalism: Professionalism is crucial in customer service interactions. Representatives should conduct themselves with professionalism, maintaining a courteous and respectful demeanor at all times, even in challenging situations.
- Problem-solving skills: Effective customer service involves the ability to resolve customer issues and problems efficiently and effectively. Customer service representatives should be resourceful, proactive, and solution-oriented, working to address customer concerns and find satisfactory resolutions.
- Consistency: Consistency in service delivery is important for building trust and credibility with customers. Good customer service teams strive to deliver consistent service experiences across all customer interactions, regardless of the channel or individual representative.
- Follow-up: Following up with customers after their initial interaction demonstrates care and commitment to customer satisfaction. Good customer service teams follow up with customers to ensure that their issues have been resolved satisfactorily and to gather feedback for continuous improvement.
By embodying these qualities, organizations can provide exceptional customer service experiences that foster customer loyalty and drive business success.
FAQs
What are military substrates?
Military substrates are the physical materials or components used in the construction of military equipment, vehicles, structures, and technologies. These substrates are designed to meet the specific requirements and challenges of military operations.
What materials are commonly used in military substrates?
Common materials used in military substrates include metals (such as steel, aluminum, titanium), composites (such as fiberglass, carbon fiber reinforced polymers), ceramics, electronics components, and specialized textiles.
What are the key considerations in designing military substrates?
Designing military substrates involves considerations such as durability, reliability, performance, compatibility, interoperability, security, maintainability, and environmental impact.
How are military substrates manufactured?
The manufacturing process for military substrates involves design and planning, material selection, preparation, fabrication techniques (e.g., welding, machining, molding), assembly, quality control, finishing, and testing.
What are the applications of military substrates?
Military substrates are used in a wide range of applications including armored vehicles, aircraft, naval vessels, weapons systems, communications equipment, protective gear, shelters, and infrastructure.
How are military substrates tested for performance and durability?
Military substrates undergo rigorous testing procedures to verify their performance and durability under simulated operational conditions. Testing may include mechanical testing, environmental testing, ballistic testing, electromagnetic compatibility testing, and more.
What companies manufacture military substrates?
Various companies specialize in the production of military substrates, including defense contractors, military suppliers, and specialized manufacturers. Some well-known companies in the defense industry produce military substrates as part of their product offerings.
How can I ensure the quality and reliability of military substrates?
Quality and reliability can be ensured by working with reputable suppliers, adhering to military specifications and standards, conducting thorough testing and inspection procedures, and implementing robust quality management systems throughout the manufacturing process.